Dimensione autocentrante | 8″ |
Diametro max. di lavorazione | Φ 670 mm |
Lunghezza max. di lavorazione | 1011mm / 1519mm |
Macchine multitasking
INTEGREX AG
- L'integrazione di specifiche funzionalità per la lavorazione di ingranaggi, semplifica la lavorazione ad alta precisione, riducendo i tempi di lavorazione e i costi iniziali
- Sono integrati tre tipi di funzionalità di lavorazione ingranaggi, smussatura, dentatura con utensili dedicati e fresatura con frese convenzionali, per soddisfare diverse esigenze, dalla produzione a basso volume, produzioni diversificate fino a volumi maggiori
- I percorsi, le traiettorie utensili e le misurazioni possono essere generate facilmente e rapidamente tramite la pratica e intuitiva programmazione conversazionale MAZATROL, specificamente dedicata a questi processi
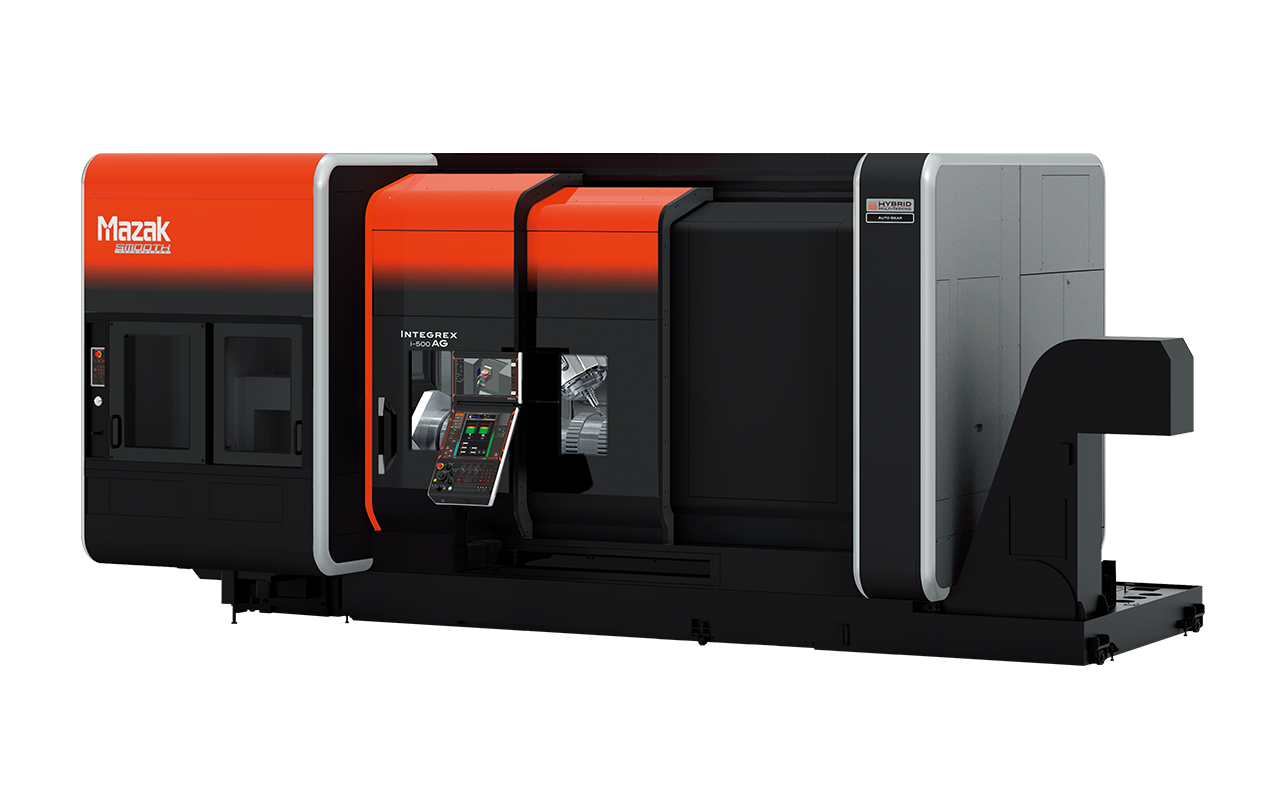
I vantaggi della serie INTEGREX con l'integrazione dei processi di lavorazione e misurazione ingranaggi
La serie INTEGREX AG è in grado di lavorare in modalità tornitura e fresatura fino ai 5 assi in continuo con l'integrazione della lavorazione e misurazione ingranaggi
In questa singola macchina sono integrate tre funzionalità, espressamente dedicate alla lavorazione ingranaggi: fresatura con utensili dedicati (tipo skiving, dentatura a creatore, fresatura con frese convenzionali, ecc.). Tutte le funzionalità disponibili, dalla fresatura con utensili dedicati a quella con frese convenzionali. È anche possibile misurare gli ingranaggi in process.
- 1: Lavorazione a 5 assi
- 2: Lavorazione dentatura in modalità “skiving”
- 3: Misurazione ingranaggi
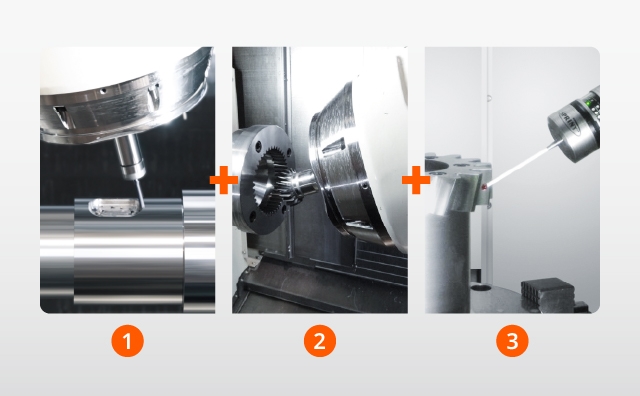
Produzione ingranaggi su macchina universale e non dedicata
Smussatura di ingranaggi
- Modalità skiving ad alta precisione con l'esclusiva tecnologia di controllo super preciso di INTEGREX AG.
- La precisione della sincronizzazione della rotazione tra il mandrino di tornitura e il mandrino di fresatura viene mantenuta anche alla massima velocità di rotazione di ciascun mandrino.
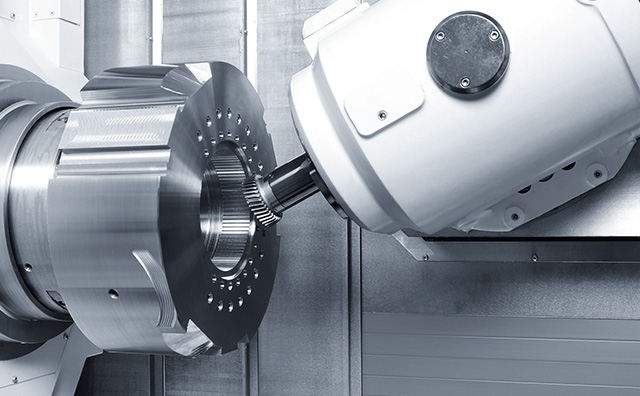
Dentatura
Semplicità di messa a punto per la modalità di fresatura a creatore attraverso “maschere” di programmazione semplificate. L'utensile a creatore supportato da un solo lato (attacco mandrino) garantisce precisioni di lavorazione di classe ISO 7. Software di supporto alla programmazione "Smooth Gear Hobbing" con maschere di interfaccia semplici ed intuitive. "Hob Shift" sposta il punto di lavorazione del creatore a ogni passata per prolungare la durata dell'utensile, mentre "Micro Geometry" modifica il punto in cui i denti degli ingranaggi si incontrano dopo la lavorazione.
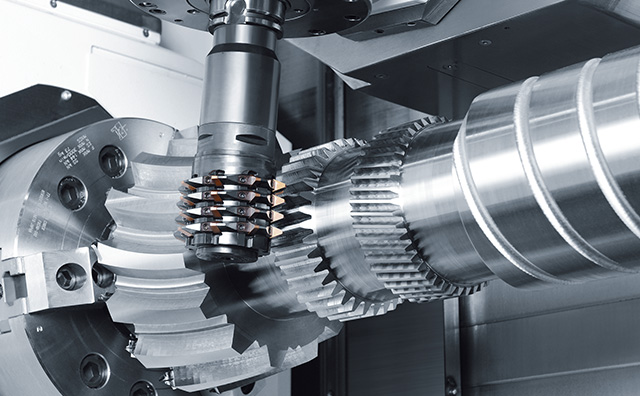
Modalità di fresatura dentature con frese convenzionali
È possibile utilizzare frese a codolo disponibili in commercio. Utilizzando il software dedicato "Smooth Gear Milling", i denti degli ingranaggi possono essere lavorati singolarmente con frese standard. La "Funzione di correzione del profilo del dente" e la "Funzione di correzione del passo del dente" consentono la migliore gestione della fresatura ingranaggi lavorati. Questa modalità garantisce una precisione di lavorazione di classe ISO 5 (ex classe JIS 1).
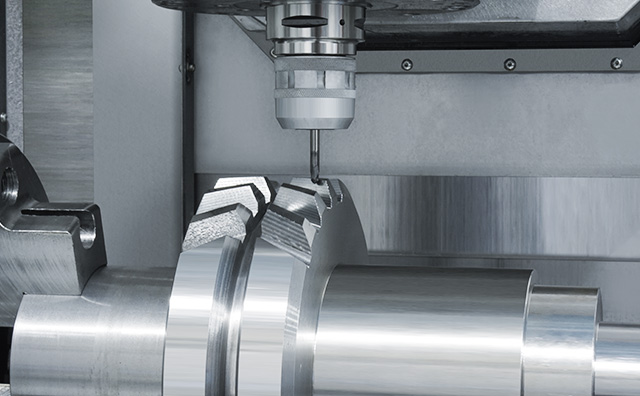
Riduzione dei tempi di lavorazione
Confronto tra la dentatura con una macchina multitasking convenzionale e la fresatura frontale con una INTEGREX in versione AG
Nel caso di lavorazioni meccaniche di pezzi destinati a produzioni di grandi quantitativi e bassi volumi, utensili speciali come i creatori, richiedono molto tempo di approvvigionamento per preparare gli utensili e le attrezzature. INTEGREX AG è in grado di lavorare un'ampia gamma di ingranaggi con frese convenzionali comunemente in commercio, riducendo così notevolmente i tempi e costi di produzione.
1: Preparazione utensili e prese pezzo
2: Programmazione
3: Lavorazione ingranaggi
4: Lavorazione
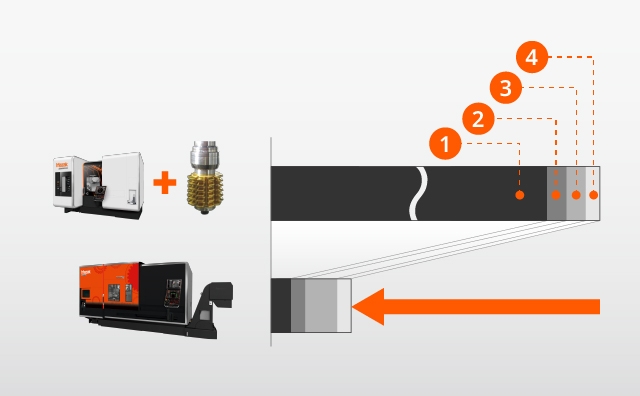
Posizione angolare e fasatura denti ingranaggio per il posizionamento in fase di messa a punto
Fasatura e posizionamento radiale ingranaggio
Dopo la dentatura (in skiving o a creatore), viene identificato centro angolare della scanalatura del dente ingranaggio. Sulla base degli angoli di fasatura identificati, la macchina può automaticamente eseguire tutte le altre lavorazione previsto fasate tra di loro. Il centro angolare della scanalatura dente dell'ingranaggio, viene identificato sulla superficie terminale o sul cerchio della punta durante la determinazione della presenza o dell'assenza di denti. La precisione effettiva dell'identificazione è di 0,005° (16 μm su un cerchio di 360mm di diametro). La posizione della sonda e la direzione di avanzamento della sonda senza interferenze possono essere impostate in base alla forma del pezzo di destinazione e ai punti di contatto dello stilo.
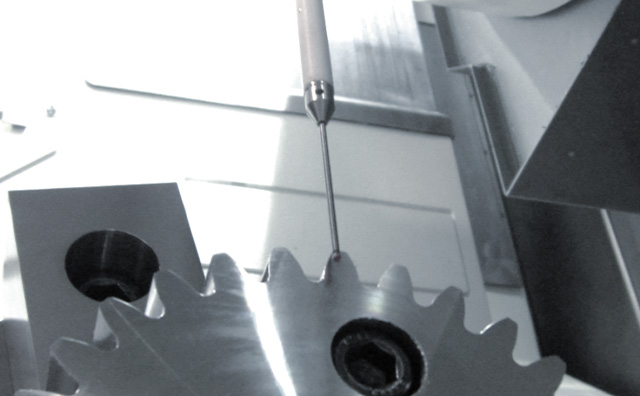
La scansione continua della superficie degli ingranaggi è disponibile come opzione. Visualizzare la superficie lavorata dell'ingranaggio misurandone il profilo e il passo.
Misurazione del profilo e del passo dell'ingranaggio*
Il profilo e il passo degli ingranaggi vengono misurati in process con la sonda a scansione dopo la lavorazione.
Netta riduzione dei processi necessari tra il pezzo lavorato e la macchina di misura 3D per l'ispezione e poi riportarlo su INTEGREX per ulteriori lavorazioni.
I risultati della misurazione vengono visualizzati sul display MAZATROL SmoothAi ed è possibile osservare la superficie dei denti degli ingranaggi.
*Opzione
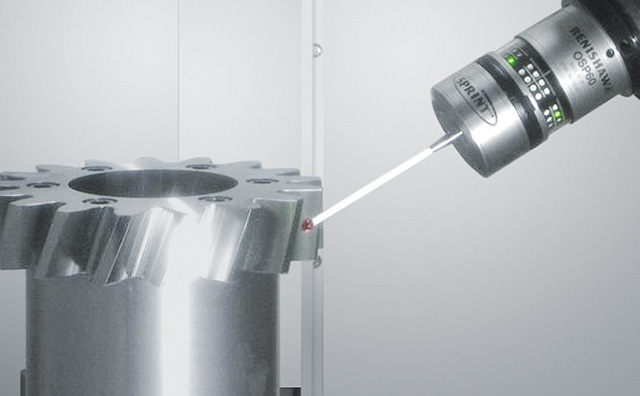
Misurazione della superficie dei denti degli ingranaggi con sonda a scansione
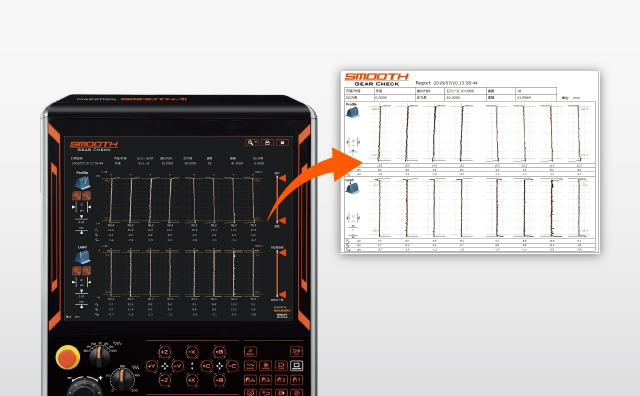
CNC MAZATROL SmoothAi visualizza i risultati delle misurazioni
I risultati delle misurazioni sul display CNC possono essere visualizzati come immagine (file PNG) con un solo tocco
Programmazione conversazionale per il taglio e la misurazione di ingranaggi ad alta precisione
I programmi vengono creati in modo semplice e rapido, semplicemente impostando i vari parametri e le velocità di avanzamento indicati nei disegni, visualizzando al contempo la guida grafica. Questo software di supporto crea programmi G-code dedicati e genera automaticamente percorsi di lavorazione e misurazione. Il taglio e la misurazione degli ingranaggi vengono eseguiti premendo il pulsante di avvio del ciclo.
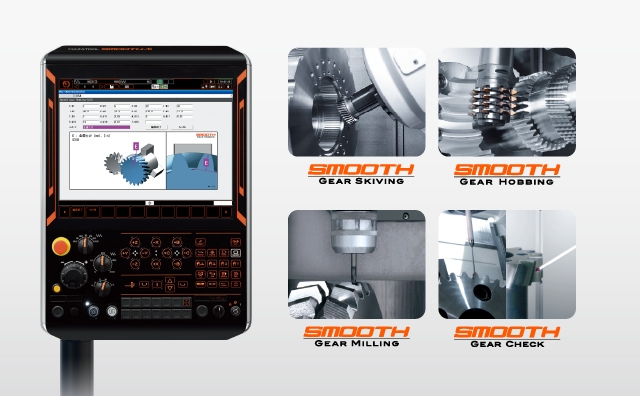