The Advantages of High-Power Beam Shaping Technology in Laser Cutting
Mazak’s OPTIPLEX 3015 NEO Combines High Power and Maximum Beam Control for Optimal Laser-Cutting Performance
By Al Bohlen, President, and Atika Rafiq, Marketing Specialist, at Mazak Optonics Corp.
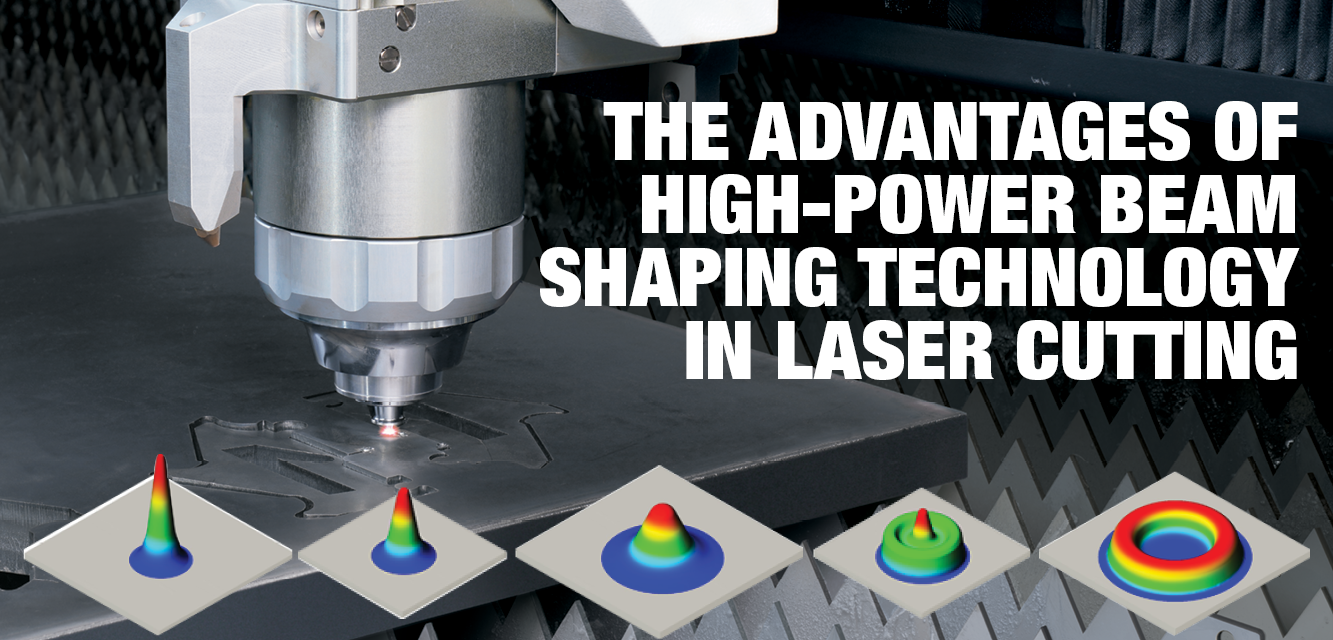
Before laser cutting, fabricators relied on punching and stamping machines to cut metal. However, the dawn of lasers brought about the ability to cut material with thermal energy.
Users of the first CO2 laser-cutting machines took advantage of increased cutting capabilities and improved cut quality. As the industry shifted its focus to fiber lasers for higher cutting speeds and reduced costs of operation, fabricators reminisced about the part quality achieved by CO2 lasers on thicker material. To remedy this, the technical aspect of laser-cutting needed to be better understood first.
CO₂ vs Fiber Laser Beam
Making the switch from a 4kW CO2 laser to a 4kW fiber laser resulted in faster cutting speeds on thinner material. In this instance, while the power levels have remained the same, the reason for increased cutting speeds is due to the fiber laser’s beam mode. Standard fiber lasers operate in 00 mode which produces the perfect laser beam—symmetrical, with high power density at the tip of the beam. CO2 lasers, on the other hand, operate in 01 mode where a lot of the power is on the outer edges of the beam and the center is slightly cooler.
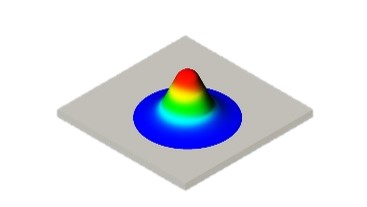
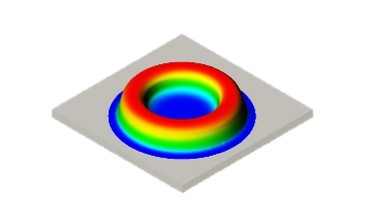
In addition, a CO2 laser beam is physically larger in diameter when compared to standard fiber lasers. Being 1/3 the size of a CO2 laser beam in diameter, the standard fiber laser beam is almost ten times more concentrated in the center. While this is optimal for thin metal cutting, it poses a challenge when thermal cutting on thicker material because the high power concentration in a small spot size results in a very narrow kerf width. In thicker material, the assist gas is fighting to get a high volume of molten material through a narrow kerf width and can result in heavy striation, speed degradation, and reduced part quality.
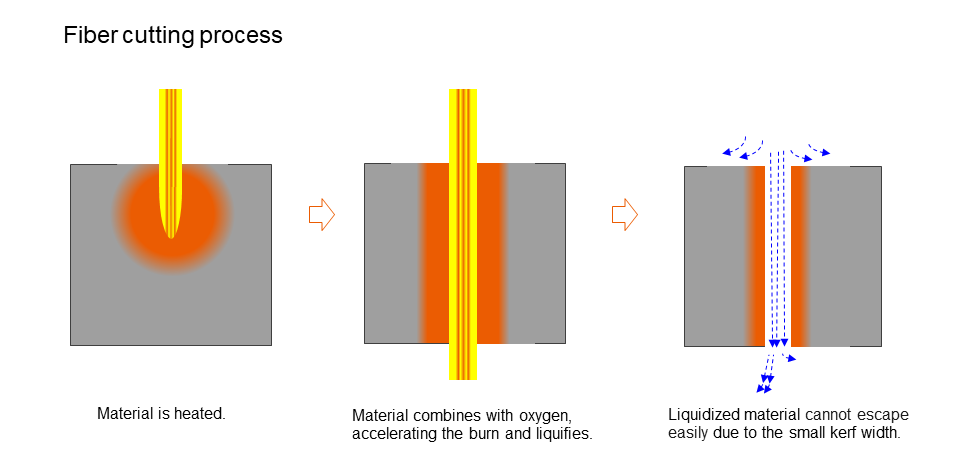
The CO2 laser beam or 01 mode is optimal for thick plate cutting due to its size and power distribution. Removing all molten material freely through the kerf provides a smoother edge, less striation, and a lower amount of dross on the bottom edge of the material.
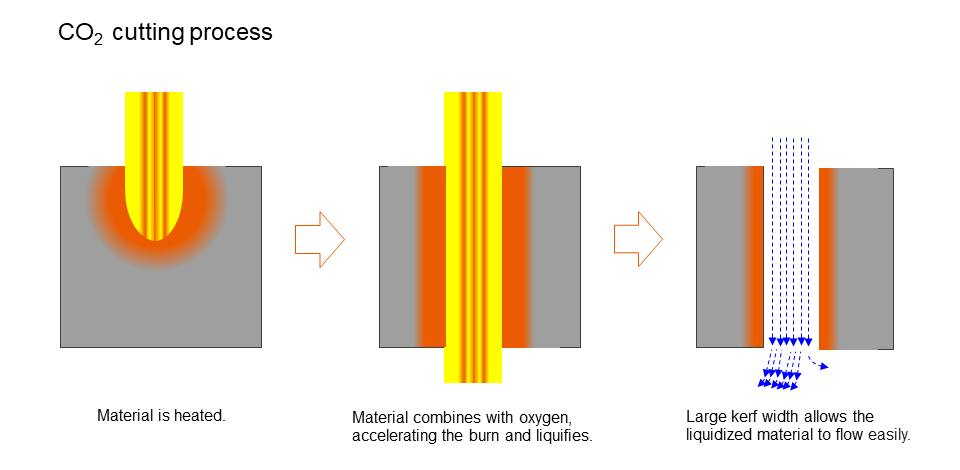
Introducing Beam Control on a Fiber Laser
With the industry’s shift to fiber lasers, many operators lost access to CO2 laser cutting technology. For that reason, laser manufacturers began looking for ways to manipulate the fiber laser in order to replicate the CO2 laser beam. Knowing the science behind the technology, it was easy to make the fiber laser beam bigger by running it through a pair of optics, a process called collimation, and simply expanding the diameter of the beam. The result was a wider kerf width and the ability to better cut heavier plate material.
The part quality on thicker material, however, still wasn’t the same as it was when cutting with a CO2 laser beam because the mode was still the same. Power distribution of the laser beam was not altered in any way; the beam was simply made wider.
In response to this, Mazak developed proprietary beam shaping technology that can deliver power through a fiber optic cable but in a multi-core format. With this new technology, operators can decide how much power is in the center versus the outer edges of the beam. Multiple cores in the fiber optic cable make it possible to select and move where the power goes into the cores. In fact, users can command power distribution from the generator—before it ever reaches the cutting head. The result is a true 01 mode out of a fiber generator.
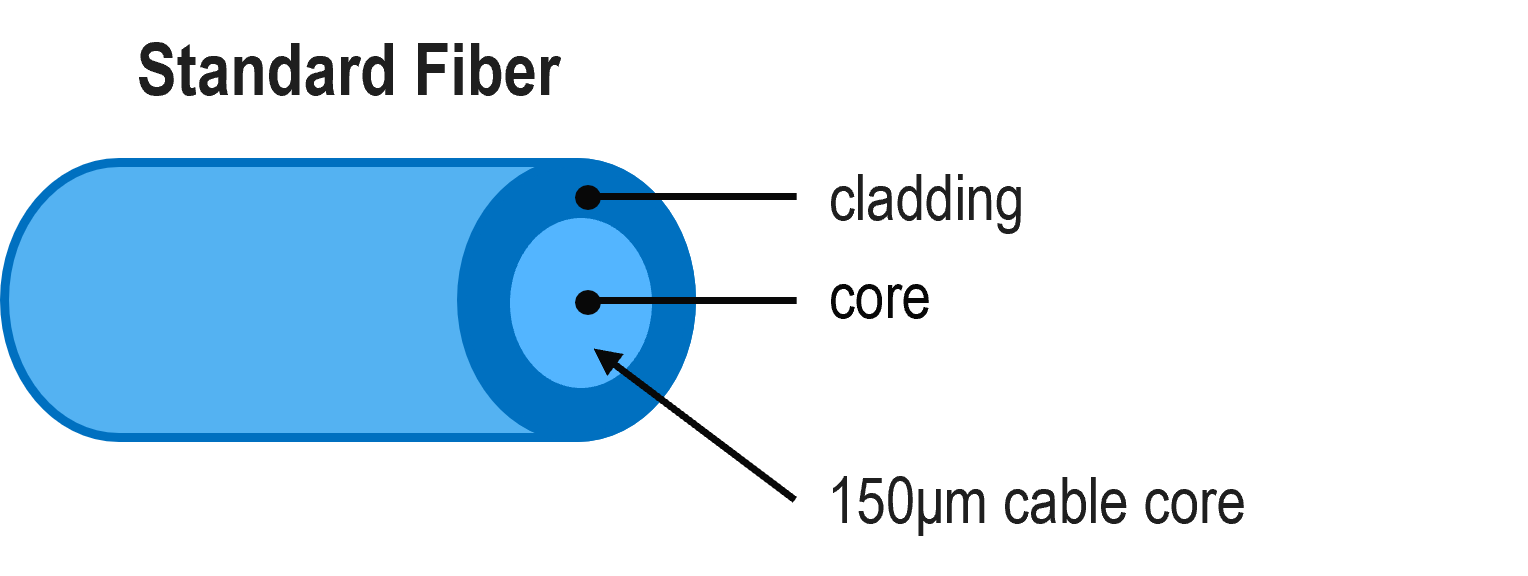
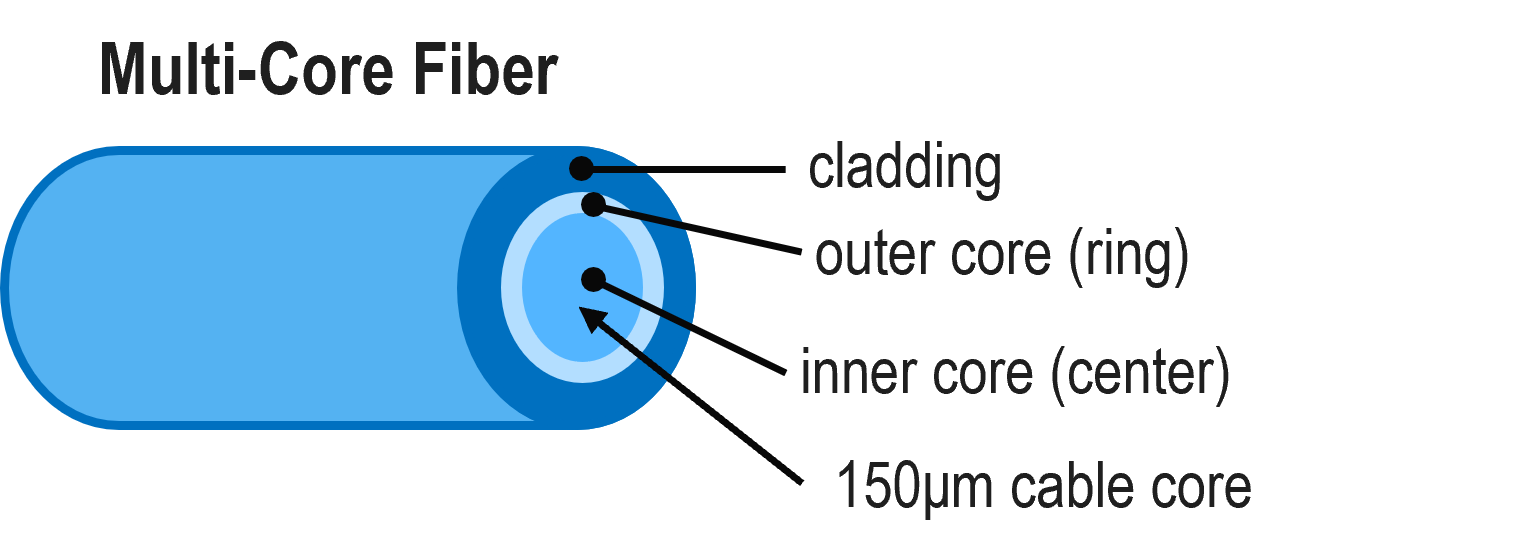
In thick plate cutting, 01 mode or ring mode is vital for achieving zero taper. The outer ring makes the initial cut which creates a wider kerf width, produces good molten material flow, and burns off scale/debris. After the initial cut with the outer ring, the center core can then provide a clean edge that is high quality, super sharp, and has zero angle draft. All of this is possible without a reduction in cutting speed.
High Power and Maximum Control
While Mazak offers beam control technology in 4kW and 7kW power levels, the OPTIPLEX 3015 NEO provides this proprietary technology in the high 15kW power level.
It’s important to note that higher power, by itself, does not result in high-quality parts. There’s more to the science of laser cutting than just sheer brute force. Machines that tout high power will have amazingly fast cutting speeds, but the part quality may not be great. The combination of high power and beam shape/diameter control ensures high speed and high accuracy when cutting a wide range of materials.
Featured on Mazak’s OPTIPLEX 3015 NEO, these technologies allow operators to select the appropriate beam mode for the material being cut. For example, users can select 01 mode when cutting thick plate and 00 mode when cutting thin material. The OPTIPLEX 3015 NEO comes equipped with ten different heat profiles and offers beam diameter control.
State-of-the-Art Laser Technology
Advanced equipment, like the new cutting head and nozzles available on Mazak’s OPTIPLEX 3015 NEO, facilitate these machine operations. Implementing new nozzle technology, like the TrimCut nozzle, increases cutting speeds and reduces gas consumption by capturing the gas better. This helps ensure that the assist gas is not lost before it gets in the cut. Additionally, the new nozzle technology can run higher velocity and higher pressure through the kerf—when compared to a standard nozzle. Nozzles can also assist when making adjustments to beam diameter; the laser beam can be configured through the nozzle to be any size diameter desired.
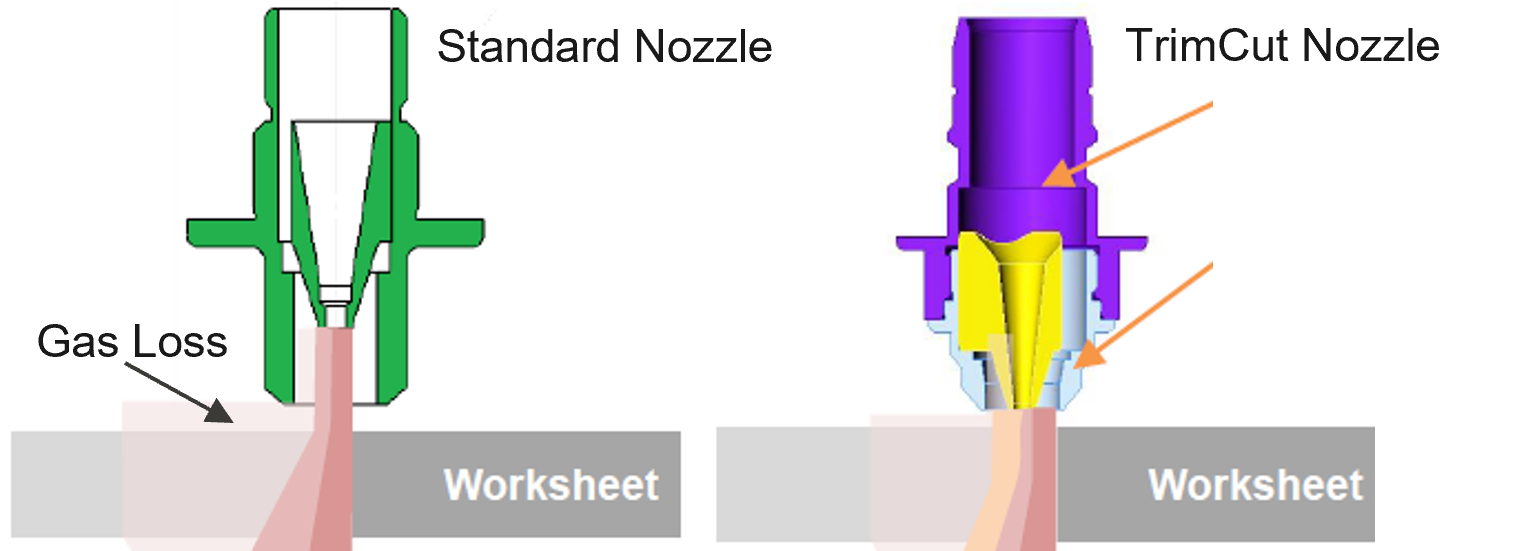
Furthermore, the new Mazak cutting head makes it easy to command different beam modes. Operators may need to switch between modes in rapid succession to pierce in one mode and cut in another mode. The new cutting head handles these prompt changes with ease.
Mazak’s OPTIPLEX 3015 NEO comes equipped with all the latest laser-cutting technologies in one machine—15kW of high power, beam shape/diameter control, an advanced torch head, and a new series of nozzles. Combined, these features provide the capabilities needed for optimal laser cutting performance.
About Mazak Optonics Corporation
Mazak Optonics Corporation is a major supplier of laser-cutting systems, offering 50 laser models and leading the industry in the implementation of emerging laser technologies. The company’s 50,000 sq. ft. North American Headquarters are located in Elgin, Illinois, and feature a 30,000 sq. ft. laser technology center housing up to 18 machines for demonstrations and training. Mazak Optonics is part of Yamazaki Mazak Corporation (Oguchi, Japan), the global leader for the manufacture of machine tools and systems for the precision machining of metal parts, including CNC turning centers, horizontal and vertical machining centers, Multi-Tasking machining centers, turnkey cells and software solutions. The North American Headquarters for Yamazaki Mazak are located in Florence, Kentucky. For more information on Mazak Optonics’ products and solutions, visit https://www.mazak.com/moc-en/, email sales@mazaklaser.com or call 847.252.4500.