Średnica przelotu wrzeciona | Φ76 mm |
Rozmiar uchwytu | 8” |
Maks. średnica obróbki | Φ320 mm |
Maks. długość obróbki | 860 mm |
Centra tokarskie CNC
HQR NEO
- Konstrukcja z 3 głowicami rewolwerowymi / 2 wrzecionami umożliwiająca pracę w krótkim cyklu roboczym
- Obróbka materiału podawanego z pręta do Φ102 mm (opcja)
- System automatyzacji do różnych zastosowań, od obróbki w uchwycie do obróbki detali w formie pręta
- System CNC MAZATROL SmoothG3 do wydajnej obróbki z wykorzystaniem 3 głowic rewolwerowych
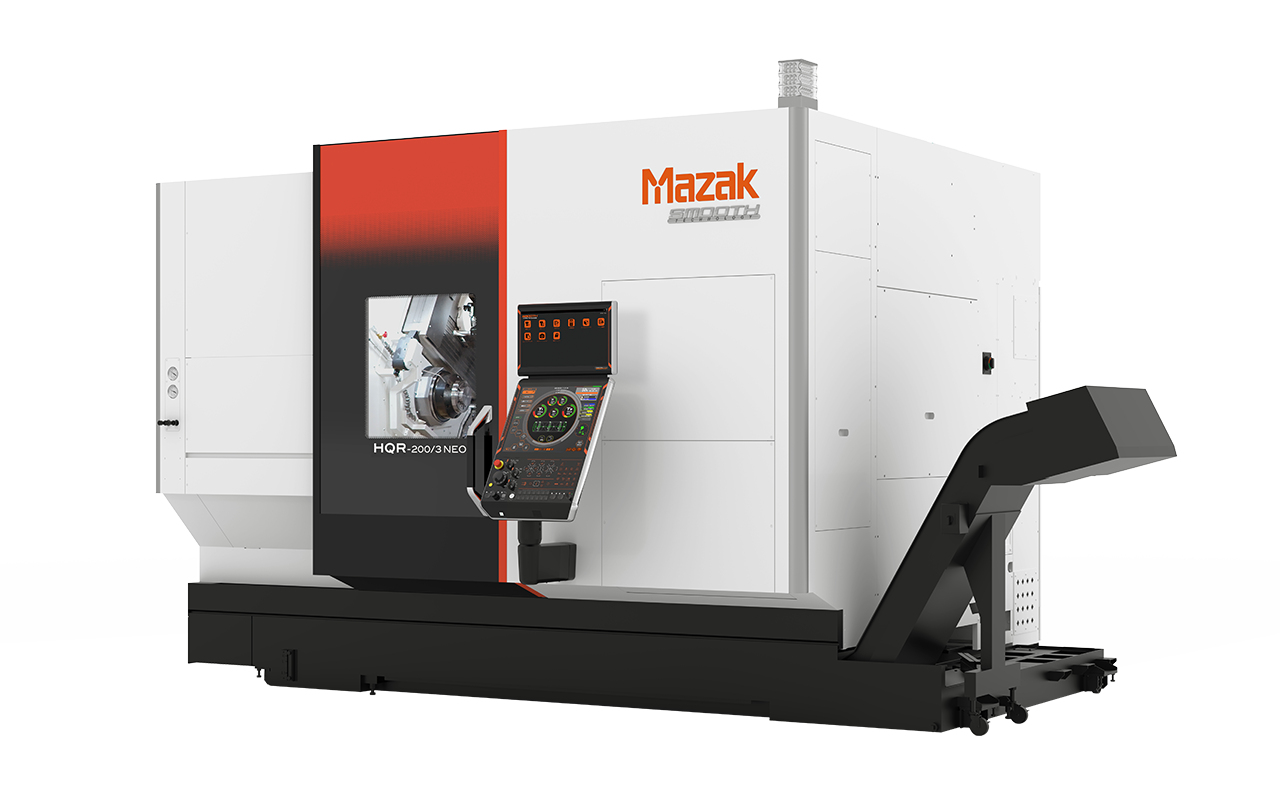
Konstrukcja maszyny, która przyczynia się do istotnego skrócenia cyklu roboczego
Maszyna o unikalnej konstrukcji z 3 głowicami rewolwerowymi / 2 wrzecionami realizuje jednoczesną obróbkę „balance cutting” dwóch detali przy wykorzystaniu górnej i dolnej głowicy rewolwerowej.
W przypadku detali, w której między pierwszą a drugą operacją występuje różnica w ilości skrawanego materiału, nasza maszyna pod względem wydajności ma znaczną przewagę nawet nad centrum tokarskim CNC z 2 głowicami rewolwerowymi / 2 wrzecionami.
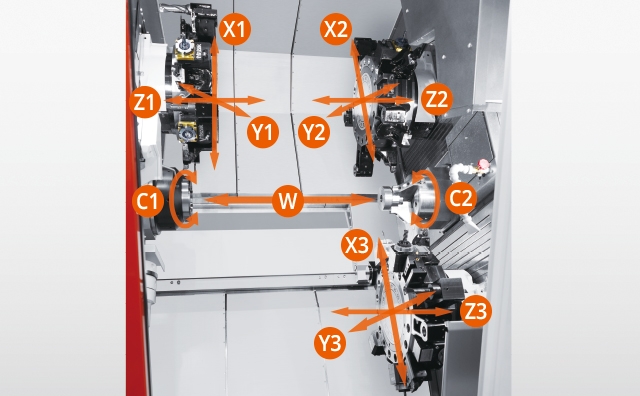
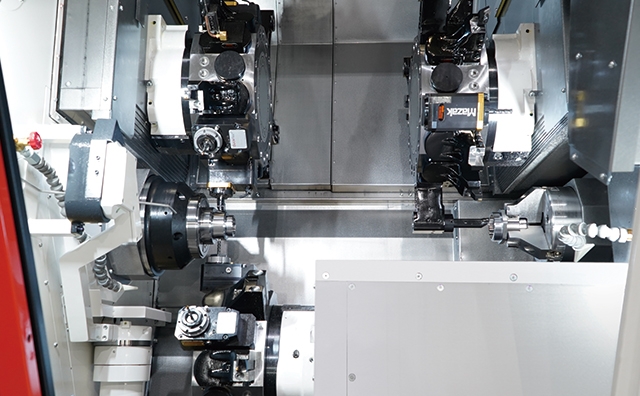
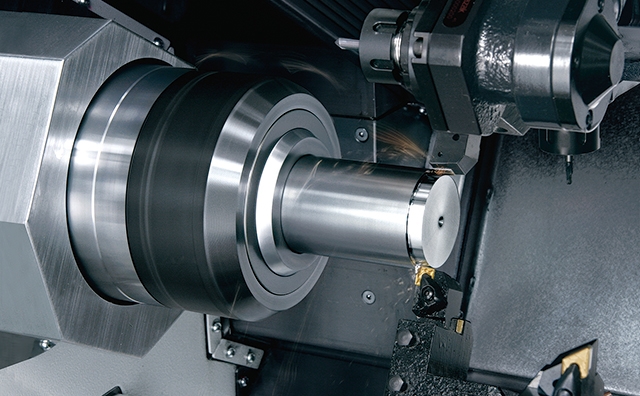
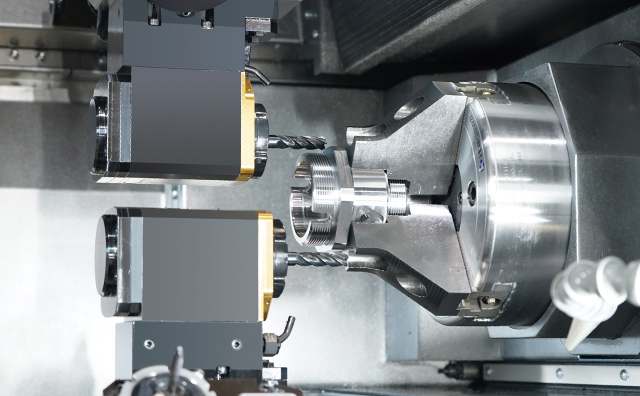
Obróbka materiału podawanego z pręta
Ponieważ zarówno wrzeciono główne, jak i drugie wrzeciono mają duże średnice przelotu wrzeciona, pozwalają na obróbkę materiału z pręta o różnych wymiarach.
Model maszyny | Wrzeciono główne | Drugie wrzeciono |
HQR-200/3 NEO | Φ65 mm | Φ65 mm |
Φ102 mm* | Φ65 mm | |
HQR-250/3 NEO | Φ80 mm | Φ65 mm |
Φ80 mm* |
*Opcja
Jeszcze wyższa wydajność dzięki automatyzacji
Dostępna jest szeroka gama opcjonalnych systemów automatyzacji, takich jak podajniki prętów, transportery detali i roboty, dzięki którym maszyna może przez długi czas pracować automatycznie.
Podajnik prętów i transporter detali
Efektywna obróbka: od materiału z pręta do gotowego detalu. Użycie transportera detali zamiast automatycznego chwytaka pozwala uniknąć uszkadzania wykończonej powierzchni podczas wyjmowania detali z maszyny.
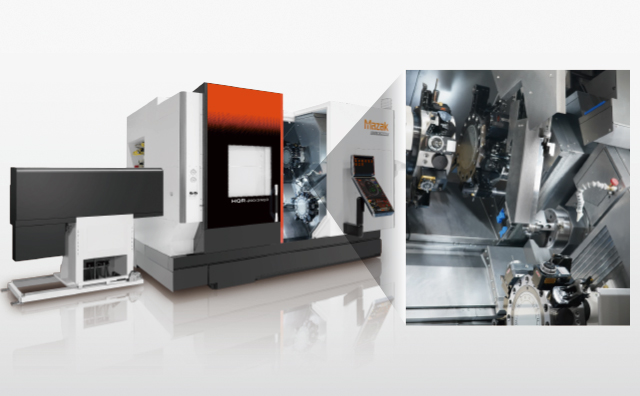
- Etap 1
- Etap 2
System CNC MAZATROL SmoothG3
System CNC do jednoczesnej obróbki 4-osiowej

- Ekran dotykowy przyspiesza realizację różnych zadań, takich jak programowanie i edytowanie.
Specjalny ekran do obsługi 3 głowic rewolwerowych usprawnia skomplikowaną obróbkę.
- Złożone ruchy 3 głowic rewolwerowych są nadzorowane przez różne funkcje kontroli kolizji dla zapewnienia bezpieczeństwa.

Interfejs ułatwiający używanie systemu
Duży ekran dotykowy do intuicyjnej obsługi
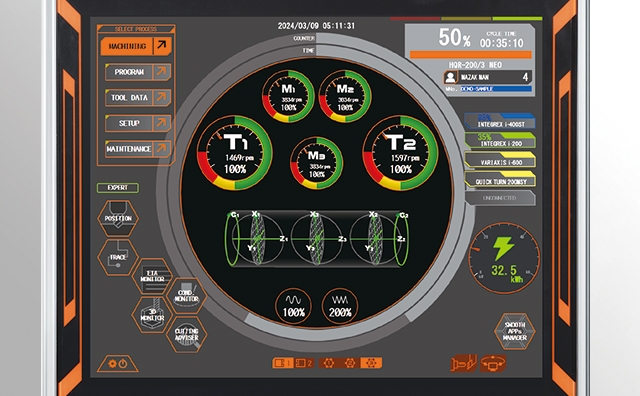
Wydajna obróbka na 3 głowicach rewolwerowych z wykorzystaniem specjalnego ekranu i funkcji wspomagających
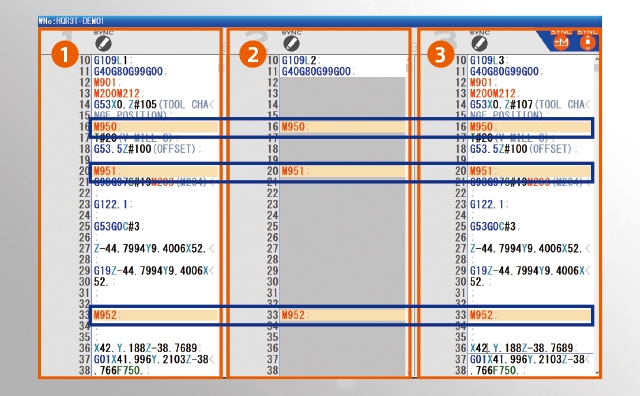
Ekran podzielony na trzy kolumny ułatwia weryfikację pracy poszczególnych głowic rewolwerowych. Na ekranie programowania EIA/ISO położenia poleceń oczekiwania wyświetlane są obok siebie, co pozwala na intuicyjne i łatwe edytowanie programu.
Różne funkcje kontroli programu
W obrabiarce z 3 głowicami rewolwerowymi kontrola programu stanowi wyzwanie ze względu na złożoność ruchów głowic, która utrudnia ich synchronizację.
Dostępne funkcje kontroli programu nie naruszają synchronizacji głowic.
Virtual Machining
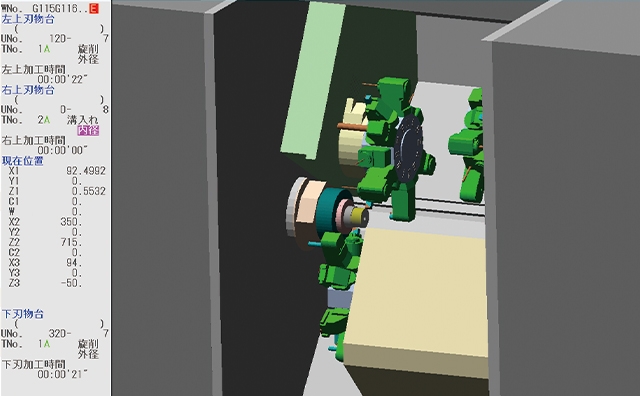
Dokładna symulacja w środowisku identycznym z rzeczywistym środowiskiem maszyny pozwala zawczasu zweryfikować kształt i bezkolizyjność.
Dzięki temu produkcja jest wydajna już od pierwszego detalu.
Osłona bezpieczeństwa
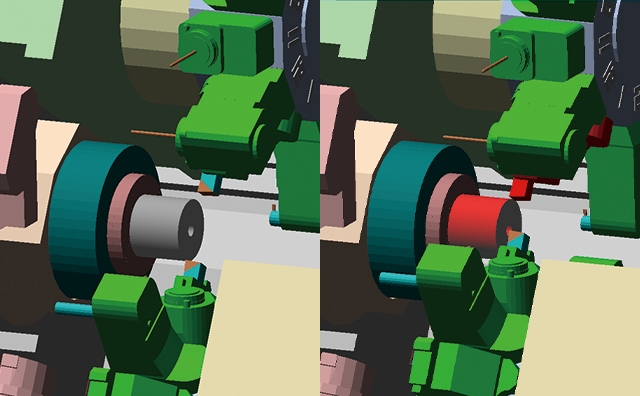
Model 3D na ekranie systemu sterowania wykrywa kolizje nawet wtedy, gdy operator przemieszcza osie ręcznie podczas ustawiania maszyny.
Sprzężenie bloków programu
Gdy jedna głowica rewolwerowa ukończy proces, wszystkie pracujące głowice zatrzymują się jednocześnie, nawet gdy końce bloków programu dla tych głowic są różne.
Sprzężenie bloków programu zapewnia synchronizację między głowicami, zapobiegając kolizjom i przestojom spowodowanym przez niedopasowanie programów.
Ze sprzężeniem bloków programu
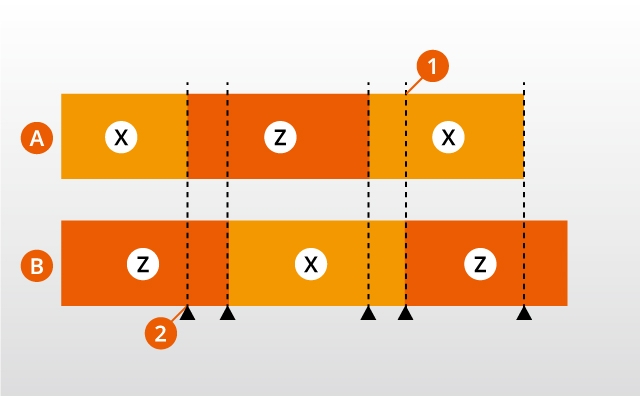
A: Głowica rewolwerowa A
B: Głowica rewolwerowa B
1: Gdy posuw osi X głowicy B osiągnie ▲, głowica A również się zatrzymuje.
2: Gdy posuw osi X głowicy A osiągnie ▲, głowica B również się zatrzymuje.
▲: Zatrzymanie
Bez sprzężenia bloków programu
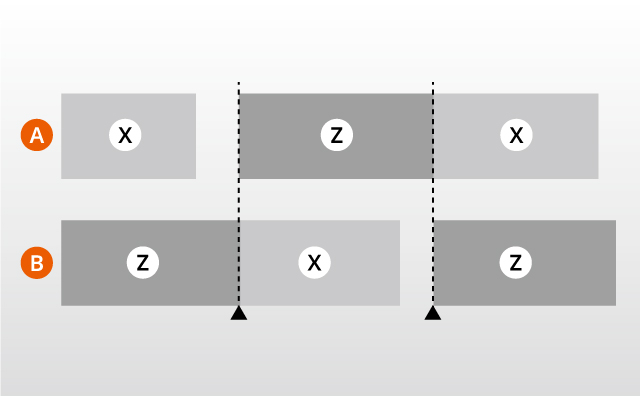
A: Głowica rewolwerowa A
B: Głowica rewolwerowa B
▲: Zatrzymanie
Synchronizacja wymuszonych zmian
Wymuszone zmiany czasów w programie są odzwierciedlane nie tylko w czasie pracy głowic rewolwerowych, lecz także w czasie oczekiwania, zatem nie powodują zakłócenia synchronizacji pracy głowic. Dzięki temu można z dużą dokładnością wykrywać możliwe kolizje.
Z synchronizacją wymuszonych zmian (50%)
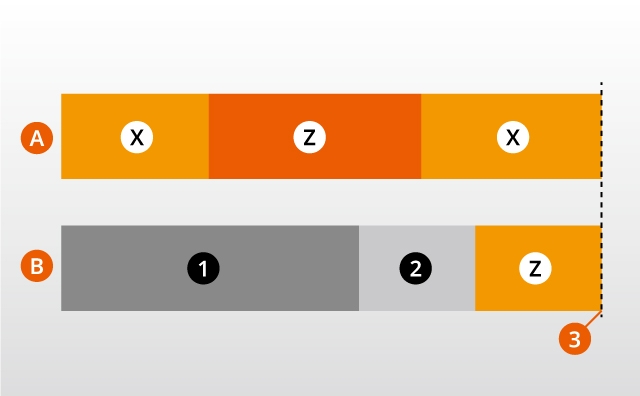
A: Głowica rewolwerowa A
B: Głowica rewolwerowa B
1: Oczekiwanie (czas pozostawania w gotowości)
2: Funkcje pomocnicze
3: Bez niedopasowania programów
Bez synchronizacji wymuszonych zmian (50%)
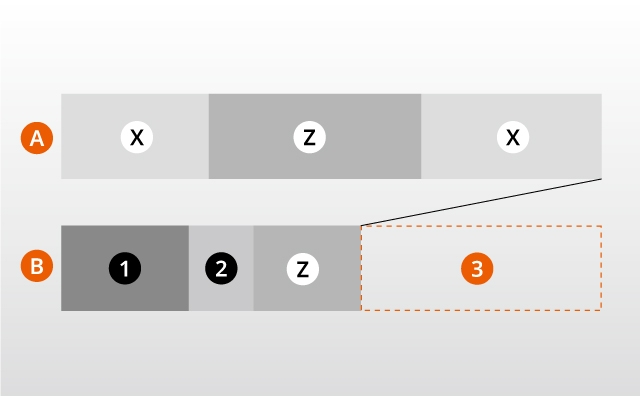
A: Głowica rewolwerowa A
B: Głowica rewolwerowa B
1: Oczekiwanie (gotowość), bez zmiany czasu
2: Funkcje pomocnicze
3: Niedopasowanie programu
Ręczne sterowanie impulsowe
Szybkość wykonania programu można regulować, ręcznie obracając pokrętło systemu CNC. Pozwala to na dokładne sprawdzenie pozycji podejścia i punktów prawdopodobnych kolizji.
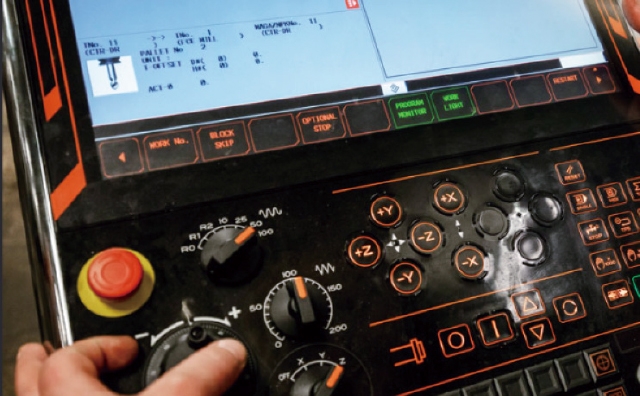
HQR-200/3 NEO
HQR-250/3 NEO
Średnica przelotu wrzeciona | Φ91 mm |
Rozmiar uchwytu | 10” |
Maks. średnica obróbki | Φ320 mm |
Maks. długość obróbki | 860 mm |