Max. Machining Diameter | Φ19.69" |
Max. machining height | 18.11" |
Chuck size | 12" to 18" |
CNC Turning Centers
MEGA TURN
- Outstanding cutting capacity for high productivity
- Automatic tool changer for further improvement of productivity
- Large machining area
- Symmetrical machines can be lined up to build an efficient line
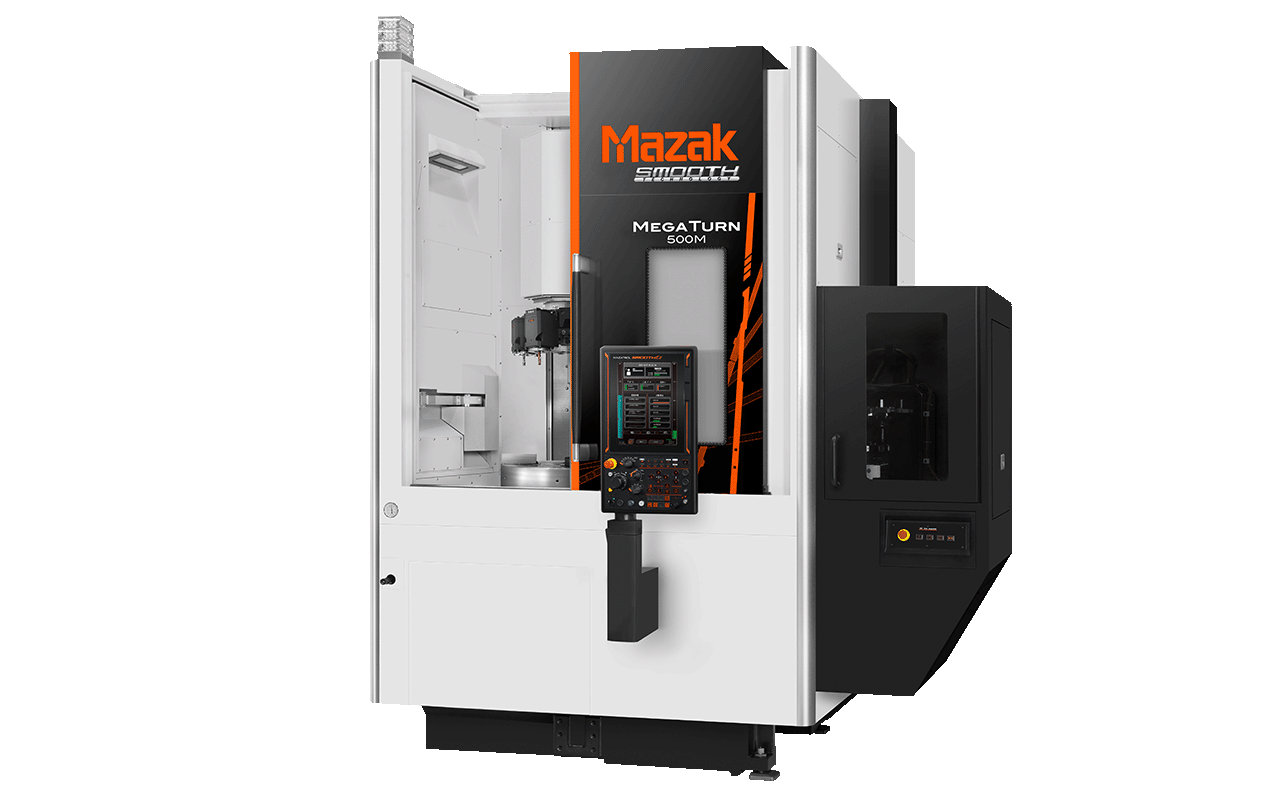
Unique design for large machining area
Adopts a column travelling design which eliminates limits of machining diameter based on machine structure.
The travelling column design has been adopted instead of cross rail design that interferes with the workpiece and turret. This leads to eliminating limitations of the machining diameter caused by the machine structure, allowing for a large machining area.
Machining Capacity | ||
---|---|---|
Model | 1: Diameter | 2: Height |
500, 500S, 500M, 500MS | Φ19.69" × H18.11" | |
600, 600S | Φ24.8" × H21.65" | |
600M, 600MS | Φ23.62" × H21.65" | |
900, 900S, 900M, 900MS | Φ36.22" × H31.5" | |
1600, 1600M | Φ64.96" × H35.43" |
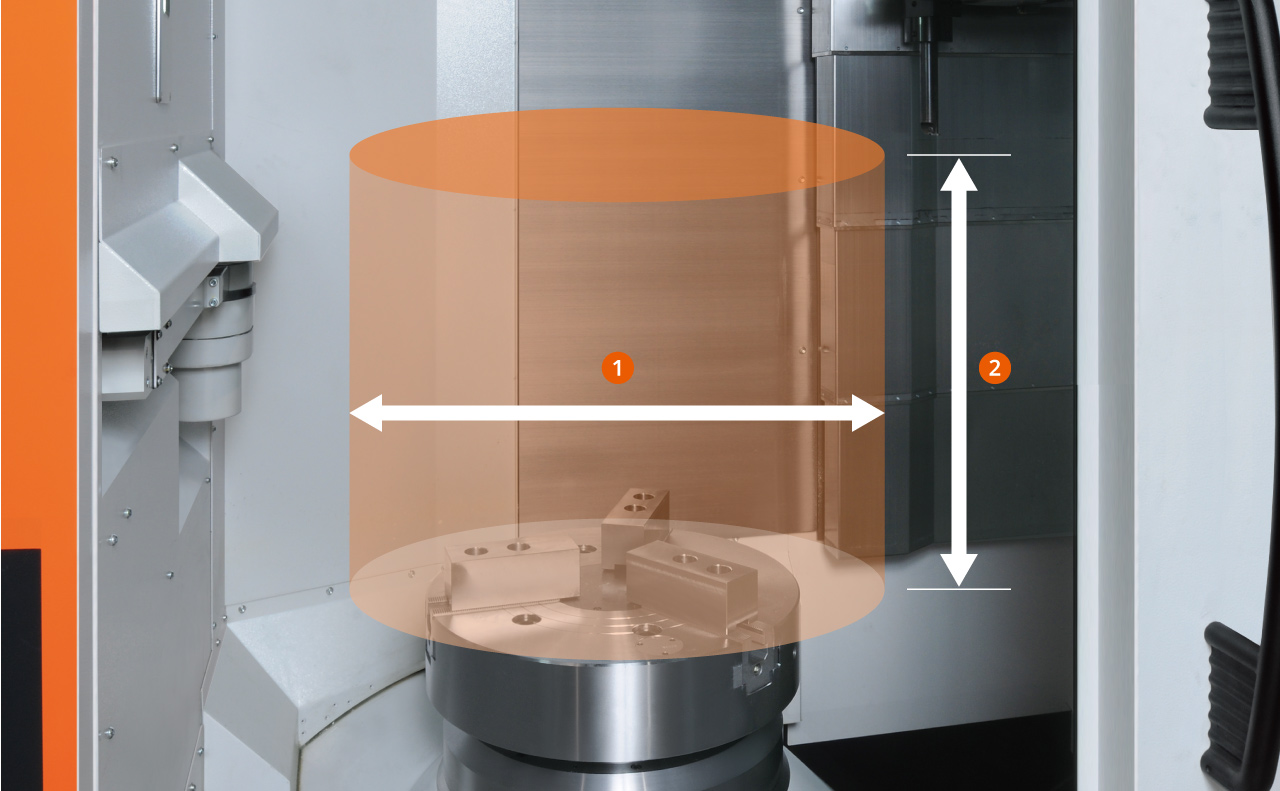
Equipped with a highly rigid, high-torque turning spindle
High-rigidity headstock for machining heavy workpieces
MEGA TURN 900 Series
Material removal rate: 58.6 in³/min
Material: S45C / Spindle speed: 80 rpm / Feed rate: 0.03 IPR / Depth of cut: 0.31"
Maximum workpiece weight: 6614 lbs
Output: 30 kW (40 HP) [40% ED] / Max. torque: 3655 N・m (2696 ft・lbs)
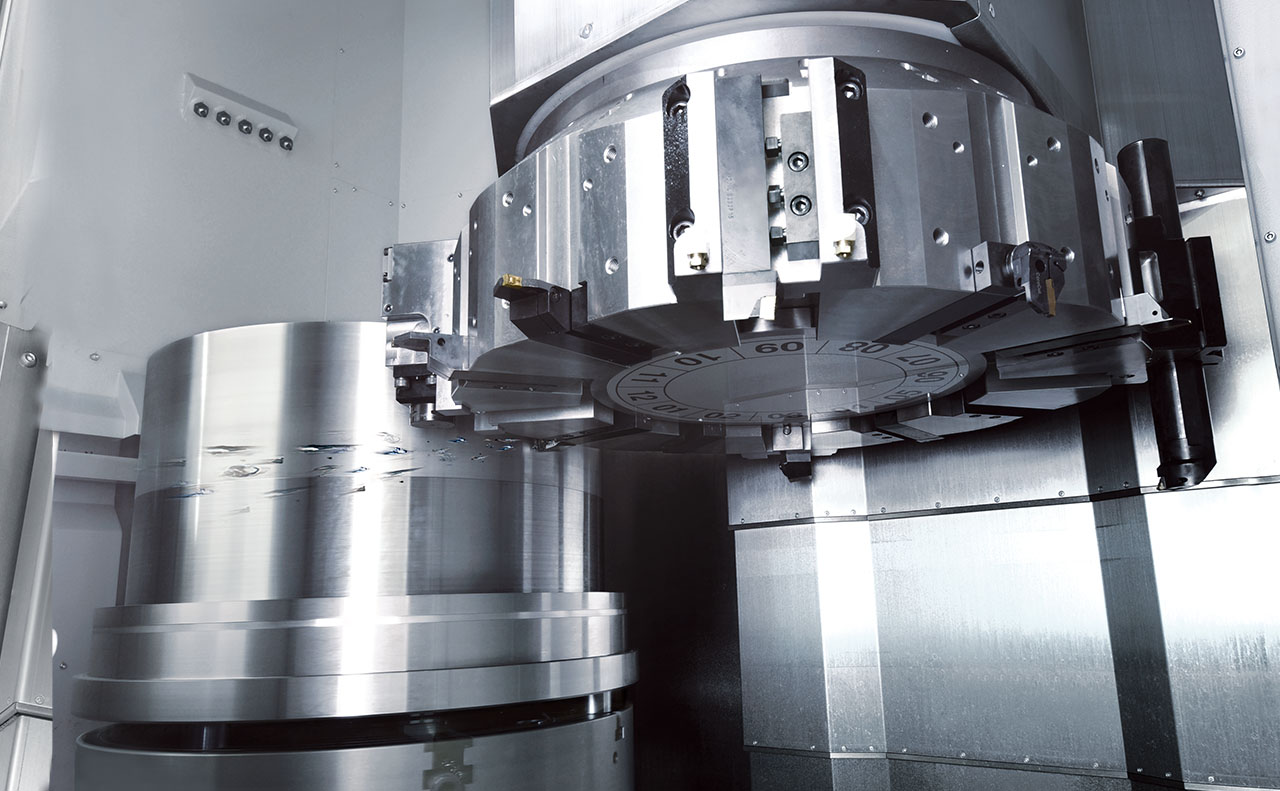
Process integration by high-speed turret lathe and milling performance
Turret for mounting up to 12 tools
The turret is rigidly clamped by a high-index coupling for high-performance machining including intermittent cutting. Tool interference with the workpiece by adjacent tools is minimized, enabling stress-free tool setup.
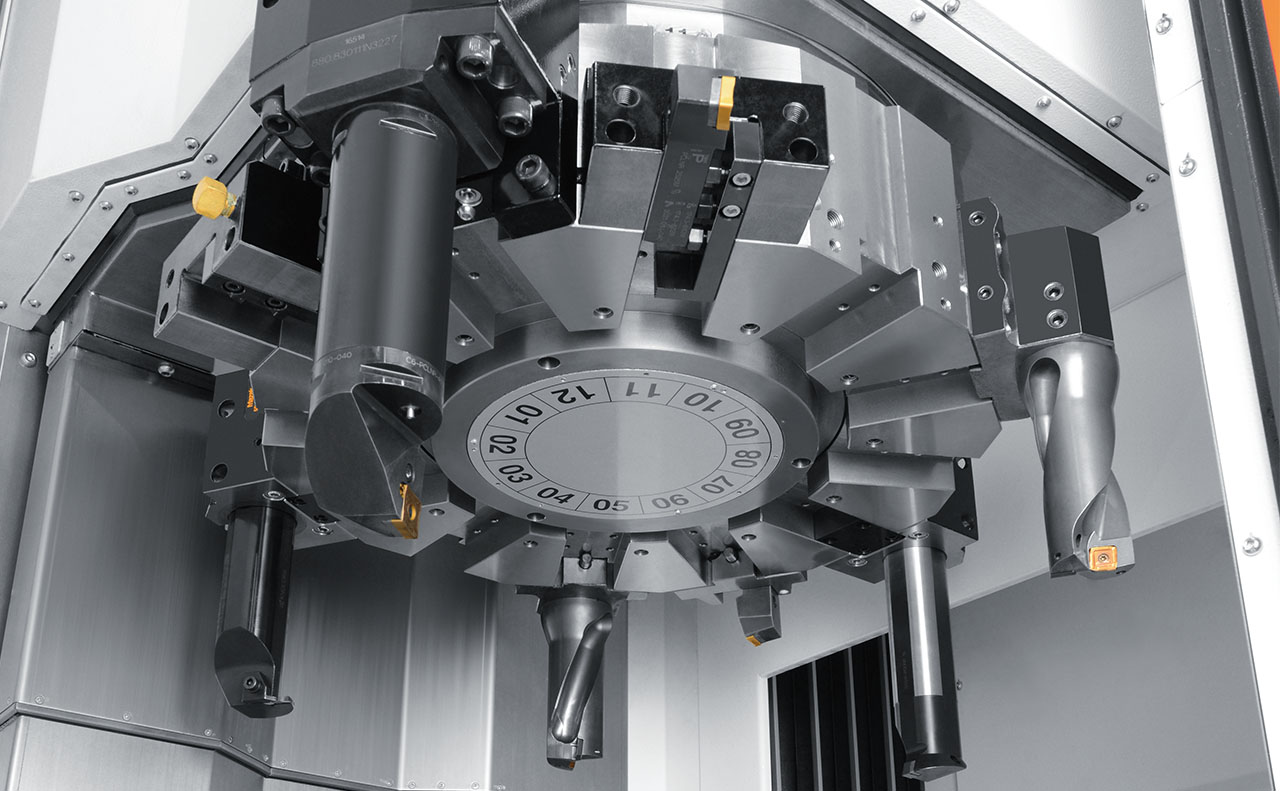
Milling performance for process integration
The MEGA TURN series can combine turning and secondary machining operations for large workpieces such as those found in the construction and aerospace, and other industries. This contributes to greatly reducing production lead time.
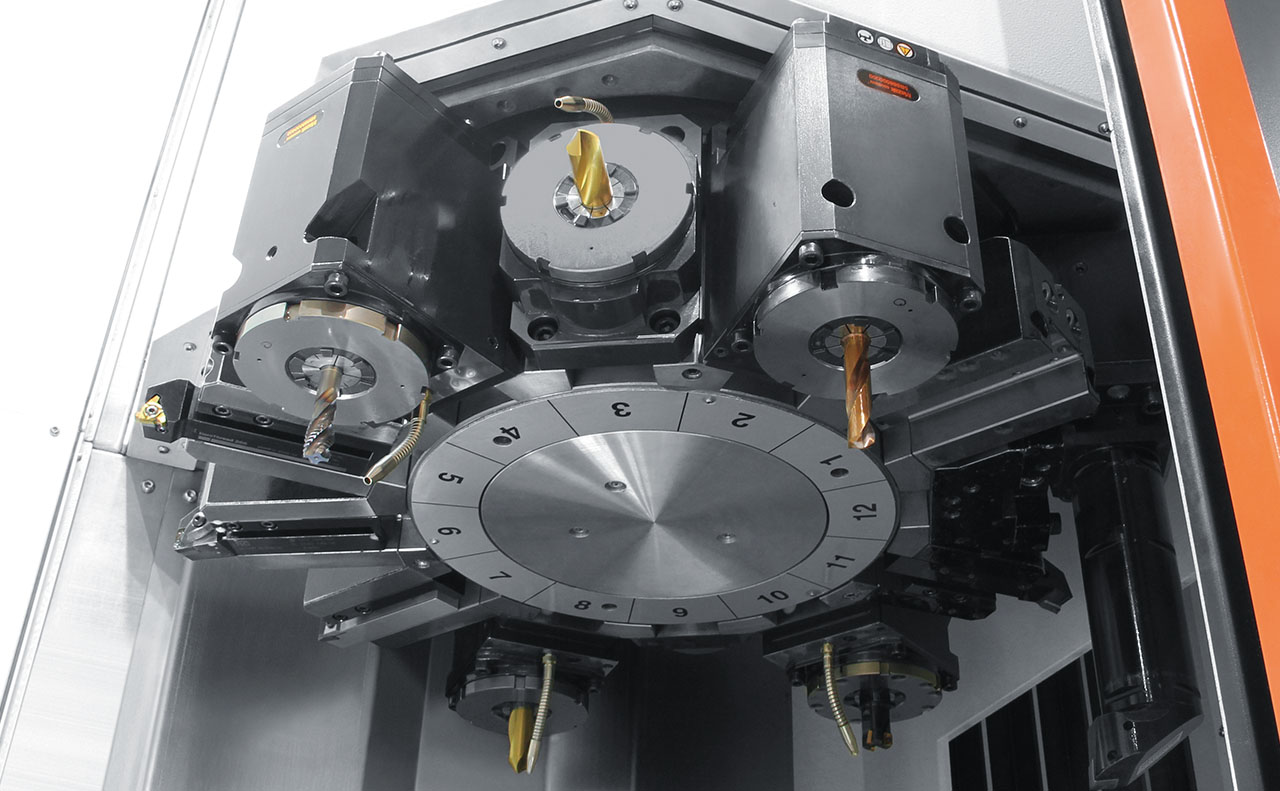
Automatic Tool Changer for increased productivity (Option)
Automatic tool change to prevent interference with workpiece
To eliminate the reduction in the number of tools due to interference between the boring tool and the workpiece, we have developed an unique automatic tool changer. It can recall tools from adjacent tool magazines when necessary, so not only can the interference be eliminated, but it also allows for full tool mounting, which greatly reduces setup man-hours.
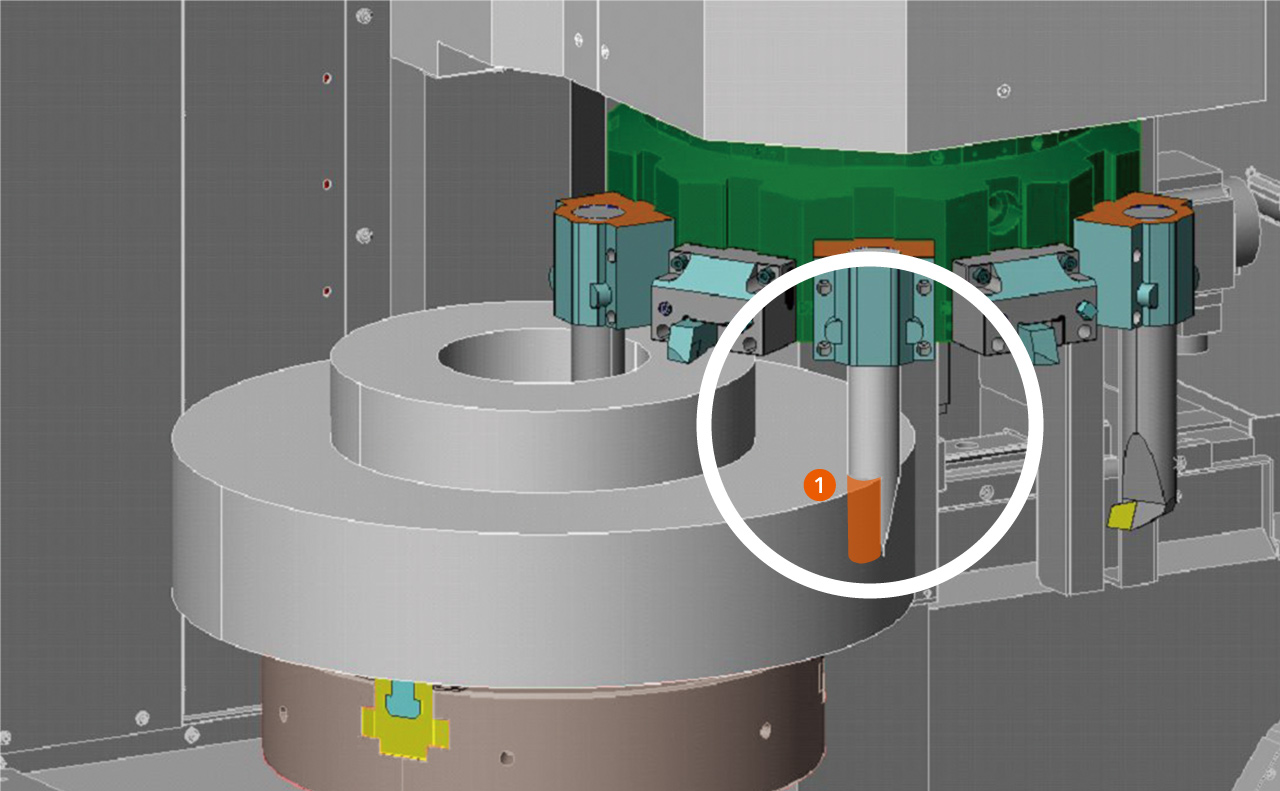
Tool interference occurs
(No automatic tool changer)
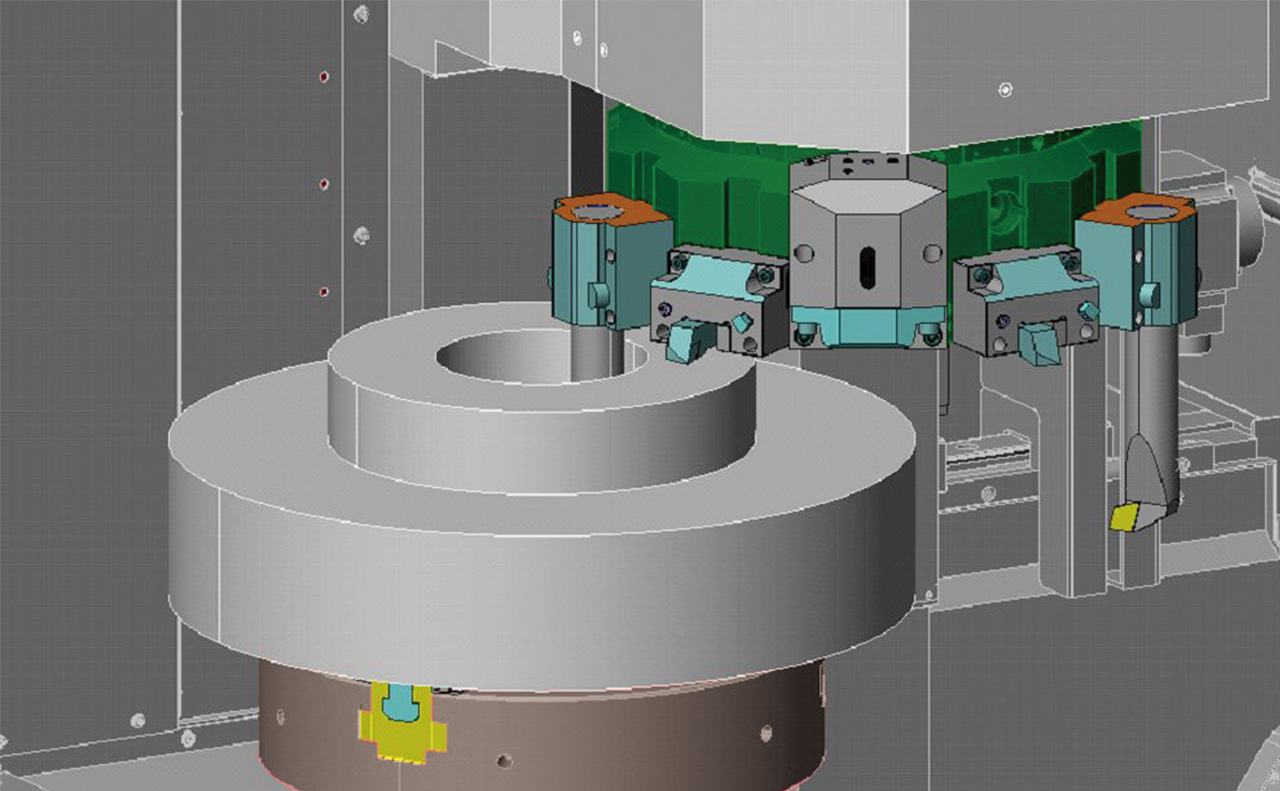
No tool interference
(Automatic tool changer equipped)
Variety of selection to suit your production system
2-pallet changer for reduced setup time and long continuous machining, available with mirror-image versions for efficient operation
2-pallet changer (900, 900M) (option)
Productivity is increased by the ability to setup the next workpiece during the machining of the current one.
Continuous machining capability of 1st and 2nd pallets ensures long-hour machining.
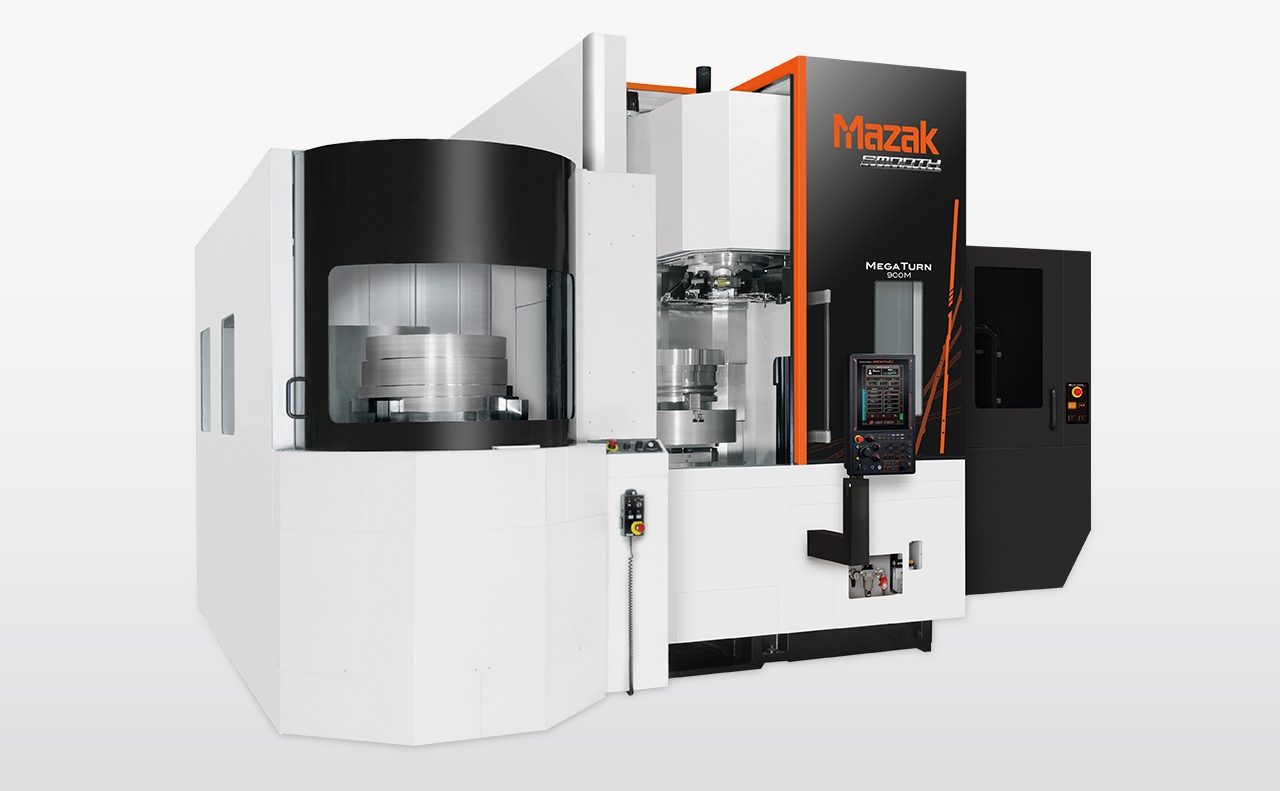
Mirror-image versions available to solve placement problems (except for 1600, 1600M)
Two machines can be operated by a single operator.
By combining mirror-image versions with standard version machines, the machine layout can be set up with a shorter traveling distance between machines, when only one operator is available for production (compared to installing two standard version machines).
Floor space can also be reduced.
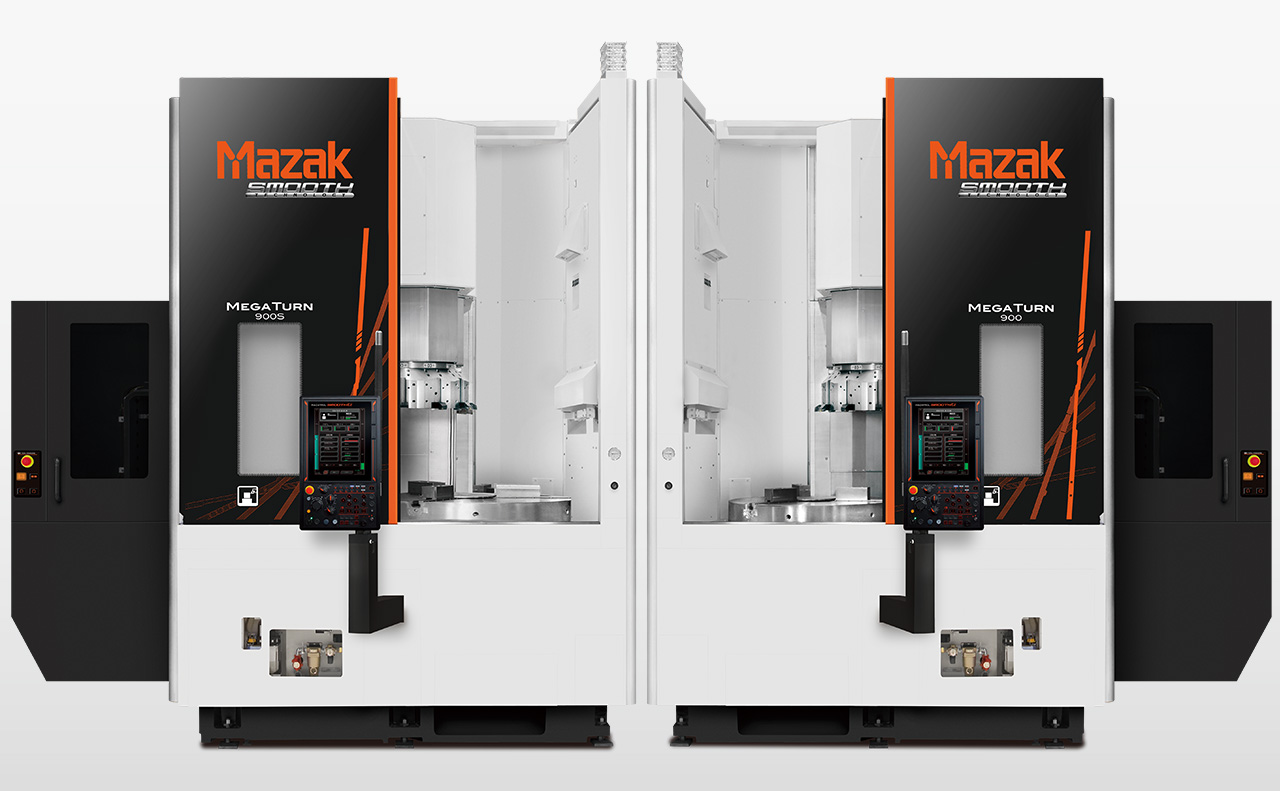
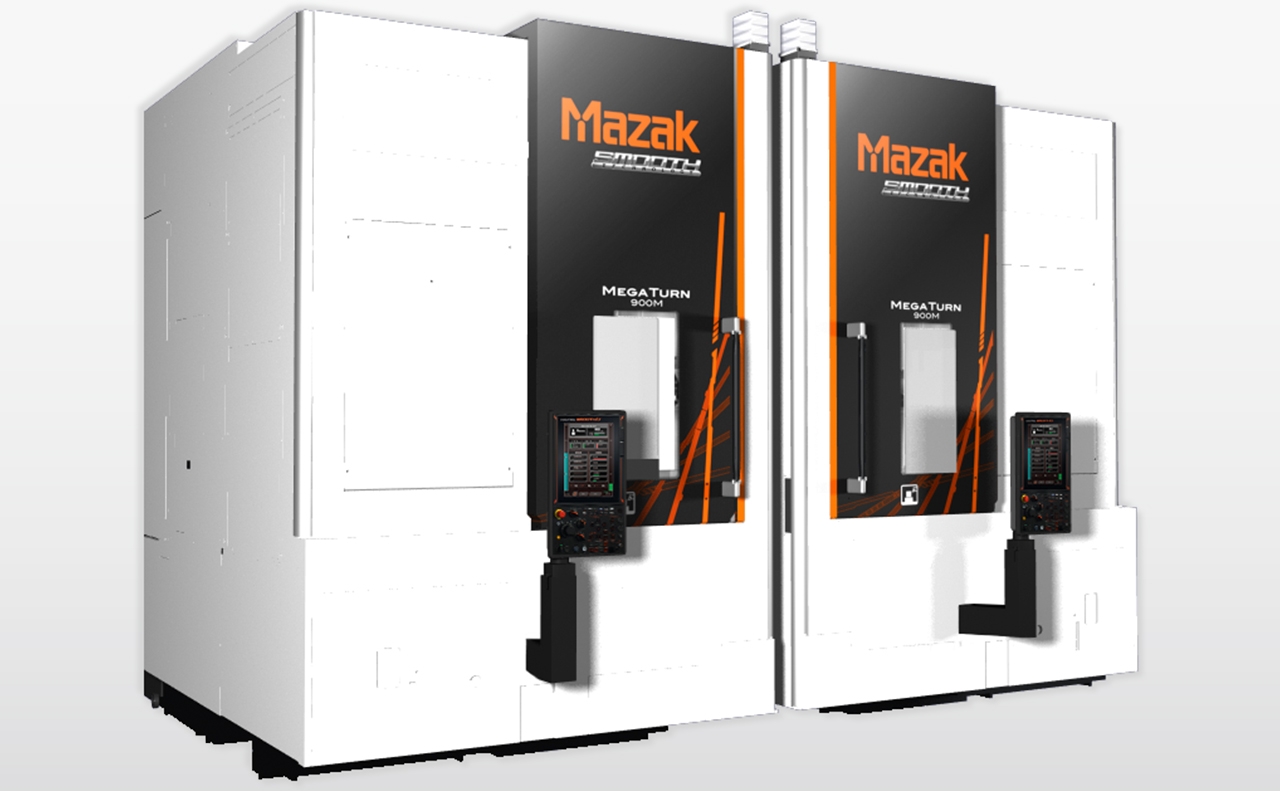
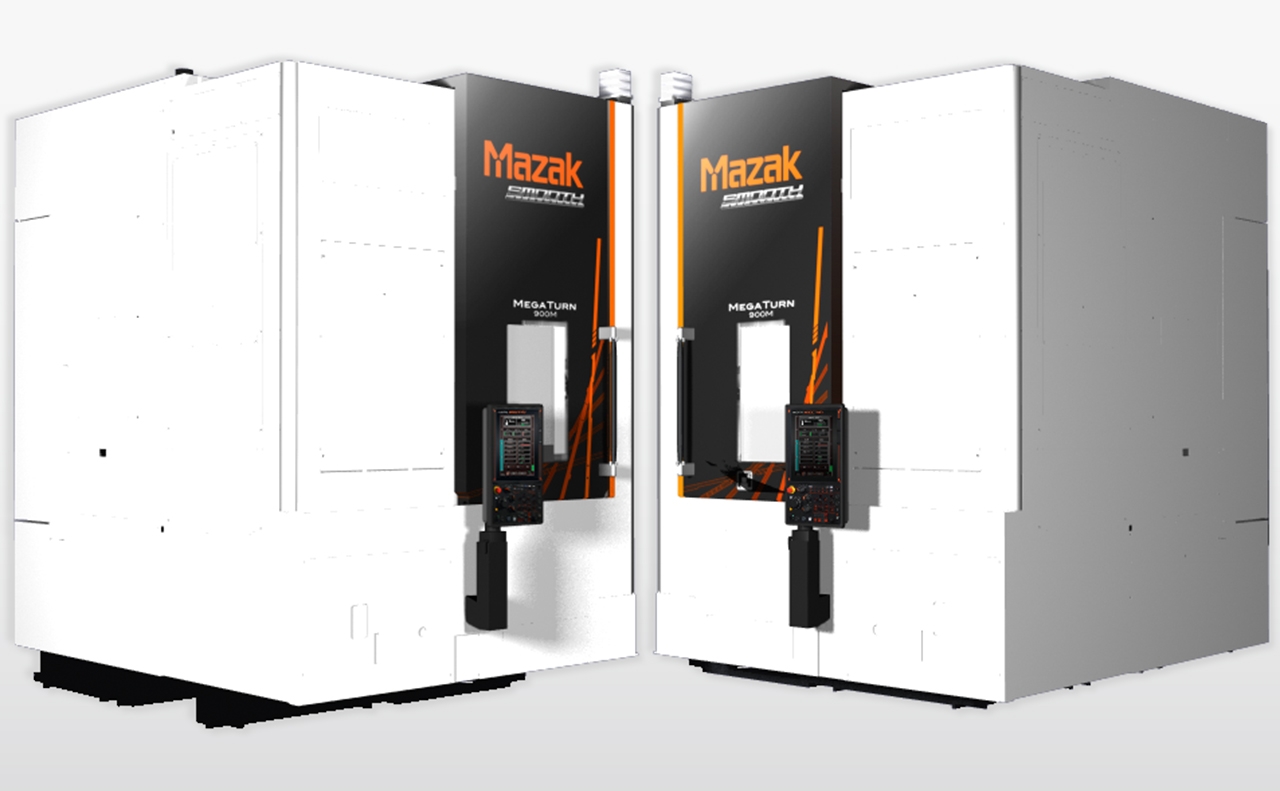
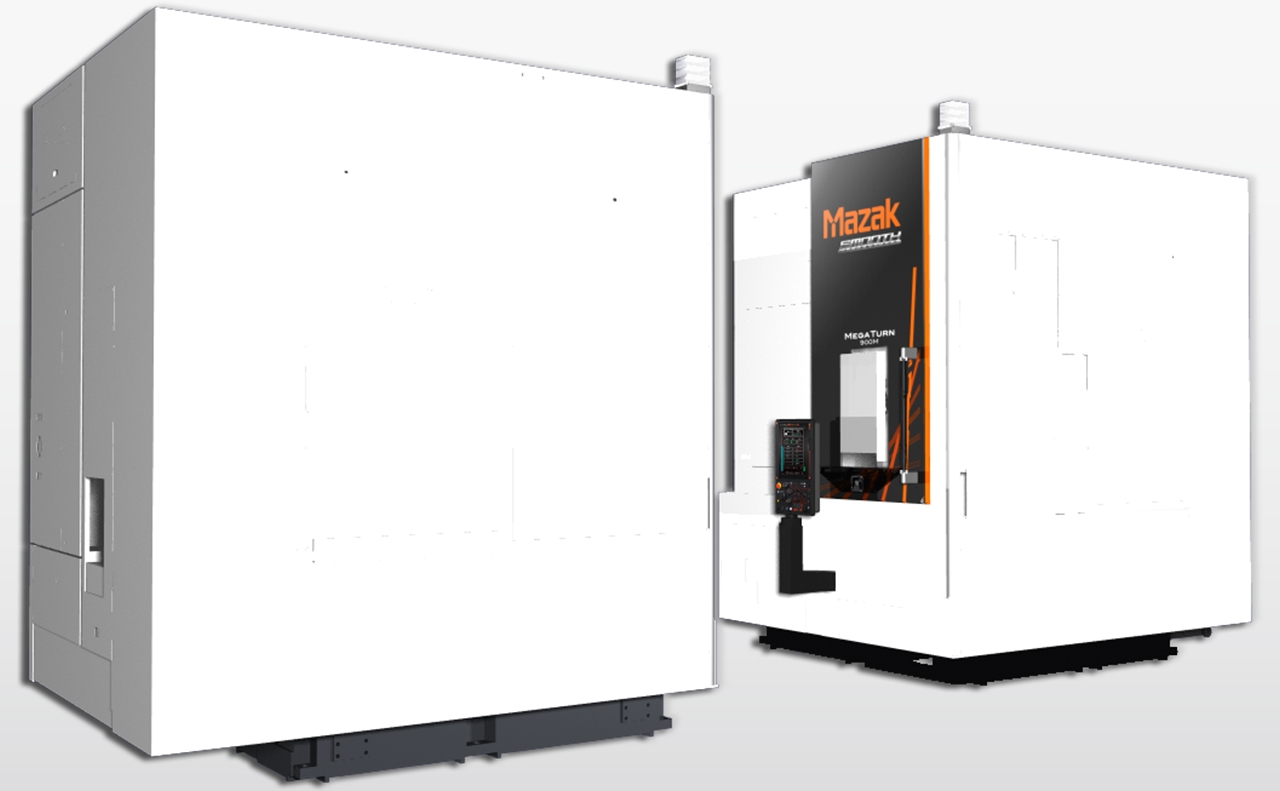