Automation Systems for Machining Centers
A full lineup of automated systems to suit production volume and product type
Mazak offers a variety of transport devices to suit the machines and production methods that you have installed. For customers who require a more complex automation system, we will individually propose the optimal system per section.
For Machining Centers
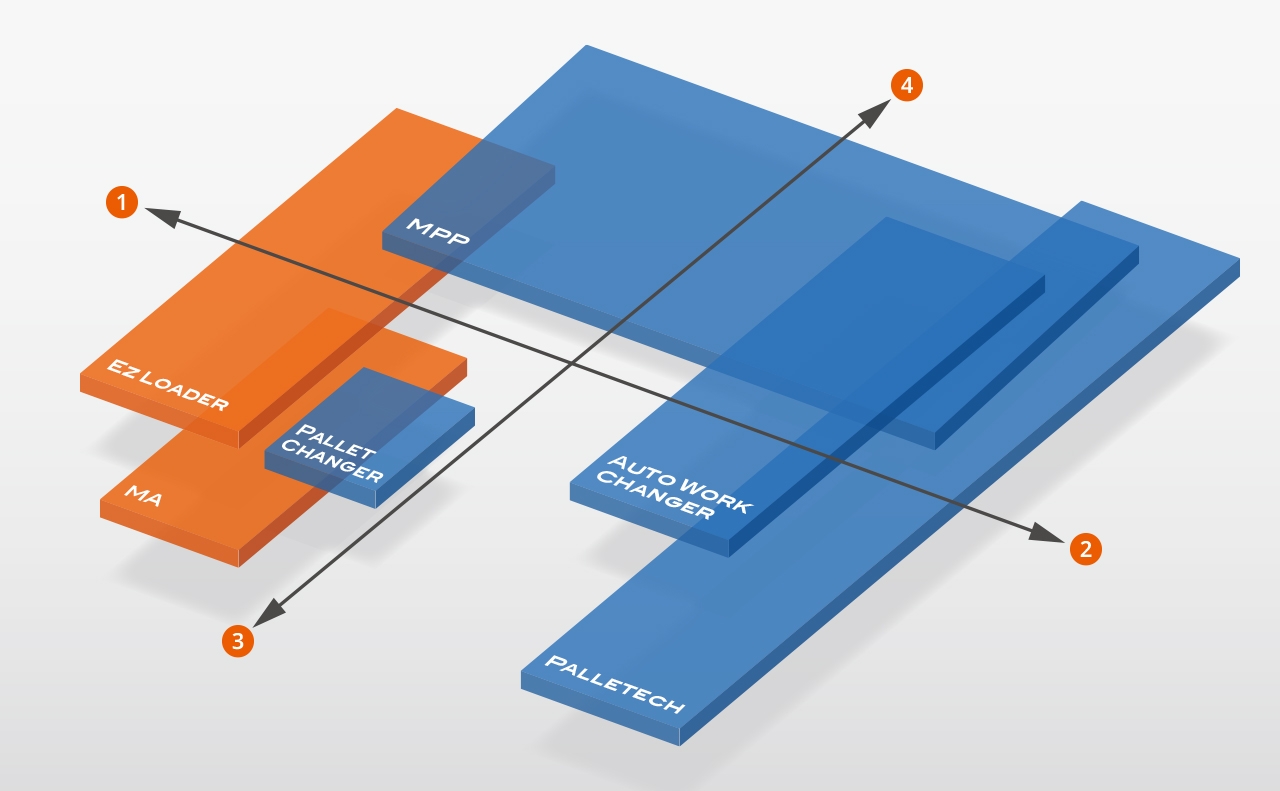
1: Low-volume production 2: High-volume production 3: Low-mix 4: High-mix
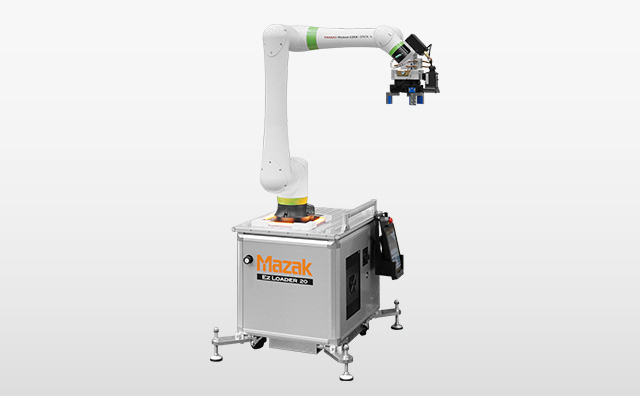
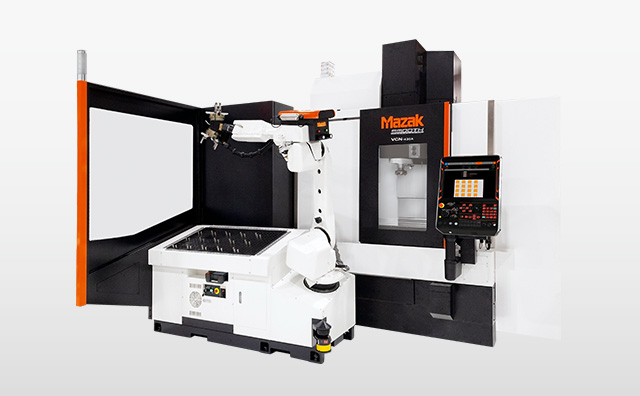
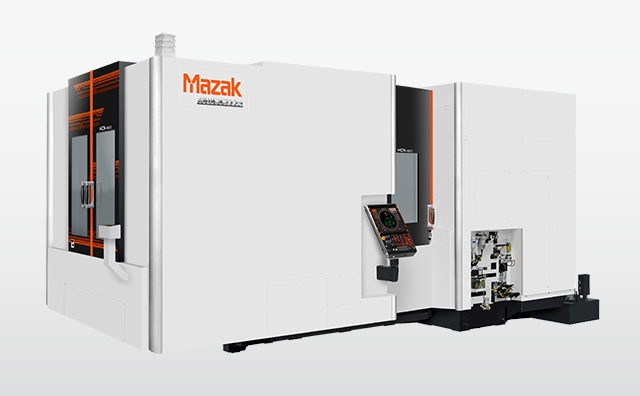
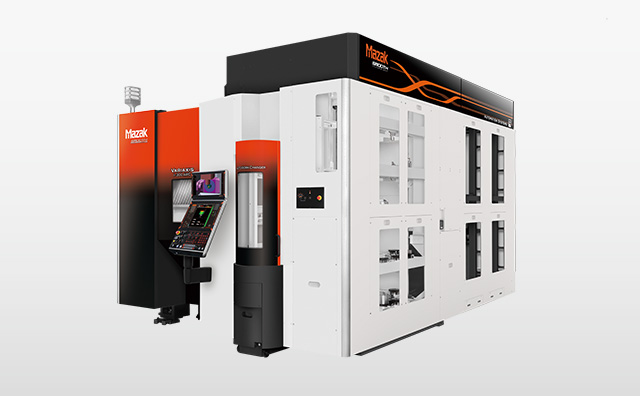
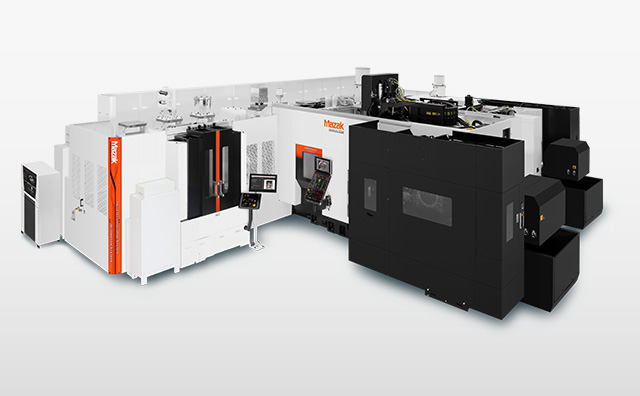
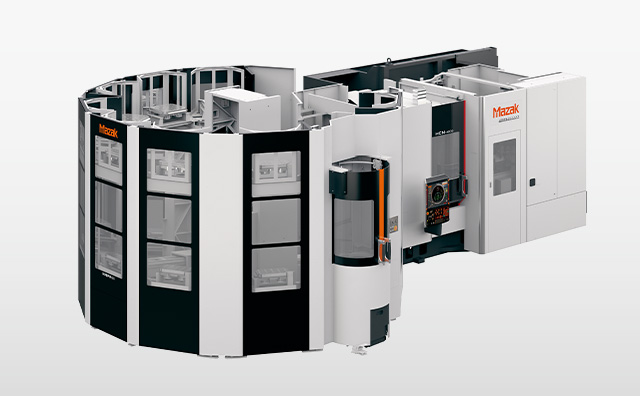
MA(MILL ASSIST)
Machining center Workpiece transport type
An automated system that reduces manpower through a simple operation
- Improve productivity with unmanned continuous operation at night.
- One operator can operate multiple machines.
The easy-to-operate conversational software Smooth TURN ASSIST or Smooth MILL ASSIST allows you to complete automatic operation settings simply by following the instructions in the software; robot teaching is not required.
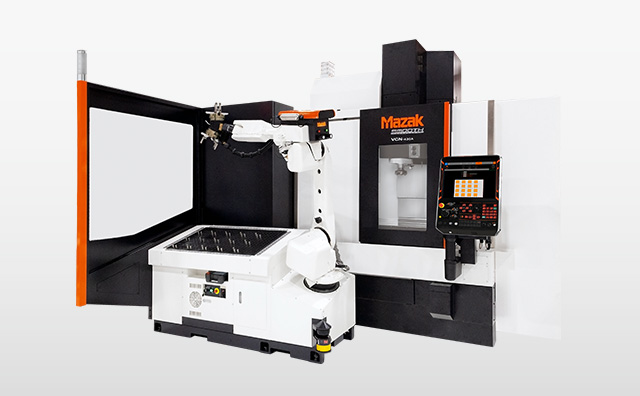
Smooth MILL ASSIST Robotic Autonomous Operating Software
The software is easy to operate through a conversational interface.
- You just need to input the material and the finished product shape. No robot teaching is required.
- Easy operation by simply turning on automatic operation for each lot
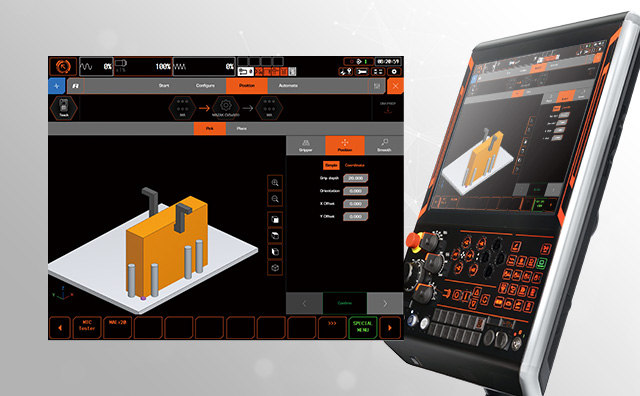
Ez LOADER
Machining center Turning center Workpiece transport type
Compact automation system for
collaborative robots
- Includes a robot arm, a vision sensor, and dedicated software
- Compatible with Mazak’s small and medium-sized multi-tasking machine, CNC turning centers, and vertical machining centers
- Utilizing collaborative robots to create a safe and compact system
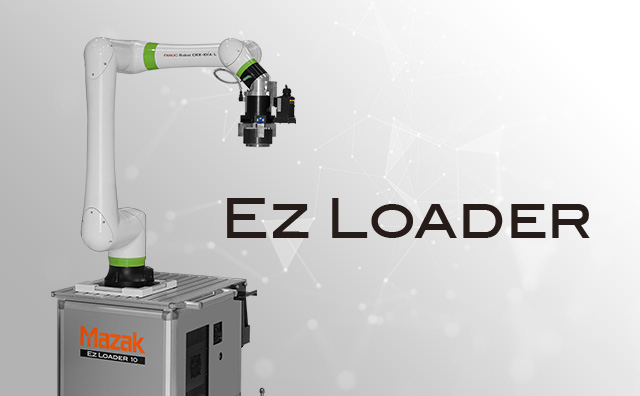
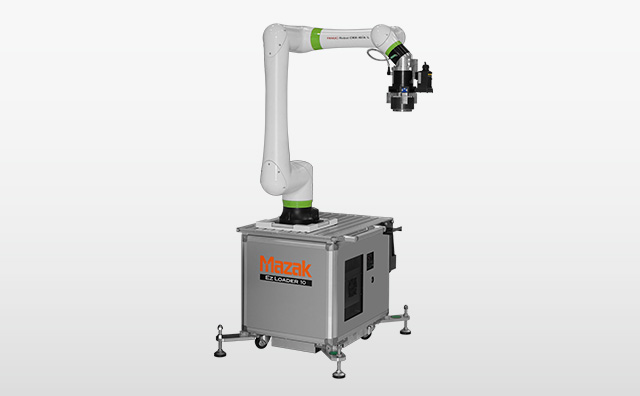
Ez LOADER 10
Maximum workpiece weight : 5 kg
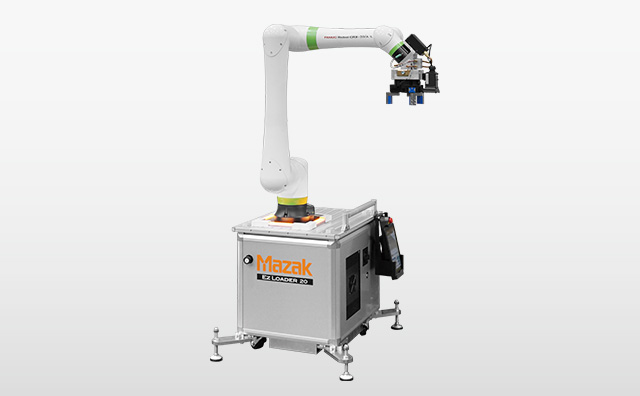
Ez LOADER 20
Maximum workpiece weight : 10 kg
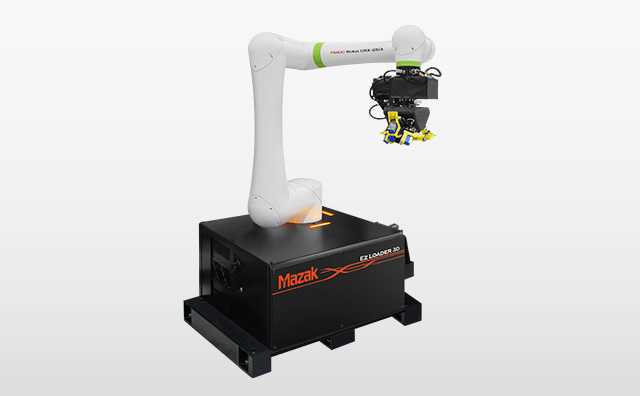
Ez LOADER 30
Maximum workpiece weight: 21 kg*
* Single-handed
Case study
Ez LOADER 20 + measuring unit
This system combines Ez LOADER with a measuring unit. By automatically reflecting the measurement results in tool offset, measuring errors during unmanned operation can be prevented. This system also includes boxing of finished products using the Ez LOADER.
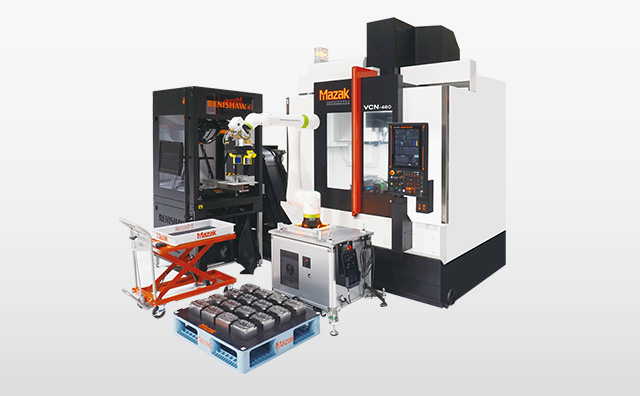
Ez LOADER APP*
Dedicated application for collaborative robot cell operated by MAZATROL
- Includes a robot arm, a vision sensor, and dedicated software
- Compatible with Mazak’s small and medium-sized multi-tasking machine, CNC turning centers, and vertical machining centers
- Utilizing collaborative robots to create a safe and compact system
- Interview
- Considering solutions
- Proposal
- Design
* Only compatible with Ez LOADER 30
Pallet Changer
Machining center Pallet transport type
The next workpiece can be setup
during the machining of the current
workpiece for higher productivity.
Rotary-type pallet changers quickly change pallets with heavy workpieces for higher productivity.
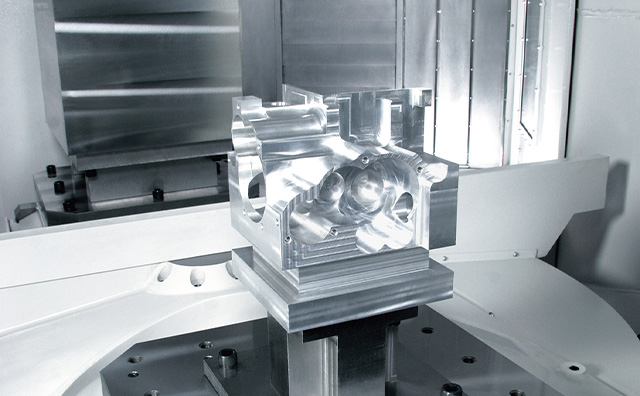
6-pallet changer
Set up multiple workpieces for automatic operation over extended periods of time.
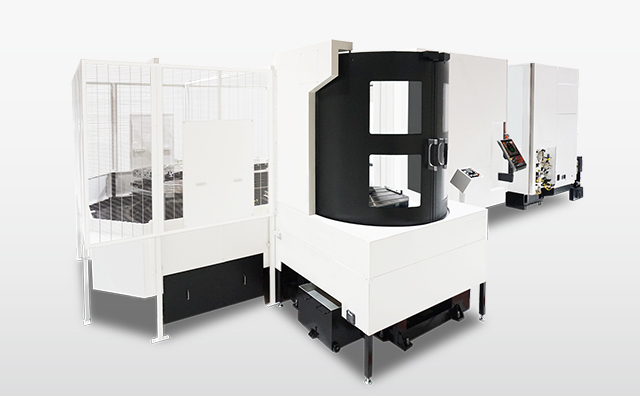
AWC
Machining center Pallet transport type
Automatic Work Changer (AWC)
Materials stored in the work stocker are carried into the machine, and after machining is complete, they are removed and stored in the work stocker. According to the set schedule, materials are loaded and unloaded in sequence for continuous machining.
[Transportable workpieces]
Maximum transportable weight *1: 65 kg
Maximum transportable dimensions *2: Φ350 mm × H315 mm
*1: Workpiece holder included.
*2: Some stockers of the 40 workpiece stocker have different dimensions.
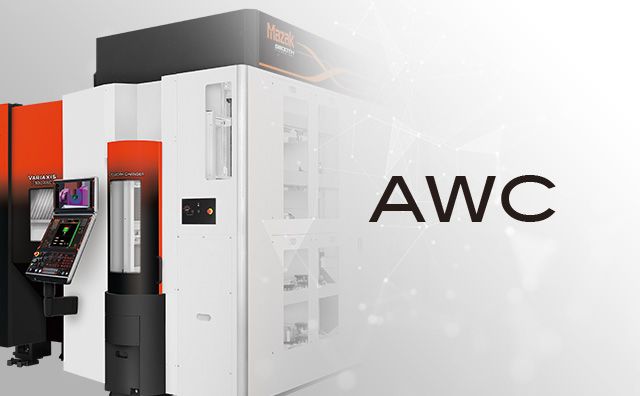
Selectable work stocker
After the initial installation, the work stocker can be expanded from 32 to 40 work stockers, depending on the production situation.
- 1
- 2
Setup management and automatic operation software: Smooth AWC
Smooth AWC is a setup management and automatic operation software for the VARIAXIS i-300 AWC incorporated in the CNC system, MAZATROL SmoothAi.
- The 19- inch touch panel allows for intuitive operation and clear display of the overall AWC system status
- Easy operation even when machining different workpieces with the same fixture on the work holder
- During automatic operation, the operator can be instructed on work setup by switching the CNC screen.
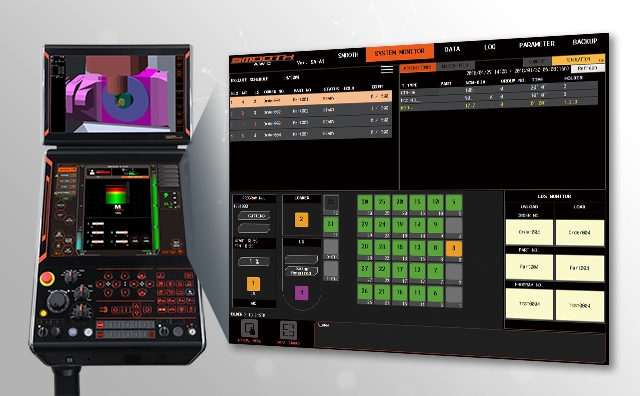
PALLETECH
Machining center Pallet transport type
Automated pallet transfer system
The PALLETECH system improves productivity by making effective use of machines and fixtures with minimal capital investment and by improving system uptime.

- Automatic transport of pallet with fixture and workpieces
- Reduced idle time of machines and fixtures identified through system simulation by optimizing machining schedules
- Highly reliable machines and systems that enable improved system availability
Flexible system expansion
You can choose the optimal size of the "PALLETECH MANUFACTURING CELL" (1-level), "PALLETECH HIGH RISE SYSTEM" (2-level), or " PALLETECH HIGH RISE SYSTEM" (3-level) based on your current production volume and budget. Once installed, it can be expanded as needed to accommodate growing production volumes.
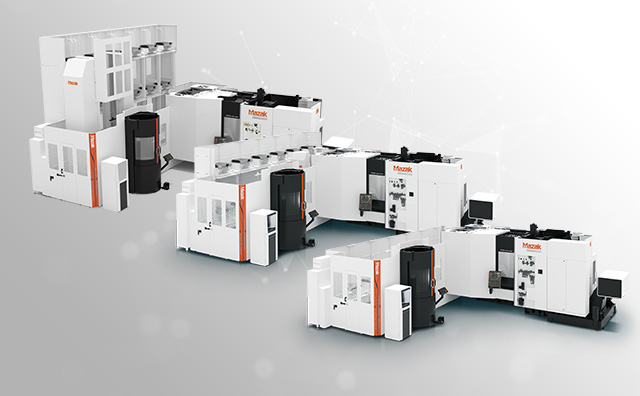
Different types of machine tools can also be incorporated
A horizontal machining center, simultaneous 5- axis machining center, and multi-tasking machine can be integrated into one system.
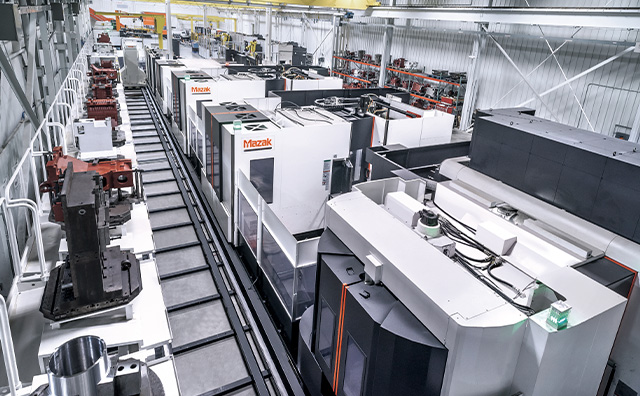
PMC NEO
PMC NEO is software that automatically operates and manages Mazak's flexible manufacturing system "PALLETECH System". With "Smooth simulation", you can check machining progress and tool resources for up to one month in advance during automatic operation, enabling long-term unmanned operation.
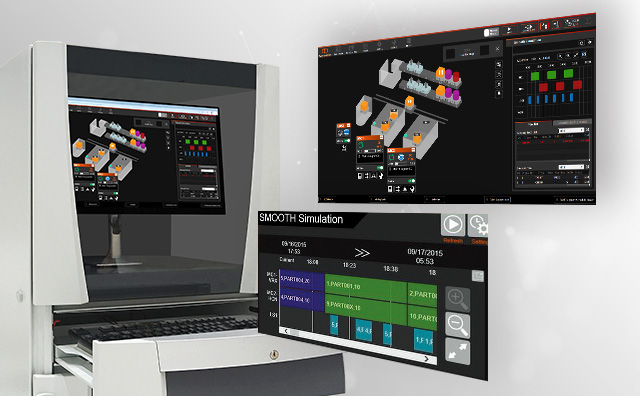
Smooth Simulation
Simulation can be performed for up to one month during automatic operation. Easy tool preparation makes production output easy to predict. It is also possible to level out the machine load.
Scheduling
PMC NEO can be operated according to your production style; schedules based on part numbers that allow for flexible production, or schedules based on simple pallet numbers. It is also possible to operate production that combine multiple part numbers, or complete all the steps one item at a time.
Server PC maintenance
It comes standard with an uninterruptible power supply for unexpected power outages, as well as HDD duplication using RAID. This helps reduce the risk of PC downtime.
Home Screen
The basic screen allows you to see the system status at a glance, and has a similar design with MAZATROL SmoothCNC.
Connectivity
It can also be monitored from an office PC connected via LAN.
Performance tracking
Various performance data is output in a variety of graphs. We have made it easier for administrators to analyze operation.
MAZATEC SMS
Machining center Pallet transport type
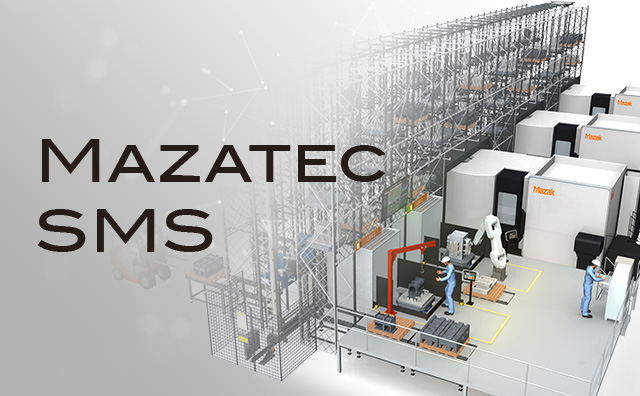
- Machine tools: Maximum 15 units, Loading stations: Maximum 8 units, Warehouse: Maximum 240 shelves.
- The overall length and height of the system can be laid out to suit the installation space in the plant.
- The size of each shelf can be set to up to six different sizes depending on the workpiece, general pallet, or material bucket. Stacker crane enables high-speed transport.
- A station dedicated to the storage and retrieval of material pallets can be installed.
- The loading station is easy to access from two directions, and area sensors ensure safety.
- Smooth PMC is a processing management system that enables diverse operations.
- We can also provide connection and integration with higher-level systems (special order). This customization requires discussion with the customer's system administrator.
MAZATEC SMS processing management system
Having this machining management control software lets you create operation data, check operation status, and machining progress. The software is based on PALLETECH System's Smooth PMC and has been developed to also manage material pallets. In automatic operation, the fixture pallet and material pallet are synchronized at the setup station.
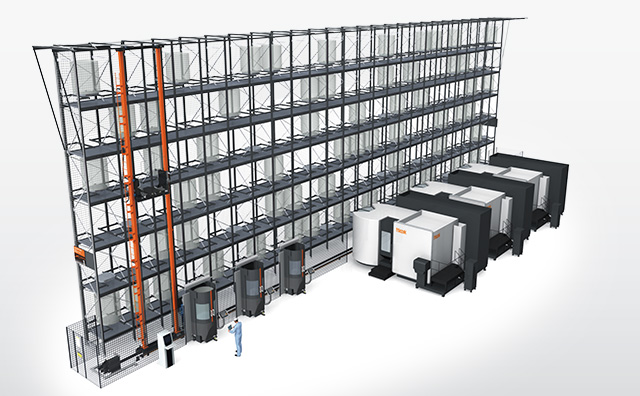
MPP(MULTI PALLET POOL)
Machining center Pallet transport type
Compact multi-level pallet stocker system
MPP (MULTI PALLET POOL) is a space-saving multi-stage pallet stocker system developed in response to the growing demand for automation. This automation system is ideal for small-lot, multi-product production and will dramatically improve productivity.
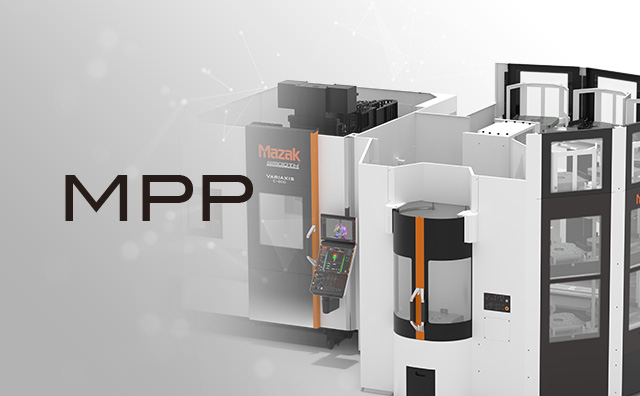
MPP 6PC, 12PC, 18PC type
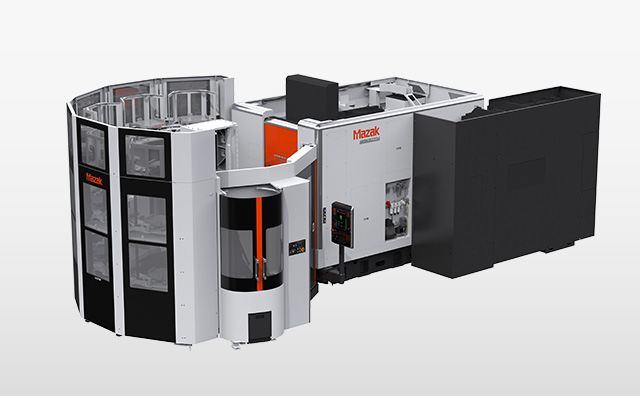
Minimum floor space requirements
Uses the same production system as Mazak's automation system (PALLETECH system) for reduced floor space.
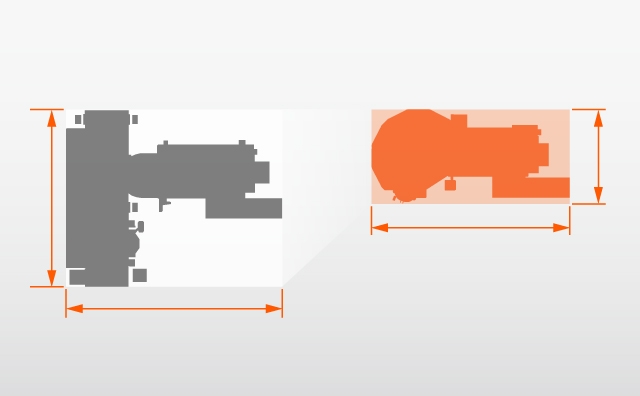
Expandable pallet stocker
6, 12 and 18 pallet storage capacities are available after initial machine installation.
- * |Only for VARIAXIS i series (excluding i-800NEO), MPP can be installed after delivery of the stand-alone machine. MPP installation preparation (single table) is required.
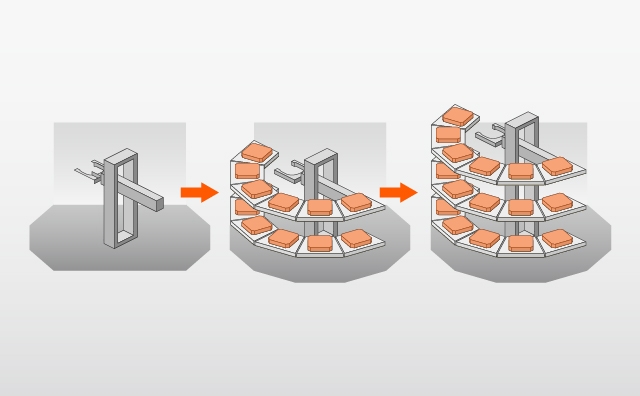
Transportable workpiece specifications
Model | Pallet size | Transport weight (Without pallet) | Maximum transport dimensions [diameter x height] (Without pallet) |
---|---|---|---|
VARIAXIS i-600 | 400 mm × 400 mm | 300 kg | Φ600 mm × 425 mm |
VARIAXIS i-700 NEO | 500 mm × 500 mm | 600 kg | Φ730 mm × 500 mm |
VARIAXIS i-700T | Φ610 mm | 600 kg | Φ730 mm × 500 mm |
VARIAXIS i-800 NEO | 500 mm × 500 mm | 700 kg | Φ730 mm × 500 mm |
VARIAXIS C-600 | 500 mm × 500 mm | 500 kg | Φ730 mm × 450 mm (C110)*1 |
HCR-5000S | 500 mm × 500 mm | 500 kg | Φ700 mm × 643.6 mm (R602)*2 |
- *1: |C110 mm with chamfering
- *2: |R602 mm with chamfering|
MPP 10PC, 16PC type
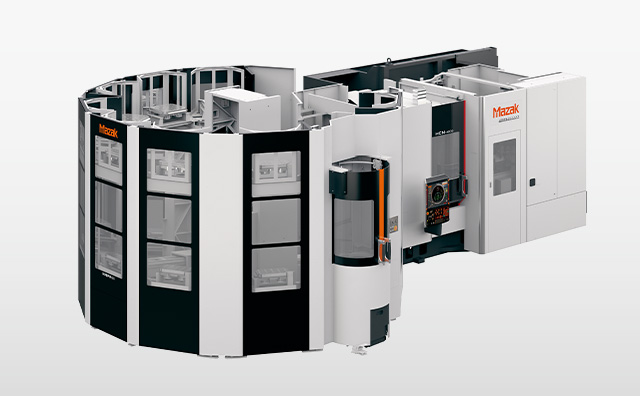
Minimum floor space requirements
Uses the same production system as Mazak's automation system (PALLETECH system) for reduced floor space.
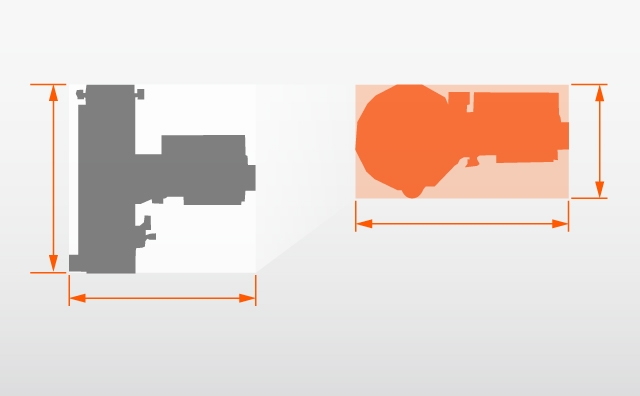
Expandable pallet stocker
10 and 16 pallet storage capacities are available after initial machine installation.
- * |MPP can be installed after delivery of single machines. 2PC or flexible manufacturing system preparation (optional) is required. The number of stockers is different from the standard specification and can be selected from 8 or 14 PC.
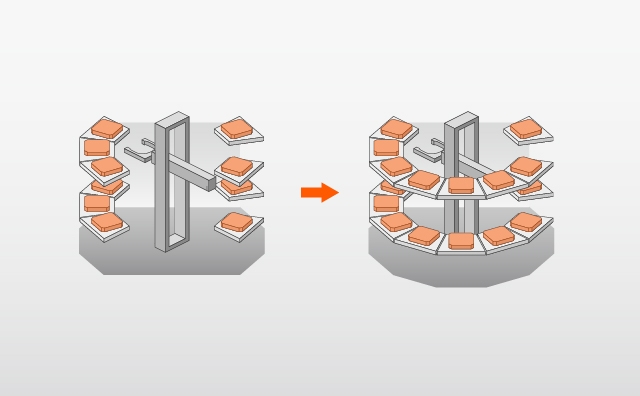
Smooth MPP is software that automatically operates and manages MPP.
You can create operation data, check schedule progress and operation status on the display screen of the machine's CNC operation panel. The use of a touch panel allows for intuitive operation. In addition, you can view the operation status on your office PC, tablet, or smartphone by connecting to the local internet.* *A Wi-Fi environment must be prepared by the customer.
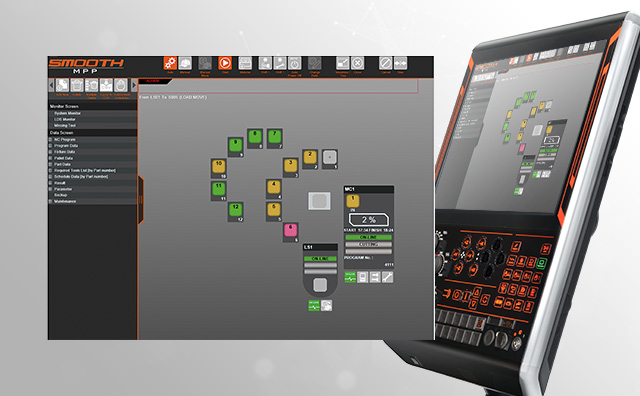
Understanding the situation at a glance
It visually displays the status of the system and process progress. This makes it easier to monitor system operation.
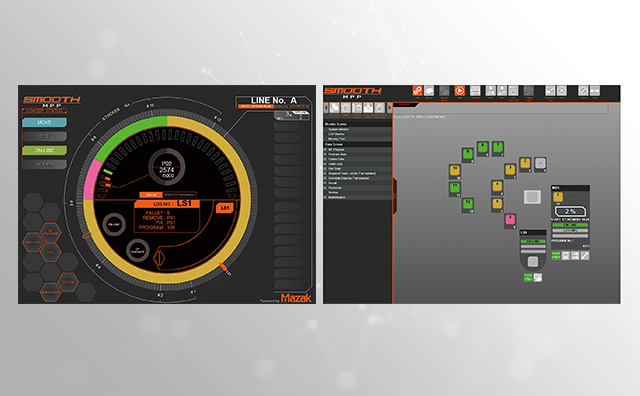
Display work instructions on time
The system supports the operator's work by displaying work instructions at the loading station and a screen that prompts the operator to prepare missing tools.
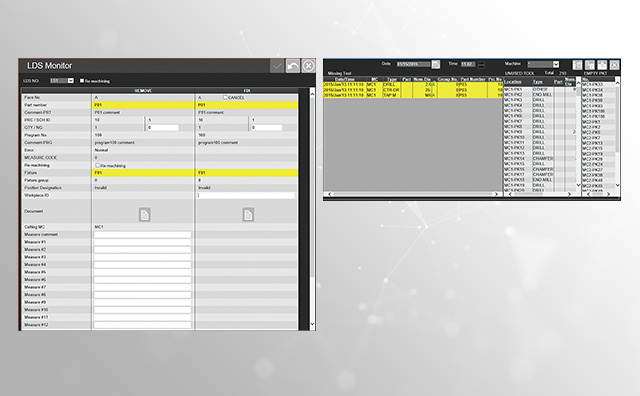
Various performance displays
Various performance data is output in a variety of graphs, making it easier for system administrators to analyze operations.
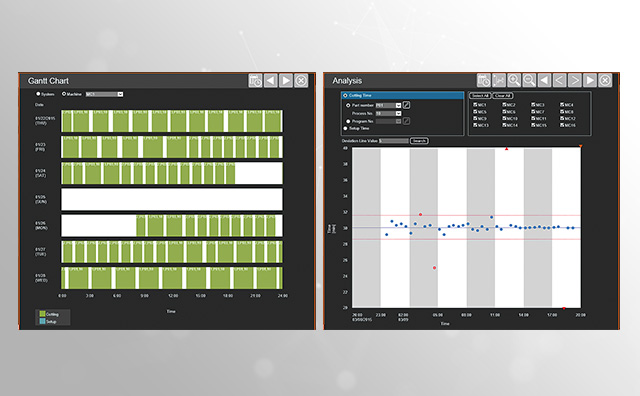