Application Areas
Application Areas for Mazak MegaStir Friction Stir Welding (FSW)
Since its invention, Friction Stir Welding (FSW) technology has become a critical part of joining applications throughout numerous industries. Mazak MegaStir works closely with customers in various industry sectors as a partner for the development of FSW tooling and programming solutions to achieve superior joins.
Key industry sectors benefitting from Mazak MegaStir FSW technology include electronics, aerospace, automotive, rail, oil & gas and marine.
Electronics – Mazak MegaStir
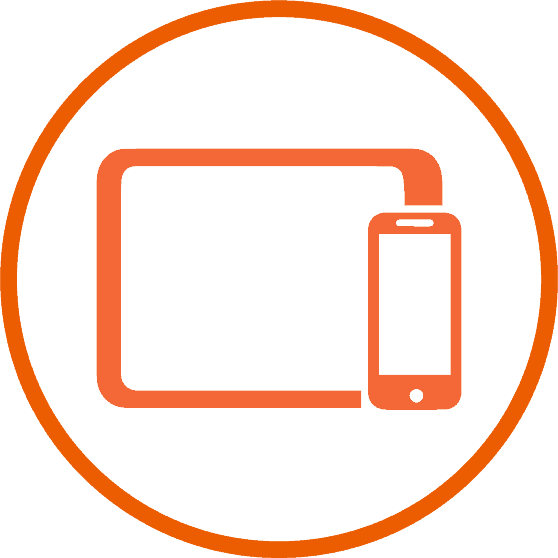
The electronics industry is one of constant change, and manufacturers continuously improve and evolve to control costs and integrate new technology that empowers that constant change. Following that same path of constant improvement, Mazak MegaStir continues to innovate and lead in in the development of FSW applications. The company has supported customers in this market segment on FSW applications involving materials from 0.030" to 0.5" in thickness.
Friction Stir Welding provides unique process characteristics that are unlike any other joining technology.
- Low heat input yields virtually no distortion on assemblies to minimize the need for post-weld cleanup or machining.
- Internal components sensitive to elevated temperatures experience less heat exposure.
- Manufacturers maximize floor space and achieve highly efficient single-setup operations through the combination of subtractive and joining technologies within a single machine tool platform.
Aerospace – Mazak MegaStir
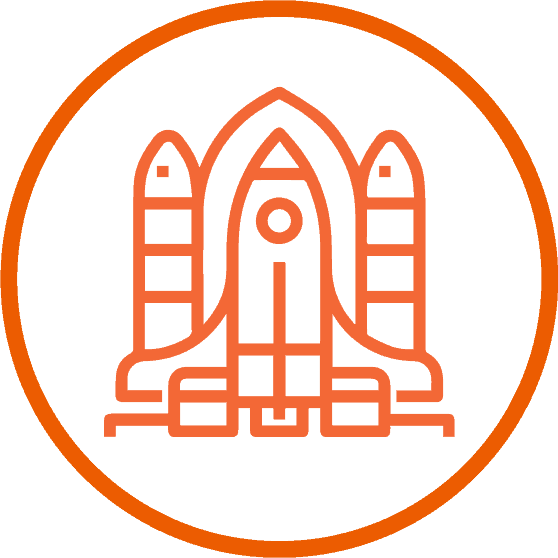
Aerospace manufacturers pioneered Friction Stir Welding (FSW) technology in the late ’90s, realizing its value in time-savings and in the reduction of weld defects when producing large aluminum structures. The technology also offers a better solution for the constant struggle with strength-to-weight ratio for aerospace components and assemblies.
Weight reduction through FSW translates to greater payload capabilities; a reduction of the slight weld distortions over a given length that typically occur with competing weld technologies; and significant increases in propellant volume. The results are aircraft capable of higher speeds and/or reduced fuel consumption.
FSW continues to evolve along with the materials designed to improve vehicle performance, and its ability to join dissimilar materials makes FSW a critical process. Mazak MegaStir continues to improve the process and open doors for its customers to implement and explore new applications for FSW as they build the aircraft of the future.
Practically every launch vehicle manufacturer in the government or private sector relies on FSW in several key applications:
- Cryogenic fuel tanks for space vehicles
- Aviation fuel tanks
- External throw-away tanks for military aircraft
- Military and scientific rockets
- Wings, fuselages and empennages
- Repair of faulty welds
Automotive – Mazak MegaStir
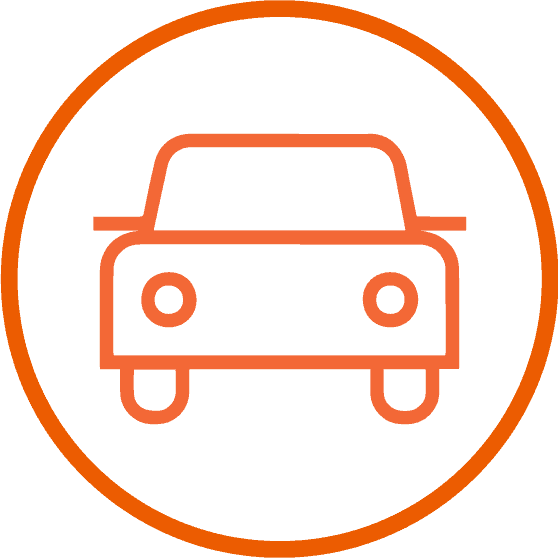
As the automotive industry increases its use of aluminum to help improve fuel efficiency, FSW offers many potential benefits. In contrast to most other joining processes, FSW handles the variations inherent in high-volume production while simultaneously providing improved mechanical properties. The process delivers distinct benefits and cost savings superior those of other welding alternatives.
With pressure to development greener, more fuel-efficient vehicles capable of meeting increasingly strict fuel economy standards, automotive manufacturers must engineer lighter, more efficient car bodies. FSW allows these manufacturers to easily avoid problems such as the porosity in casting assemblies, which creates significant scrap due to frequent defects. Instead, FSW passes through affected areas to resolve defects and improve material properties with a more refined gain. Joining thinner high-strength automotive steels, aluminum and magnesium alloys, automakers can reduce weights far below what was once thought possible.
Automakers turn to FSW technology for several applications.
- Joining similar and dissimilar materials
- Welded blanks for passenger doors or liftgate sheet panels
- Wheel assemblies
- Bumper beams
- Crash zone/stiffening boxes
- Suspension systems
- Drive shafts
- Intake manifolds/cylinder heads
- Batteries, battery trays and vehicles, especially hybrid and electric models
Rail – Mazak MegaStir
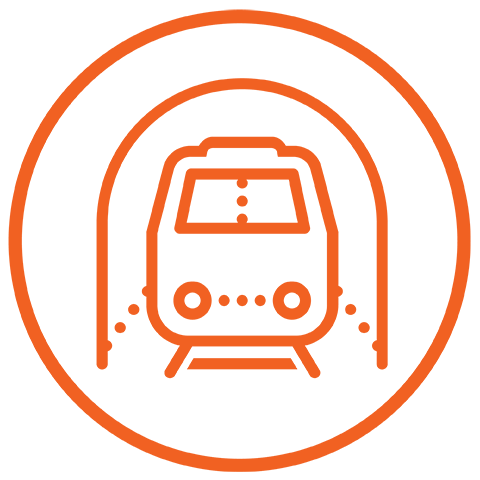
To meet the growing transportation needs of countries around the world with the least possible environmental impact, the rail industry has worked to improve the efficiency of car designs. As a result, suppliers are evaluated on their ability to provide efficient solutions while meeting the national and international safety standards. To achieve this, many railcar companies have turned to FSW and use it to create car bodies with extrusions designed for stiffness and lightness without any sacrifice in the ability to endure the long service life required for rail applications.
Several FSW benefits allow railcar suppliers to optimize processes and stay ahead of the competition include.
- Increased joint efficiencies
- Reduced post-weld clean up
- Higher processing speeds
Oil & Gas – Mazak MegaStir
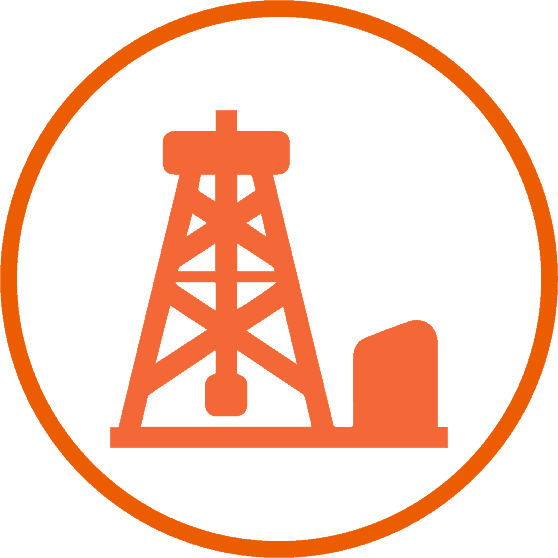
With a long history in the oil and gas industry, Mazak MegaStir assists customers with welding applications for petroleum-grade steel, nickel and stainless alloys. Constructed and installed both onshore and offshore, pipelines can require welding applications that range from 12" to 42" in diameter, with wall thicknesses up to 1.75" thick. With FSW, oil and gas industry suppliers can handle walls up to 1.25" thick while also minimizing defects.
For down-hole drilling and service equipment, FSW enables the joining of dissimilar high-temperature or high-wear alloys. It does so with a single-pass thermoplastic joining process that reduces or eliminates post-weld heat treatment.
Mazak MegaStir high-temperature FSW tools benefit oil & gas production.
- Endure the elevated temperature of the process and harsh environment
- Leave behind minimal defects
- Single-pass welding for industry-leading efficiency
Marine – Mazak MegaStir
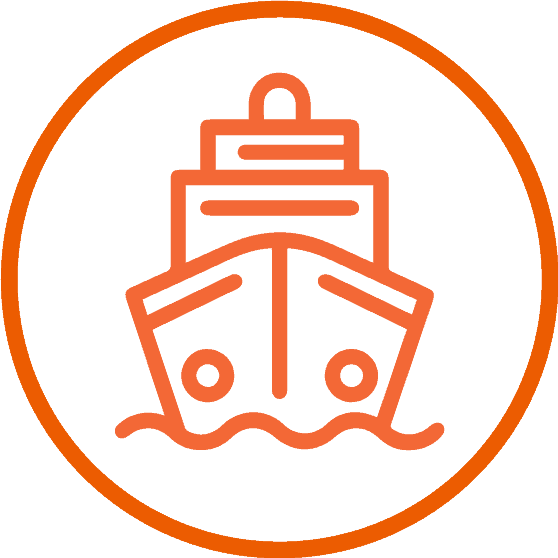
The need for lightweight and more efficient ships requires shops use FSW technology to develop creative aluminum extrusions into panels for several different seafaring applications. The low heat input minimizes stress and creates a superior microstructure, minimizing distortion and eliminating the need for further operations to improve flatness or remove defects.
FSW is used worldwide in commercial and military shipbuilding and marine component applications ranging from aircraft carriers to fishing boats.
- Panels for decks, sides, bulkheads and floors
- Hulls and superstructures
- Helicopter landing platforms
- Marine and transport structures
- Refrigeration assemblies
Panel producers optimize their shipbuilding operations using Mazak MegaStir FSW.
- Extruders take advantage of smaller presses to create large assemblies previously available to only large companies with massive presses and complicated/expensive dies
- FSW replicates the forging process more closely than the welding process and generates superior joints in environmentally friendly conditions
- With post-weld dimensional accuracy and superior weld quality, FSW joints replicate the base material and its characteristics
- FSW eliminates weld distortion and post-weld correction processing to improve profitability
Panel producers benefit from FSW panels.
- Parts produced with FSW have a high degree of completion, with few, if any, post-weld processes required
- Exceptional repeatability guarantees a uniform level of performance and quality with very narrow tolerances
- Flexible production equipment permits customized solutions without compromising delivery reliability
- The completed panel units have been inspected and approved by classification authorities such as DNV GL, RINA and Lloyd’s Register
- The panels’ high degree of straightness ensures easy assembly at the yard, reducing the need for manual welding
- Outstanding build quality results in level floors and easy preparation for floor coverings, thus creating less supplementary work by the customer for major cost savings