Western Steel and Mazak Optonics Partner for Success
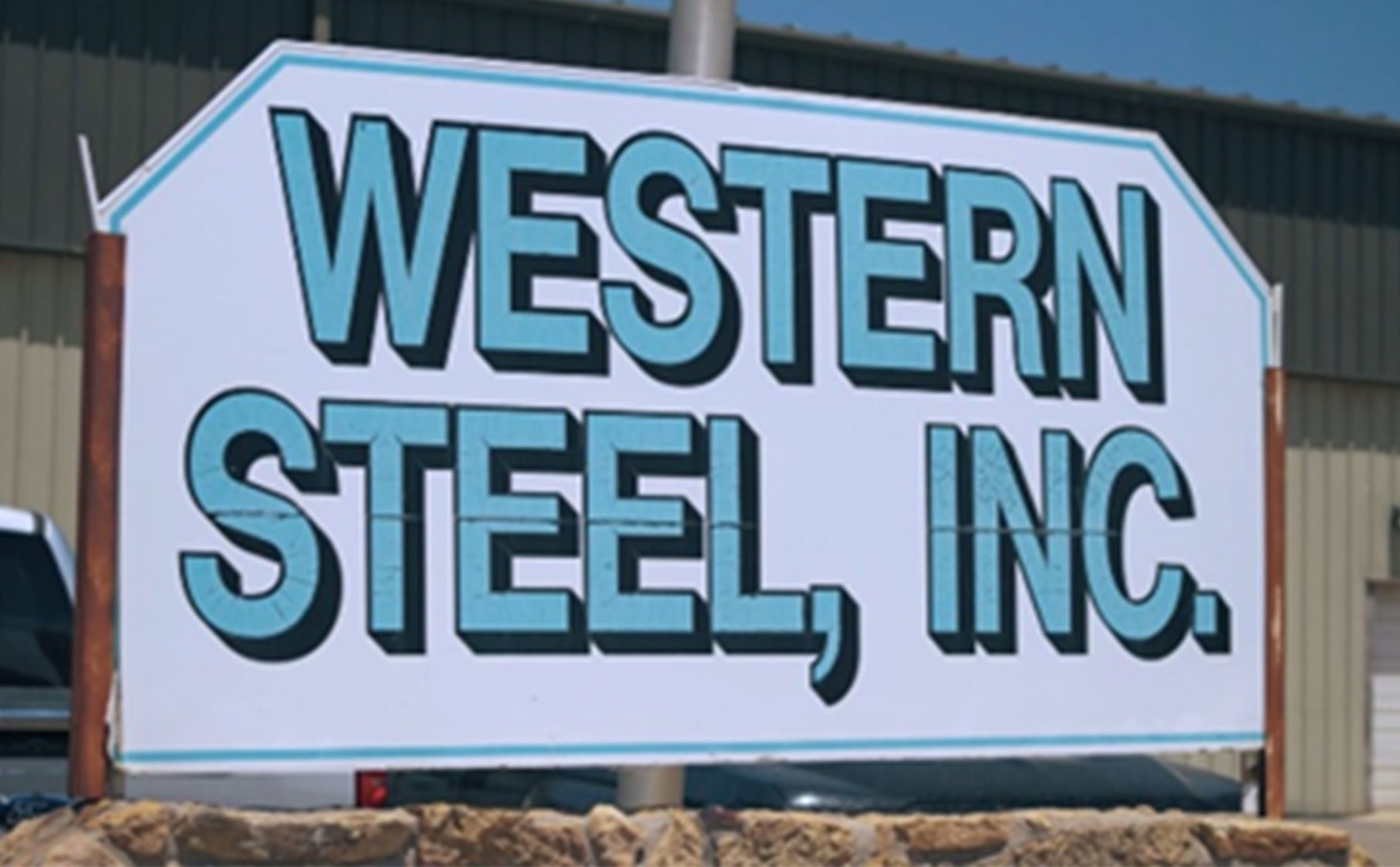
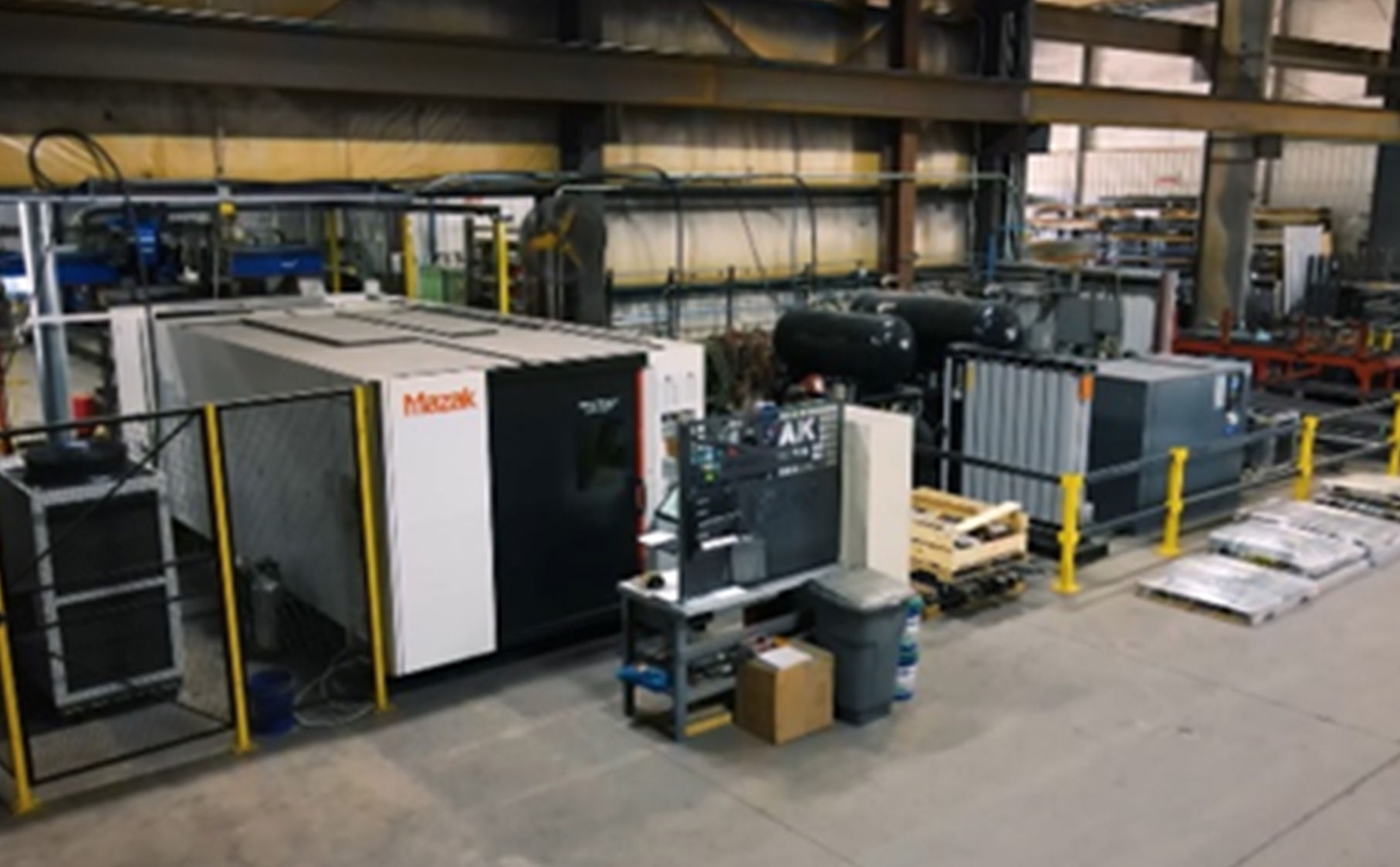
Western Steel, Inc., a family-owned business spanning across three generations, is based in Colorado Springs, CO. It originated as a scrap yard in 1904, the company has evolved into a one-stop service center within their 50,000 sq. ft. facility. They offer raw material sales and a variety of services, including braking, shearing, plasma cutting, beveling, and laser cutting.
Micah Olesky, Vice President of Western Steel, emphasizes their commitment to serving all customers, big or small, without minimum order requirements. Their clientele includes sectors from manufacturing, construction, military/government, ornamental, and infrastructure. “We regularly cut parts for OEM and after-market car and equipment companies, signs, construction-related parts, and equipment manufacturing,” Olesky stated.
To meet customer needs, Western Steel has continually expanded its offerings and services by investing in technology. This strategic move has enabled them to provide high-quality parts more efficiently and cost-effectively, allowing their customers to focus on assembly and installation. “Our commitment to quality is demonstrated through our invest in technology for our customers, while providing on-time delivery and industry-leading customer service,” said Olesky. He added that Western Steel values its employees and aims to extend a family-like environment to its customers as well.
One of the biggest challenges they have faced is the labor market. “As the older generation retires, finding skilled workers who know the ins and outs of things like bending material, plasma cutting, drilling, and so on has been challenging,” Olesky noted. “We have addressed this challenge with our new technology. While technology by no means replaces skilled labor, it is there to support them, make their jobs easier, and frankly, the new generation gets excited about fancy machinery.”
When it came time to purchase laser equipment, their choice was clear, and they focused immediately on Mazak. “Over the years, we had visits from several companies wanting to show us their laser technology. However, I had heard much about Mazak, the reliability of their machines, the quality to which they are built, and their after-sales support,” said Olesky. Due to Mazak’s outstanding reputation, they purchased an OPTIPLEX 3015 NEO 15kW in February of 2023, with the machine installed in September of that same year.
“The initial reaction to the new laser technology was great,” Olesky reported. Coming from a background of plasma machines, we were amazed at the simplicity and the speed at which we could cut parts. Furthermore, we loved the quality of the cut compared to a high-definition plasma. The ease and simplicity of the machine's operating system is a big plus for everyone. Other features that our operators appreciate are the ability to run the machine lights out, the nozzle check camera, and the flexibility of the machine to run 1 1/4” A36, followed by a sheet of 22GACR, followed by another sheet of 11ga stainless 304, all without having to intervene with the machine to change out consumables.”
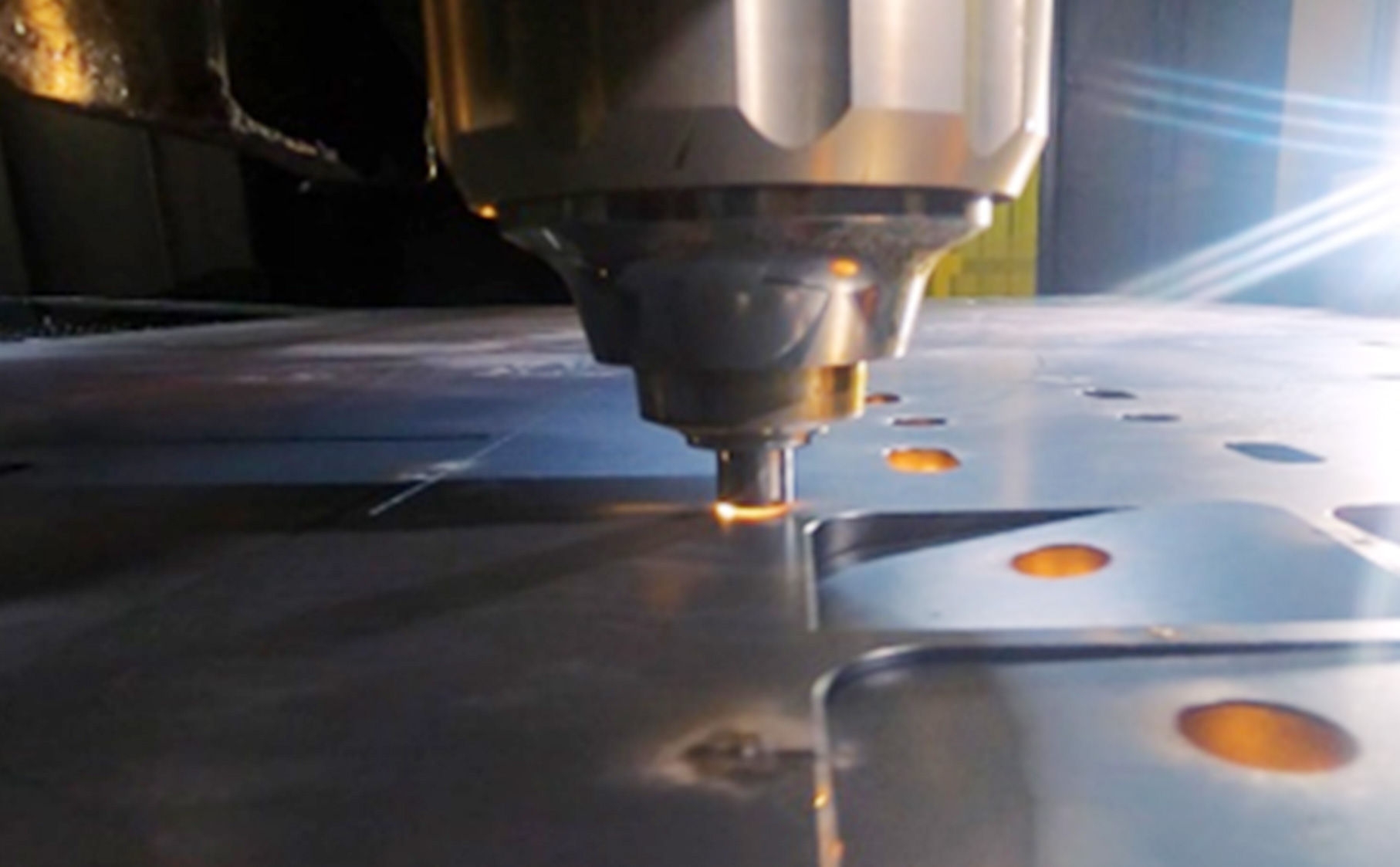
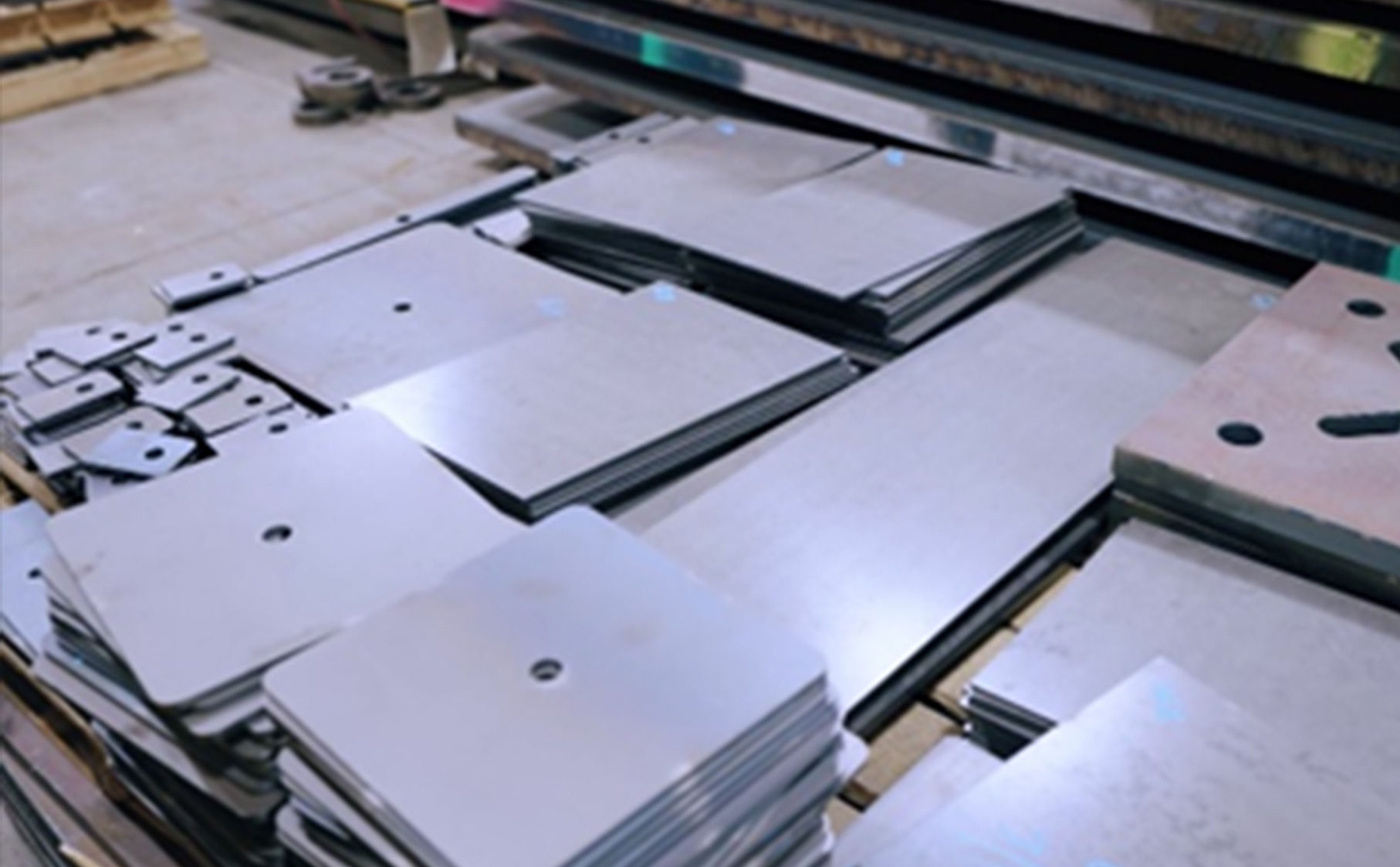
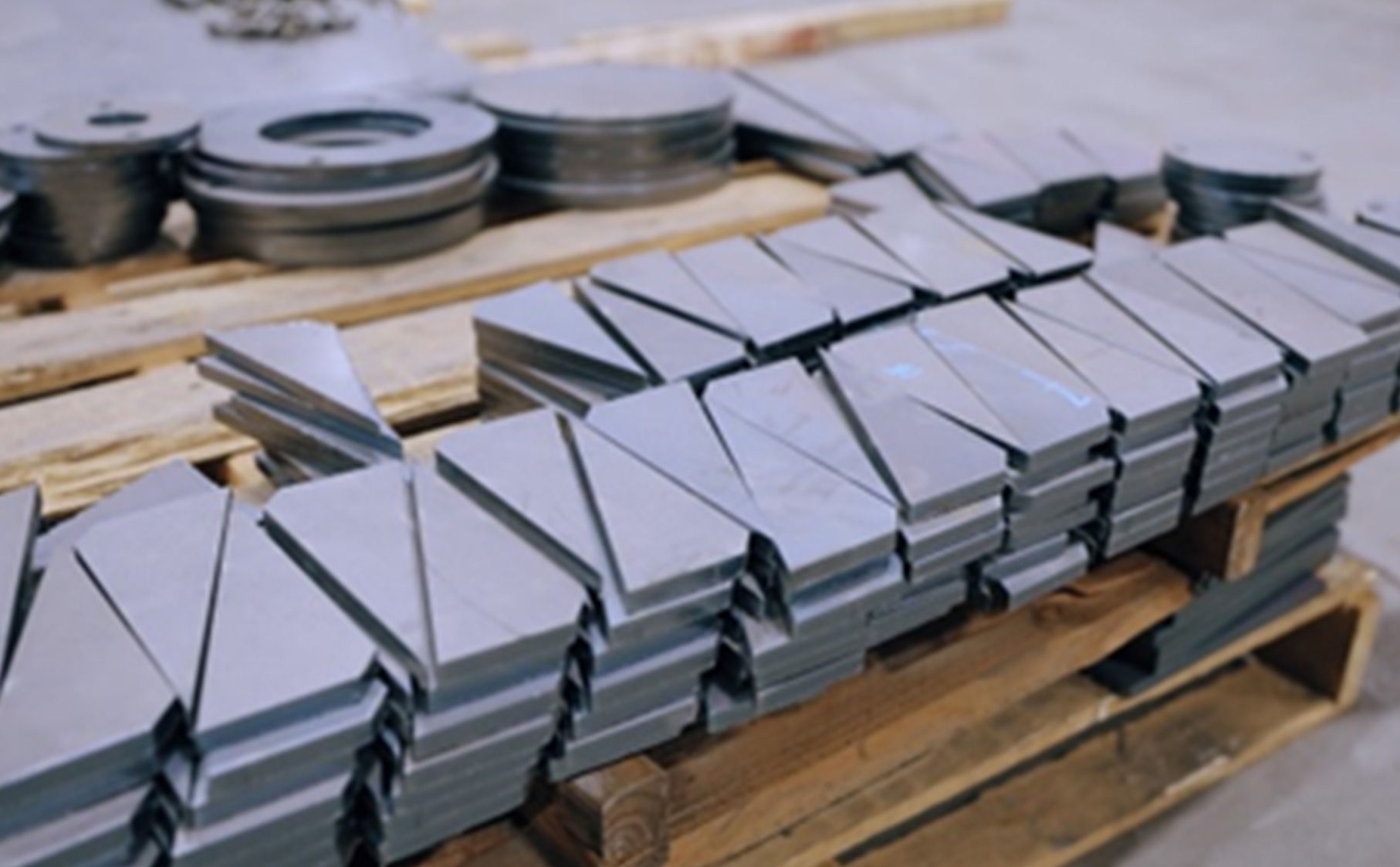
Unlike previous experiences with other manufacturing equipment, Mazak provided on-site training for training for the new laser machine, ensuring a seamless transition for Western Steel’s team. “Mazak came to our facility and trained our employees on our actual machine at our request,” Olesky shared. “After a few days of training, we had a great starting grasp on the system. After Mazak’s trainers left, with the orange support system, our operators could get assistance within minutes of requesting it to fine-tune the machine,” said Olesky.
“During initial startup and over the first few weeks of operations, we encountered some mechanical problems. While this is not surprising and typically expected of a new machine, Mazak was there with support immediately and almost always had a tech onsite within 24 hours of first reporting the problem. I couldn’t speak more highly of how Mazak handled it,” said Olesky.
The OPTIPLEX 3015 NEO 15kW allowed Western Steel to retire an older high-definition plasma and a waterjet, enhancing their production efficiency. “Not only was the new laser capable of handling the combined workload of both those machines, it allowed us to bring our overall production back to a 3-5 day lead time. We currently run the machine with a 3-man crew on each shift. Not only does the machine produce a substantially larger amount in a given shift, it does so at a cheaper hourly rate than our plasmas,” Olesky commented. He also added that their average plate utilization is nearly 20% higher than on the plasmas due to how tightly they can pack parts onto a sheet. Another area in which NEO is more efficient is the after-cutting cleanup. Olesky reported that 95% of parts have no edge cleanup after cutting, unlike plasma, where 100% of parts must be run through the surface finisher or hand-grinder to clean up dross-buildup.
Olesky highlighted some timing metrics that shows the success Western Steel has encountered by purchasing the Mazak OPTIPLEX NEO:
- ½” A36 60” x 120” cut into customers parts. Had to be drilled and plasma cut. Run time was 2 ½ hours. 3015 NEO cuts the same job in 30 min.
- ¼” A36 48” x 96” drilled and plasma cut into small parts. Run time on plasma was about 4 hours. 3015 NEO runtime is 25 min.
- ¼” Brass 36” x 120” cut on waterjet ran nearly 6 hours, and 3015 NEO is currently running in 20 minutes.
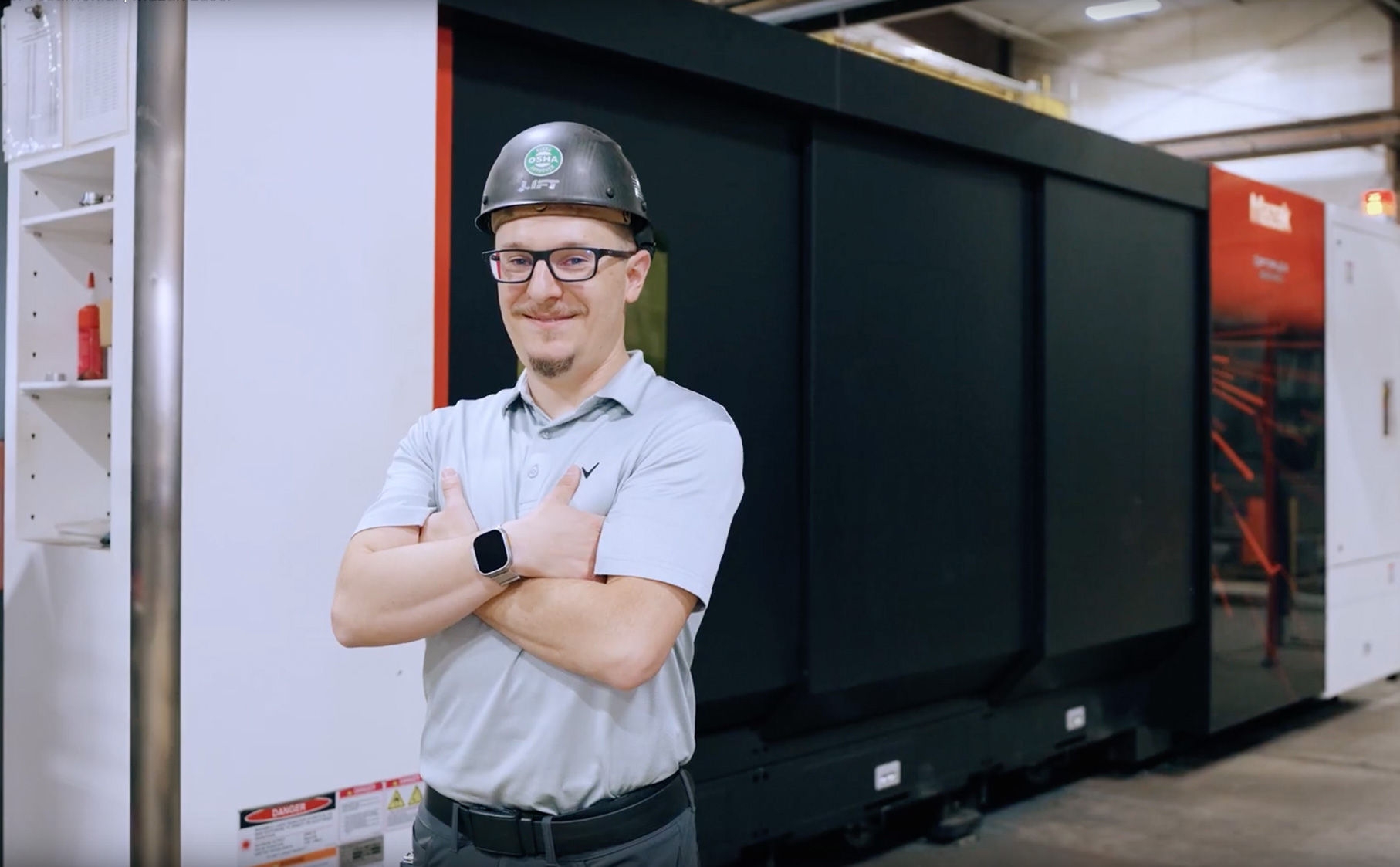
“The quality has really exceeded our expectations, and the reliability has been excellent. Most importantly, we have been impressed with the support,” Olesky stated. The orange support app provides quick service, whether for technical issues, software or programming help, or ordering parts. “It has been the most beneficial and seamless partnership we have experienced with a machine manufacturer,” he added.
Looking ahead, Western Steel plans to add automation to the current NEO and recently purchased an FG-400 NEO tube laser to expand their business. “It truly has become a great partnership,” Olesky concluded.