Chuck size | 6″ |
Max. machining diameter | Φ340 |
Max. machining length | 385mm |
Multi-Tasking Machines
INTEGREX i-150
- Small floor space requirement with exceptional processing versatility
- Long Y-axis stroke
- Versatile machining and automation with tailstock center and work handling system
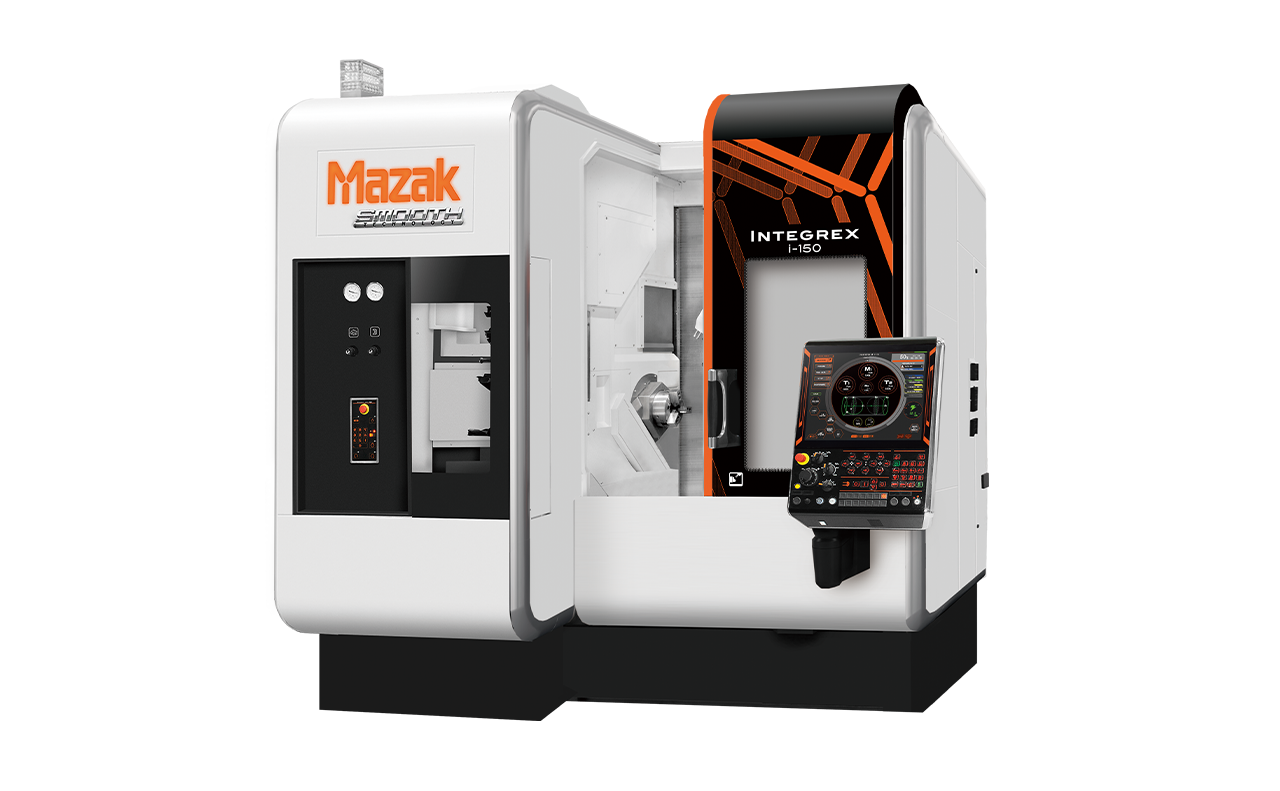
Small floor space requirement with exceptional processing versatility
Compact machine with large machining area
The INTEGREX i-150 is designed with a bar work capacity of Φ65 mm, equivalent to that of a higher class machine, while providing more compact floor space than similar machines with a 6" or 8" chuck with a second spindle. The INTEGREX i-150 is ideal for customers who mainly process small square workpieces and have trouble with floor space.
Automated system best suited for multi-product processing
Continuous OP1 and OP2 machining thanks to work handling system
The machine is equipped with work handling system and tailstock unit.
By reversing the workpiece at the unit, continuous OP1 and OP2 machining can be performed.

Machine construction for high-accuracy machining
Long Y-axis stroke
A generous Y-axis stroke of ±100 mm is achieved by using the proven orthogonal Y-axis structure. This provides a wide range of machining.
High-accuracy B-axis positioning
The B-axis is driven by a roller gear cam with no backlash, which can be indexed and positioned in 0.0001 degree increments.
Closed-loop control with scale feedback system is standard equipment. In addition, Mazak's unique clamping brake system ensures secure positioning and indexing. This ensures stable and high-accuracy positioning for extended periods.
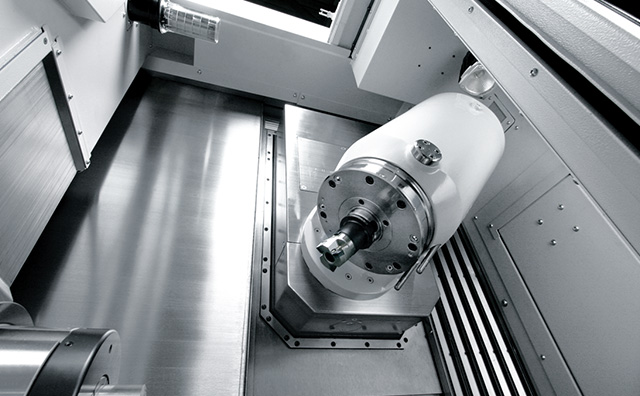
Heat countermeasures for turning spindle and milling spindle
The chiller unit circulates temperature-controlled oil through the spindle and built-in motor housing to reduce elongation and achieve high-accuracy machining.
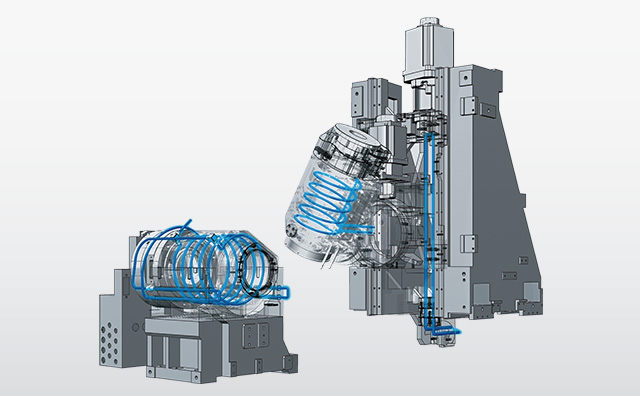
Heat displacement control - Thermal Shield
Room temperature changes and spindle heat generation have a significant impact on machining accuracy.
The Thermal Shield suppresses changes in cutting edge position based on spindle rotation speed and temperature sensor information, ensuring stable precision in continuous machining through precise machine control.
Temperature and compensation information are recorded and displayed on the screen of the CNC system. Operator can adjust compensation while looking at the data.
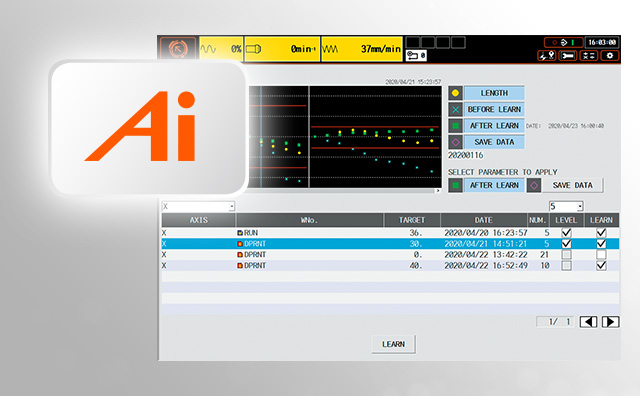