Chuck size | 10″ |
Max. machining diameter | Φ700 |
Max. machining length | 1574 mm / 2594 mm / 3074 mm |
Multi-Tasking Machines
INTEGREX i-500
- Ease of operation and compact design of the INTEGREX i series with a large machining area equivalent to that of the INTEGREX e-H series
- Exceptional performance versatility - Special processes, such as gear machining with end mills, gear hobbing, and deep drilling, are now incorporated on one machine, achieving process integration.
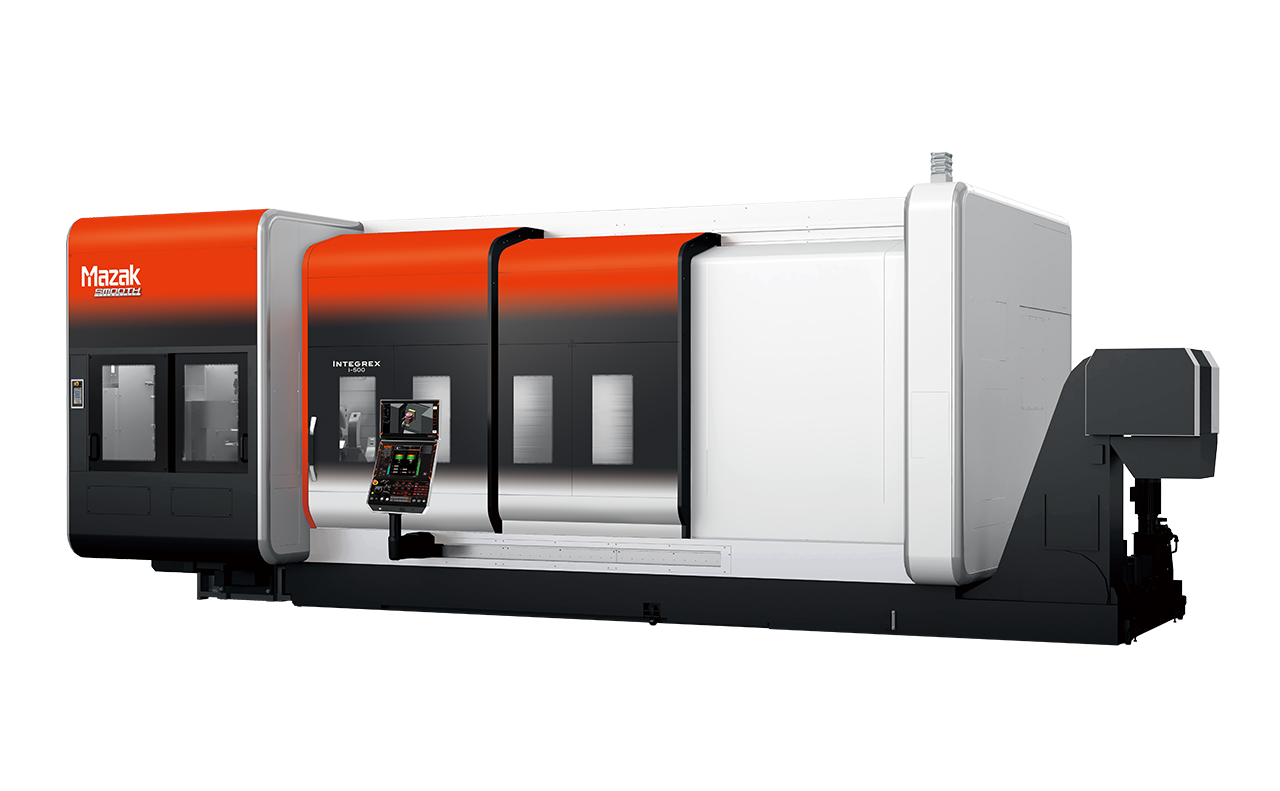
A wide variety of specifications to meet your production requirements
A wide range of bed length type for large-diameter and long workpieces. A variety of tailstock, second spindle, and lower turret specifications can be selected, as well as turning spindles and milling spindles. Optimal customization is possible for machining in all industries.
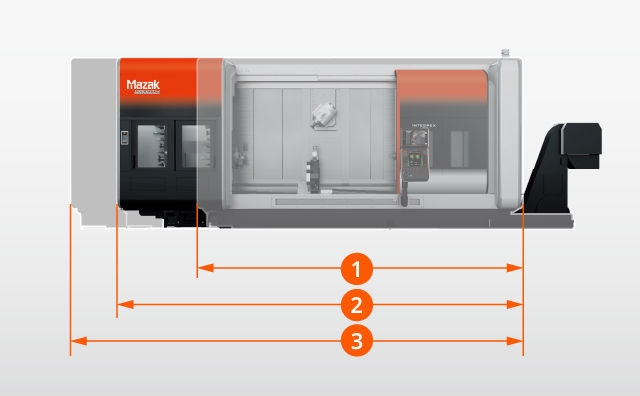
Universal
1: 1500U
2: 2500U
3: 3000U
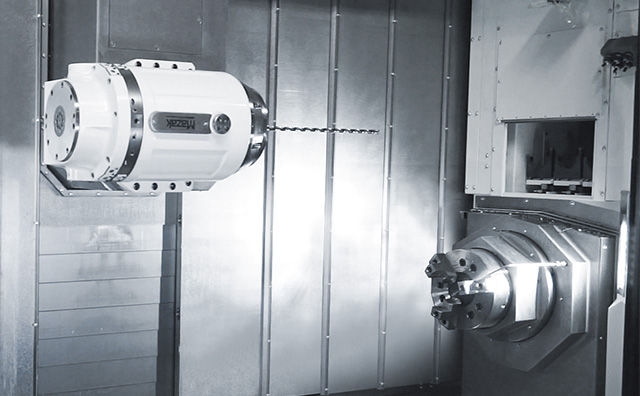
Second spindle
Standard type 4000 min-1
High output type 3300 min-1
High output and high torque type 2500 min-1
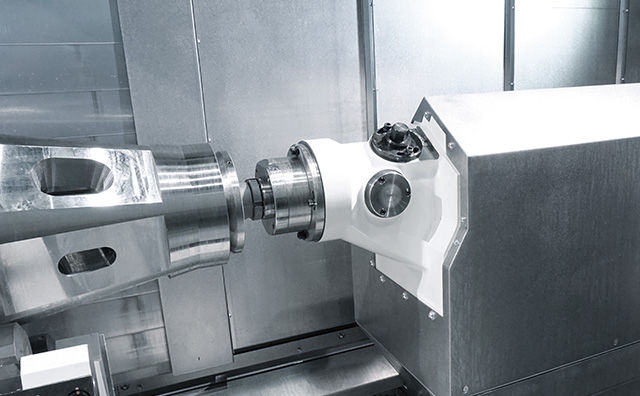
Tailstock
MT No.5 Built-in center
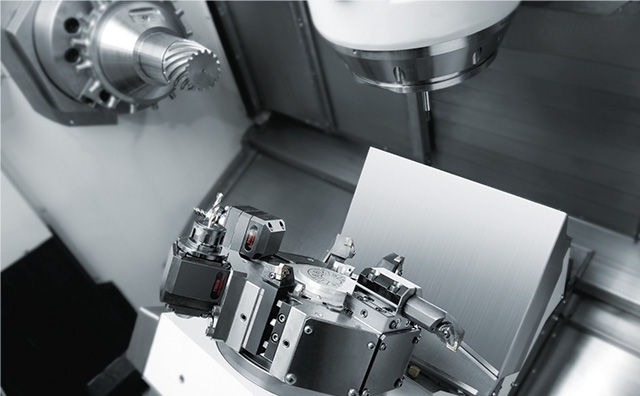
Lower turret
9D (turning/milling)
Compact milling spindle and large machining area minimize interference
The standard compact milling spindle is 17% shorter in overall length than the conventional milling spindle, increasing the machining range and reducing the interference.
Long Y-axis stroke : 430 mm
Max. swing / Max. machining diameter : Φ 700 mm
X-axis Travel: 845 mm
Y-axis Travel: 430 mm
Pursuit even more high-accuracy machining
B-axis and C-axis achieve high-accuracy machining
B-axis is equipped with a roller gear cam with no backlash, and C-axis is equipped with a full circumference disc brake. Both B-axis and C-axis are equipped with high-performance and high-accuracy scales as standard to improve positioning and contouring accuracy.
B-axis: min. indexing increment 0.0001° (roller gear cam)
C-axis: min. indexing increment 0.0001° (full circumference disc brake)
X-, Y-, Z-axis ball screw core cooling as standard
Temperature-controlled cooling oil circulates through the ball screw cores to reduce heat and thermal effects from the servo motor.
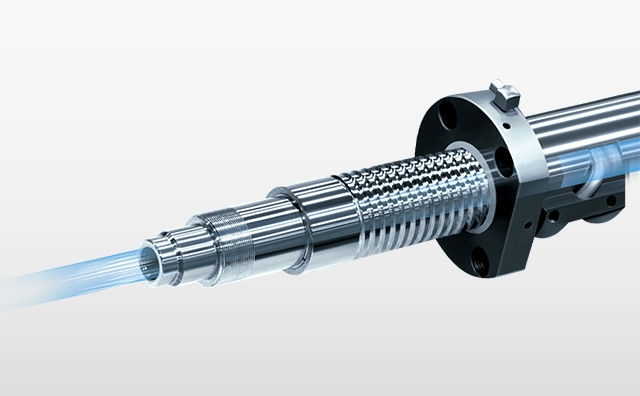
Wide range of milling spindle greatly contribute to productivity improvement
The milling spindle is equipped with a high output and high torque integral spindle / motor. In addition to standard No.40 taper spindle, high speed and high output specifications as well as a No.50 taper spindle are optionally available to meet the various machining requirements.
No.40 standard spindle 12000 min-1
No.40 high output spindle 12000 min-1 *
No.40 high speed spindle 20000 min-1 *
No.50 high output spindle 10000 min-1 *
* Option
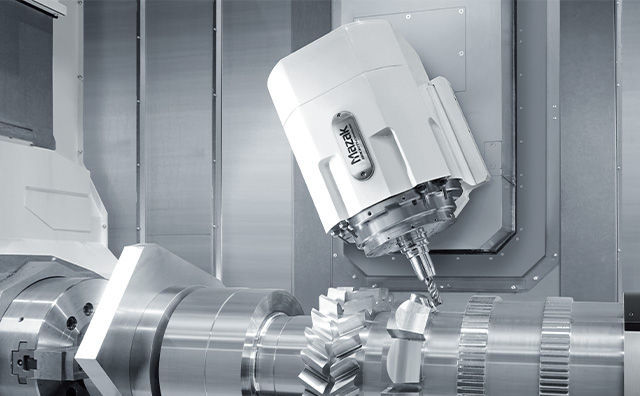
4 sizes of spindle bores for turning spindle
Optimal selections based on the machining requirement
The integral spindle / motor makes it ideal for continuous machining of first and second operations.
The first and second turning spindles can be completely synchronized, enabling high-speed, high-accuracy machining of thin, long workpieces.
C-axis (0.0001° indexing increment*) achieves indexing accuracy comparable to that of rotary axis on machining centers by employing a full circumference disc brake and a magnetic detector.
*Standard specification for second spindle is 0.001°.
4000 min-1 standard spindle, Φ91 mm bore
3300 min-1 high output spindle, Φ112 mm bore*
2500 min-1 high output and high torque spindle, Φ132 mm bore*
2000 min-1 high output and high torque spindle, Φ185 mm bore*
* Option
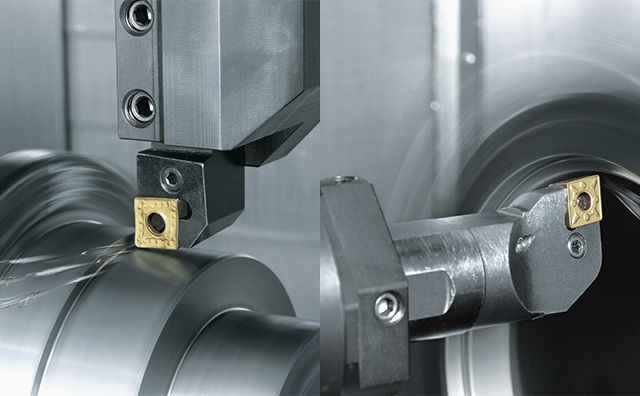
CNC system MAZATROL SmoothAi
Innovative MAZATROL CNC system for higher productivity
MAZATROL SmoothAi offers high operability and high-speed, high-accuracy control, improving productivity by utilizing the Digital Twin, an AI-equipped and advanced digital simulation.
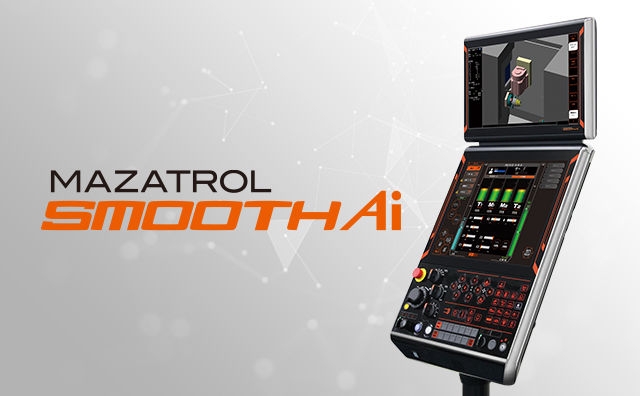
Reference Video
INTEGREX i-500
INTEGREX i-500S
Chuck size | 10″ |
Max. machining diameter | Φ700 |
Max. machining length | 1574 mm / 2594 mm / 3074 mm |
INTEGREX i-500ST
Chuck size | 10″ |
Max. machining diameter | Φ700 |
Max. machining length | 1574 mm / 2594 mm |