Expanded Parts Facility Streamlines Customer Support
Mazak’s commitment to customer service prompted the investment in an expanded parts facility and the latest automation technologies
By Joe Hagee, Parts Center Manager, and Atika Rafiq, Marketing Specialist, at Mazak Optonics Corp.
As a leader in manufacturing advanced laser-cutting solutions, Mazak Optonics Corporation prioritizes customer satisfaction. The recent expansion of the parts department aligns with Mazak’s commitment to better serve customers—by increasing capacity for parts and streamlining operations. The goal is to keep customers’ facilities running smoothly.
Our Commitment
When manufacturers upgrade their processes with a laser-cutting machine from Mazak, they can rest assured that they have partnered with a company that stands by its products. Mazak guarantees lifetime parts support on every laser-cutting machine sold. Whether a machine is new or has been running reliably for years, Mazak has the parts needed to achieve maximum machine performance.
Furthermore, the parts department maintains a 97% same-day shipping rate. If an ordered part is in stock, it is shipped out to customers the same day. If a part happens to be out of stock, Mazak team members communicate with their supply chain contacts to have parts shipped directly to the customer as quickly as possible.
Customer satisfaction is at the forefront of Mazak’s support efforts. With every parts order received, the Mazak team strives to ensure that each customer’s needs are heard and met. Their main priority is to respond to customer requests as quickly as possible. Terms of urgency such as “machine down” are flagged as high priority and consequently set a series of procedures in motion to get customers’ machines up and running without delay.
Passion for Innovation
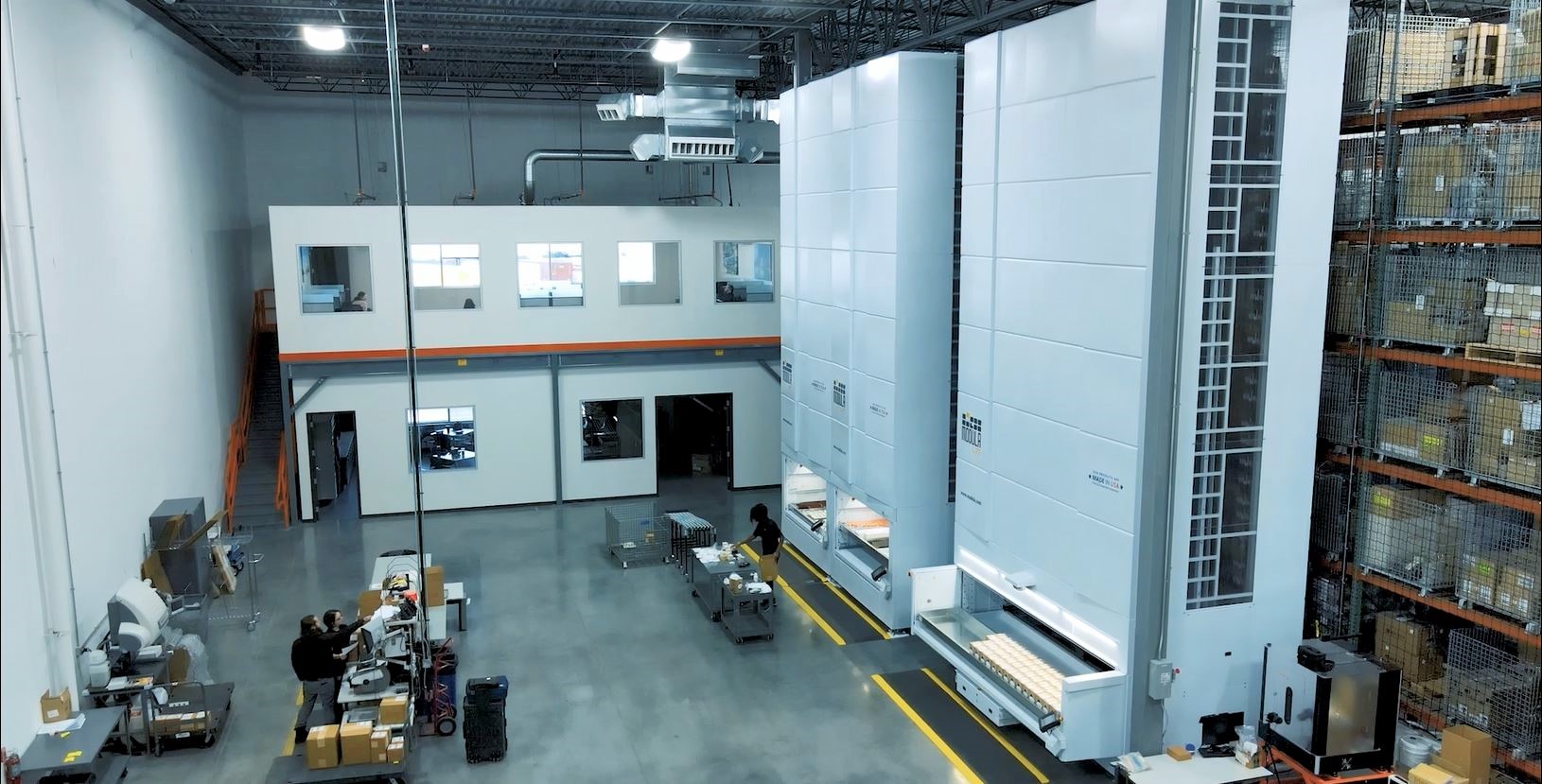
This assurance comes with the challenge of storing numerous machine parts. In 2019, the parts department at Mazak’s North America Laser Technology Center in Elgin, IL consisted of 5,000 square feet of space. With new machines being consistently added to Mazak’s product offerings, acquiring more space to support new and old laser machines was imperative. The need for increased parts capacity led to the recent expansion, which resulted in double the square footage—a total of 10,000 square feet.
With the expansion, Mazak invested in technology to increase efficiency. Three new automated towers easily store and retrieve parts of various sizes. Additional bay doors allow for easy accessibility when receiving and shipping deliveries. A second-story office further facilitates collaboration within the department to provide the best customer service experience possible. The implementation of these technologies helps department team members work in sync to prioritize the needs of Mazak customers.
Looking Ahead
Looking ahead, Mazak intends to keep up with the latest technologies and plans to implement a Pick to Light system to help employees pick parts for multiple orders simultaneously. Once a parts order is received, Mazak employees will simply scan the barcode associated with the order. From there, most of the fulfillment process will be automated. Storage tower trays containing parts from the order will automatically be brought down. A laser pointer will point to where parts are located in the tray. Mazak team members will place the selected items in a barcoded tote. Once all the parts from the order are picked, the tote will automatically move to the shipping area to be prepped for shipment. Implementing this technology will significantly reduce picking time in the warehouse, increase efficiency when restocking machine parts, and vastly improve turnaround time. With customer satisfaction at the forefront of Mazak’s business operations, the team intends to continue investing in resources to aid these efforts.
About Mazak Optonics Corporation
Mazak Optonics Corporation is a major supplier of laser-cutting systems, offering 50 laser models and leading the industry in the implementation of emerging laser technologies. The company’s 50,000 sq. ft. North American Headquarters are located in Elgin, Illinois, and feature a 30,000 sq. ft. laser technology center housing up to 18 machines for demonstrations and training. Mazak Optonics is part of Yamazaki Mazak Corporation (Oguchi, Japan), the global leader for the manufacture of machine tools and systems for the precision machining of metal parts, including CNC turning centers, horizontal and vertical machining centers, Multi-Tasking machining centers, turnkey cells and software solutions. The North American Headquarters for Yamazaki Mazak are located in Florence, Kentucky. For more information on Mazak Optonics’ products and solutions, visit https://www.mazak.com/moc-en/, email sales@mazaklaser.com or call 847.252.4500.