Chuck size | 12" |
Max. machining diameter | Φ580 |
Max. machining length | 2080 mm / 2985 mm |
CNC Turning Centers
TURNING CENTER M-5
- Excellent chip removal mechanism, high-rigidity bed construction
- High rigidity spindle structure, ideal for large diameter workpieces of difficult machining material.
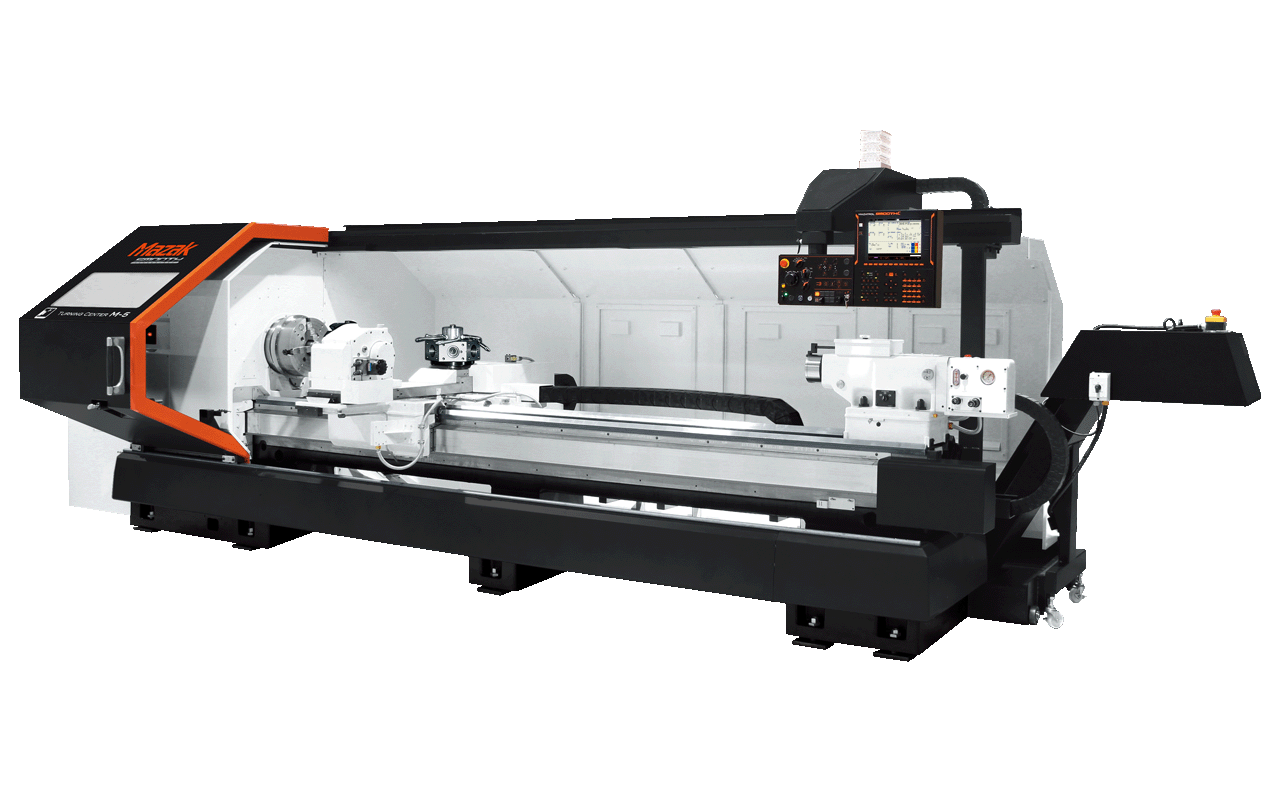
Designed for high productivity and reliability
Excellent chip removal mechanism, high-rigidity bed construction
The bed has sand sealed within its double-walled box-type structure, and has excellent vibration absorption. This improves stability during cutting along with dynamic stiffness of the bed. The M-5's precision-ground V-shaped slide ways undergo a special induction hardening process developed by Mazak (over HS 70).
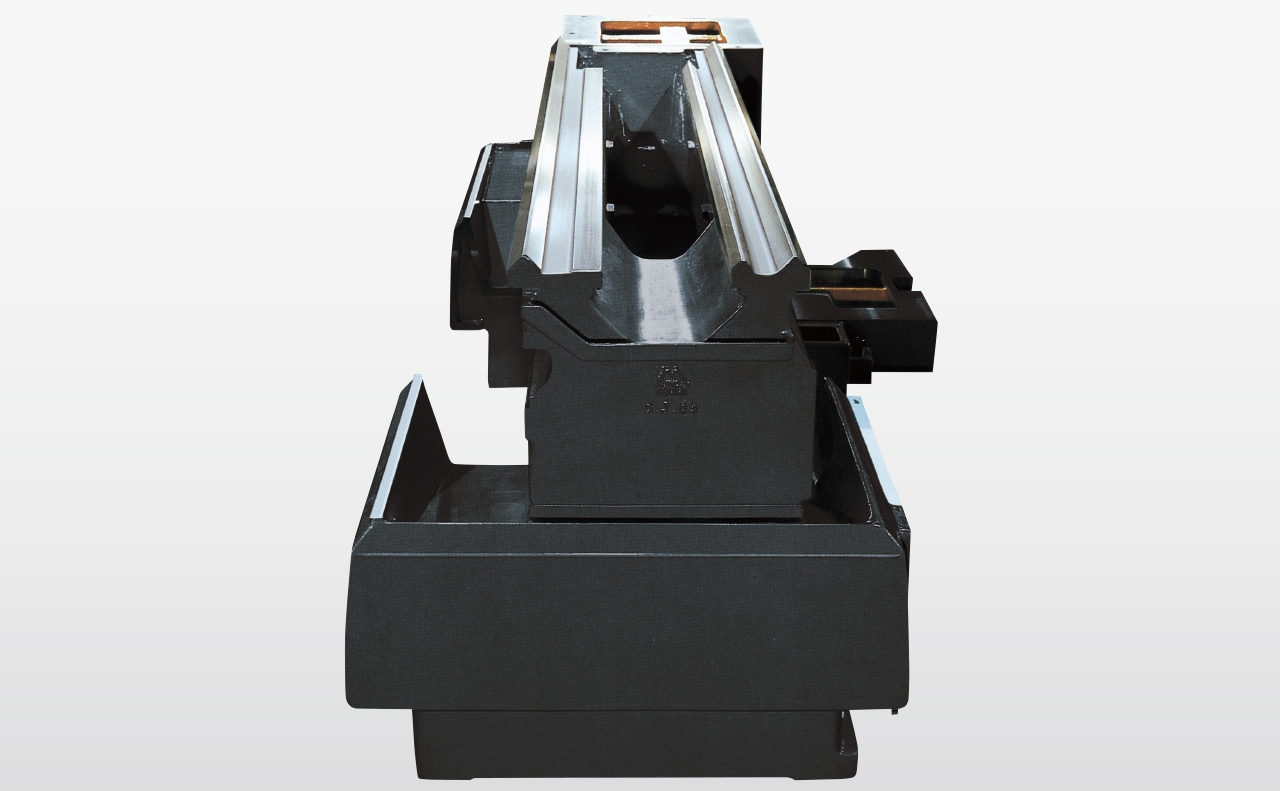
High power / rigidity spindle
Ideal for large diameter workpieces of difficult machining material.
With a spindle speed range from 6 to 2200 min-1, and full power available between 178 to 2200 min-1 by a 3 speed hydraulic gear shift system.
Large spindle bore for shaft workpieces
The spindle has high rigidity due to it being supported by precision bearing, and the diameter of the spindle bore is Φ104 mm, which is favorable for turning. The Φ181 mm spindle bore option is very effective for machining large diameter workpieces in the spindle.
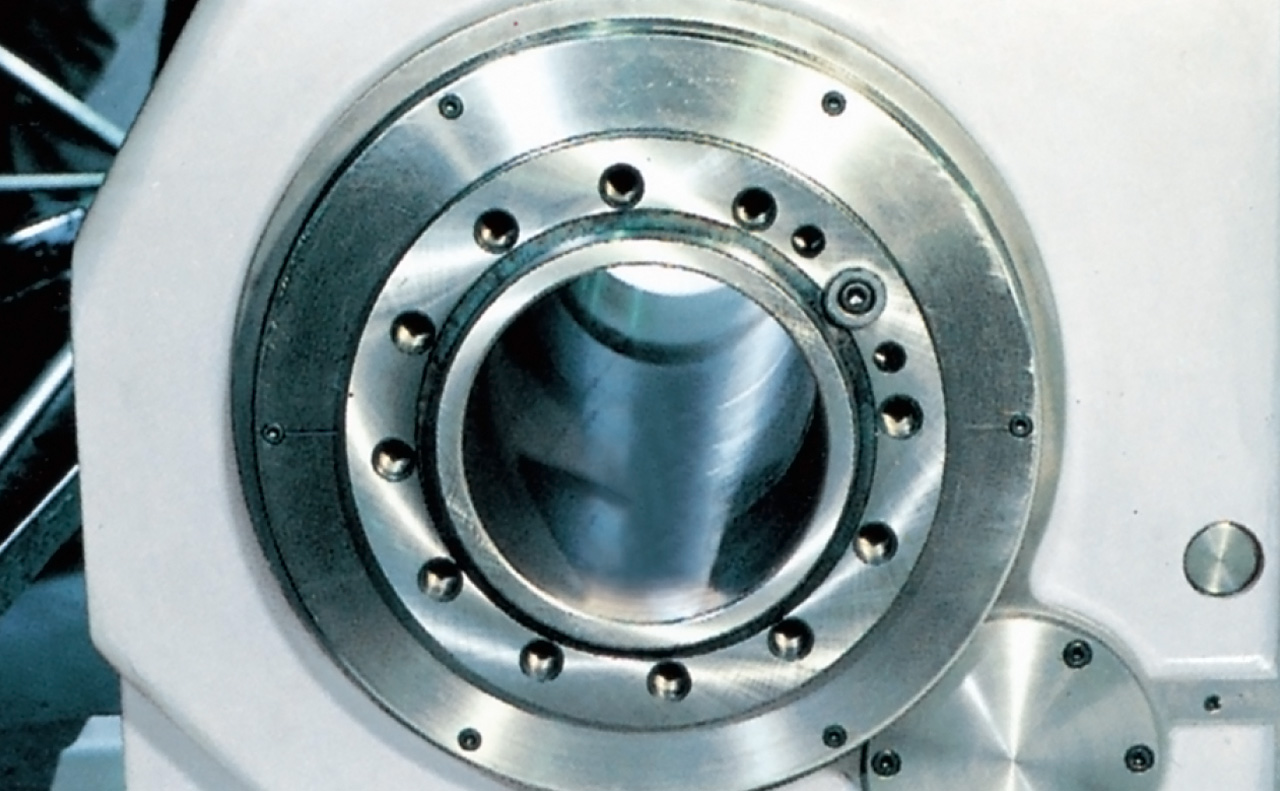
Unique turret structure
Reduced setup time
Allow 14 permanently set tools to minimize setup time.
High precision, heavy duty cutting is available thanks to large diameter couplings and high turret clamping force (front octagonal disc turret coupling : 252 mm, 44600 N / 4550 kgf ; rear hexagonal boring turret coupling : 230 mm, 40200 N / 4100 kgf).
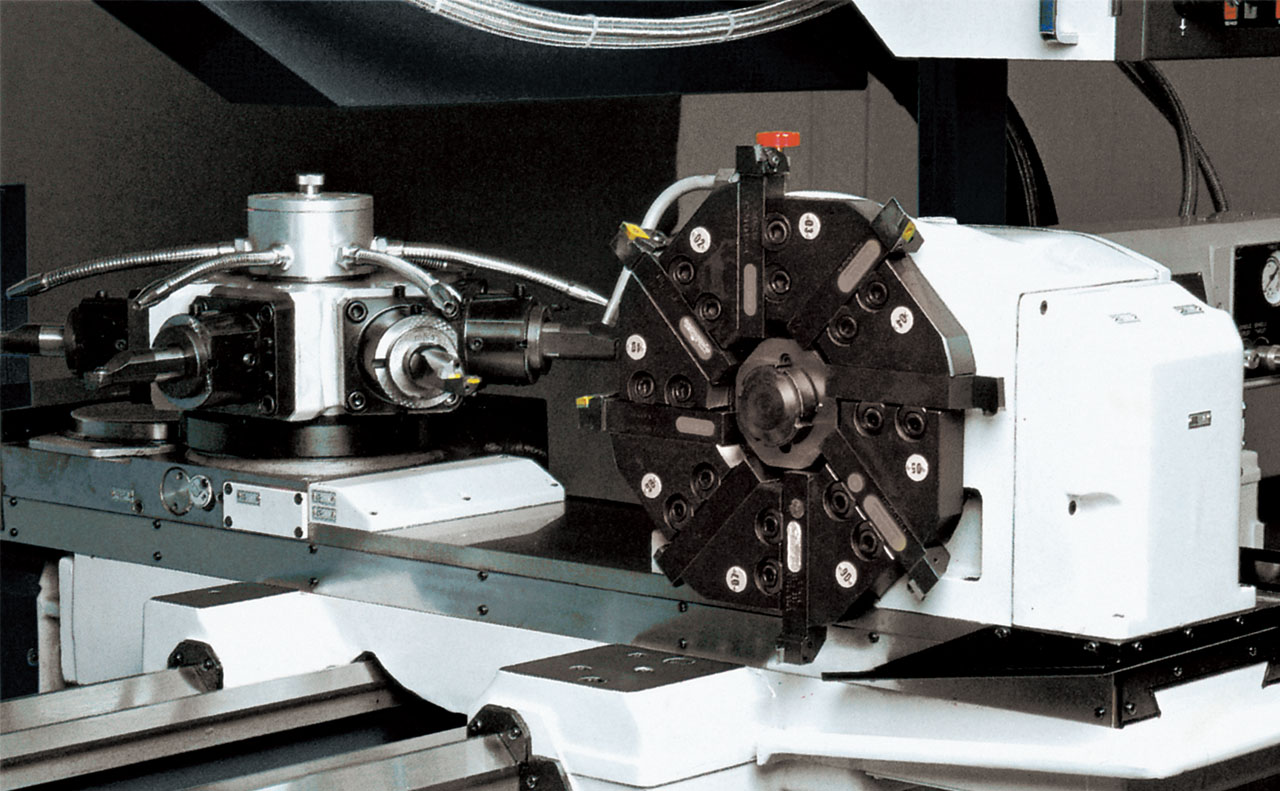
Heavy duty hydraulic tailstock
Large sleeve diameter and wide base structure ideal for heavy cutting.
The tailstock's large 100 mm diameter quill and wide base, together with its maximum thrust of 14700 N (1500 kgf) and bed clamping force of 78400 N (8000 kgf), make it ideal for heavy duty cutting.
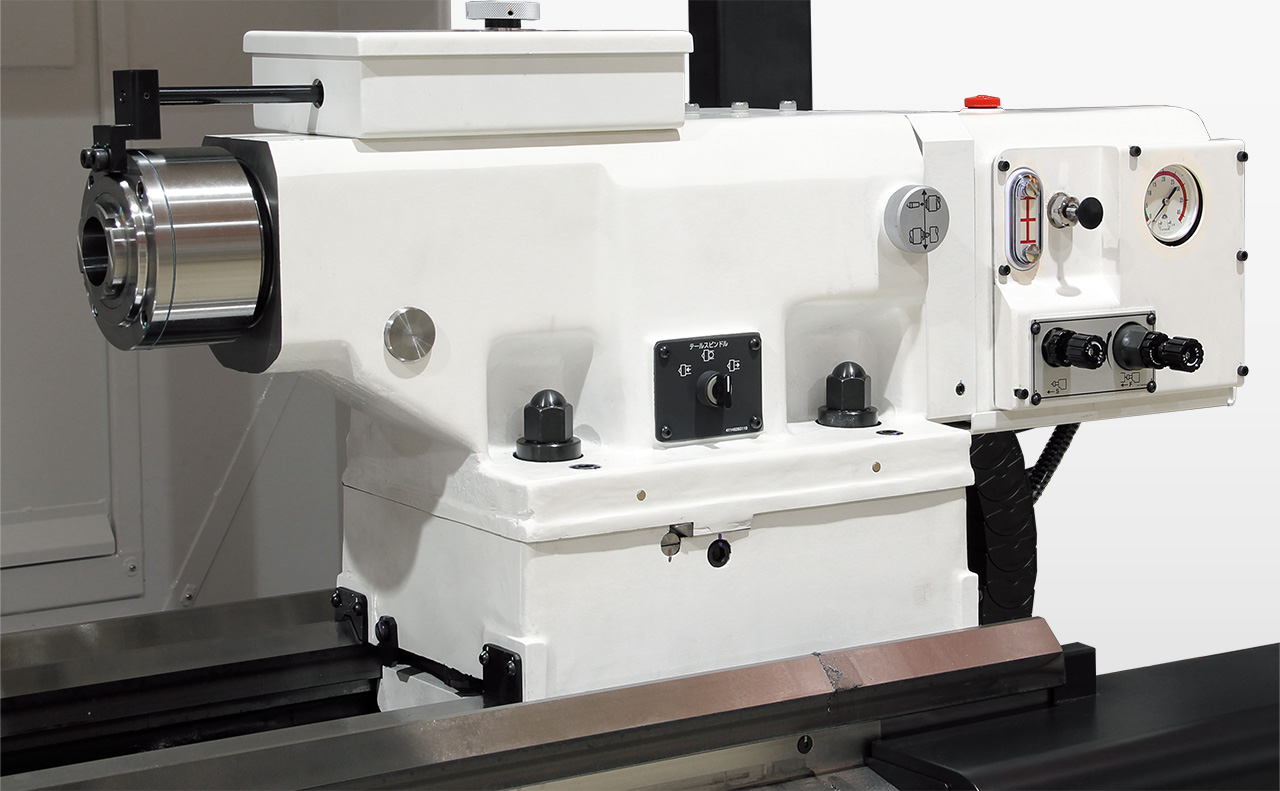
Ease of programming by MAZATROL conversational programming
75 % reduction of setup time for the first workpiece
Setup of the first workpiece from programming to tool path check, tool setup, and work coordinate setup can be conducted in a very short period of time.
Compared with other CNC systems, setup of the first workpiece can be reduced by as much as 75 %.