Elimina largos tiempos de configuración con automatización avanzada
Erik Anderson, presidente y CEO de Basin Precision Machining LLC, ha determinado que las configuraciones son la raíz de todos los males cuando se trata de productividad de fabricación. Causan variaciones en las piezas, tiempos de inactividad y altas tasas de chatarra. Y como muchas otras tiendas, Basin también enfrentó el desafío de configuraciones de trabajo largas y complejas, hasta que la tienda con sede en Jefferson, WI, se defendió con automatización.
Basin se considera un taller relativamente no convencional debido a su extrema obsesión por la calidad, la fabricación esbelta y la producción de flujo de una sola pieza altamente eficiente en toda su planta de taller. Pero en ninguna parte esta falta de convencionalidad es más evidente que con el uso de automatización de la empresa dentro de un entorno de producción de alta mezcla / bajo volumen en oposición al escenario típico de alto volumen.
Para lograr su automatización especial de producción de alta mezcla y bajo volumen, Basin confía en celdas de fabricación compuestas por la última tecnología de máquinas herramienta más avanzada armada con las mayores capacidades de almacenamiento de herramientas posibles y conectividad digital, una combinación que básicamente ha eliminado los tiempos de configuración.
Como taller de máquinas de precisión, Basin da servicio a los mercados de petróleo y gas, aeroespacial, de vehículos recreativos e hidráulicos. Entre sus clientes se encuentran la compañía de petróleo y gas FHE USA LLC, el fabricante de válvulas de cartucho HydraForce Inc. y el fabricante de motocicletas OEM Harley-Davidson Inc.
En algunos casos, la tienda producirá alrededor de 250 versiones de una pieza para un cliente. Los tamaños de lote de trabajo asociados pueden variar de cinco a 500 piezas, lo que, según Anderson, equivale a unas 80 configuraciones por mes para cambiar de una versión a la siguiente. Estas configuraciones que requieren mucho tiempo y mano de obra requieren personas expertas que entiendan las configuraciones de más de 100 herramientas, la fijación complicada de múltiples lados y cómo ejecutar piezas complejas.
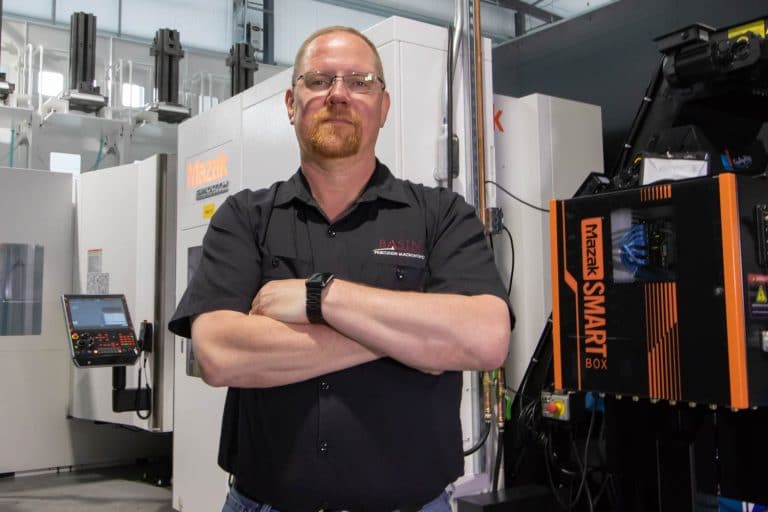
Con una de sus celdas de fabricación automatizada más grandes, Basin puede tener alrededor de 200 números de pieza configurados en un momento dado. La celda permite a la tienda configurar trabajos una vez, dejarlos en la celda y ejecutar cada uno cuando sea necesario. Ubicada en una nueva adición de 22.500 pies2 (2.090 m2) y produciendo principalmente colectores hidráulicos, la celda consta de seis centros de mecanizado horizontal Mazak HCN-5000 dentro de un sistema Mazak PALLETECH que cuenta con tres niveles, 120 paletas y tres estaciones de carga. Para una capacidad máxima de la herramienta, cada centro de mecanizado se empareja con una Mazak TOOL HIVE que contiene 348 herramientas cada una para un total de 2.088 herramientas.
Las grandes capacidades de herramientas, según Anderson, contribuyen significativamente a las reducciones de configuración, ya que permiten que el taller deje las herramientas configuradas a medida que las células cambian de una parte a la siguiente. En la mayoría de los casos, hay suficientes herramientas para una sola máquina para ejecutar una docena de números de pieza diferentes de tres tamaños de materia prima.
El año pasado el taller realizó alrededor de $11 millones de trabajos de colector hidráulico en 15 máquinas independientes operadas por 32 personas. Solo con el nuevo sistema Mazak, Basin ahora manejará aproximadamente $9.5 millones de trabajo con solo seis máquinas y seis personas que producen el 90% de lo que hacía anteriormente.
Todos los HCN-5000S tienen los controles MAZATROL SmoothG de Mazak, que son fáciles de usar y ofrecen un mecanizado de alta velocidad y alta precisión. Las mesas giratorias de accionamiento directo y los cambiadores de dos paletas vienen de serie en las máquinas. Esta función de automatización simple y eficiente mejora la productividad al permitir que el robot guiado por carril PALLETECH cargue o descargue un palé mientras la máquina continúa trabajando en una parte fija en su otro palé.
Para una mayor optimización de los procesos, cada uno de los HCN-5000S de la célula está equipado con un MAZAK SMARTBOX, una plataforma de lanzamiento que proporciona a Basin una entrada fácil y segura en el Internet Industrial de las Cosas (IIoT). Con la tecnología MTConnect en su base, el protocolo abierto SmartBox facilita la conectividad de las máquinas y dispositivos de la tienda, al tiempo que permite mejorar las capacidades de monitoreo y análisis.
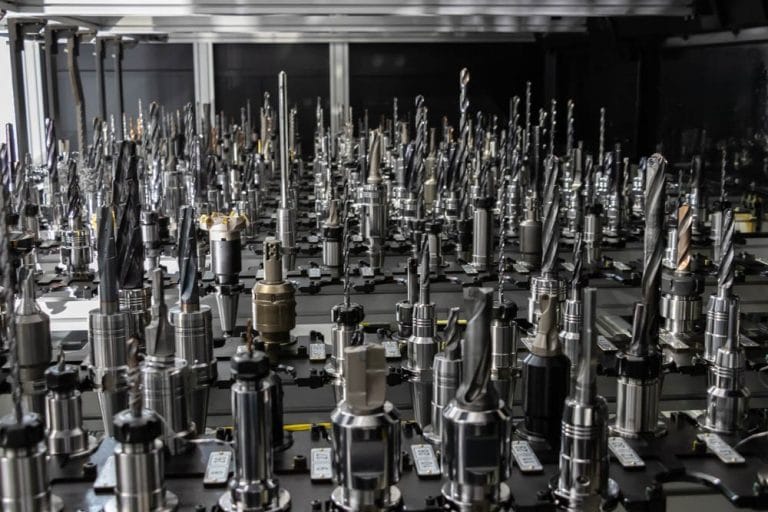
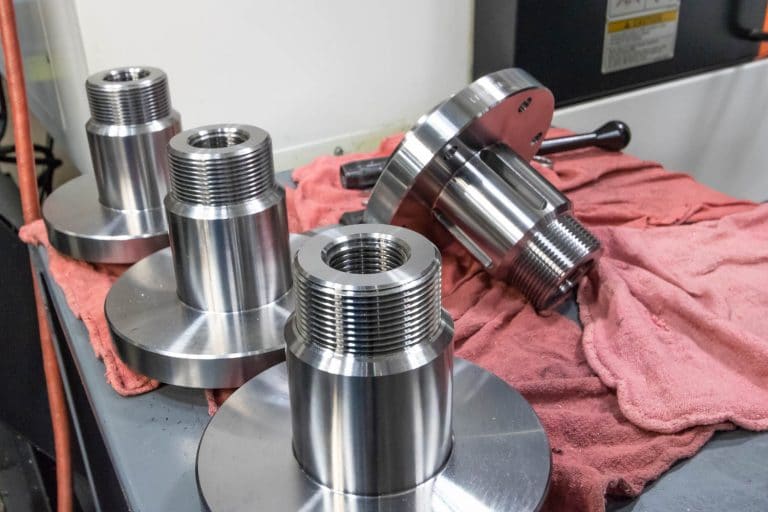
Según Anderson, Basin instaló SmartBoxes para monitorear la efectividad general del equipo (OEE) y eventualmente interactuar con el sistema ERP de la tienda. Actualmente las SmartBox de Mazak transfieren datos de herramientas, a través de chips RFID, desde los preajustes de herramientas de Basin a las máquinas. Pero, dijo que la tienda eventualmente detectará el equipo para que pueda usar las SmartBox de Mazak para el mantenimiento preventivo y el monitoreo de sistemas críticos en las máquinas
Otra célula de fabricación automatizada añadida recientemente en Basin se centra en un centro de mecanizado horizontal Mazak HCN-8800 y un 348 tool TOOL HIVE dentro de un sistema PALLETECH de seis paletas. La célula produce componentes principalmente para un sistema de la industria del petróleo y el gas para asegurar equipos a las cabezas de pozo, RigLock de FHE.
Además del HCN-8800, Basin también produce componentes para el sistema RigLock con una máquina multitarea Mazak INTEGREX i-630V/6, una solución de cinco ejes con potentes husillos de torneado y fresado diseñada para el mecanizado resistente. La máquina procesa cuerpos RigLock que miden 20′′ (508 mm) de diámetro, pesan 1200 lb y están hechos de acero con una dureza de Rc 32. Estas piezas utilizan para otro proveedor seis operaciones de mecanizado y 55 días de tiempo total de procesamiento; Cuenca ahora las termina en poco más de siete horas con solo una operación de mecanizado en la INTEGREX i-630V/6.
Para estas piezas, según Anderson, el proceso es mucho más fácil si se puede hacer en una sola operación. “Esto permite eliminar todas las variables como el manejo, la carga, la pérdida de registro y la necesidad de múltiples equipos”, explicó. “Si un taller convencional hiciera el mismo trabajo, necesitarían dos torneras y un molino vertical con indexador y tendrían que manipular la pieza cuatro veces”.
En Cuenca, el flujo de una sola pieza y la capacidad de la máquina Done in One Mazak significa que la materia prima entra en el proceso y sale como componentes terminados. Esto significa cero WIP, muchos menos problemas de calidad y tiempos de entrega más rápidos. Todo esto ha resultado en un sub-50 partes por millón (ppm) en el rendimiento de calidad de defectos para Cuenca. De hecho, la tienda ha sido tan baja como 19 ppm, y ha sido así durante los últimos 10 años.
Anderson dijo que algunos de los otros Mazak de la tienda, como su INTEGREX i-630V/6, no son lo que se consideraría automatización tradicional: ningún robot carga la máquina. En cambio, la automatización es el resultado de la capacidad de la máquina multitarea para realizar operaciones de torneado, así como el fresado completo de cinco ejes para procesar piezas en configuraciones únicas.
Otros ejemplos de automatización integrada incluyen otras cuatro máquinas multitarea Mazak recientemente adquiridas. Se trata de la INTEGREX i-400S de la tienda, que cuenta con un segundo husillo giratorio; una INTEGREX i-200ST, que cuenta con una torreta inferior además de su segundo husillo giratorio; y dos máquinas multitarea INTEGREX e-500H-S, cada una de las cuales cuenta con dos husillos giratorios opuestos igualmente potentes con control del eje C. Esas máquinas también tienen husillos de fresado integrales que giran en el eje B para operaciones simultáneas de fresado de cinco ejes y alta velocidad de alimentación.
La INTEGREX e-500H-S fabrica piezas grandes para el sistema RigLock. Las INTEGREX i-400S e i-200ST también procesan componentes RigLock y piezas de prevención de estallido que se alimentan con barras en la máquina INTEGREX i-200ST. Mientras estas máquinas funcionan, su operador también tiene tiempo para ejecutar la INTEGREX i-400S.
“Los sistemas de mecanizado automatizado como nuestros Mazaks,” dijo Anderson, “son la solución a problemas laborales como la falta de mano de obra calificada. Nuestra gente es gerente de automatización porque es difícil encontrar maquinistas. Son conscientes con un fuerte sentido de propiedad para supervisar nuestros sistemas y mantenerlos produciendo. No son pulsadores de botones, son individuos invertidos en el proceso, gerentes de planta individuales, en cierto sentido, y son responsables de la materia prima de su célula de trabajo, las máquinas en la célula, las herramientas, la calidad, cómo se registra la pieza y cómo se empaqueta y presenta al cliente".
La mayoría de las piezas en Basin están hechas de materiales que incluyen 4140, 4340 y algunos aceros preendurecidos en forma de barras, forjas y piezas fundidas. También produce algunas piezas de aluminio Invar 36, 6061-T6 y hierro dúctil DuraBar 65-45-12. Las piezas de trabajo pueden pesar entre 2 oz y 2.000 lb y requieren tolerancias ajustadas y acabados superficiales. Las tolerancias posicionales van desde 0,005′′ (0,12 mm) hasta 0,001′′ (0,0254 mm), y en muchos casos, el taller debe mantener tolerancias diametrales de ±0,00025′′. Los tamaños típicos de lotes de trabajo van desde la producción continua que involucra cientos de miles de piezas por año hasta trabajos individuales que producen tan solo dos piezas.
Iniciada originalmente por los padres de Anderson, la tienda tiene 190 empleados, dos instalaciones en Jefferson y Whitewater, WI, y un espacio de fabricación combinado de 85,000 pies2 (7,897 m2). La tienda tiene alrededor de 10 clientes, y según Anderson, no están tratando de ser el taller de trabajo para 100 clientes porque es muy difícil proporcionar a todos ellos un servicio adecuado al mismo tiempo.
“Nos esforzamos por desarrollar relaciones sólidas con clientes clave que quieren que produzcamos cantidades significativas de trabajo”, dijo. “Al hacerlo, obtenemos compromisos sólidos de nuestros clientes y estamos dispuestos a hacer grandes inversiones en tecnología de fabricación para producir sus componentes lo mejor que podamos con la mayor calidad y rentabilidad. Muchas tiendas no están dispuestas a hacer eso”.
Cuenca continuará centrándose en trabajos de alta mezcla / bajo volumen que consisten en partes complejas porque son los que la mayoría de las tiendas rehúyen. Anderson dijo que el objetivo es obtener el trabajo y el equipo correcto para ello, como las máquinas Mazak flexibles y los sistemas de automatización que la empresa utiliza hoy en día. Esta estrategia le ha funcionado bien y continúa abriendo nuevos mercados para Basin.
“Estamos mirando hacia el futuro y estamos dispuestos a hacer inversiones”, dijo Anderson. “Esto resuena con los clientes potenciales porque es difícil para ellos obtener los trabajos que buscamos. Estos clientes quieren proveedores que se comprometan a obtener la tecnología de punta y todo lo demás necesario para el trabajo”.