Pallet size | 800 mm × 800 mm |
Tool shank (standard) | BT50 |
Max. spindle speed | 10000 min-1 (rpm) |
Max. workpiece size | Φ1450 mm × 1450 mm |
Horizontal Machining Centers
μ
- High productivity and high-accuracy machining
- High power spindle for optimal cutting conditions in various parts machining
- High-speed operation for class-leading productivity
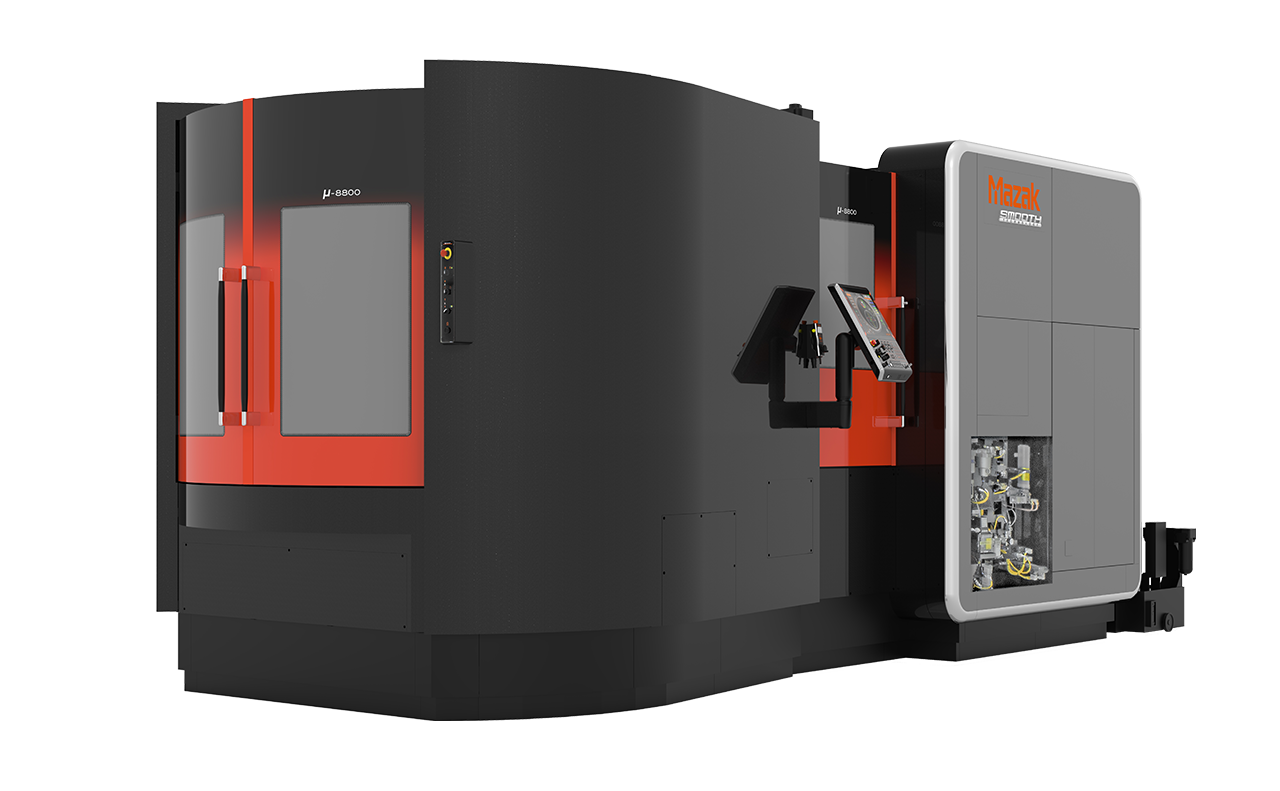
High-rigidity, high-accuracy structure, and complete temperature control system
Ultra high positioning accuracy of 1/8 of the ISO machining centers inspection standard over extended periods of operation
High-rigidity and high-accuracy positioning structure designed with the latest technology
Thorough machine temperature control enables stable, high-accuracy machining.
Thermal displacement prevention
Column cooling system
Base cooling system
Ball screw core cooling system
Coolant temperature control system
Head stock cooling system
High-accuracy structure
High-precision Scale feedback
High-accuracy positioning
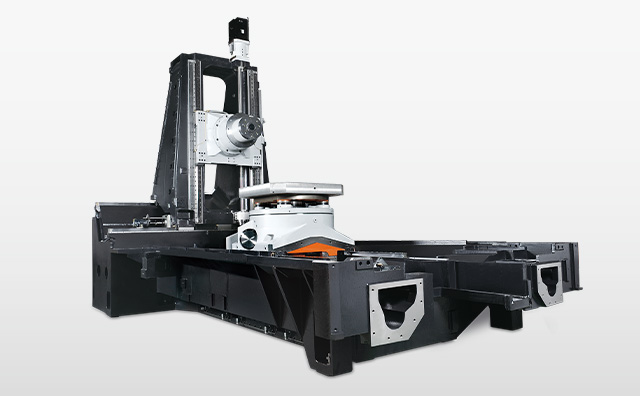
High productivity
The spindle has high power, high torque, and high rigidity. With spindle output of 44.4 kW (1 min. rating) and maximum torque of 586 N・m, the powerful high-speed performance enables heavy cutting during rough machining of iron, cast metal, and aluminum, and also high-speed, high-accuracy machining during finish machining.
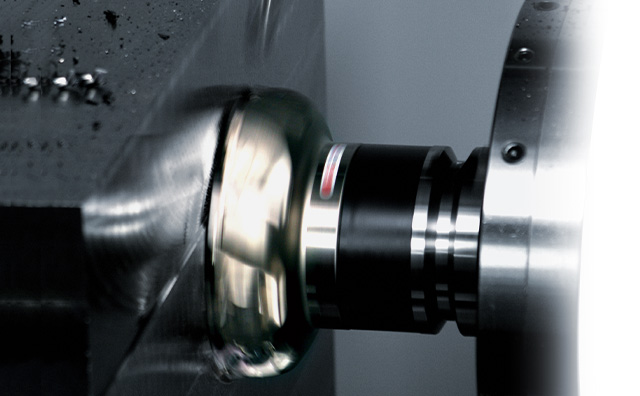
Fastest feed speed and largest axis stroke in its class
By utilizing roller linear guides on all axes, high-accuracy machining is ensured even at high-speed federates. Additionally, fast, vibration free acceleration / deceleration are realized thanks to the smooth high-gain servo control and high-power AC servo motors.
Rapid traverse rate (X-, Y-, Z-axis)
60 m/min : μ-8800
52 m/min : μ-10800
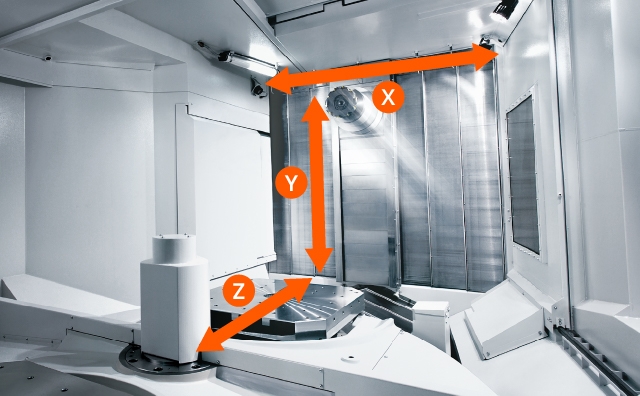
High-speed indexing of large, heavy workpieces
Enables quick table indexing when loading large, heavy workpieces to improve productivity by reducing non-cutting time. The μ-8800 comes standard with a 1° x 360 index table. μ-10800 is equipped with an NC rotary table (with high-accuracy scale) as standard.
μ-8800 | μ-10800 | |
1: Max. workpiece diameter | Φ1450 mm | Φ2050 mm |
2: Max. workpiece height | 1450 mm | 1600 mm |
Weight | 2200 kg | 3000 kg |
Table indexing time (90°) | 3.2 sec / 1.7 sec*. | 2.4 sec |
*NC rotary table (option)
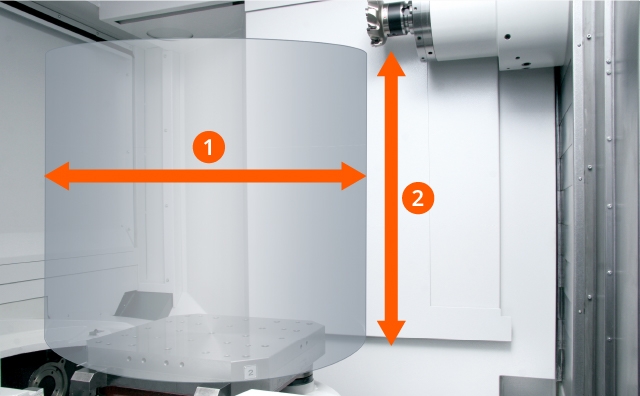
Support for high-speed and high-accuracy machining
Smooth Machining Configuration
Machining time, finished surface smoothness and machining shape can be adjusted for improved productivity.
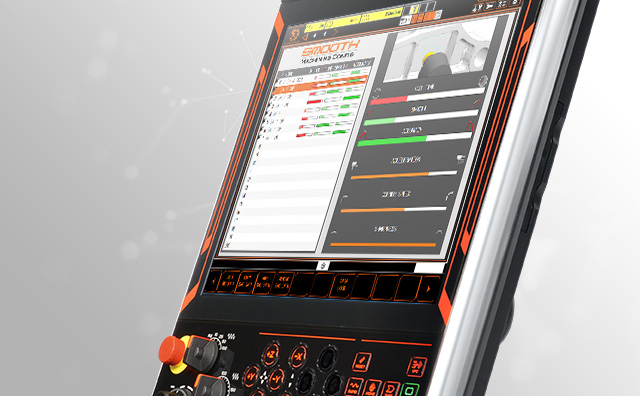
Heat Displacement Control - THERMAL SHIELD
THERMAL SHIELD is an automatic compensation system for room temperature changes, which realizes enhanced continuous machining accuracy. MAZAK has performed extensive testing in a variety of environments in a temperature controlled room and has used the results to develop a control system that automatically compensates for temperature changes in the machining area. Stable machining accuracy can be obtained over a long period of time without difficulty in countermeasures against thermal displacement. Temperature and compensation is displayed on screen. Operator can adjust compensation while looking at the data.
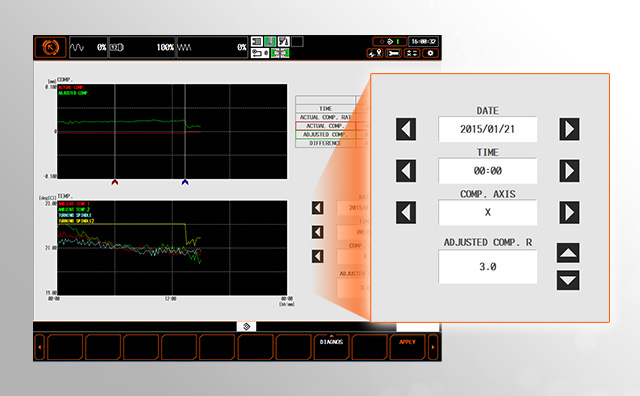
Various types of automation from stand-alone machines to systems
2-pallet changer
Rotary-type pallet changers quickly change pallets with heavy workpieces for higher productivity.
Robot integration
Interface for connecting an external robot for workpiece loading / unloading to / from automatic hydraulic fixtures is optionally available.
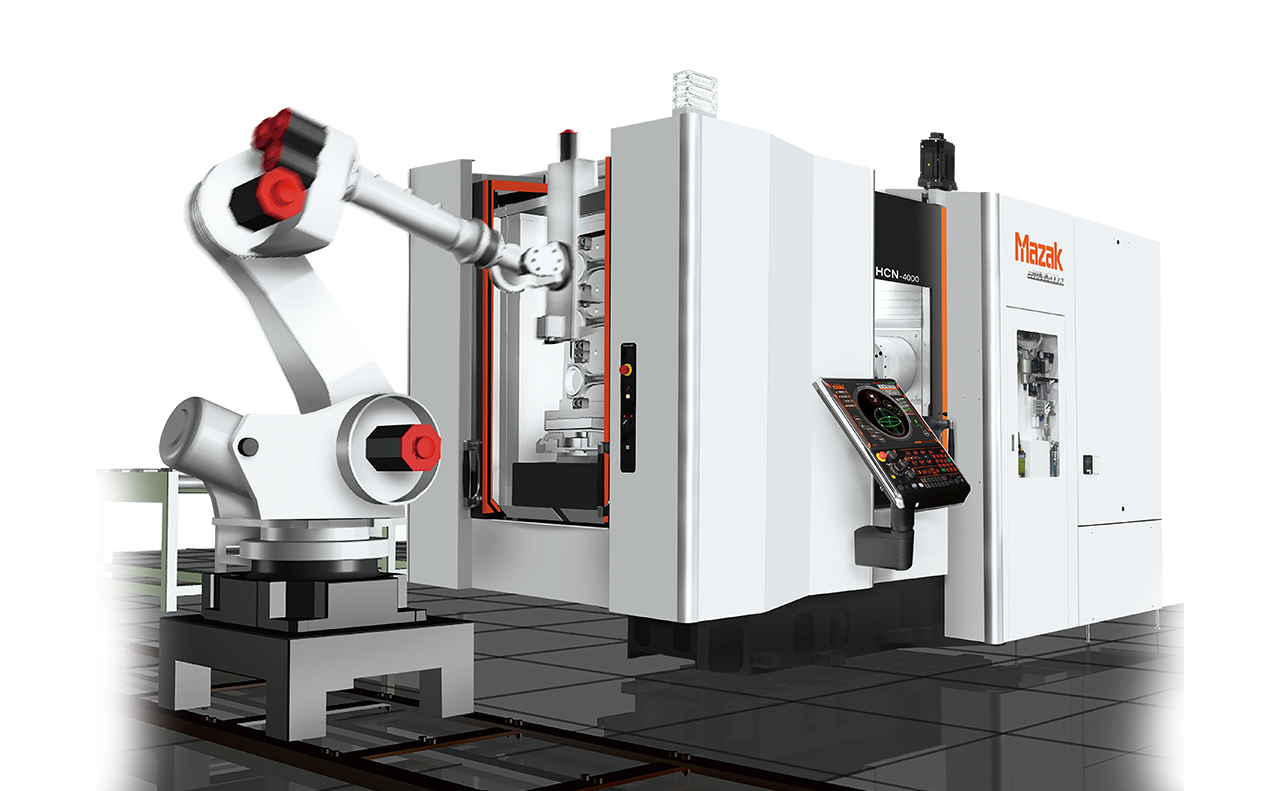
PALLETECH SYSTEM*
Automated system best suited for multi-product machining, supporting the mixing of different types of machine. As a modular design, the system can be expanded flexibly according to production conditions.
* Option
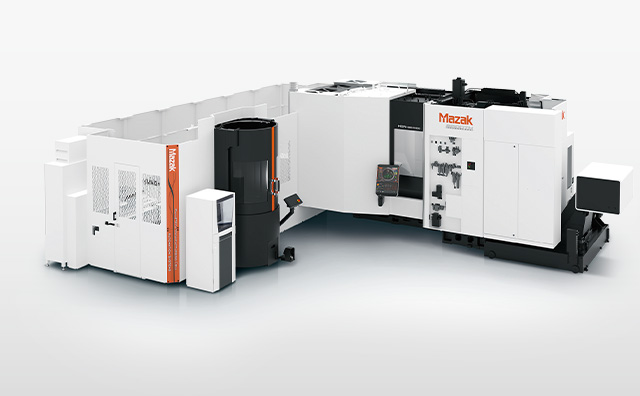
Hydraulic fixtures*
Type A (supply from machine top, maximum : 8 ports)
By hydraulic hoses, hydraulic power is supplied from the top part of the pallet changer to fixtures mounted on each pallet.
Preparation of hydraulic fixtures
Preparation specifications are available for easy changeover to hydraulic fixtures specifications (supply from the top) after installation.
* μ-8800 option
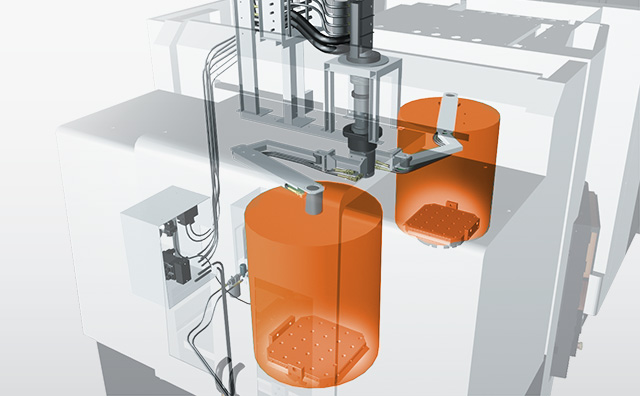