Process integration
Process integration by hybrid multi-tasking machines and automation systems can reduce not only the number of machines but also energy consumption during machining.
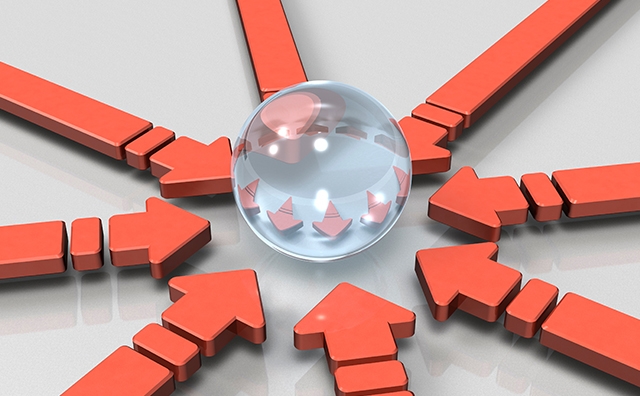
Process integration enables reduction of CO2 emissions
By integrating additive manufacturing technology to hybrid multi-tasking machines, machining processes that previously required multiple machines can now be done in one machine. Additive manufacturing can deposit harder material that eliminates heat treatment process, and can perform grinding process for a substantial reduction in total production time, cost and CO₂ emissions. All of these process integration ultimately resulted in reducing the manufacturing lead time from 14 days to only one day.
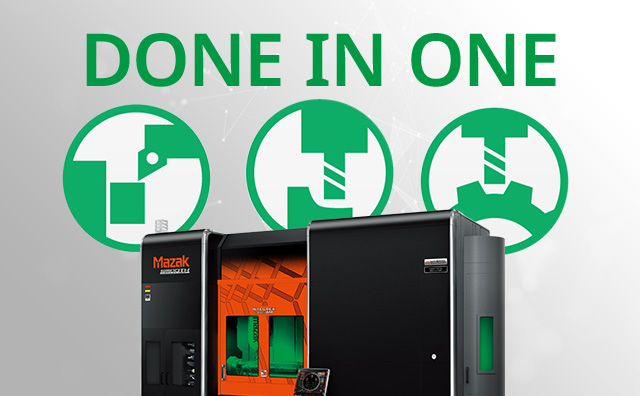
Reduce CO2 emissions by process integration that eliminates workpiece transportation
Multi-tasking machines integrated with gear machining can perform all processes such as turning, milling and gear machining in a single machine. Previously gear production required multiple machines and workpiece transportation between machines. Multi-tasking machines eliminates workpiece transportation and give considerable reduction of CO₂ emissions. In the case of pipes and steel turning gears (Φ710 mm) for laser processing machine parts, CO₂ emissions have been reduced by 1.7 tonnes.
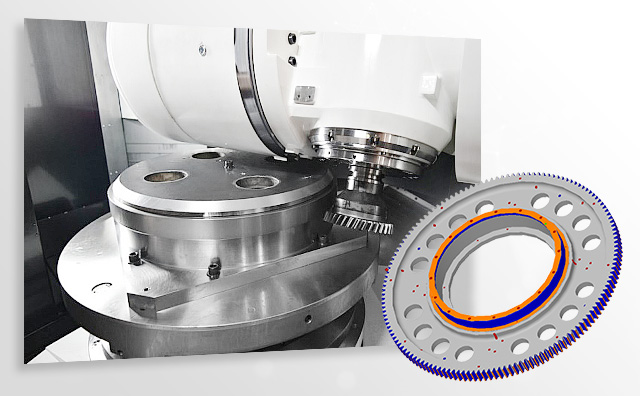
Higher efficiency energy saving by automation system
The PALLETECH automation system integrates different types of machines including horizontal machining centers, simultaneous 5-axis machining centers and multi-tasking machines into one system.
Process integration for components machining and automatic operation over extended periods of time can improve the operation rate for even more savings in energy usage.
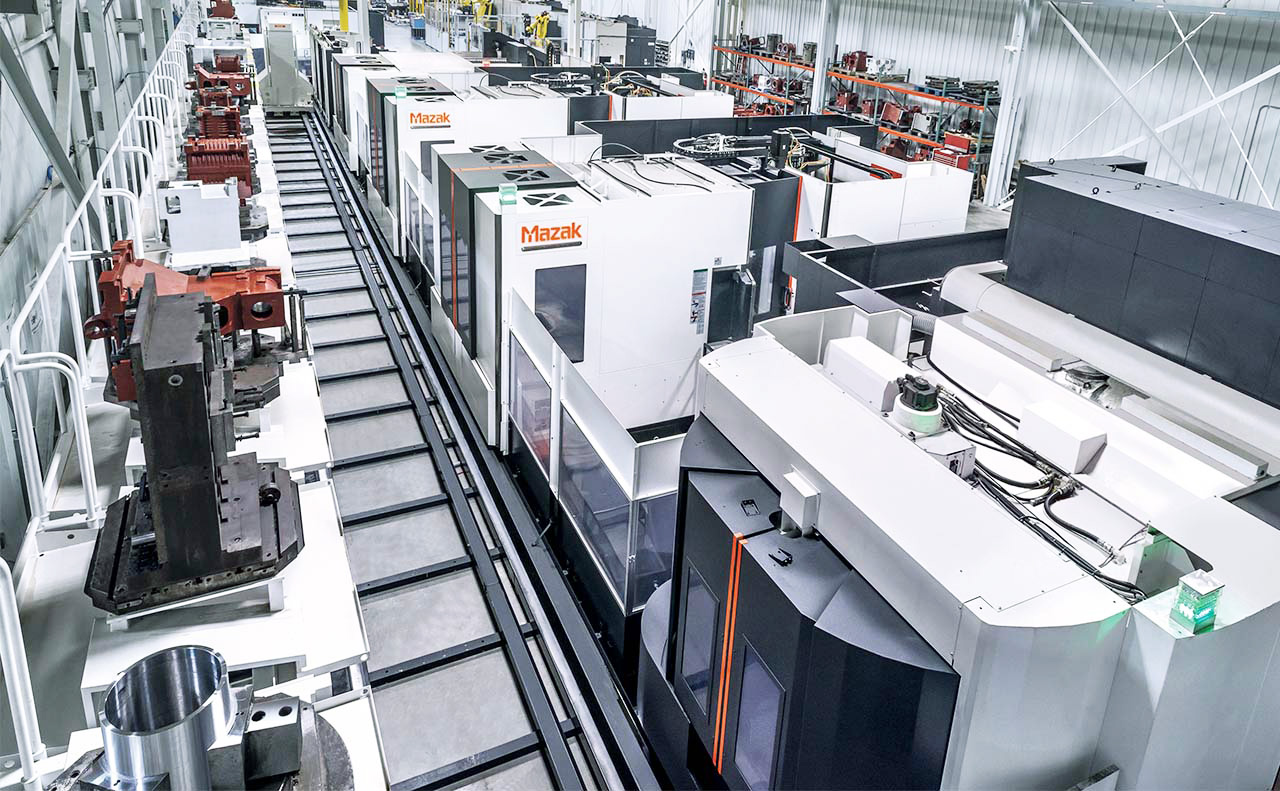