Energy-saving technology
Most of the CO₂ in the product life cycle is emitted when a machine is in use at customer's factory. We estimate approximately 80% of CO₂ is emitted in this phase. We will contribute to reducing the environmental impact at our customers' factories by developing new models and new functions with the consideration of saving energy.
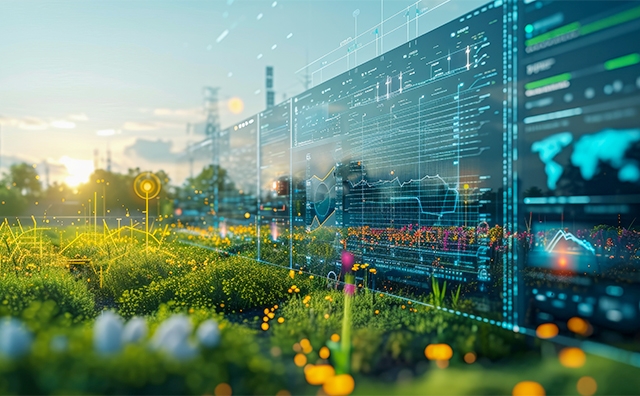
Energy Dashboard Plus contributes to energy saving of the entire factory
Power consumption and CO₂ emissions of multiple machines in a factory can be monitored by utilizing Energy Dashboard Plus of Smooth Monitor AX, our monitoring software. Using a sensor box, the operation of other manufacturer's equipment can also be monitored to save energy of the entire factory.
- Display of power consumption trends by date
- Power consumption is linked to the machining programs and used tools
- Total daily / weekly / monthly power consumption, CO₂ emissions and electricity costs can be outputted
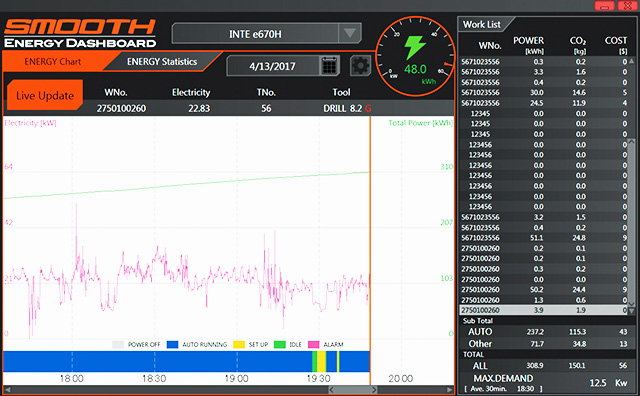
Visualization of machine power consumption with MAZATROL (Energy Saver)
Energy consumption and the regenerative power produced through the energy-saving equipment can be viewed visually on the MAZATROL CNC system. The system can control coolant and other equipment based on the cutting amount to reduce power consumption.
- Graphical Display
- Trend display
- Optimal control function
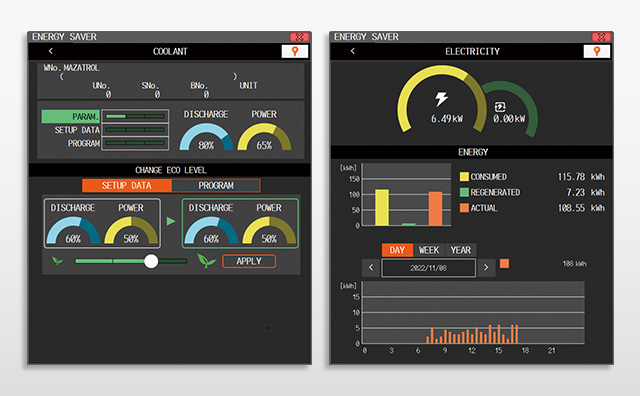
Optimal control of coolant and standby power with MAZATROL (Energy Saver)
Optimal control of coolant discharge amount
Energy Saver automatically determines the optimal coolant discharge for energy-saving machining. Processing with reduced power consumption is possible at all times.
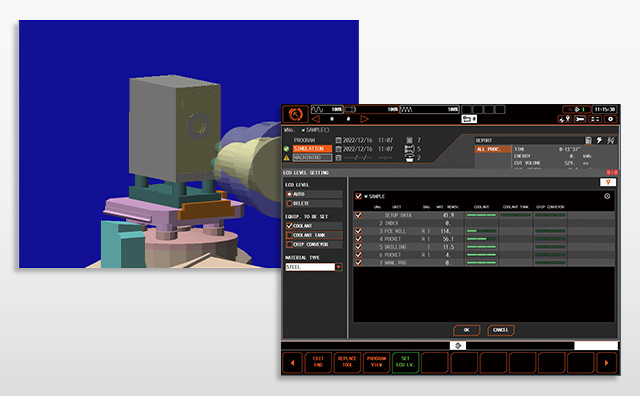
Auto power off for lower energy consumption
The machine worklight, CNC screen, chip conveyor, cover coolant and other equipment can be set to energy-saving mode with Energy Saver. The off time after standby can be set for each equipment, reducing power consumption. Energy-saving mode can reduce power consumption by approximately 65% compared to normal standby state.
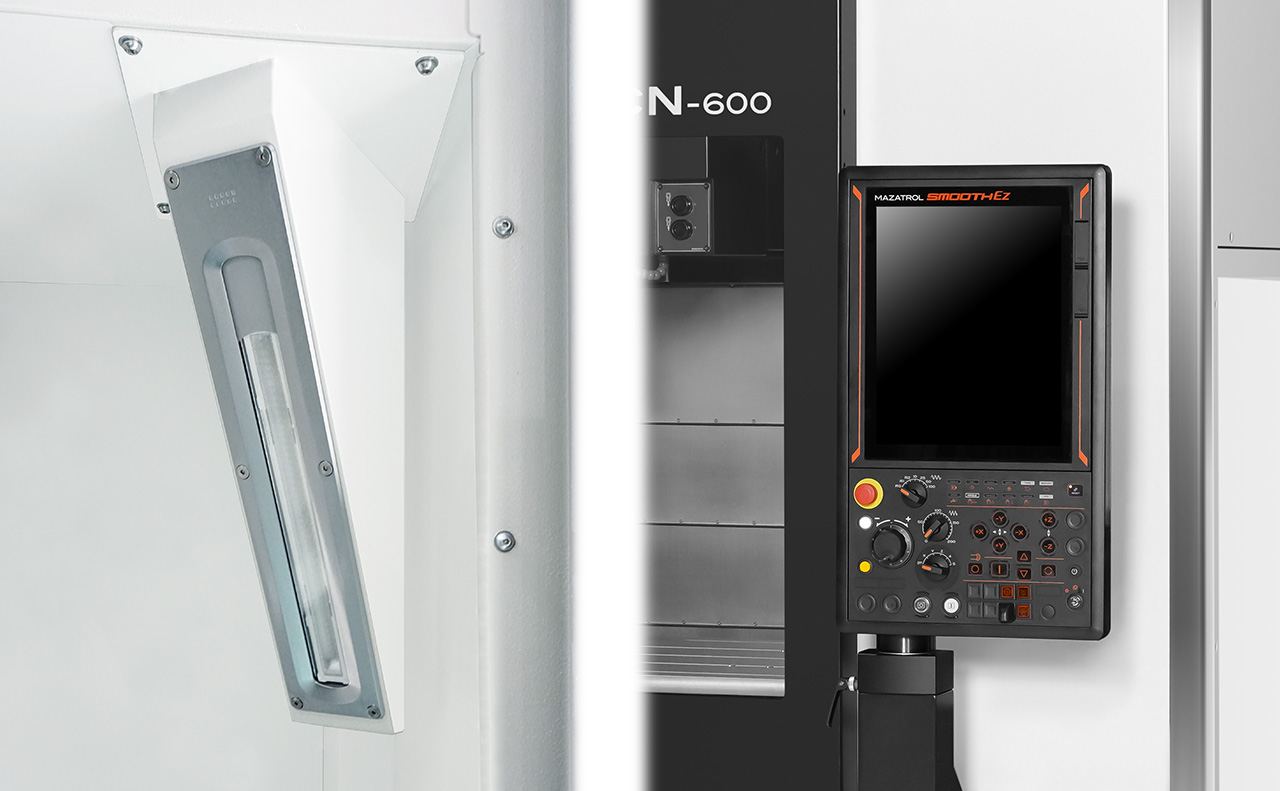
High energy-saving chiller unit
Improved refrigerant inverter optimizes cooling capacity according to the spindle load during machining, achieving a higher energy saving rate. As an example, the vertical machining center VCN-600 was able to reduce annual power consumption by approximately 11% compared to conventional machines.
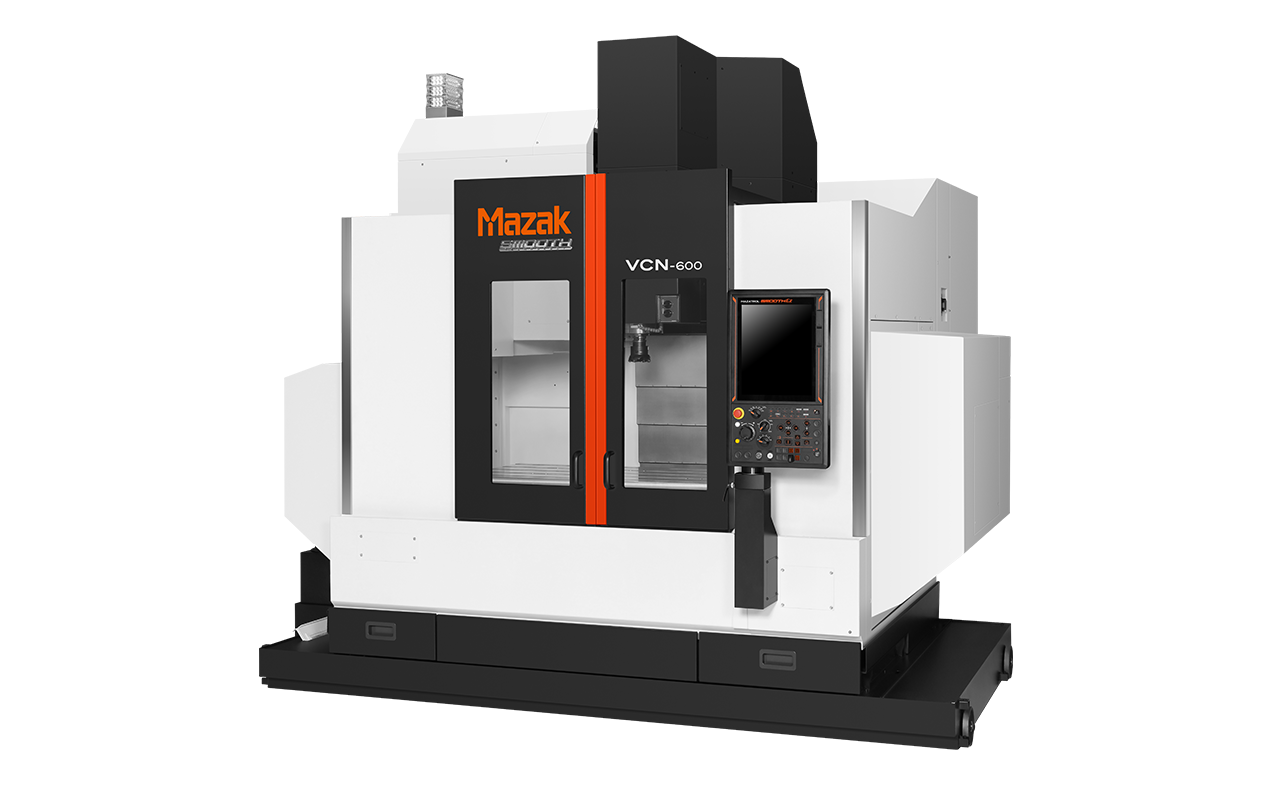
Significantly reduces CO2 emissions during machining
By equipping a hydraulic unit that utilizes an accumulator with an inverter type chiller unit, energy consumption in operation is significantly reduced. As an example, the VARIAXIS i-800 NEO 5-axis machining centers consumes approximately 21% less power per year compared to conventional machines.
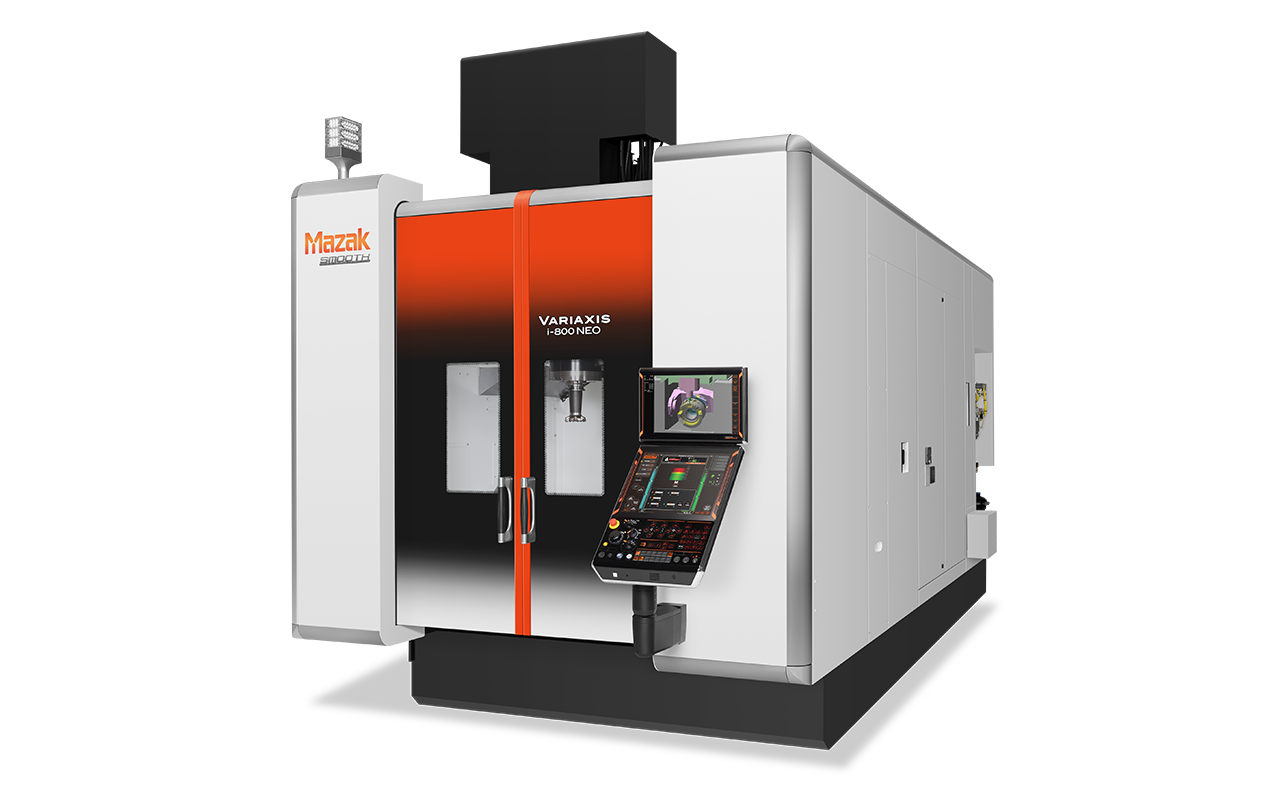
Regenerative electric power system
The power regeneration converter recovers the energy generated by acceleration/deceleration of the spindle motor and servomotor. Recovered energy is supplied to other equipment for effective energy saving. Regenerative electric power system is available for all Mazak models to reduce CO₂ emissions.