Resource saving and waste reduction
Mazak actively promotes resource-saving to have a minimum impact on our environment. We minimize consumption of consumables used for machine tools and reduce the amount of waste as well as CO₂ emissions generated in disposal process.
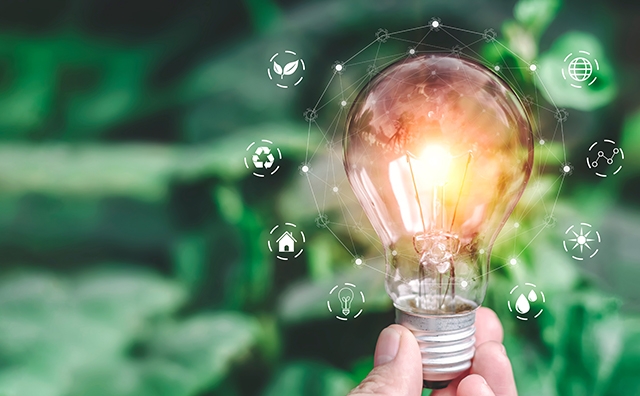
Energy-saving coolant system with sludge removal performance
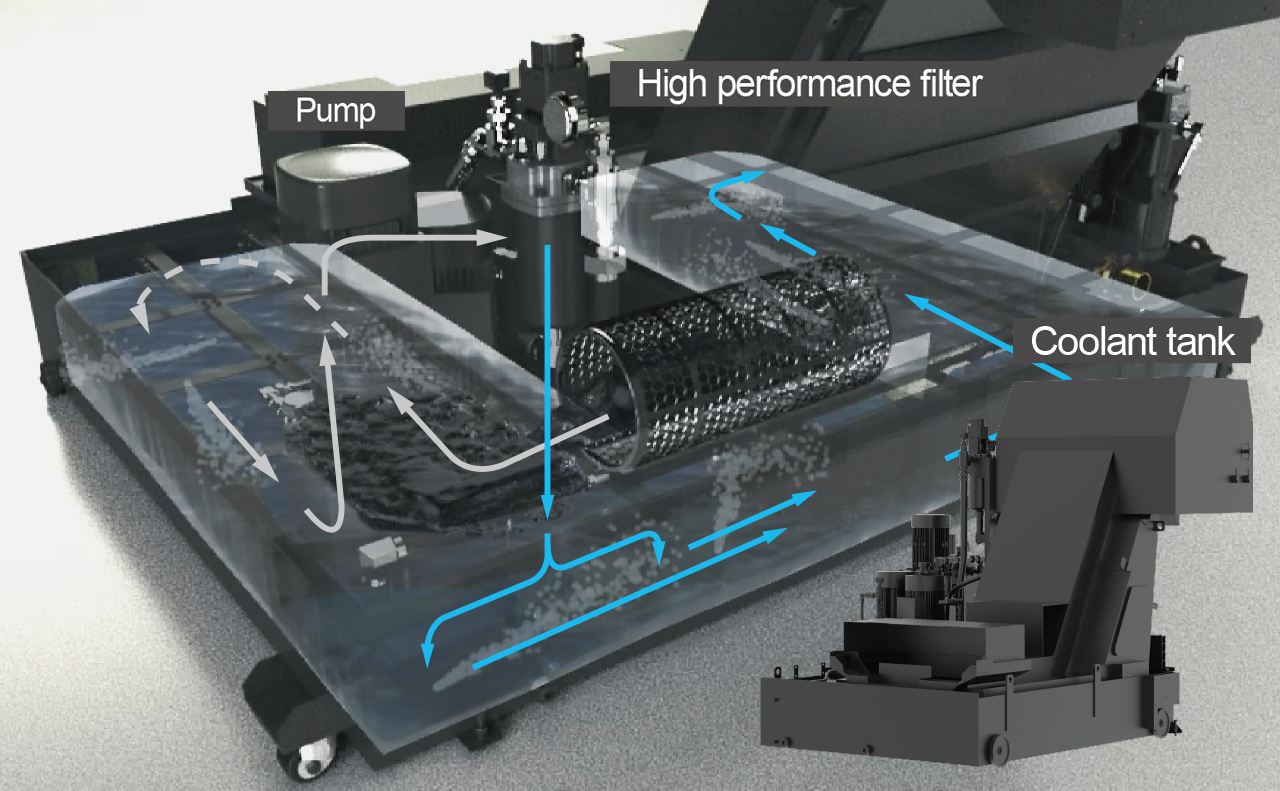
No need to frequently clean the tank
The coolant tank has a coolant jet that makes a vortex in the center so that small machined chips will not settle in the tank. This feature makes it possible to keep the coolant tank clean and extend the service life of the coolant. Ease of maintenance is also ensured. The frequency of coolant changes is reduced as well as CO₂ emissions at coolant disposal.
High performance filters removes 99% of sludge
Chips are vacuumed up together with the coolant and separated by a high-performance filter, removing 99% of the sludge.
Reduced running costs / environmental impact
Reduced tank cleaning, optimal control of coolant discharge and the efficient pump operation with inverters reduces power consumption and CO₂ emissions.
Reduced consumption of grease lubrication
A high-performance grease-lubricated LHL centralized lubrication system is used for the X,Y, and Z-axis to minimize the consumption of lubricating fluid. In the case of the vertical machining centers VCN-600, annual consumption was reduced by approximately 46%* compared to conventional machines.
- *| Consumption amount for 300 days (10 hours of daily operation)