Pallet size | 500 mm × 500 mm |
Tool shank (standard) | BT40 |
Max. spindle speed | 12000 min-1 (rpm) |
Max. workpiece size | Φ700 mm × 643 mm |
5-Axis Machining Centers
HCR
- High-speed axial acceleration / deceleration
- Unique tilting rotary table
- Large capacity coolant system and machine structure ensure smooth chip disposal
- Spindle specifications available to meet a variety of production requirements
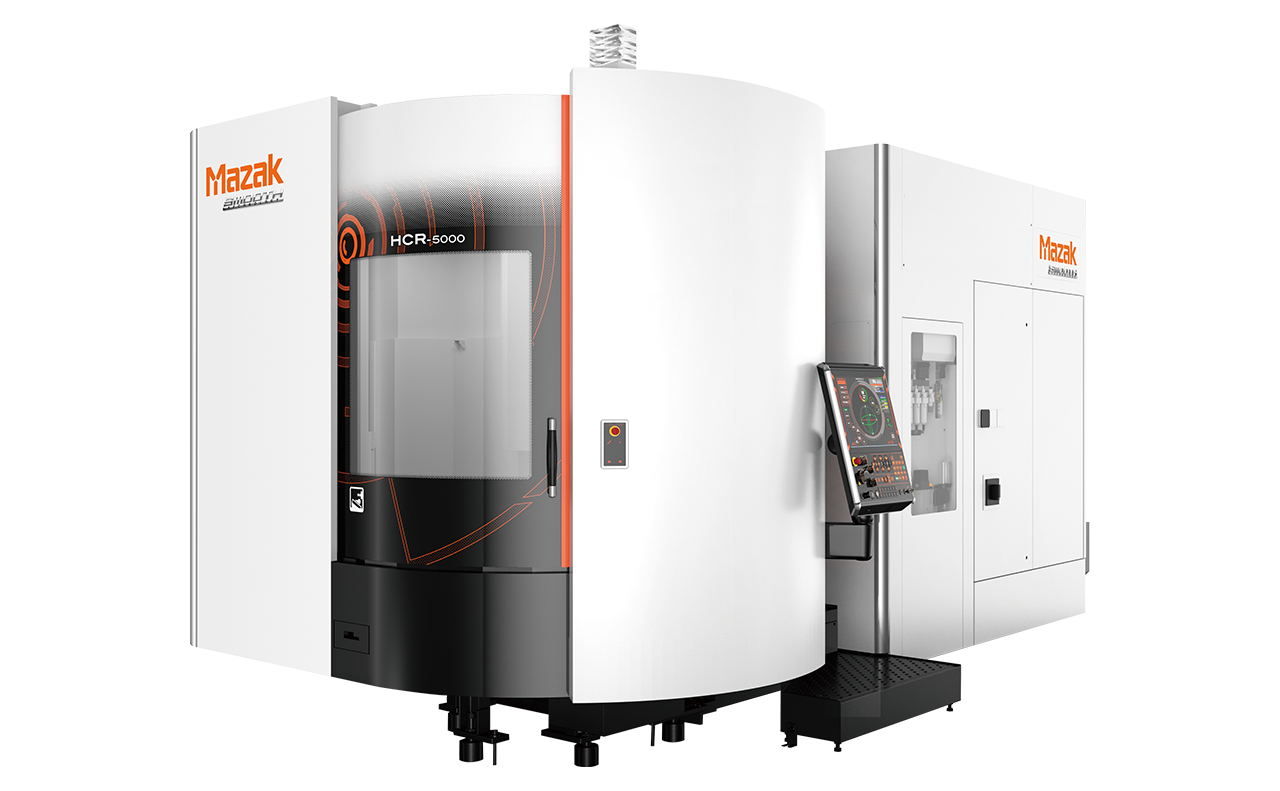
Faster simultaneous 5-axis machining cycle times

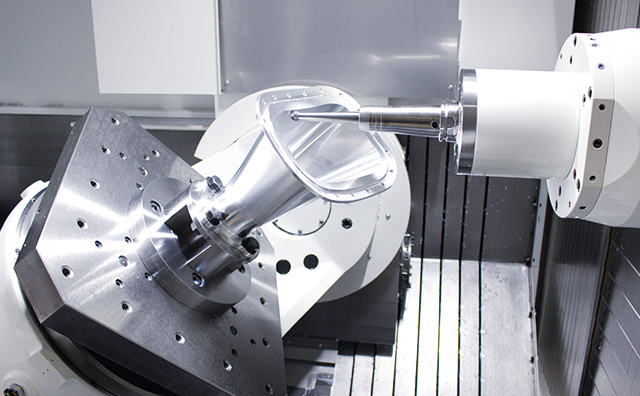
Significantly improved acceleration and jerk.
Linear axes ( X-, Y-, Z-axis )
Jerk (in rapid traverse)
X-axis, Y-axis / Z-axis : 175 m / 175 m/sec3 ← 41 m / 40 m/sec3
(Comparison with our conventional simultaneous 5-axis controlled machining centers)
Rotary table (A-, C-axis)
Rapid traverse rate
A-Axis: 30 min-1, C-Axis: 50 min-1
225°A-axis rotation
-90° to 135°A-axis rotation and ±360°C-axis rotation for the 5-axis machining of complex workpiece contours.
Roller gear cam
Both the A- and C-axis utilize a roller gear cam system for 0.0001° positioning increments and high-accuracy performance.
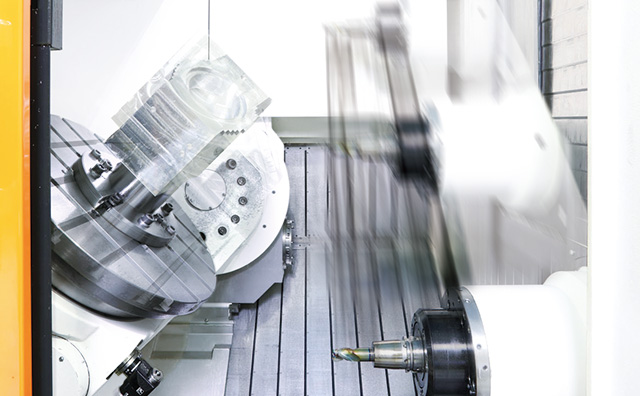
Excellent chip disposal
Large capacity coolant system and machine construction ensures smooth chip disposal
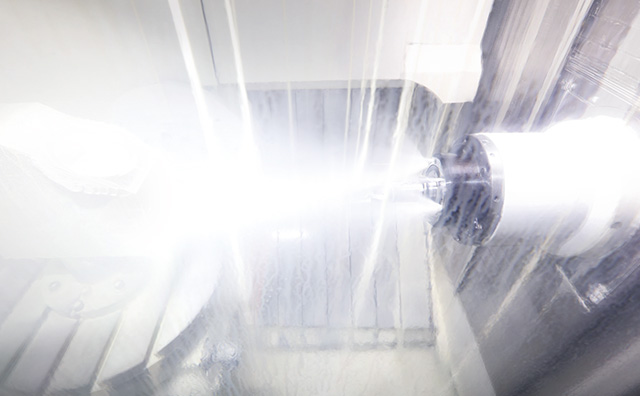
- A powerful stream of coolant will drop chips accumulated on the workpiece and pallet onto the chip conveyor in the center trough, quickly disposing them outside of the machine.
- Center trough structure to handle large amounts of chips generated in machining operations.
- Chip disposal is smoothly operated with the coolant tank (standard accessory, large capacity of 800L) which can discharge large amounts of coolant.
Applications
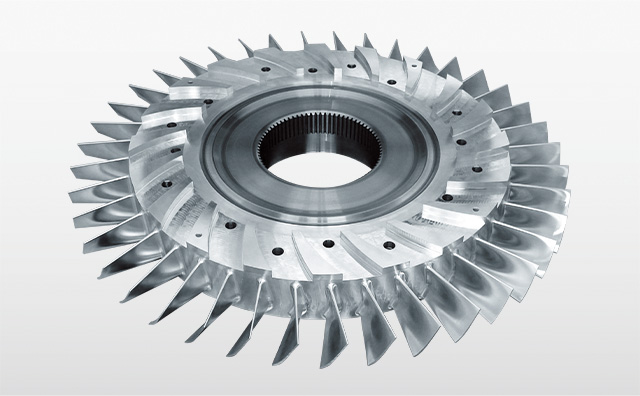
Industry: Aerospace
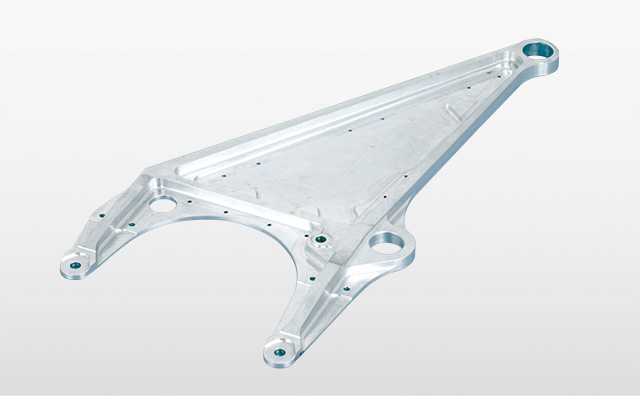
Industry: Aerospace
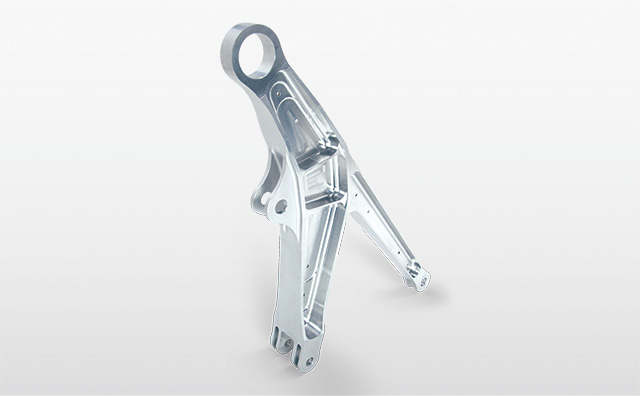
Industry: Aerospace
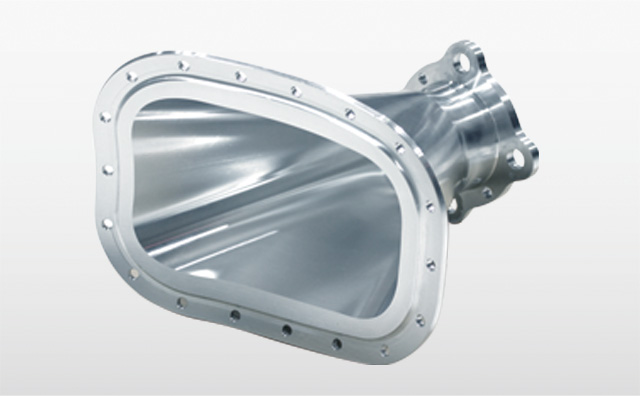
Industry: Aerospace
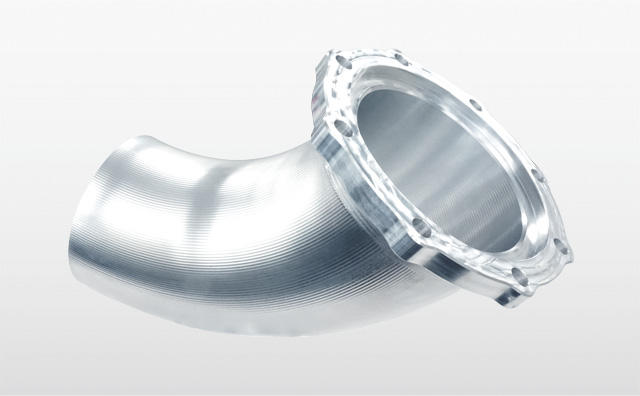
Industry: Aerospace
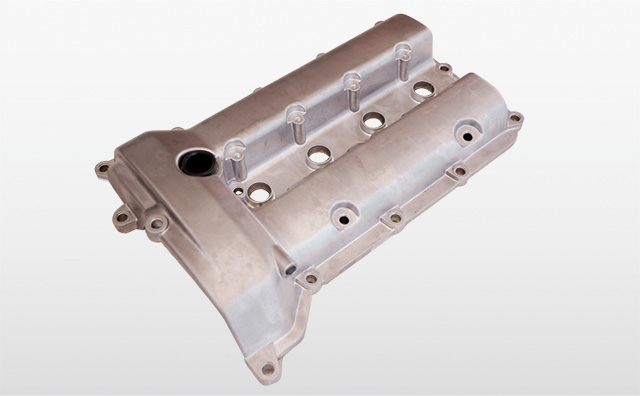
Industry: Automotive
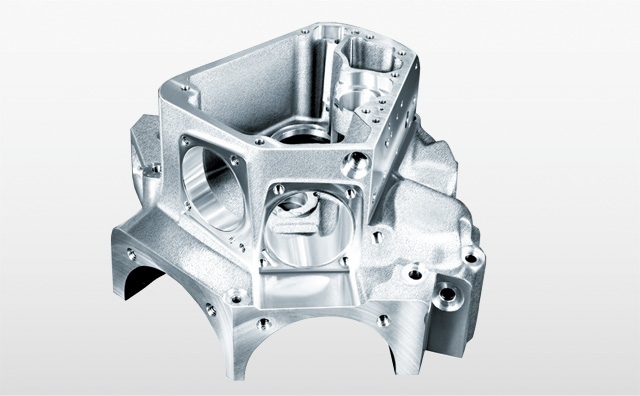
Industry: Automotive
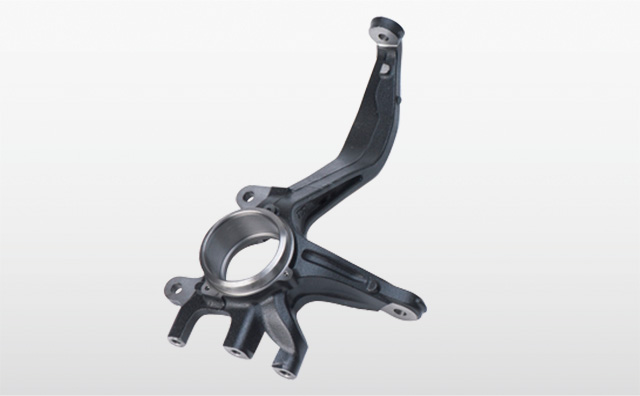
Industry: Automotive
High-speed, high-output spindle
Built-in motor structure
The integral spindle / motor design makes it possible to eliminate power loss and minimizes vibration at high revolution speeds. This leads to improving surface accuracy and extending tool life.
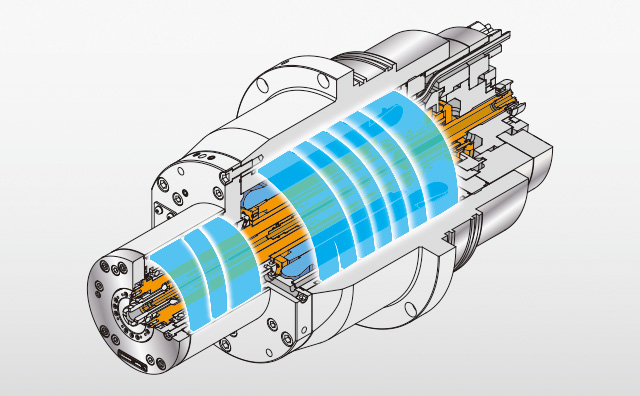
Spindle temperature control
Temperature-controlled cooling oil is circulated around the spindle bearings and headstock.
The cooling oil suppresses heat generation of the two parts, which may lead to thermal displacement of the spindle. This ultimately prevents loss of machining accuracy.
Spindle Lineup
Four types of spindles to meet the requirements of production sites
12000 min-1 18.5 kW [40% ED] BT-40 Grease lubricated (Basic model)
18000 min-1 35 kW [40% ED] BT-40 (option)
25000 min-1 23 kW [40% ED] HSK-A63 (option)
30000 min-1 80 kW [Continuous rating] HSK-A63 (option)
Automated systems for diverse workpieces and production volumes
2-pallet changer
The next workpiece can be setup during the machining of the current workpiece for higher productivity.
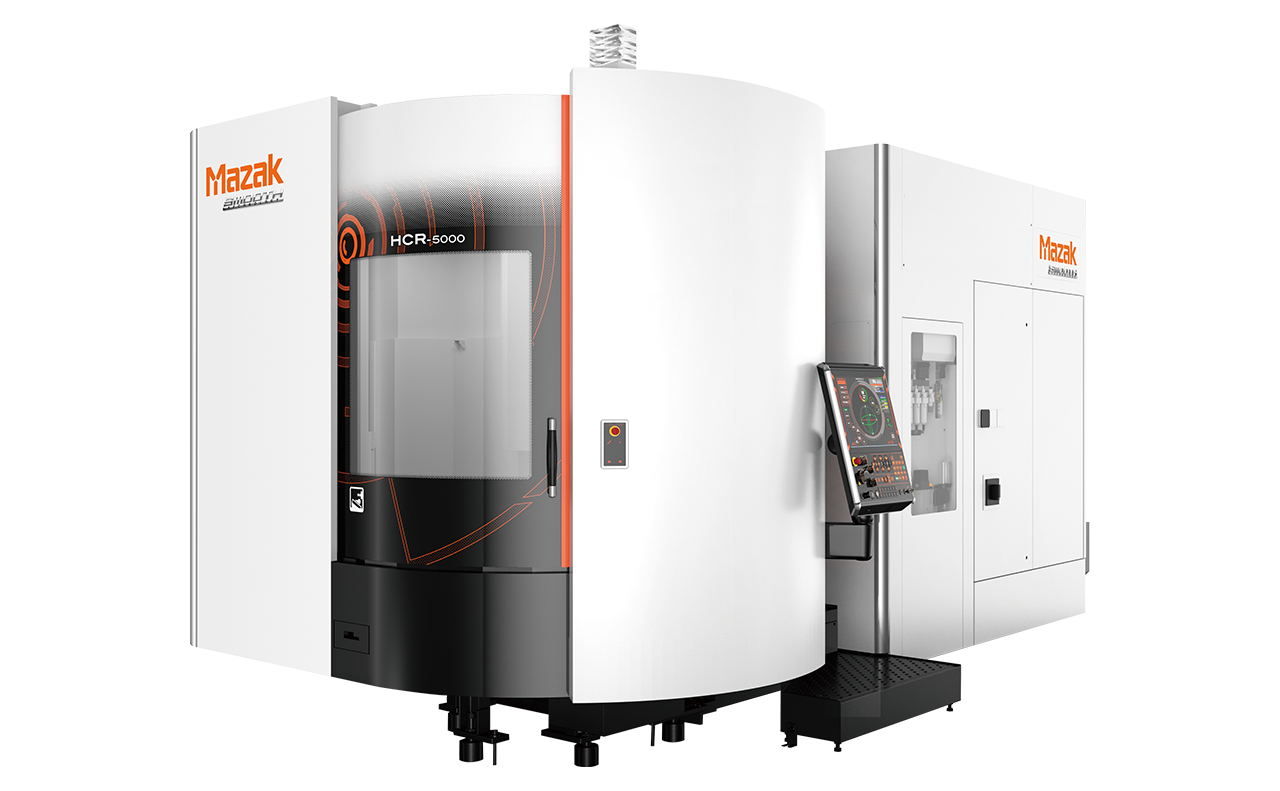

MPP(MULTI PALLET POOL) HCR-5000S
The MPP is a system to meet the increasing worldwide demand for automation. It is designed to provide high productivity in the production of a wide variety of parts in small size lots. 6, 12 and 18 pallet storage capacities are available after initial machine installation.
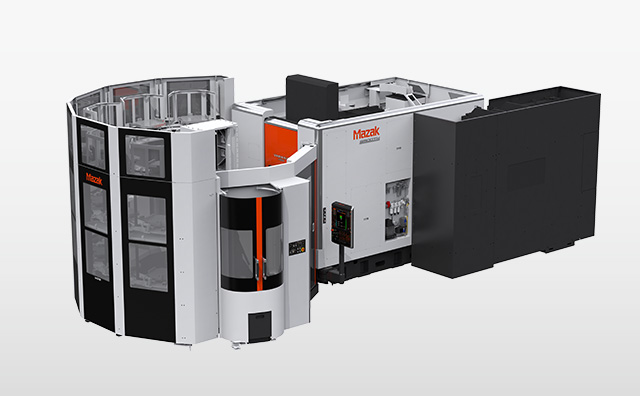

PALLETECH SYSTEM
The modular structure of the pallet stocker, pallet loader traveling unit, and loading station allows for easy system expansion based on the increase of the number of pallets or machines after installation. Pallets can be stored in a flat arrangement or in a two-leveled or three-leveled arrangement to save floor space.
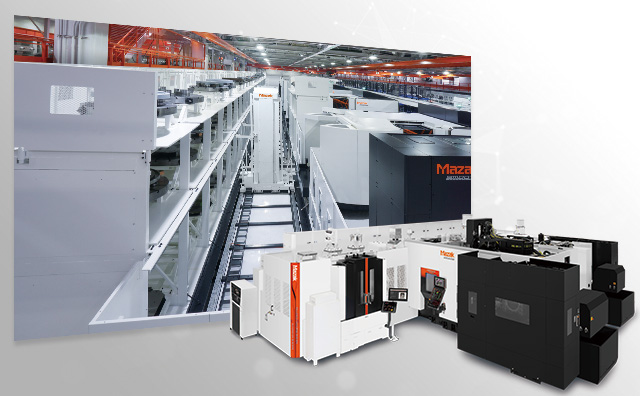