Expanding the Product Mix at Plimetal
Montreal shop invests in tube laser that can handle heavier gauges, unique shapes
Article published in the January issue of Canadian Fabricating & Welding.
Plimetal Inc. is a Montreal-based shop founded in 1986 that specializes in laser cutting and bending for a variety of industries in Quebec. The shop works in steel, aluminum, and stainless steel and cuts both sheet and tube.
“With the market constantly evolving, we do a lot of construction work but also various jobs for equipment builders and general fabrication,” said Jonathan Palumbo, the second generation of the Palumbo family to manage the business. “We even do some finished product, like signs and decorative metal work, but we do no welding or painting. We really try to specialize in working with the client to cut and bend parts precisely for them.”
A lot of the company’s work is custom, which involves producing one-offs as quickly as possible.
Tube Upgrade
Plimetal had been cutting tube with lasers for a number of years when management decided it needed to expand its capabilities.
“The tube laser we were running before was designed for high production of thinner and smaller tubes,” said Palumbo. “Our maximum diameter on that machine is 10 in., and the maximum length is 24 ft. Loading the material on that machine works well, but if we are making large parts on it, it has to be unloaded manually.”
The key niche that Plimetal wanted to expand into was structural steel.
“With our flatbed lasers we do a lot of base plates for construction companies,” he said. “Our customers always wanted us to supply the beams to go with that, and now we can.”
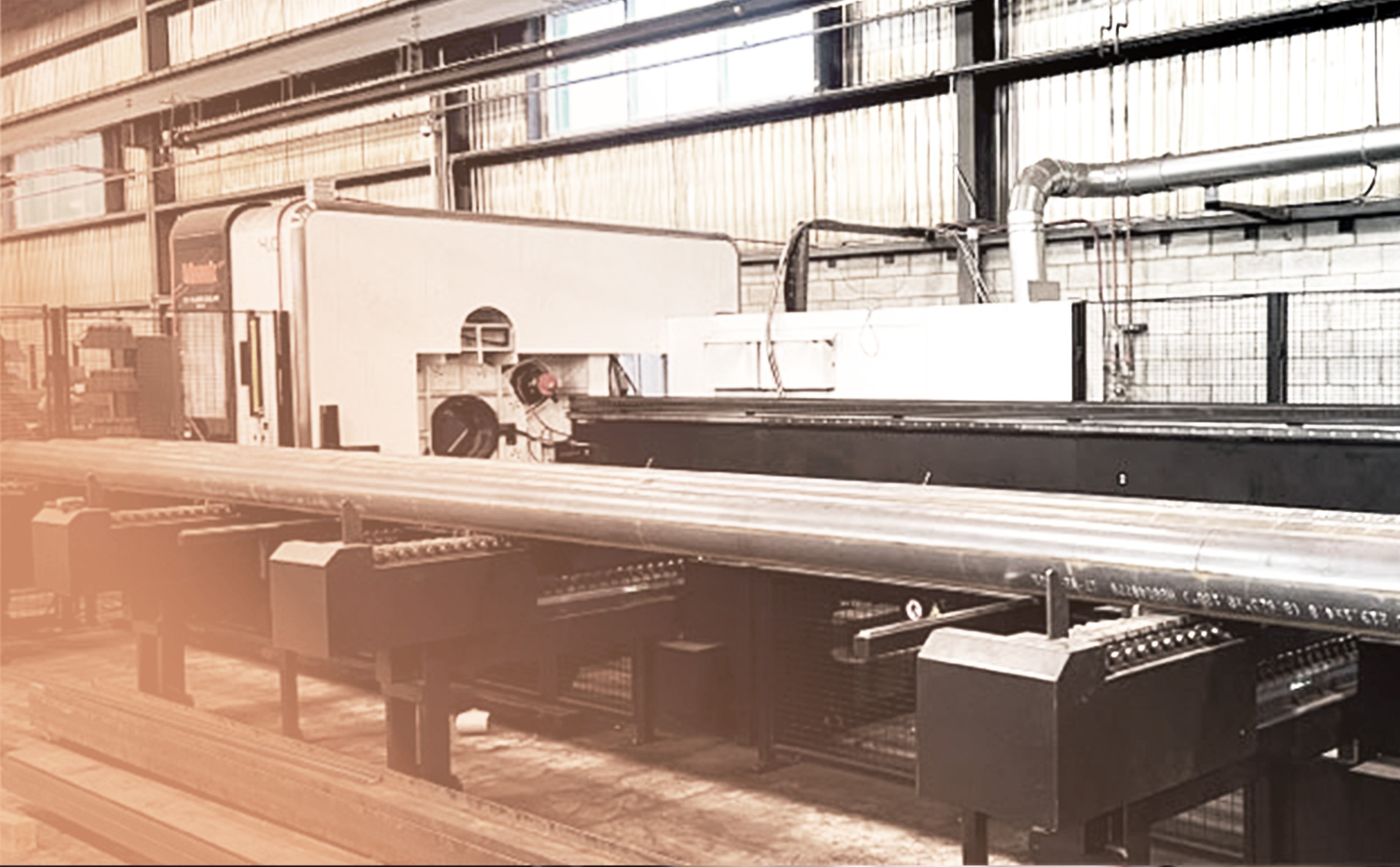
In 2019 the company installed a Mazak 4kW FABRI GEAR CO2 tube laser, purchased through Westway Machinery. “Mazak was just coming out with the fibre laser version of the FABRI GEAR—I think we missed out on that by about two months—but for the work we are doing, the value isn’t so much on speed as it is on accuracy and durability,” Palumbo said.
Moving Parts
For Palumbo and the Plimetal team, the new machine was a bit of an adjustment from the machine they were used to.
“There is just a lot more going on, so I would say it took two or three months to feel completely confident with all the new capabilities and moving parts on the machine,” he said. “For instance, it has a bevel head, whereas our older laser didn’t, and instead of two chucks operates with four.”
The maximum diameter on the FABRI GEAR is 16 in., and the maximum length of raw material is 48 ft.
“With the four chucks, we can put a 10-ft. pipe in and not lose anything from it because of where the chuck holds it. It can work the whole piece.” But perhaps the biggest plus in Palumbo’s mind is the ruggedness of the machine.
We definitely gained a new range of customers with that machine. It can handle structural steel, angle iron, and C channels. Buying profiles and cutting them helps us reduce prices to the customer.
Jonathan Palumbo, Plimetal
“We definitely gained a new range of customers with that machine. It can handle structural steel, angle iron, and C channels. Buying profiles and cutting them helps us reduce prices to the customer.”
The ruggedness has also meant less maintenance. “The main priority in our business is how fast you can produce, so service is important,” said Palumbo. “Having a reliable machine is key, and this hasn’t disappointed. Any service that we need arrives quickly. And you’d think that with this machine handling such big materials it would be at greater risk of damage, but it hasn’t been an issue at all.”
Article published in the January issue of Canadian Fabricating & Welding.
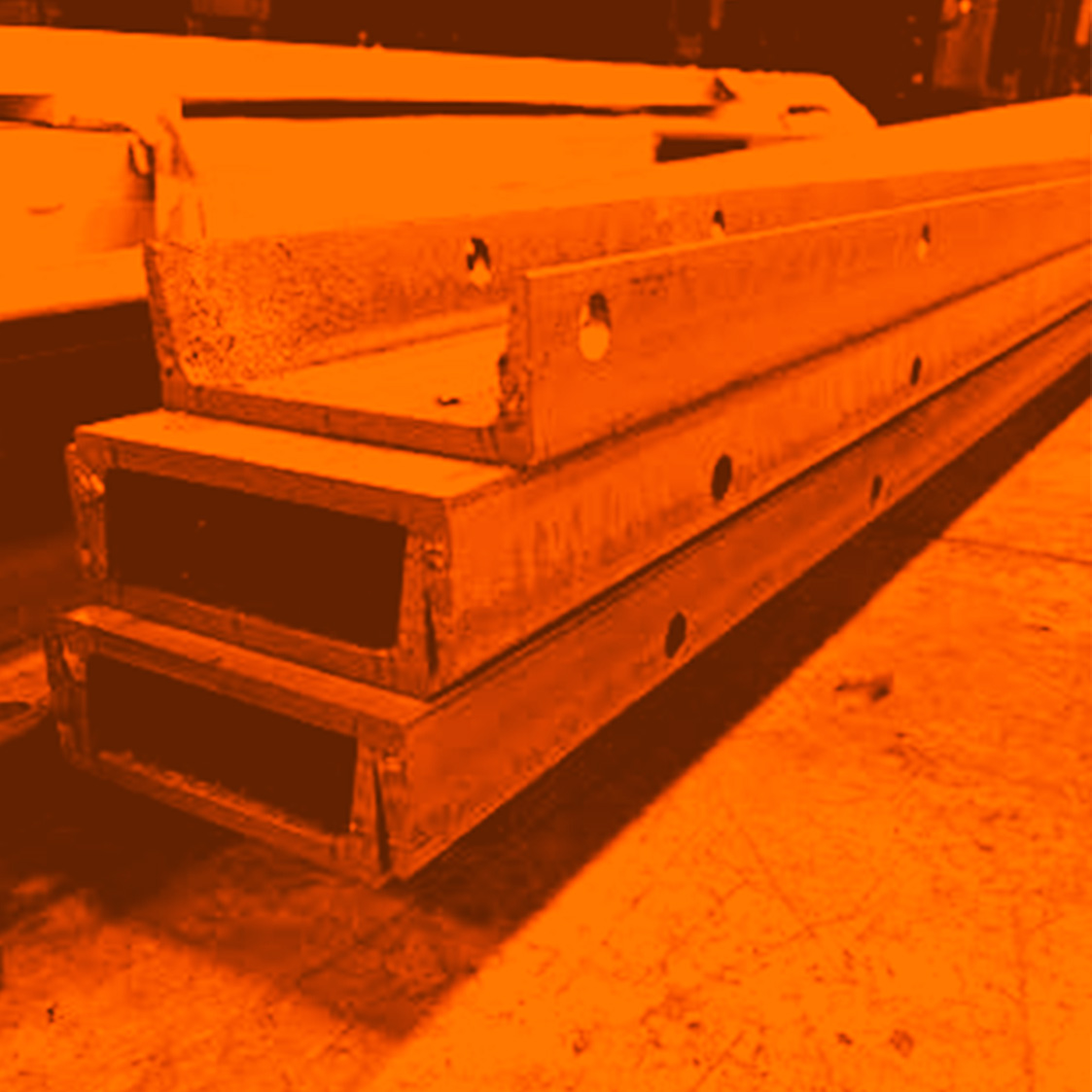