Machining Centers Help Shops Increase Output, Reduce Inspection Times
Deep in the heart of Texas (Weatherford to be exact), Frankenstein Engine Dynamics (FED) manufactures some of the best custom engine parts used in the professional auto racing industry. The company has an excellent reputation for what it does, and its components are well-known for their quality, impressive designs, and outstanding performance. From the time FED opened its doors in 2005, the company’s products have met the racer’s need for speed. By 2015, FED cylinder heads, intake manifolds, and engine kits were in such high demand that the company desperately needed to rev up operations and expand, or lose out on a great growth opportunity.
In 2016, after conducting diligent research and taking on several partners, FED’s owner and CEO, Chris Frank decided to build a new 20,000 ft2 (1858 m2) facility, hire a talented team and incorporate advanced full five-axis machine tool technology that would accelerate production speeds without sacrificing part quality. These smart investments have paid off, and the company is on track for record growth as revenues consistently increase each quarter.
FED first gained a name for itself in the top range of the racing industry, creating cylinder heads for top-fuel dragsters going to NASCAR clients. It didn’t take long for drivers and crew members to notice that FED’s products exhibited outstanding craftsmanship and provided superior performance. From the beginning, Frank’s goal has always been to build engine parts that outperform and outlast anything else out there. He began with a very high level of racing clients with much faster cars and more money to invest in extremely expensive components.
As bidding began, the company realized that machining the parts in basic turning centers would be too costly. In Tolerance COO John Renning says, “We would have been nowhere near the competitive price we needed to win the work and still be profitable. The job would have had to run on basic turning centers and would have required two operations, along with two first-piece inspections and a final-piece checkout.” The extra time caused by additional setups and inspections would translate to a higher bid, potentially losing the job.
Instead, the company turned to the HQR-150MSY multitasking machine from Mazak Corp. (Florence, Kentucky). “The machine’s speed, multitasking machining capabilities and unattended operation was what won the job for us,” Mr. Renning says.
The HQR-150MSY is a two-spindle, two-turret machine with milling and Y-axis machining capability. Each of its turrets holds 12 tools and can work at either the machine’s main or second spindle. The machine performs high-precision coordinated hand offs from its main to second spindle with an accuracy of 0.0001 inch, says machinist Shawn Flannagan.
“We have to hold part-feature orientations from first operations to second operations,” he explains. “The HQR-150MSY can machine all these features and maintain known part location. So, when the main spindle hands off to the second spindle, it orients the part prior to the hand off so the known part position is maintained in the second spindle. We’ve done 8-inch-long parts and had the position timing from the first side to the backside within one degree of tolerance.”
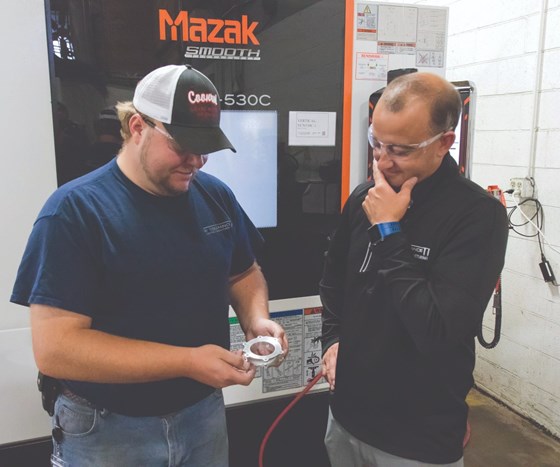
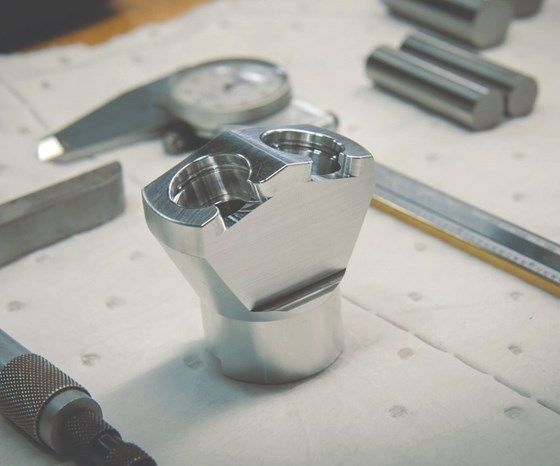
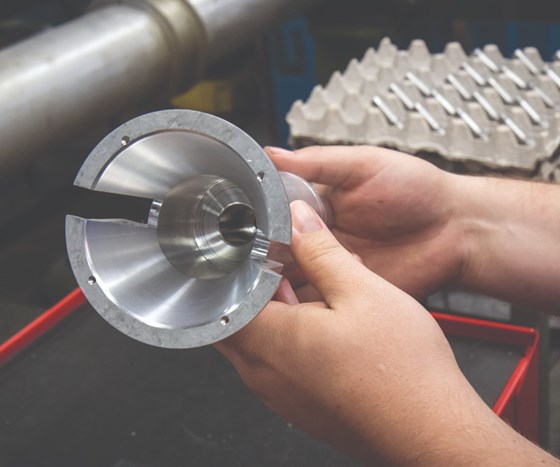
These features removed the need for additional setups and inspections, cutting down the cost of producing the parts. However, this was not the extent of the system’s cost-saving measures. For unattended operation, the shop equipped it with a bar feeder and rotary-rack parts sorter. The machine’s speed also helps the shop avoid having to machine portions of a part on one machine, then remove it and finish the rest on a second machine, further reducing the number of setups required.
The HQR-150MSY isn’t the only Mazak equipment used throughout In Tolerance’s shop floor to maximize efficiency. Practically all the machines at In Tolerance are Mazaks—four turning centers, seven vertical machining centers (VMCs) and four horizontal machining centers (HMCs) occupy the shop floor. Of these, the shop’s most recent additions include two VCN-530C VMCs, which are equipped a SmoothX computer numerical control (CNC). The controls are designed to have a user-friendly interface that enables fast uploading and downloading as well as machine positioning. According to the shop, it significantly reduces part cycle times, in some instances as much as 25 percent. With the high spindle speeds of the machines, the cycle times drop even further. Additionally, it enables the shop to turn corners faster by increasing processing speeds.
While the SmoothX is a relatively new, more powerful and faster control, it is said to be similar enough to the shop’s Mazak Mazatrol controls that machinists can move from older systems to newer ones without difficulty.
Another way In Tolerance has improved its part-processing speed is by investing in the HCN-4000, a HMC. The machine’s faster spindle speeds in particular enable the shop to keep operations basically the same but complete them much quicker for profit gains of 20 to 30 percent per job. For example, in one job the 18,000-rpm spindle speed reduced a 2.5-hour cycle time to just over an hour.
The HMC features a standard two-pallet changing system. First operations will run on one pallet, and second operations will finish on the other, so parts come out of the machine complete. Its 80-tool storage capacity enables the shop to tool it up to run three or four different jobs, maximizing production efficiency.
The speed of its newer Mazak machines enables In Tolerance to run bigger job lot sizes faster, which equates to less inspection time. Machine speed and consistency help reduce inspection sampling sizes, and faster machines mean the shop produces more in the same or shorter amount of time than previously. For example, instead of producing five pieces for one job, then changing over to the next job, In Tolerance can produce 15 pieces in that same amount of time with all those pieces going to inspection at once.
According to quality manager Tammy Baker, more parts done faster in the same amount of time reduces inspection time. It not only eliminates the number of setups and tear downs on the shop’s machine tools, but also on its inspection equipment as well.