Chuck size | 8″ |
Max. machining diameter | Φ12.6" |
Max. machining length | 5.91" |
CNC Turning Centers
DUAL TURN 200
- Symmetrical 2-spindle / 2-turret structure
- Simultaneous machining on both spindles and automatic transfer from first to second spindle enables continuous machining
- 30% reduction in floor space compared to two 2-axis CNC turning centers of the same class
- Considering dead space between machines, work-in-process storage, maintenance areas, and chip conveyors difference in space becomes even larger.
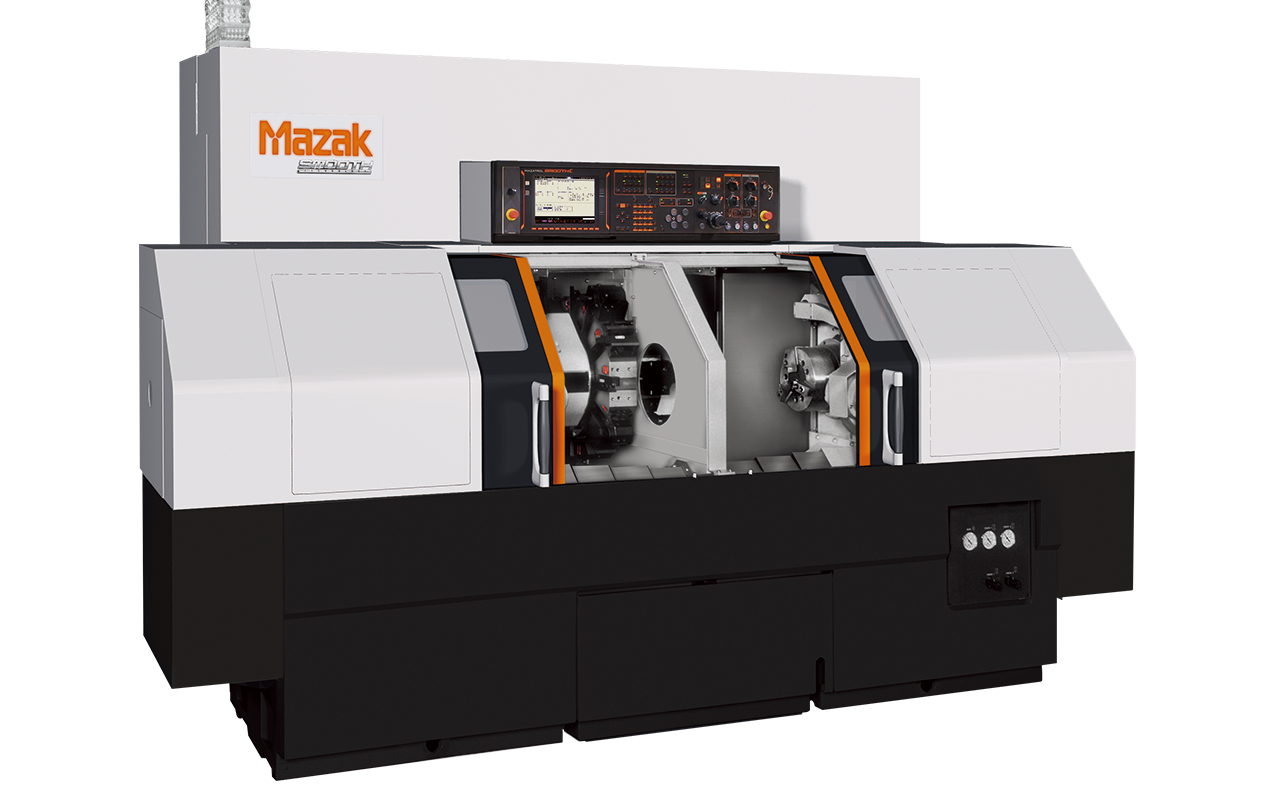
Symmetrical structure for productivity
Symmetrical spindle and turret
Two spindles / turrets with the same machining capacity are equipped on both sides of the structure. The built-in motor spindle ensures high-accuracy machining at all revolution ranges, from low speed to high speed. With the non-lift rotary indexing, high speed turret clamping / unclamping can be performed with minimum interference.
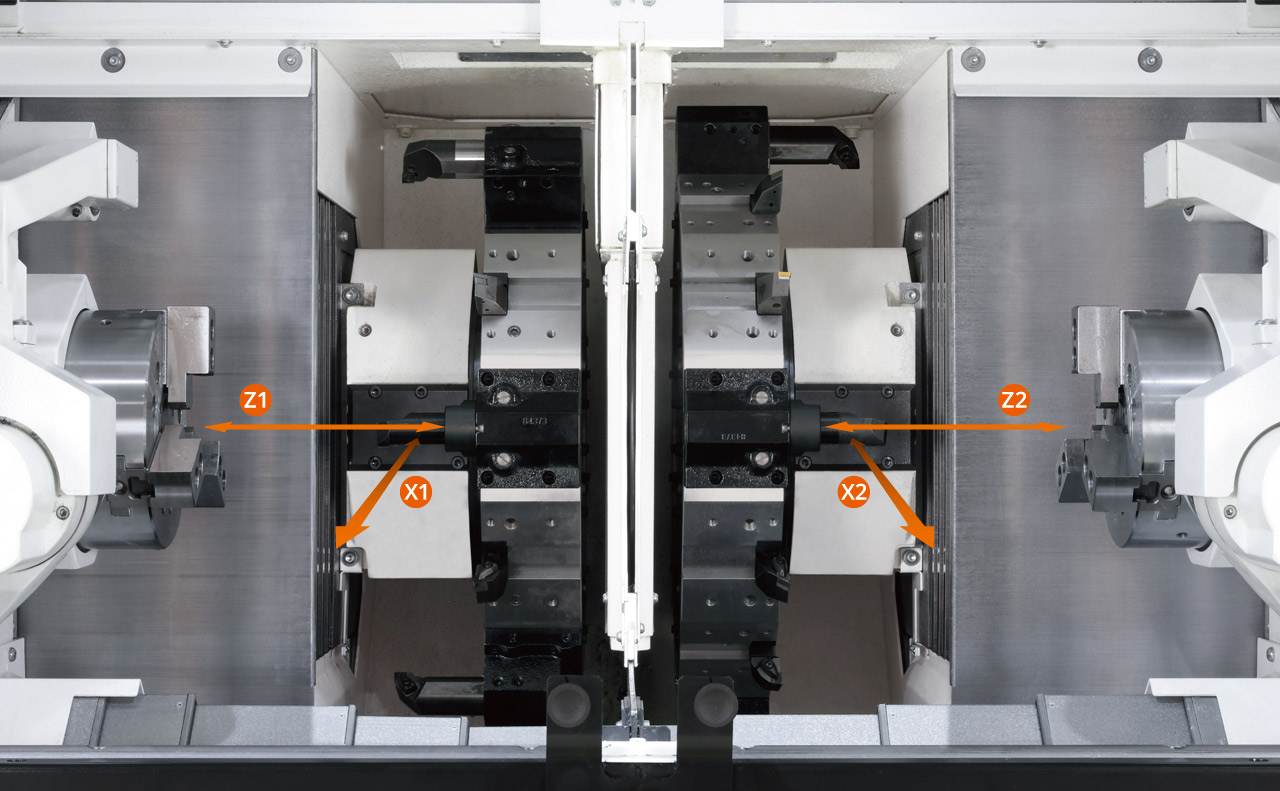
Continuous machining with automatic workpiece transfer
High-speed, high-accuracy automatic transfer function can make highly efficient OP1 and OP2 continuous machining with a single chucking operation possible.

Automatic partition for independent machining in both areas
Complete separation of the machining area prevents chips and coolant from scattering from the other side. It is possible to machine the left and right side separately, or to replace one workpiece while the other is being machined.
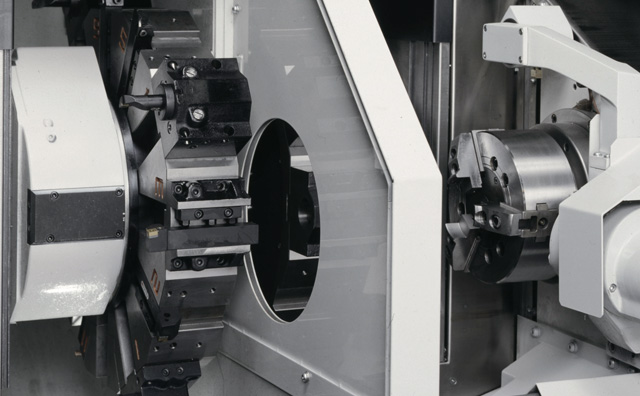
High productivity and space-saving
No in-process inventory due to process integration
Automatic transfer integrates the machining of OP1 and OP2 of the turning process. This will eliminate in-process inventory for machining workpieces.
Significantly improved productivity per area (reduced floor space)
Floor space can be reduced by 30% compared to two 2-axis CNC turning centers of the same class. (Compared with our products)
It significantly reduces the operator's walking distance and workload.
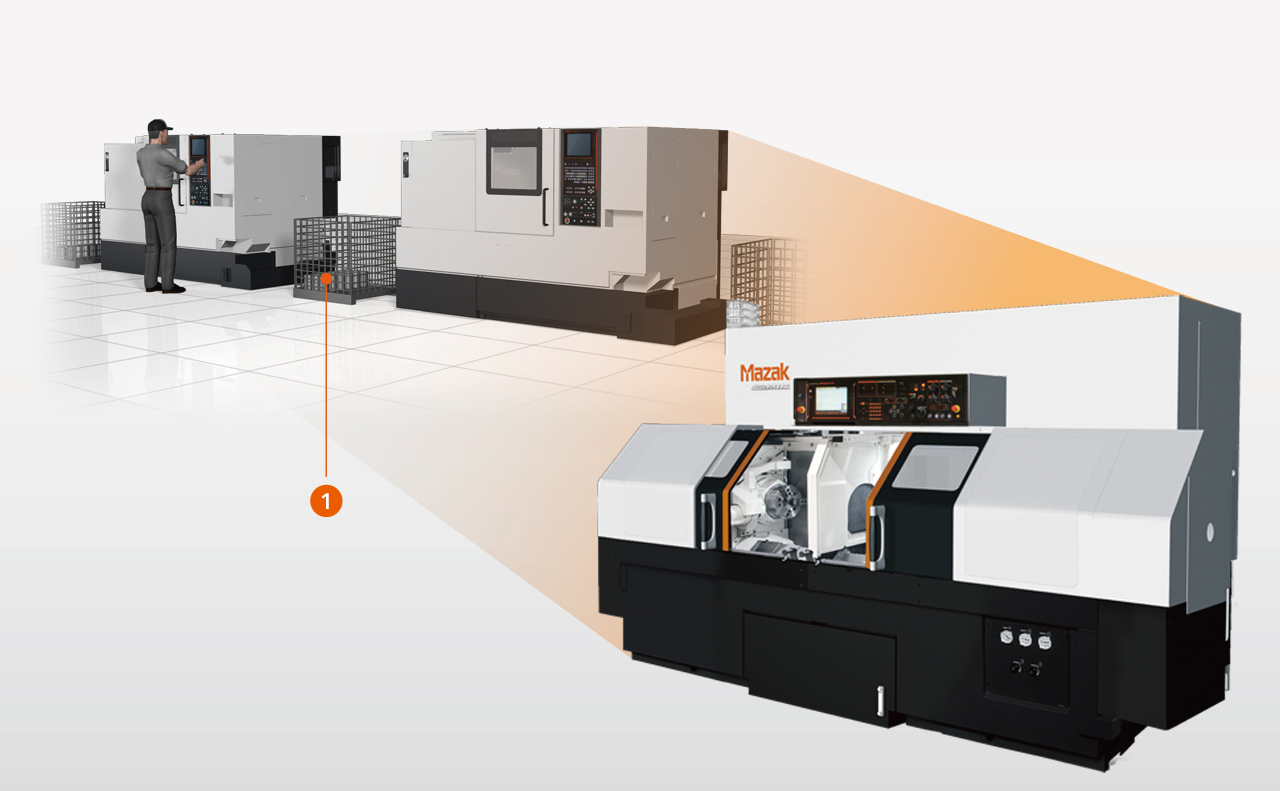
Various automation options to match your production style
Automatic unload system
The basic system is equipped with a workpiece unloading device, which can unload the finished product workpiece to the receiving table, simply by attaching the material to the chuck of the main spindle.
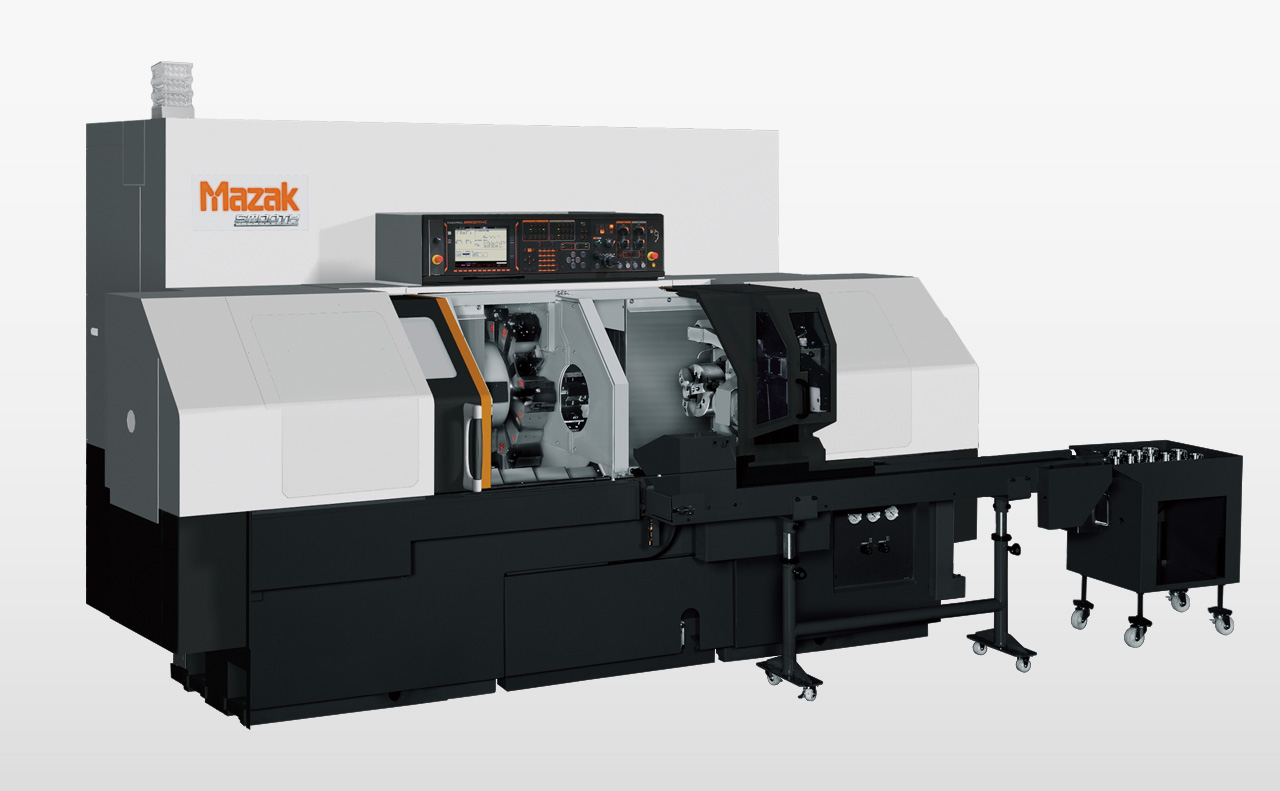
Bar Feeder + Unloading hand
Bars are automatically fed by bar feeder, and finished products can be unloaded by the unloading hand.
Bar work capacity: 2.56"
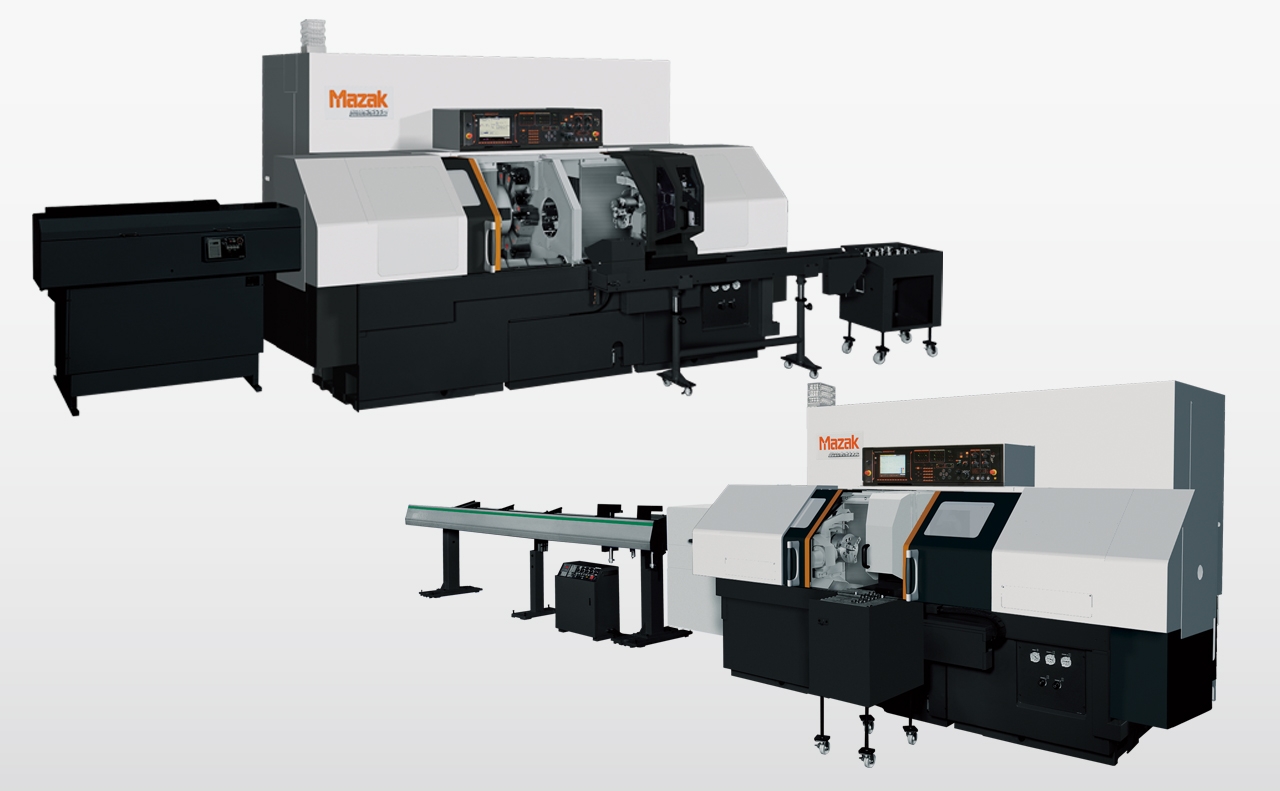
Gantry Loader system
Automatic and continuous machining from OP1 and OP2 processes for chuck / shaft workpieces can be performed. The material is automatically loaded in the machine and the finished workpiece unloaded by the gantry robot.
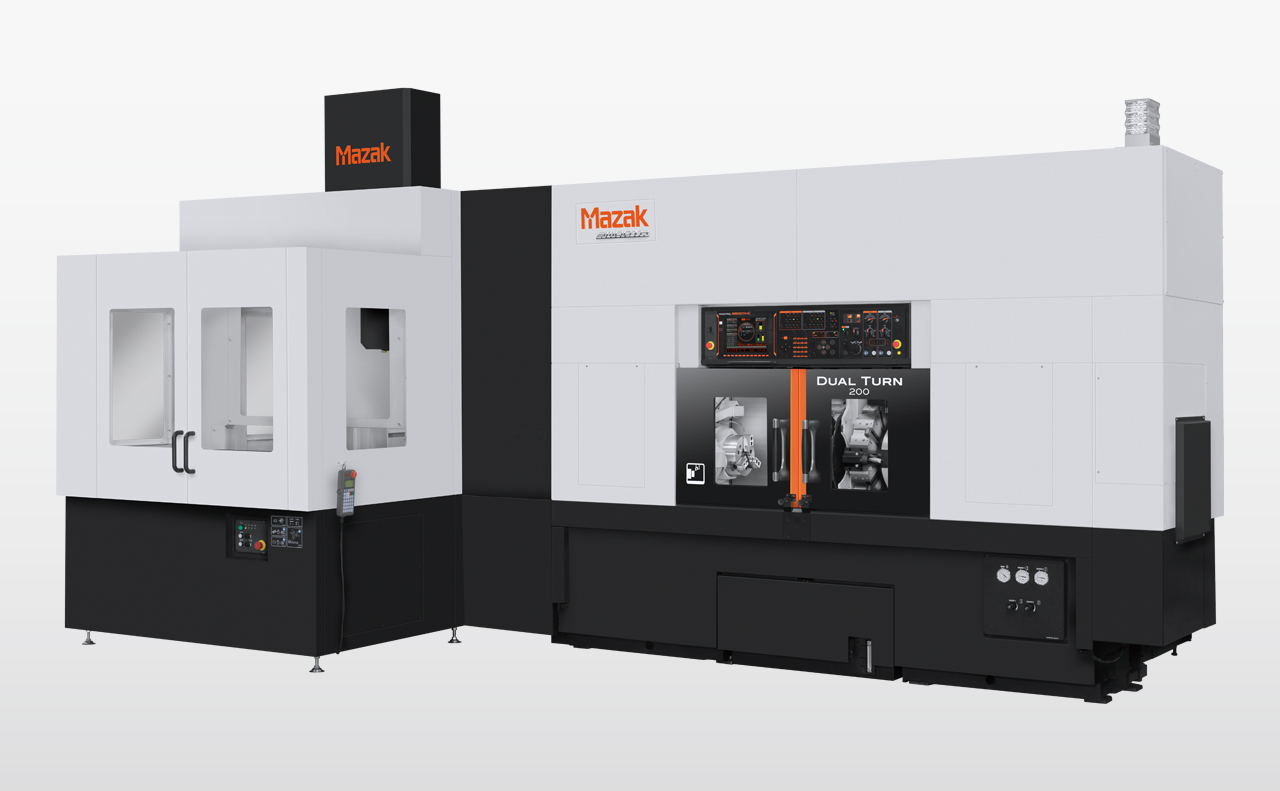
Gantry loader (2-pallet workpiece conveyor) reduces workpiece loading/unloading operation time* by 20% compared to previous systems.
*Internal machine operation time
Previous Gantry Loader : 25.1 sec → GL-100 : 20.7 sec
Faster traverse speed : A-axis 3937 IPM, B-axis 7087 IPM
Faster workpiece loading / unloading : Improved workpiece seating in chuck by feeding headstock against workpiece
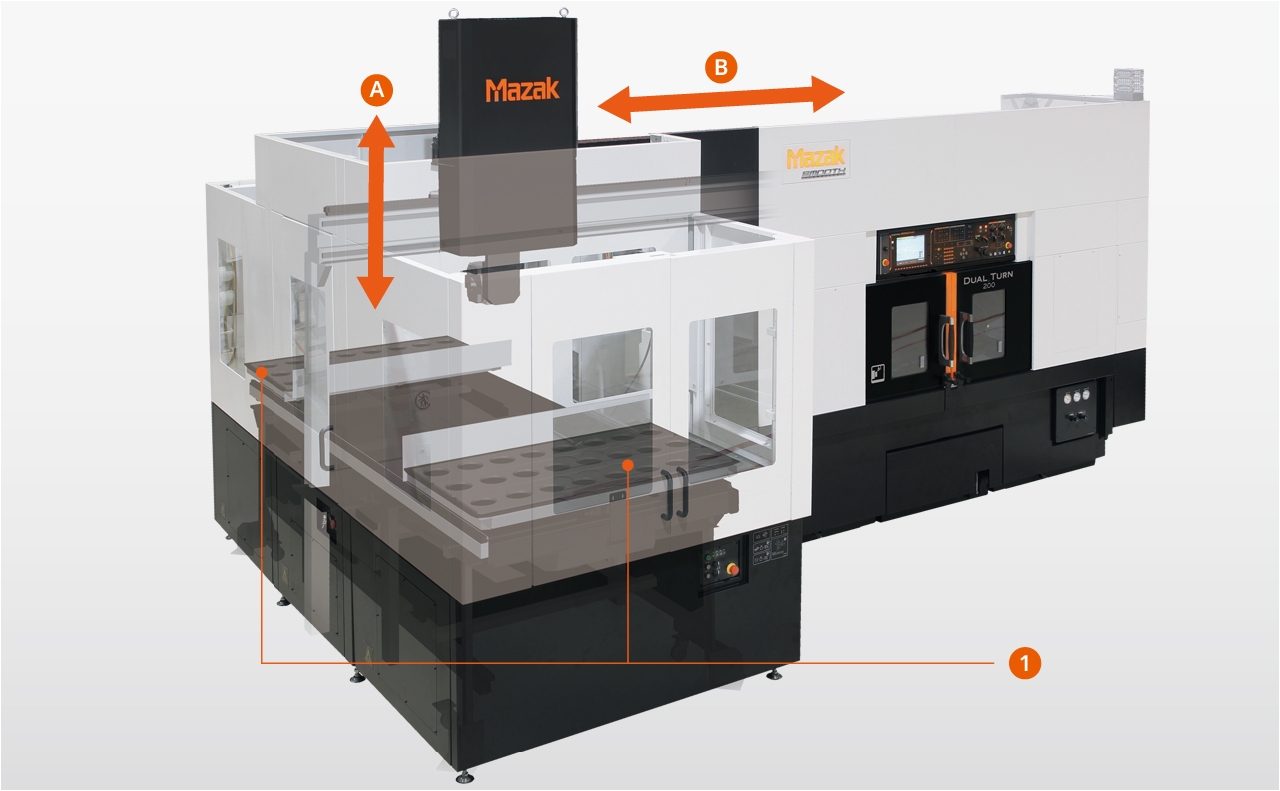
Ease of programming by MAZATROL conversational programming
75 % reduction of setup time for the first workpiece
Setup of the first workpiece from programming to tool path check, tool setup, and work coordinate setup can be conducted in a very short period of time. Compared with other CNC systems, setup of the first workpiece can be reduced by as much as 75 %.