Chuck size | 6″ |
Max. machining diameter | Φ23.62″ |
Max. machining length | 23.23″ |
Y-axis travel | 8.27″ |
Multi-Tasking Machines
INTEGREX i-H
- The flat design of the machine body front greatly improves accessibility and linkage with automation systems such as articulated robots and stockers.
- Power increased spindle and high rigidity machine structure.
- Long Y-axis stroke for expanded machining capability
- MAZATROL SmoothAi for AI, digital twin, and automation

Enhanced machine design to easily incorporate automation
Flat design of the machine body front for easy adaptation to automation
The standard compact milling spindle is 17% shorter in overall length than the conventional milling spindle, increasing the machining area with minimum interference. X-axis and Y-axis strokes are expanded to secure large machining areas.
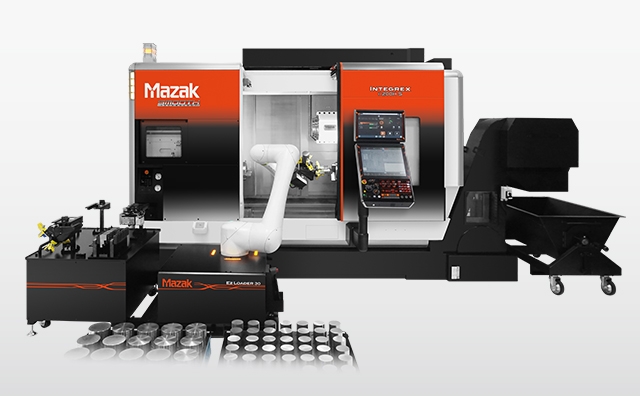
Machine construction for high-accuracy machining
Based on structural analysis, the best machine structure combining turning centers and machining centers are designed to achieve stable, high-accuracy machining over the long term. High-accuracy machining is achieved over the entire Y-axis stroke.
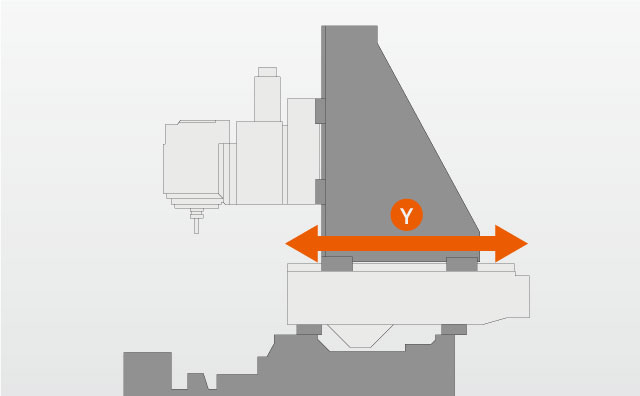
Compact milling spindle and large machining area with minimal interference
- 1: |16.93"
- 2: |Y-axis 11.81" (i-250H, i-350H, i-450H series)
Y-axis 8.27" (i-100H, i-200H series) - 3: |X-axis 27.36" (i-250H, i-350H, i-450H series)
X-axis 21.06" (i-100H, i-200H series)
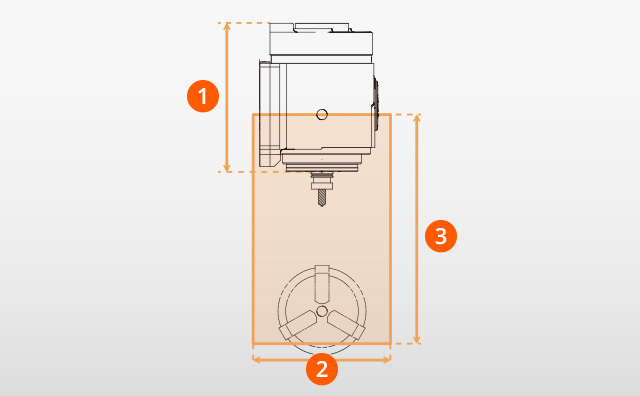
Stable high-accuracy machining
Ai Thermal Shield
Based on the spindle speed and temperature of the machine, Ai Thermal Shield suppresses changes in the cutting edge position. Stabilizes continuous machining accuracy through meticulous machine control that takes into account temperature changes, machine position, coolant ON/OFF, and other factors. Furthermore, by accumulating and learning data from subsequent measurements, thermal displacement compensation can be optimized for each machining environment to stabilize machining accuracy.
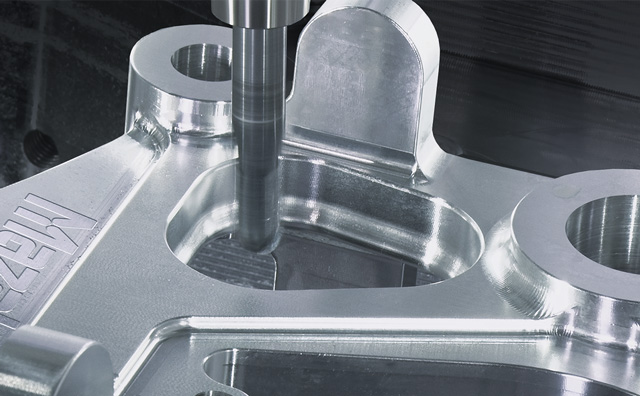
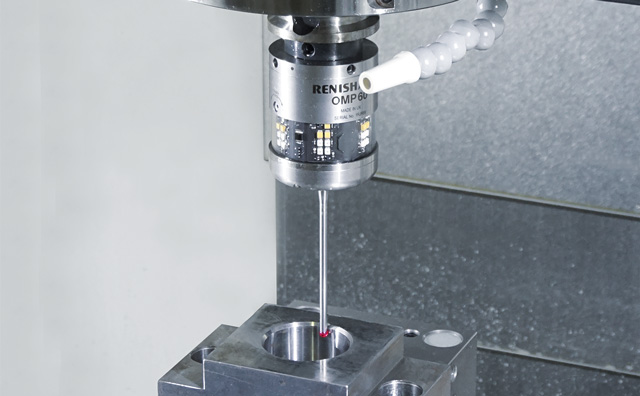
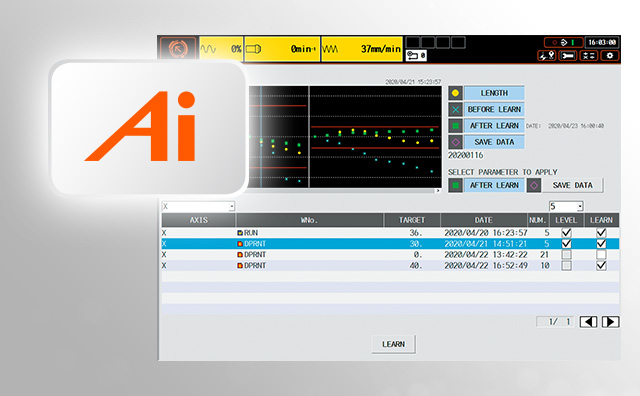
- Machining
- Workpiece inspection
- Simulation
Heat displacement control
- Spindle temperature control
Temperature-controlled cooling oil is circulated around the spindle bearings and headstock.
Thermal displacement of the spindle is suppressed to improve machining accuracy. - X-, Y-, Z-axis ball screw core cooling (Standard Specification)
Temperature-controlled cooling oil is passed through the inside of the ball screw to suppress heat generation and prevent loss of machining accuracy.
Automated systems for a variety of products and production volumes
Bar feeder*
Bar feeder can be installed to supply bar materials. The optional bar feeder scheduling function supports high-mix, low-volume production and set production.
* option
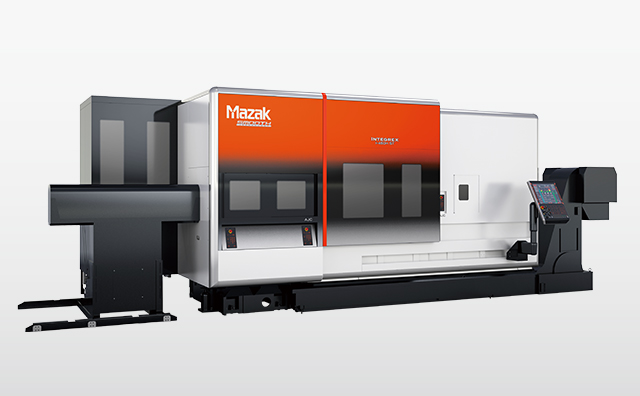
Ez LOADER*
Ez LOADER is a space-saving automation solution using a collaborative robot. It offers automatic operation without the need for extensive teaching, and customers can also customize their own operation patterns.
* option
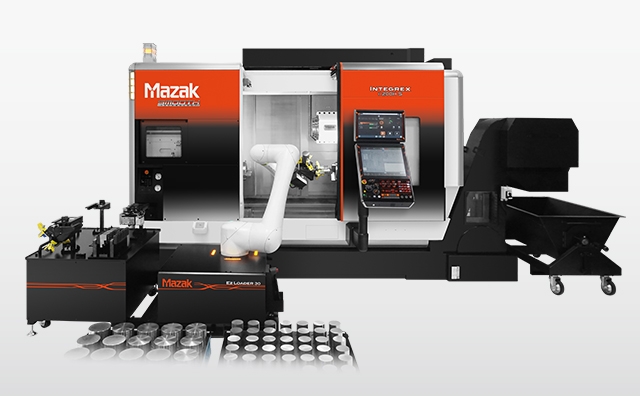
Mazak AUTO FLEX CELL*
A self-run type articulated robot and stockers are compactly arranged in the front face of the machine to automate various setup operations such as workpiece loading/unloading, chuck jaw supply, and special tool exchanging.
* option
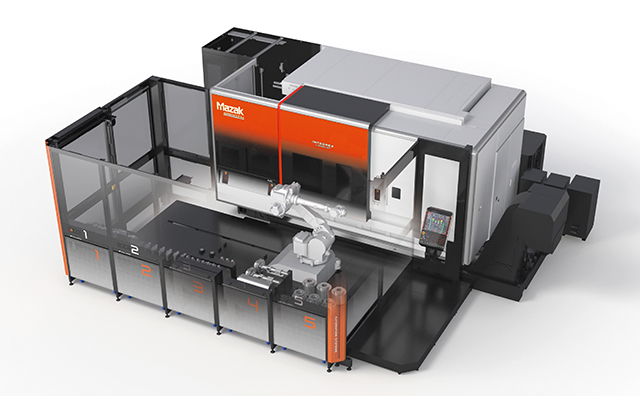
Auto Jaw Changer*
With auto jaw changer, 10 sets of chuck jaws can be automatically replaced for each of the main and second spindles.
* option
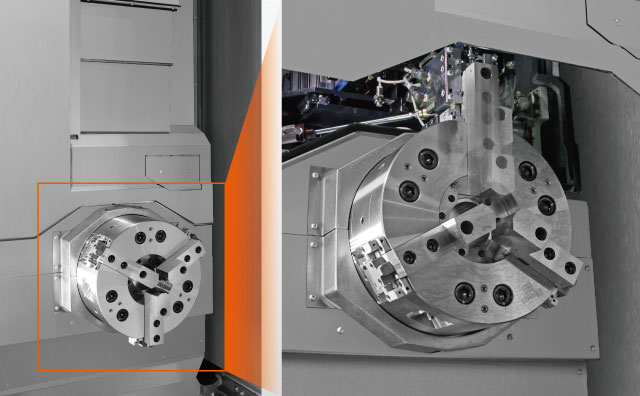
CNC system
Innovative MAZATROL CNC system for higher productivity
MAZATROL SmoothAi provides unsurpassed productivity through even faster and higher precision control while elevating your production with AI and digital twin technology.
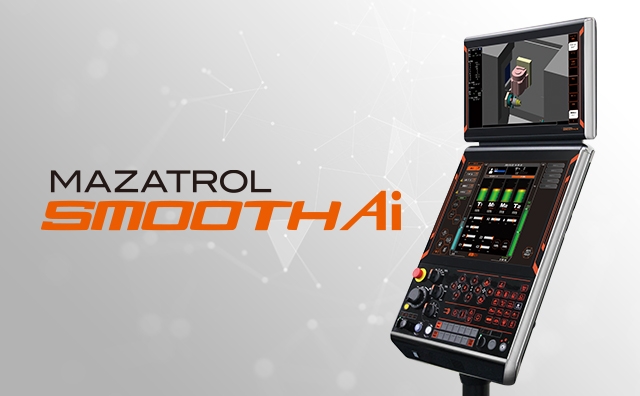
SOLID MAZATROL (Automatic programming)
MAZATROL programs are automatically generated from 3D CAD data. AI learns machining know-how from previously generated programs, automatically calculates the machining process, and generates the optimal program.

CUTTING ADVISOR
Machining simulation and visualization of the machining process based on the accumulated machining results helps optimize cutting conditions.
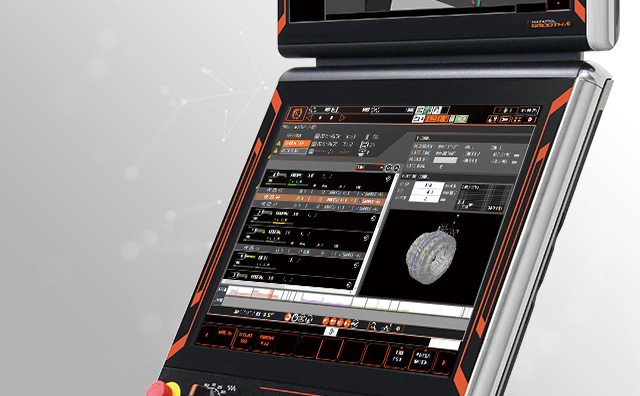