Maintaining Relevance
Staying up to date with the latest laser-cutting technology from Mazak has proven to be advantageous for Southwest Welding—by increasing efficiency, expanding capabilities, and improving part quality
Southwest Welding started out as a custom welding and repair shop almost 40 years ago in Southwest, Indiana. At the time, the company serviced and repaired equipment for local agricultural and industrial businesses from their 1500-square-foot facility.
However, the company’s focus soon shifted—from offering repairs to providing fabrication services. To facilitate this change, a CNC plasma table was purchased in 2007 to assist with the company’s transition to fabrication. As the need for more precise and cleaner cuts arose, leaders at the company decided to purchase their first laser-cutting machine in 2009, a used 2kW Mazak with a 6’ x 12’ table.
Adapt and Expand
Southwest Welding’s change in business direction and subsequent need for additional fabrication equipment required more space and capacity. The opportunity to purchase a larger building in 2011 resulted in a move three miles away to Wakarusa, IN. The additional capacity and increased customer demand that came with the move warranted the purchase of another used Mazak laser-cutting machine.
As with all laser-cutting machines, regular service and maintenance was required to ensure optimal laser-cutting performance. These required visits resulted in the first of many successful interactions with Mazak’s service and support team members. Mazak’s application engineers provide support for all 2D, 3D, and tube laser machines—including legacy machines. Furthermore, Mazak Optonics offers guaranteed lifetime parts support for every laser-cutting machine. Mazak’s North America Laser Technology Center maintains a large inventory of spare parts and has access to international inventory to quickly respond to part requests for new and legacy Mazak machines.
When we first started looking at lasers, we didn't have any brand in mind. We had found a dealer with a used Mazak at a reasonable price. We were so well pleased with the service we got out of our used machine; we looked at Mazak agin when we needed another laser-citting machine.
Johon Martin, Southwest Welding
Pleased with Mazak’s dependability and service on their used laser-cutting machines, leaders at Southwest Welding kept that in mind when looking to purchase additional laser equipment. “When we first started looking at lasers, we didn’t have any brand in mind. We had found a dealer with a used Mazak at a reasonable price,” shares John Martin, President at Southwest Welding. “We were so well pleased with the service we got out of our used machine; we looked at Mazak again when we needed another laser-cutting machine.”
Confident in Mazak’s equipment and service, the facility was upgraded in 2013 with the first of what would be several new Mazak laser-cutting machines.
Increased Production
The purchase of Mazak’s OPTIPLEX 3015 CO2 4kW assisted in the continuing demand for Southwest Welding’s growing fabrication business. “At the time, we were looking for a dependable machine to cut stainless and aluminum material,” says Martin. “We were very well pleased with the cut quality this machine offered.”
As technological advancements were made in the laser-cutting industry, fiber lasers became more mainstream. Looking to offer customers the latest in laser-cutting capabilities, Southwest Welding’s first fiber laser machine was acquired in 2015—the OPTIPLEX 4020 FIBER 4kW. “This was the first fiber laser we purchased,” comments Martin.
“The machine has proven to be very dependable, and the 6’ x 12’ table size allows us to cut parts that no other vendor can produce for their customer.”
Three years later, leaders at Southwest Welding invested in the OPTIPLEX 4020 FIBER 8kW. “We had an increase in production needs, so we bought our second fiber machine,” says Martin. “The speed and capacity for the 8kW machine over the 4kW was outstanding.”
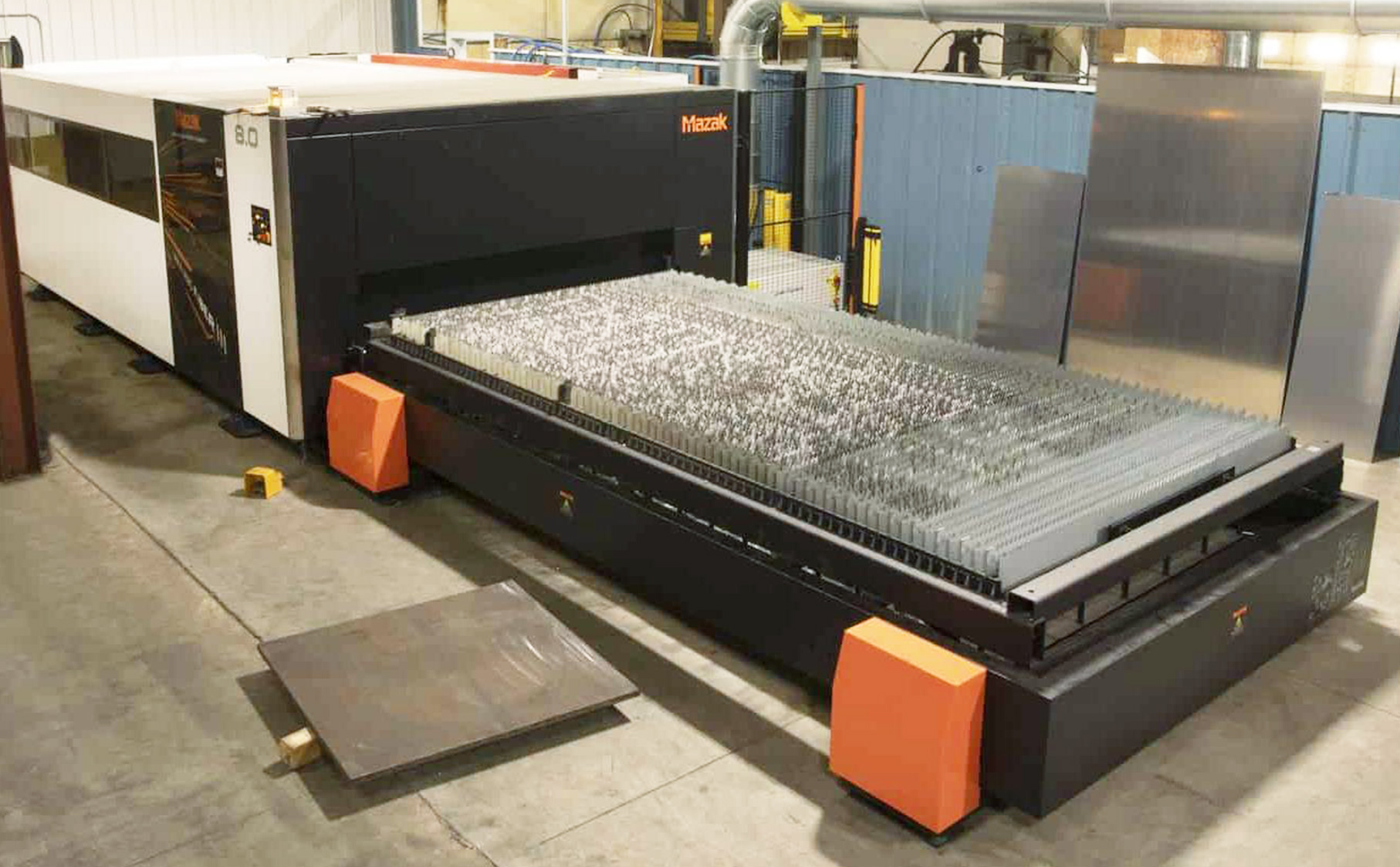
Diversifying Capabilities
The implementation of tube/pipe laser-cutting machines in 2019 and 2020 further diversified Southwest Welding’s fabrication offerings and appeased continual customer demands. Additionally, tapping into the tube and pipe market drew in a new segment of customers.
“With the need for fabricated tube and structural parts, we decided to purchase a tube laser,” shares Martin. “The 3D FABRI GEAR 220 was a very good choice for that application. It has done us quite well with round and square tubing and pipe parts. It also does very well with structural angle and channel parts for the communication tower industry.”
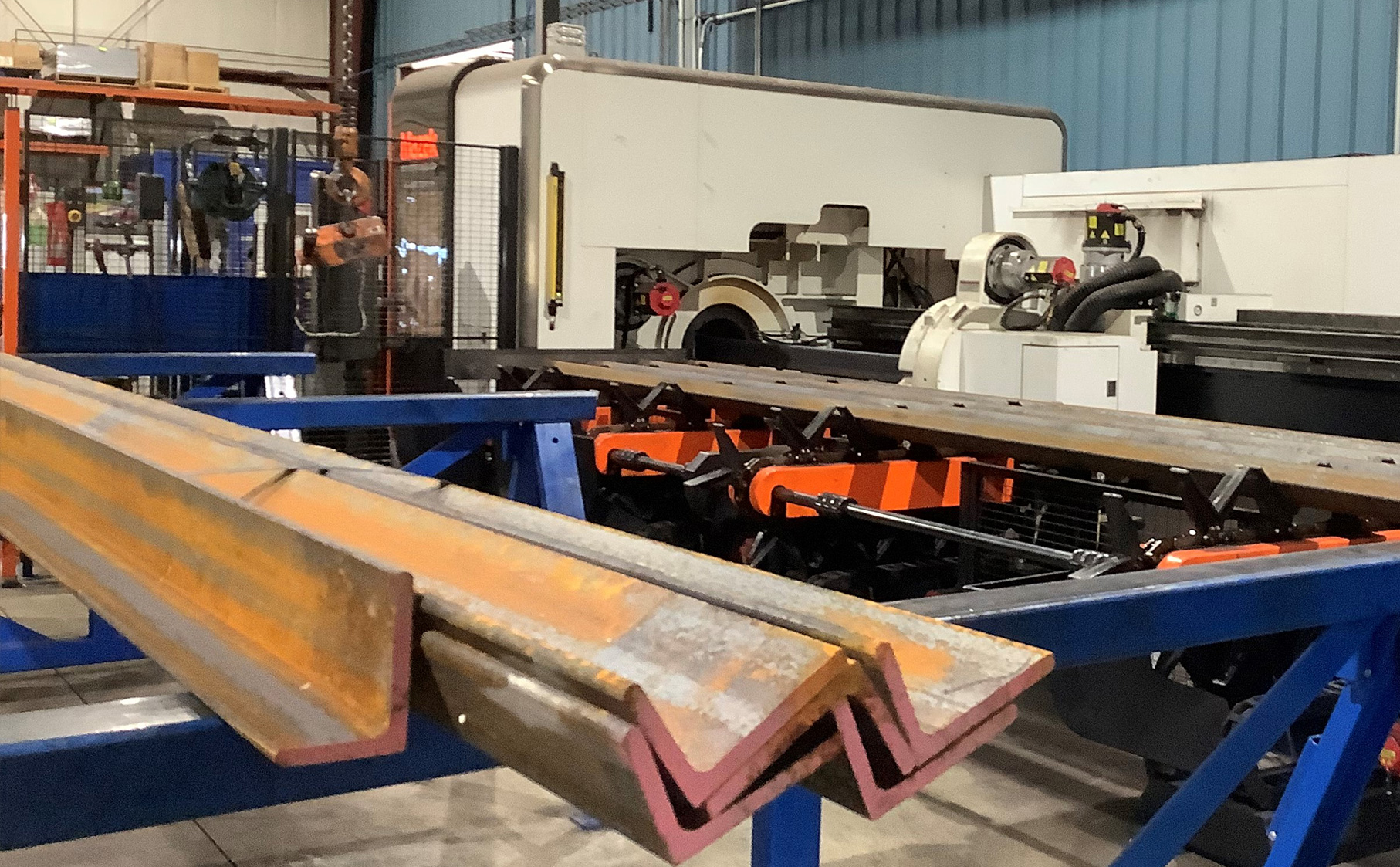
Looking to offer customers the best part quality for tube and pipe with smaller diameters, decision makers were encouraged to consider Mazak’s FT-150 FIBER. “Due to an increase in production, especially in smaller round and square parts, we were introduced to the FT-150 FIBER machine,” explains Martin. “The speed and quality of the cut of the FT-150 is amazing. The fiber machine does especially well with non-ferrous material compared to CO2.”
Continuous Innovation
Committed to providing their customers only the highest quality parts, leaders at Southwest Welding have prioritized keeping up with the latest laser-cutting technologies. Partnering with Mazak has proven beneficial; the Southwest Welding team knows they can count on Mazak for the most up-to-date technology in the industry. This is best exemplified by a couple of the most recent additions to Southwest Welding’s laser-cutting lineup.
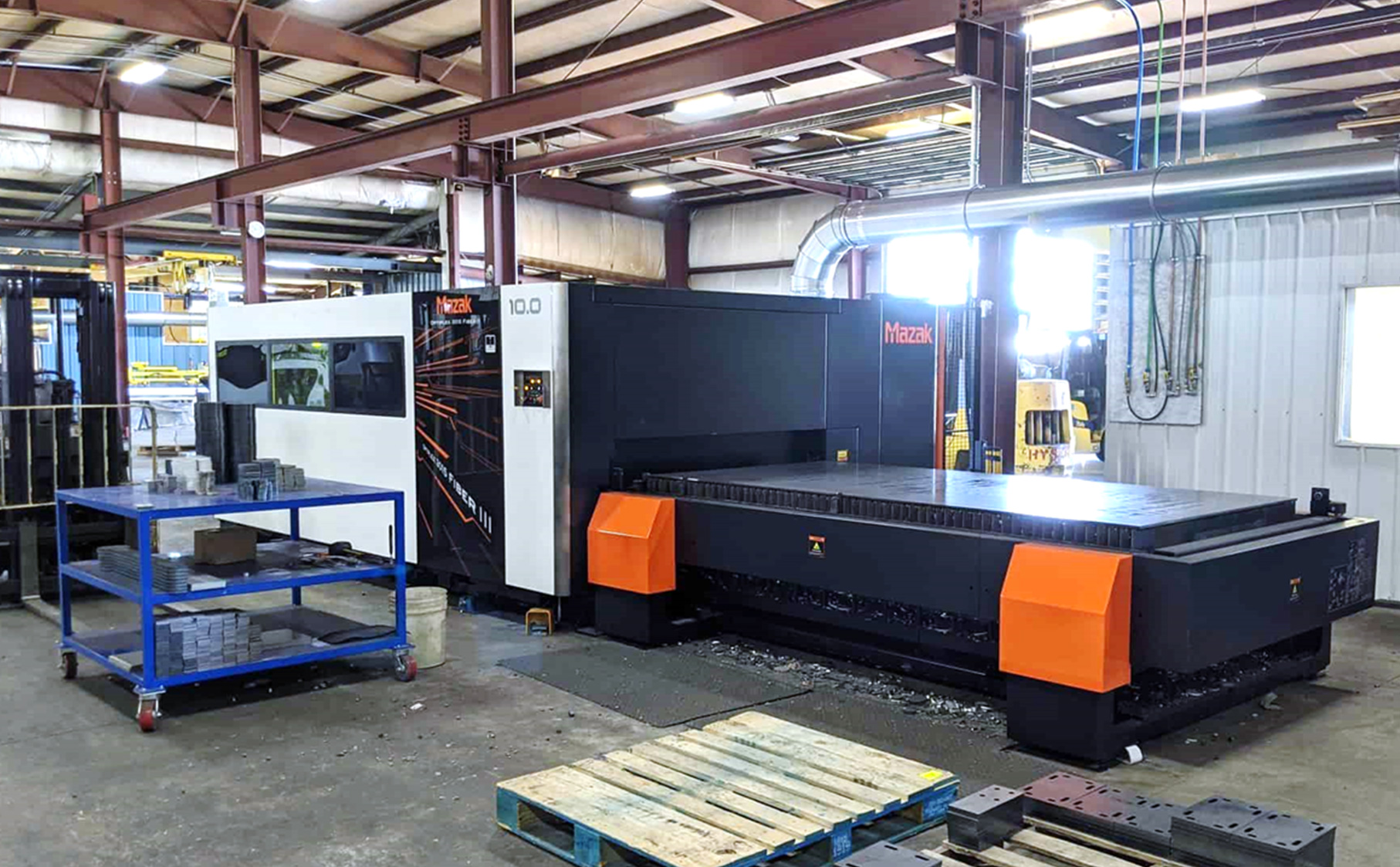
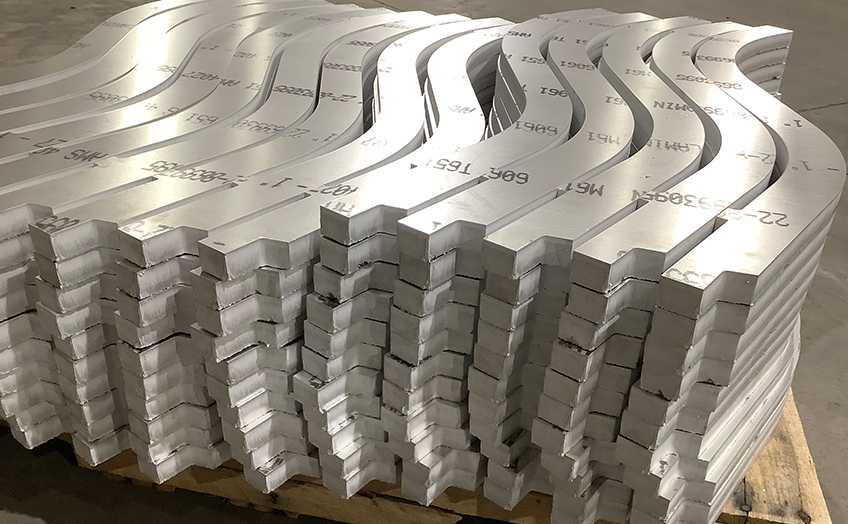
The high-power OPTIPLEX 3015 FIBER III 10kW has provided Southwest Welding the advantage of cutting thicker material. “We were looking for more power to cut steel and aluminum,” shares Martin. “The 10kW laser from Mazak is a very impressive machine with its cut quality and speed. We were able to cut 1’’ aluminum for a customer that was otherwise not possible with any other machine.”
Mazak’s introduction of groundbreaking Variable Beam Parameter Product (V-BPP) technology on the OPTIPLEX NEXUS FIBER S7 has offered better control of the laser beam and superior cut performance. The addition of Mazak’s C-Series automation has further optimized operations by assisting with the more monotonous task of loading/unloading material. “With an increase in production needs, we were advised by Mazak personnel about the S7 model and have been impressed with the cut quality of this machine,” shares Martin. “This was also the first laser cutter we installed with automation and that has really helped our production output.”