Chuck size | 8″ |
Max. machining diameter | Φ500 mm |
Max. machining length | 500 mm / 1016 mm |
Multi-Tasking Machines
INTEGREX j-200 NEO
- Exceptional milling versatility allows cutting from all directions with a single tool, reducing the number of tools required
- Wide range of machining options with B-axis indexed every 1 degree
- Main spindle utilizes high-power, high-torque built-in motor spindle
- Visualize energy consumption and regenerative power with the “Energy Saver” feature on the CNC system
- Easy automation with Ez LOADER, an automation cell with a collaborative robot
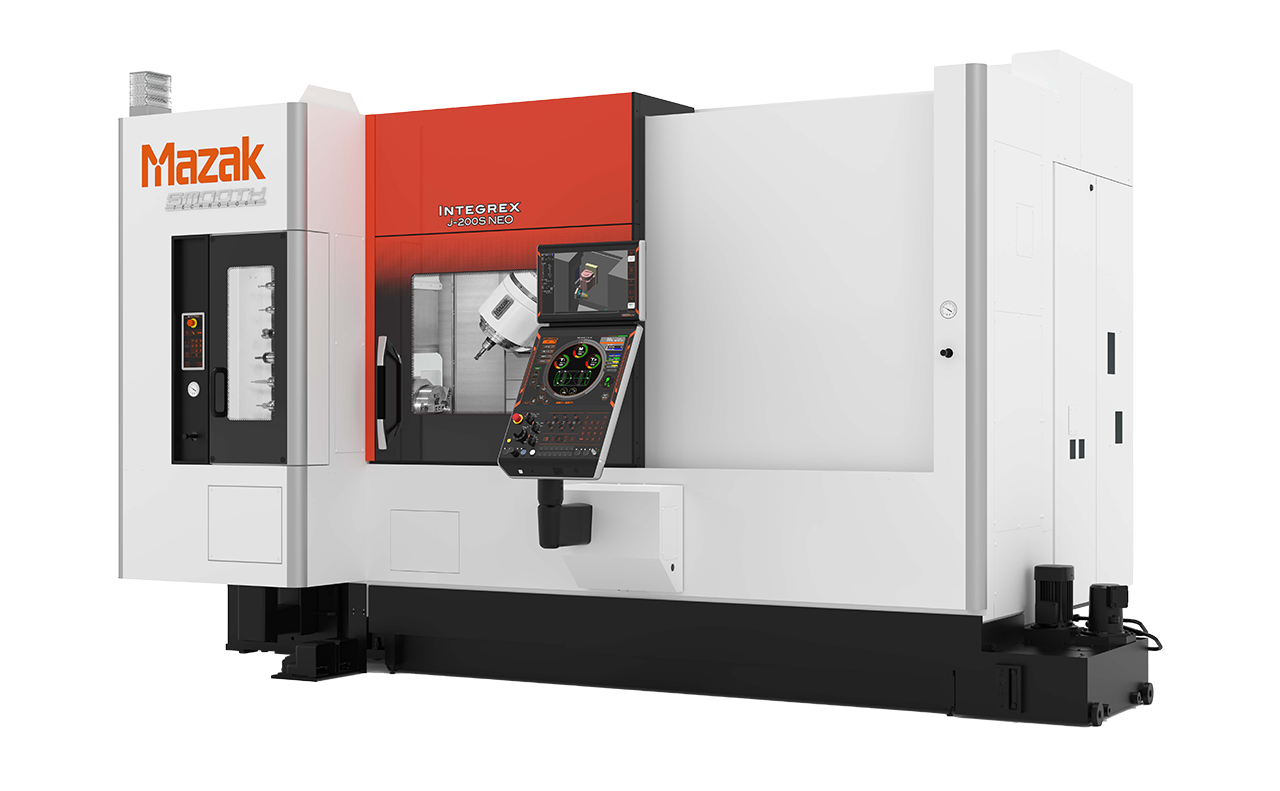
Make up for weak points of turret lathe
Weak points of turret lathe
High-performance specifications for high productivity
Specifications | Milling spindle (40% ED) | Main spindle (40% ED) | ||
---|---|---|---|---|
Standard | Single spindle turret | 1° index | 12000 min-1, 7.5 kW, 27.5 N・m | 5000 min-1, 15 kW, 167 N・m |
High-performance | Compact single spindle turret | 0.0001° index | 12000 min-1, 18.5 kW, 57.3 N・m | 5000 min-1, 18.5 kW, 326 N・m |
Exceptional milling versatility for multi-face machining
The milling spindle unit can be indexed in 1 degree increments, allowing outer diameter, end face, and diagonal machining with a single tool. Similarly, the second spindle performs various machining with a single tool, reducing cycle times. The high-performance specification with 0.0001° indexing offers enhanced versatility for a variety of workpieces.
- 1: |180°
- 2: |30°
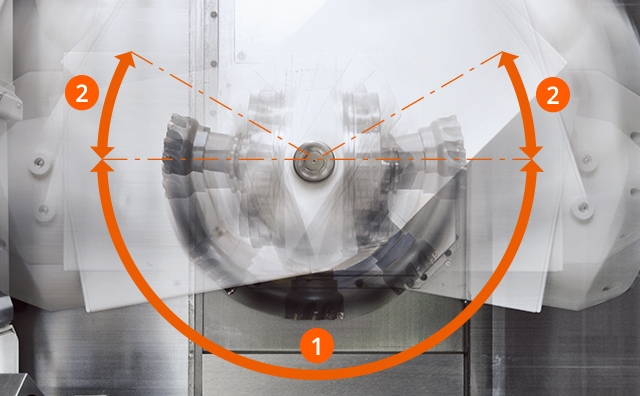
Main spindle: designed for a wide range of workpieces
The high-power, high-torque built-in motor spindle provides excellent machining capabilities. The high-performance specification provides even higher power and torque at 18.5 kW (25 HP) and 326 N·m, enabling further improvements in productivity.
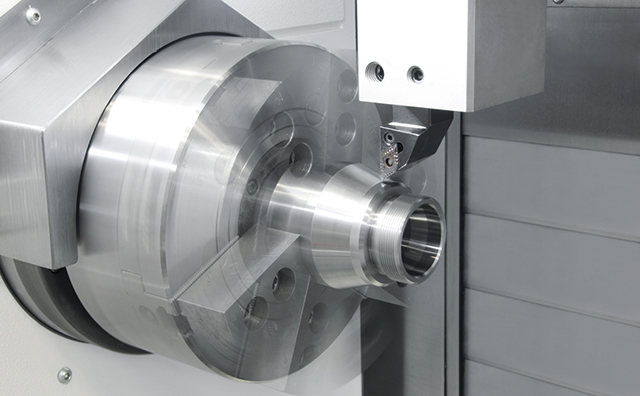
Second spindle performs continuous machining (INTEGREX j-200S NEO)
This is effective in reducing setup time for workpieces that require phase alignment. Continuous first and second machining to the finished workpiece contributes to machining accuracy.
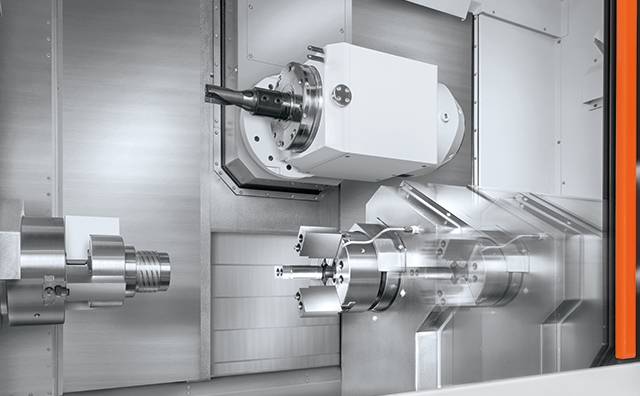
Improved environmental performance with energy-saving equipment
Energy Saver
Energy consumption and the regenerative power produced through the energy saving equipment can be viewed visually on the CNC system to stimulate awareness of energy conservation. In addition, the system can control coolant and other equipment based on the cutting amount to reduce power consumption. * An optional Smooth coolant system is required for the control of coolant and other equipment.
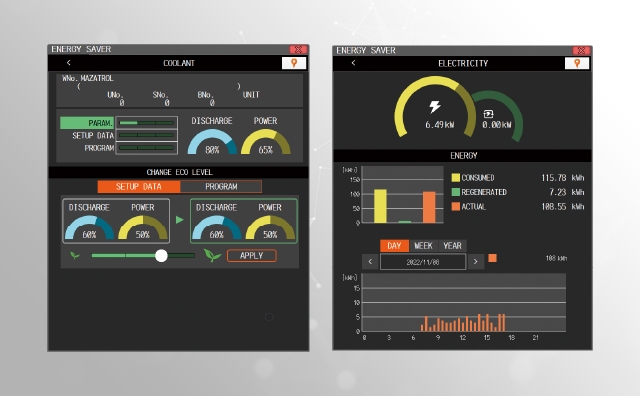
Environmentally friendly Smooth Coolant System*
Optimal control of coolant discharge amount
Energy saver automatically determines the optimal coolant discharge for energy-saving machining. Processing with reduced power consumption is possible at all times.
*Optional
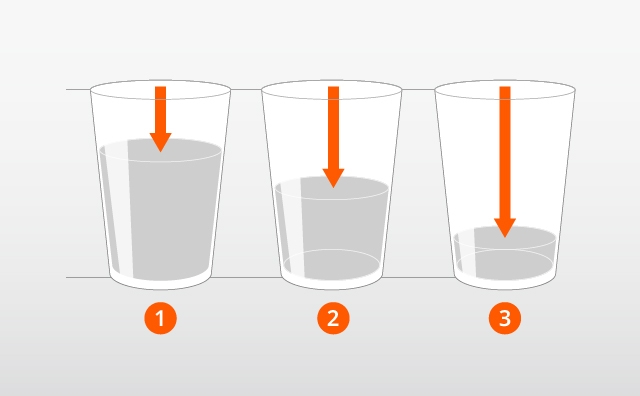
Energy-saving coolant system with sludge removal performance
No need to frequently clean the tank
The coolant tank has a coolant jet that makes a vortex in the center so that small machined chips will not settle in the tank. This feature makes it possible to keep the coolant tank clean and extend the service life of the coolant. Ease of maintenance is also ensured. The frequency of coolant changes is reduced as well as CO₂ emissions at coolant disposal.
Smooth Coolant installation results
- The conventional coolant tank
- Smooth Coolant System
Reference Video
INTEGREX j-200 NEO
INTEGREX j-200 NEO (High Performance Specification)
Chuck size | 8″ |
Max. machining diameter | Φ500 mm |
Max. machining length | 500 mm / 1016 mm |
INTEGREX j-200S NEO
Chuck size | 8″ |
Max. machining diameter | Φ500 mm |
Max. machining length | 910 mm |
INTEGREX j-200S NEO (High Performance Specification)
Chuck size | 8″ |
Max. machining diameter | Φ500 mm |
Max. machining length | 910 mm |