Maintenance Recommendations for Fiber Lasers
Maintenance Tips to Keep Your Laser-Cutting Machine Running Smoothly
By Atika Rafiq, Sr. Marketing Specialist at Mazak Optonics Corp.
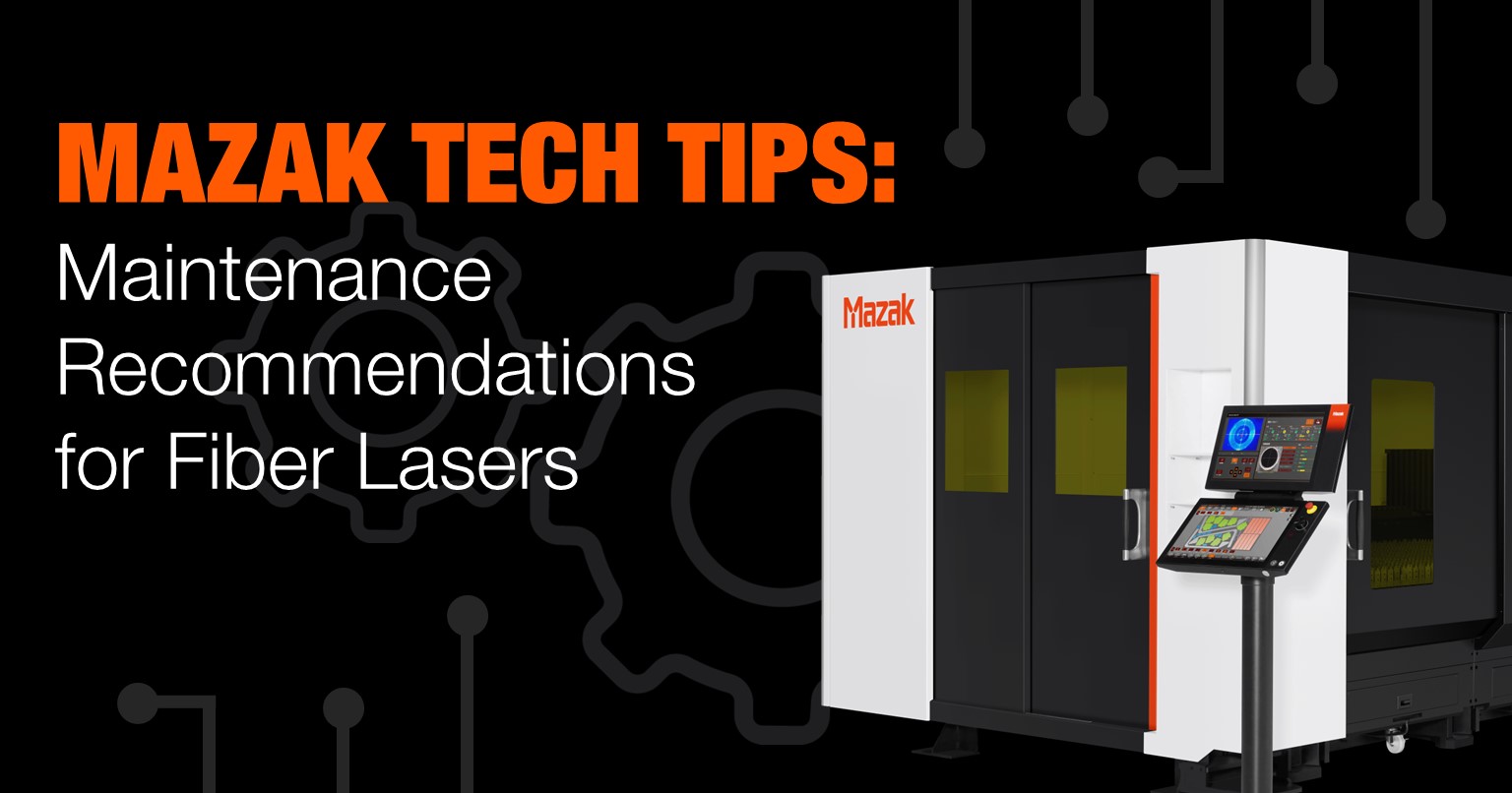
Fabricators invest significant time and resources into purchasing equipment for their business. Like most major equipment investments, regular maintenance is key for improving machine longevity. In addition to getting the most value from your investment, regular maintenance can help prevent unnecessary downtime. Below are a few things fabricators can do to keep their laser-cutting machine running smoothly.
Inspect Torch
The torch plays an integral role in the laser-cutting process. Frequent inspections of the torch are beneficial for precision laser cutting. Fabricators should check the nozzle to ensure it is free of spatters and the nozzle hole for deformation. If standard cleaning proves to be insufficient, the nozzle may need to be replaced.
The focus lens and protective window both need to be free from pollutants as well. The protective window acts as a barrier for the focus lens, and debris can occasionally get stuck on the window. Routinely check for spatters and dust on the protective window. Clean as needed to restore performance. Improper maintenance of the protective window could lead to contamination of the focus lens and require service from Mazak.
Note: Be careful not to allow dust and dirt to enter the torch. It is recommended to clean and replace the protective window in a place where there is minimal dirt or dust, such as an office. Contamination inside the torch could cause damage to the optical parts and torch.
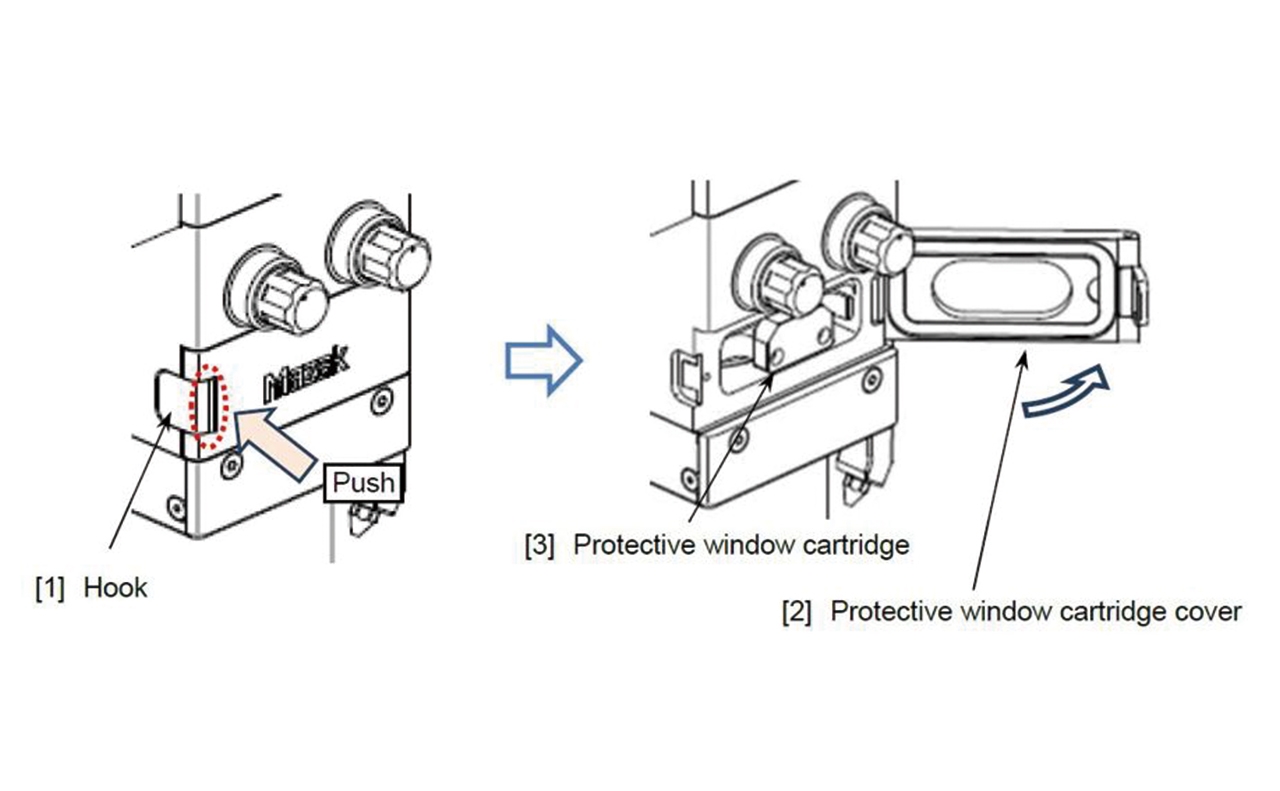
Protective window, Mazak's OPTIPLEX 3015 NEO
Remove Scraps
Each time fabricators cut parts on their laser, small fragments of the material gather at the bottom of the machine. Typically, the scrap buckets, where the material accumulates, need to be cleaned and emptied out when routinely scheduled. However, the machine needs to be cleaned, and the scrap buckets need to be emptied when laser operators change material to remove all previous debris. Failure to clean the machine and remove all scrap pieces of metal will cause the debris from different materials to mix, resulting in indefinite downtime. For optimal laser performance, thoroughly clean the machine prior to switching material.
Note: Power off the machine when removing debris. If a scrap bucket is removed during machining, the machine will be brought to a feed hold stop. Use proper equipment to remove chips from the scrap buckets. Do not touch scrap material without the proper personal protective equipment.
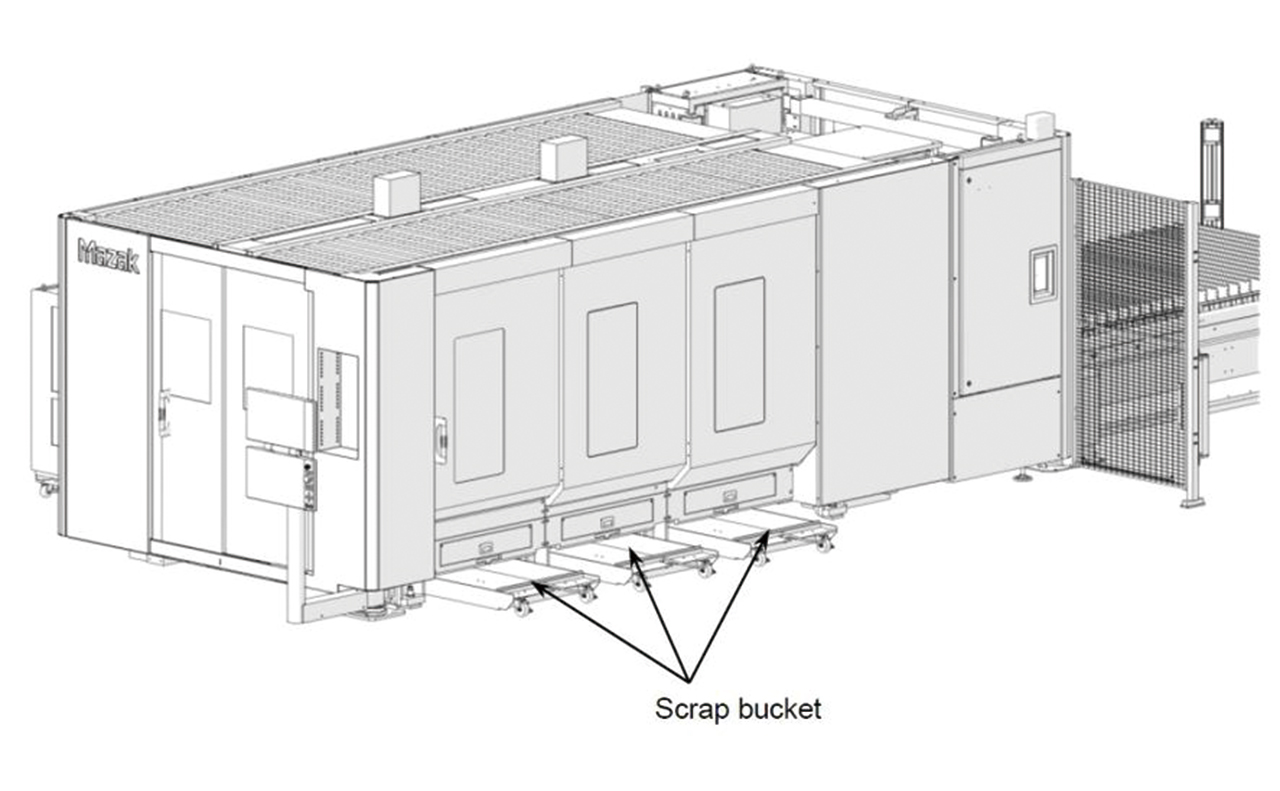
Scrap buckets, Mazak's OPTIPLEX 3015 NEO
Maintain Dust Collector
As the name suggests, dust collectors contain debris generated during the cutting process. This ancillary equipment that helps maintain a laser also requires maintenance of its own. Filters featured on the dust collector that remove contaminants from the air need to be cleaned frequently. Debris that has been collected in the dust collector needs to be removed periodically for optimal machine performance. It is important to note—the dust collector duct, dust collector, and filters need to be cleaned prior to a change in cutting material. Please refer to your machine manual for specific maintenance instructions.
Note: Do not tap or press the filter to remove debris. This could cause the filter to break and lose its ability to collect dust effectively. Do not use water or oil for cleaning as these products will remain in the filter and decrease dust collection performance.
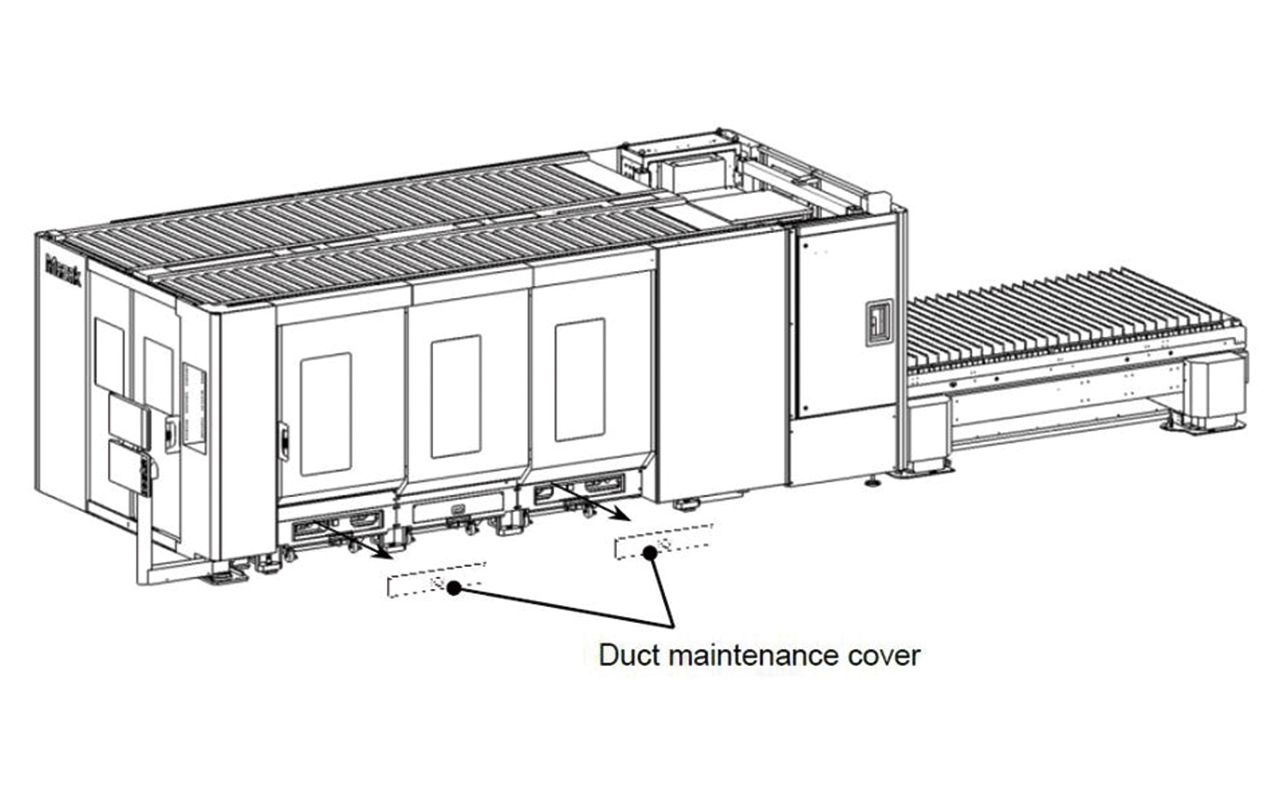
Duct maintenance cover, Mazak's OPTIPLEX 3015 NEO
At Your Service
Maintenance requirements vary based on machine type and production environment. Refer to your maintenance manual for recommendations specific to your equipment. If you have any questions about machine maintenance, don’t hesitate to reach out. Mazak’s service team is ready to help. Call 1-888-MAZAK-US or email service@mazaklaser.com to connect with a knowledgeable team member.