Table size | 4000 mm × 1250 mm |
Max. spindle speed | 26000 mm-1 (rpm) |
Max. workpiece dimension | 4000 mm × 1600 mm × 500 mm |
Spindle output | 45 kW (cont. rating) |
5-Axis Machining Centers
VORTEX HORIZONTAL PROFILER
- Box construction integrating the base, column, and table and thermally symmetrical spindle / column construction ensures high accuracy machining.
- Powerful, high speed built-in motor spindle for high productivity
- 90° table tilt system for easy setup and changeover
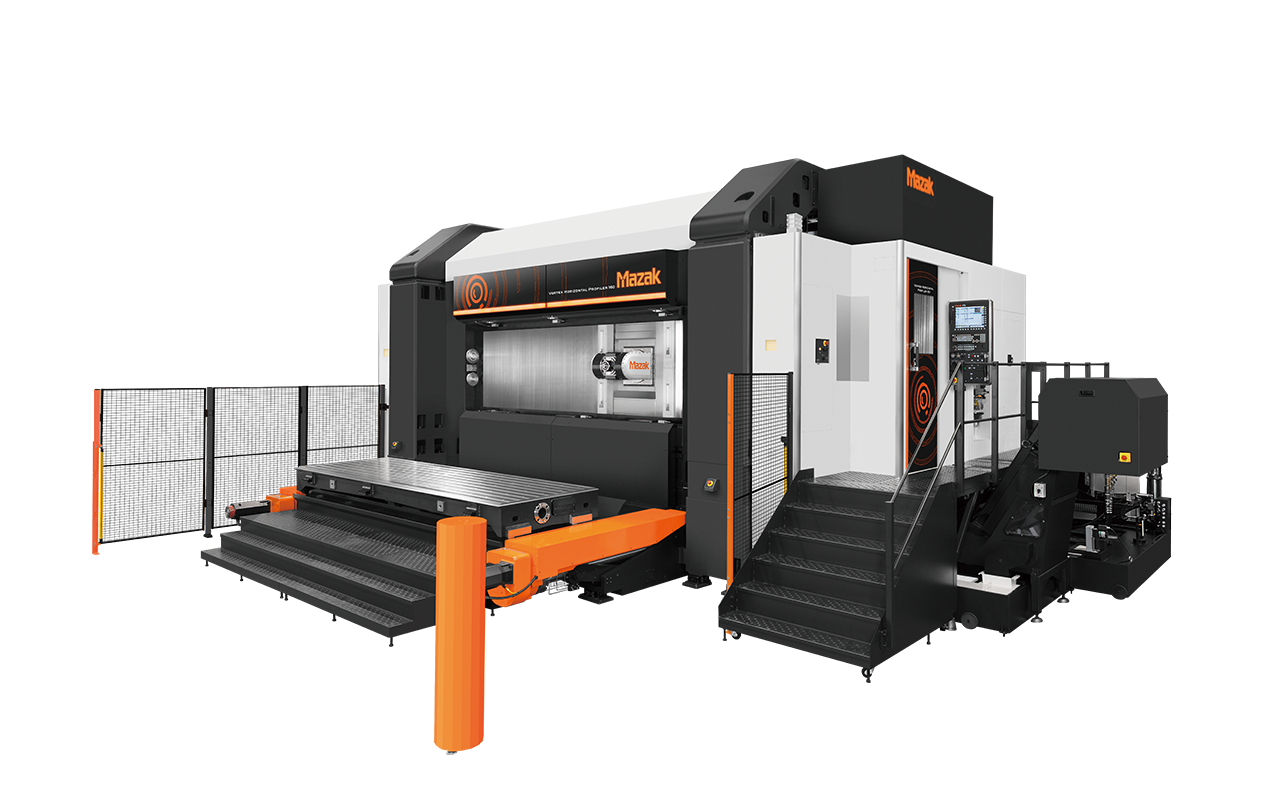
Applications
With a 4000 mm × 1250 mm wide table that has a maximum loading weight of 3000 kg, this machine is ideal for machining applications for aircrafts, especially structural components of wing systems such as wing ribs.
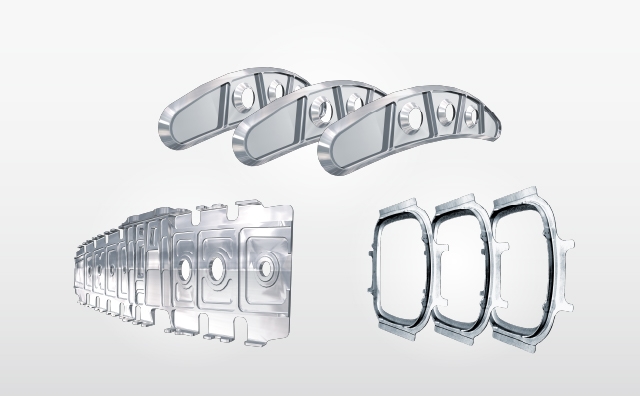
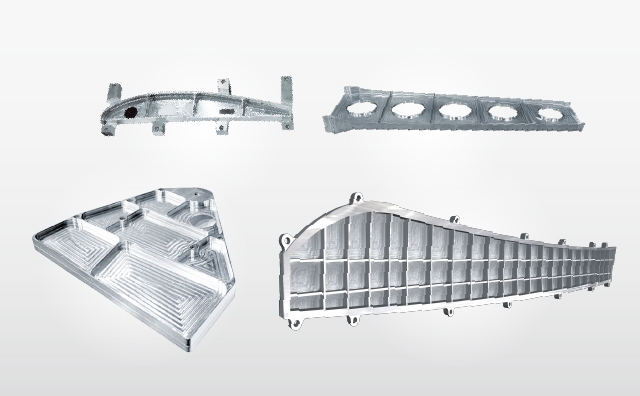
Designed for high speed, high accuracy simultaneous 5-axis machining
Machine construction ensures stable machining accuracy in the X-axis direction from the bottom to top of the machine table
The large table capacity allows the machining of large right- and left-hand components in the same machine setup.
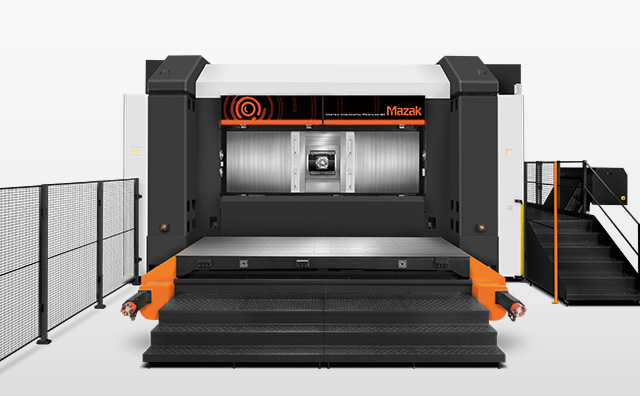
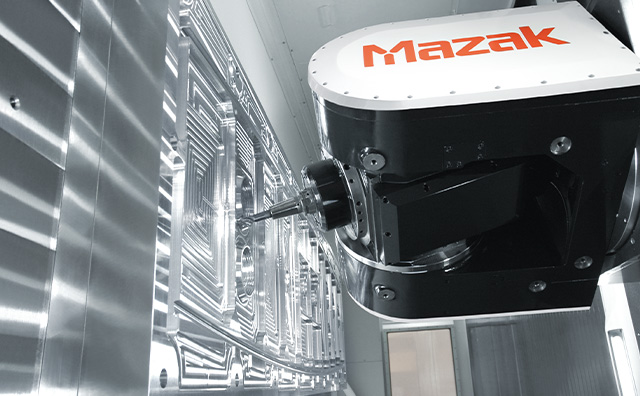
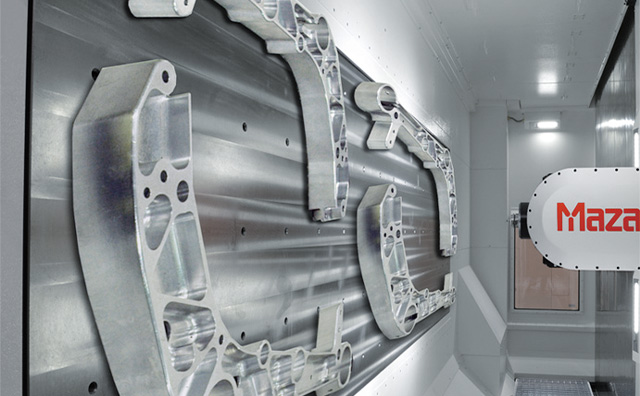
Box construction integrating the base, column, and table
Fully closed force loop construction and integrated robust table provides exceptional rigidity to ensure stable high machining accuracy.
Tilting table for large workpieces
For convenient workpiece loading / unloading, the table is horizontal for workpiece setup and tilted 90 degrees for machining.
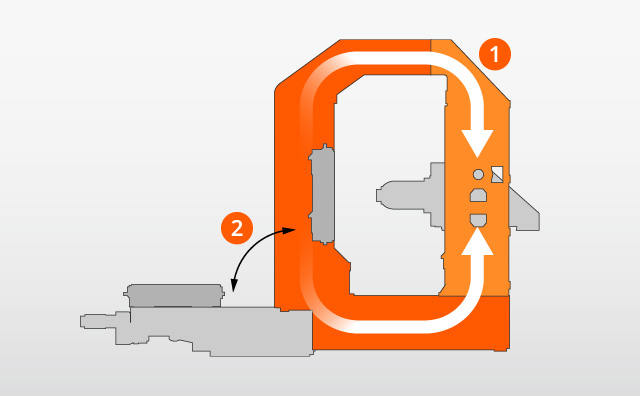
Thermally symmetrical spindle / column
Different from unstable cantilever construction, the thermally symmetrical spindle / column holds the headstock on both the right and left sides to maintain consistent high machining accuracy.
High accuracy table positioning
Tilting table repetition accuracy repeatability is within 13 μm (X / Y / Z directions).
High speed, high output spindle for high efficiency machining of aluminum components
30000 min -1 120 kW built-in motor spindle
The built-in motor spindle design helps minimize vibration during high speed operation. This ensures exceptional surface finishes and maximum tool life.
Standard spindle
Output (Cont. rating): 120 kW
Torque (Cont. rating): 42.4 N・m
High torque spindle (option)
Output (Cont. rating): 120 kW
Torque (Cont. rating): 83 N・m
Optional only for VORTEX HORIZONTAL PROFILER 160 XP.
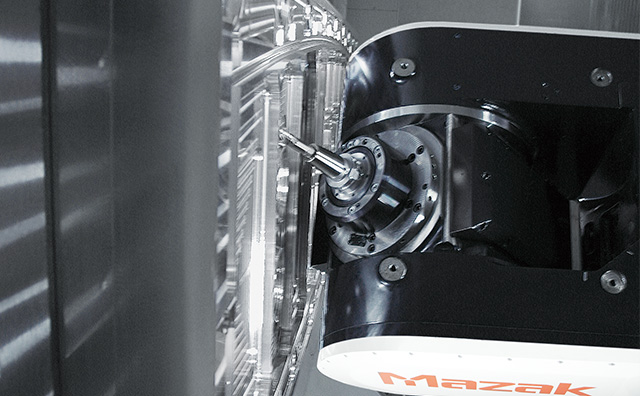
Advanced coolant / chip disposal technology
1.5 MPa (218 PSI) high-pressure coolant through spindle (standard)
High-pressure coolant through the spindle is supplied though tool passages directly to the tip of the cutting tool.
Higher-pressure coolant systems (3.5 MPa (508 PSI) / 7.0 MPa (1015 PSI)) are optionally available.
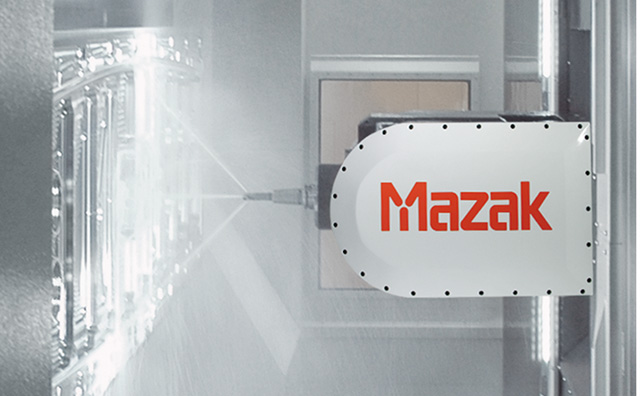
Headstock cleaning coolant (standard)
The standard coolant nozzles on the top cover remove chips from the headstock during machining.
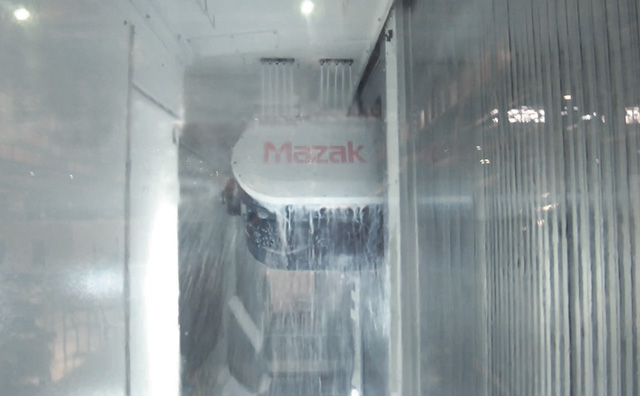
2 table changer and large capacity tool magazine long-hour automatic operation
The compact, rotary type 2 table changer makes it possible to set up the next workpiece during machining. It will be of support for long-hour automated operations.
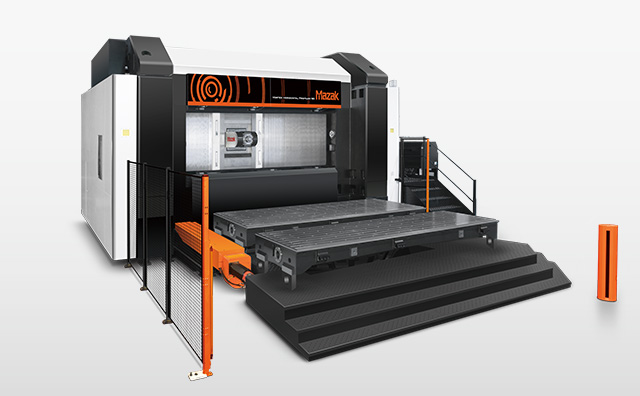
Environmentally friendly
Clean Coolant System
The internal wall surfaces of the large volume coolant tank have a coating that prevents small machined chips from adhering. The coolant tank has a coolant jet that makes a vortex in the center so that small machined chips will not settle in the tank. These features allow the coolant to be smoothly sent to the coolant filter, where more than 98% of particles larger than 10 μm (0.00039”) are removed by the dedicated cyclone filter. In addition, the maintenance-free structure significantly reduces the time required to clean filters and tanks.
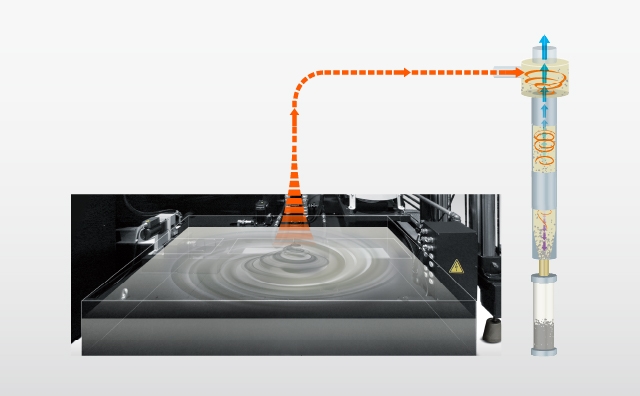
Coolant tank separated from conveyor
The tank and conveyor are separated and arranged in an upper and lower position to discharge chips more quickly while reducing the amount of coolant carried out by the conveyor. Tanks can be easily moved and maintained.
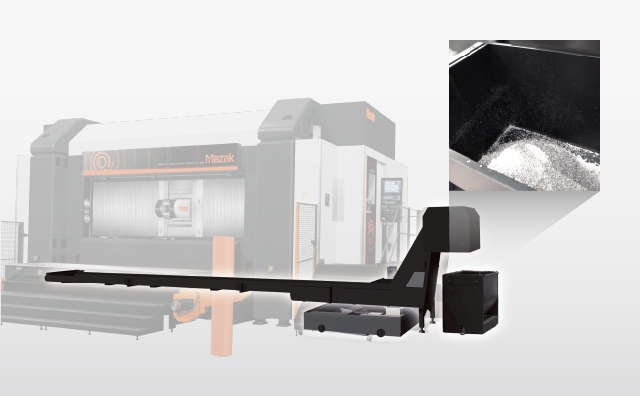