Pallet size | 320 mm × 320 mm |
Max. spindle speed | 45000 min-1 |
Max. workpiece size | Φ400 mm × 300 mm |
5-Axis Machining Centres
UD-400/5X
High-accuracy 5-axis machining centre for mould and precision machining
Designed for high-speed micro precision and mould machining
Fully symmetrical double column structure, mineral casted base and column, 45,000 min -1 high-speed spindle with core cooling to prevent heat generation and vibration. Capable of long-term, stable ultra-precision machining.
CNC / software technologies developed for high-speed machining of die and mould, especially in the free-form machining field. The functions altogether enables high-productivity and excellent machined surface quality.
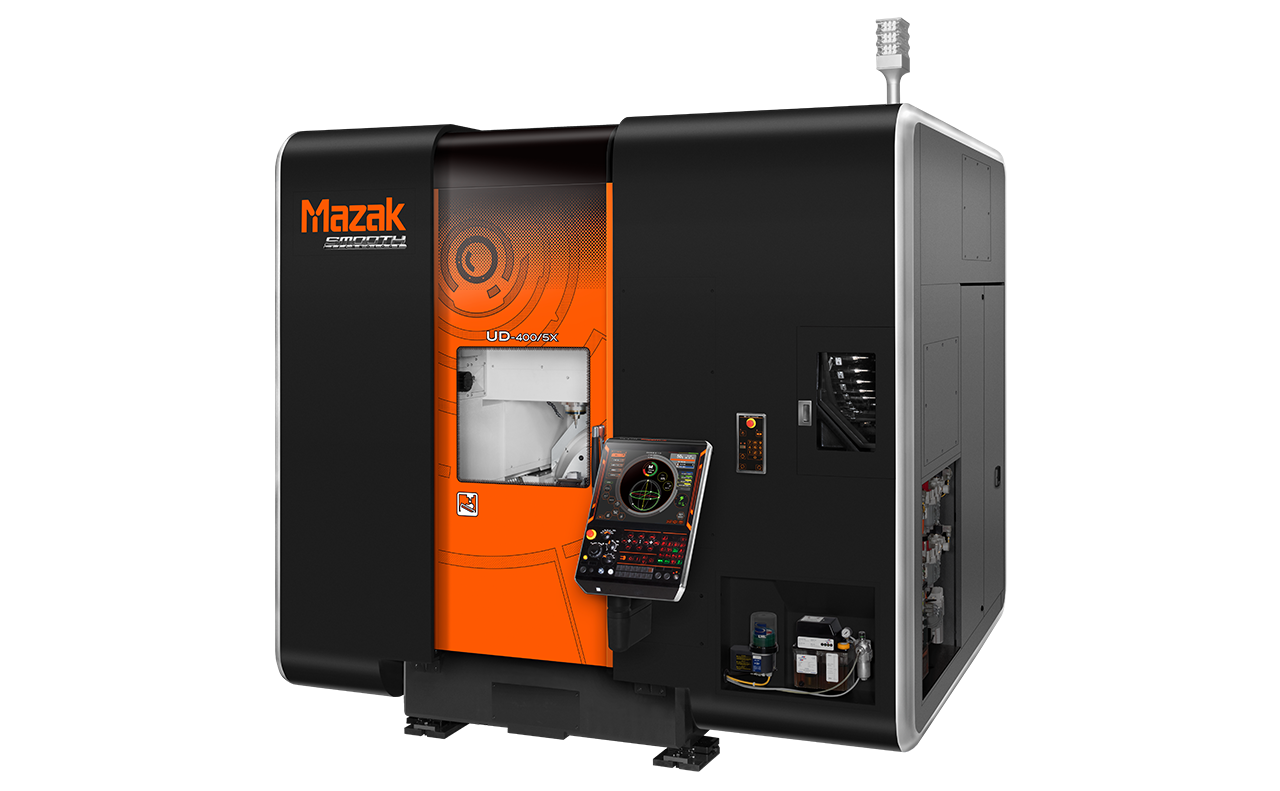
Advantages of 5-axis machining centres in mould machining and precision machining
Process integration
The UD-400/5X is capable of continuous machining of multiple surfaces and free-form surface machining by simultaneous 5-axis control, without the need to change setup.
By integrating multiple processes with a single chucking, production lead time and setup errors can be reduced.
Reduced tool protrusion length
When machining near-vertical areas with small-diameter tools, 3-axis machines require long protruded tools, limiting machining conditions such as feedrate. The UD-400/5X has a tilted table and a short tool protrusion length for stable machining. This allows the machine to function in its full potential.
Improved surface quality
The peripheral speed of the tip of the ball end mill is always zero, and machining a plane surface vertically on a 3-axis machine will reduce the accuracy of the machined surface. On the other hand, the UD-400/5X can tilt the workpiece to allow machining in areas where the tool peripheral speed is high, thus improving the quality of the machined surface and ensure stable surface accuracy.
3-Axis Machining Centres
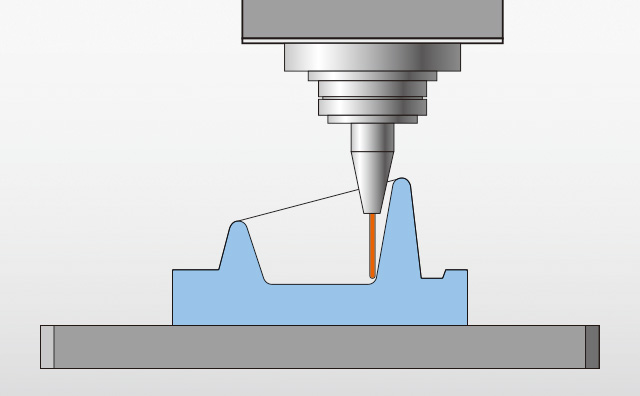
UD-400/5X
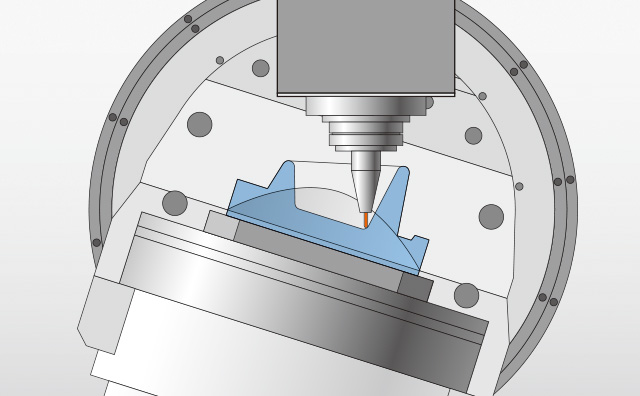
Machine construction for ultra-precision machining
High-speed 45000 min-1 spindle for ultra-precision machining
Spindle speed | 45000 min-1 |
Output [40% ED] | 13.8 kW (18.5 HP) |
Torque [40% ED] | 6.9 N.m |
Tool shank | HSK-E40 |
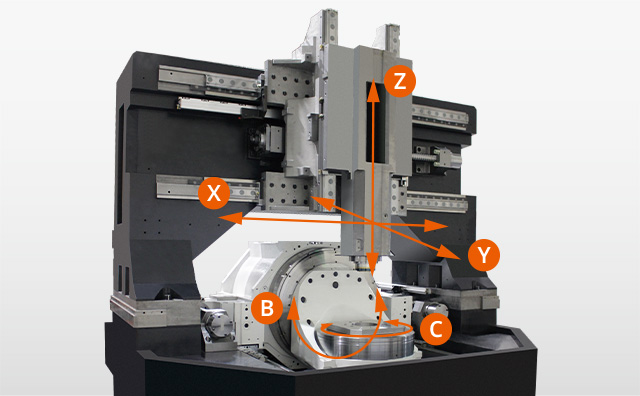
Built-in motor spindle
The integral spindle / motor design can minimise vibrations during high-speed operation to ensure exceptional surface finishes and maximum tool life.
Spindle core cooling
Temperature controlled cooling oil circulates through the spindle core and housing to ensure stable machining accuracy over extended periods of high speed operation.
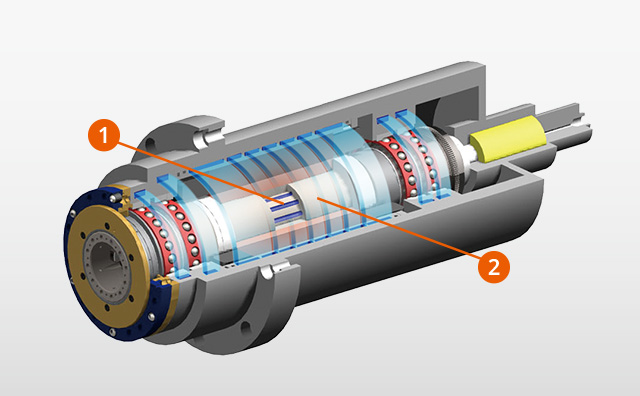
1: Spindle centre cooling 2: Housing cooling
Mineral cast
High damping mineral castings are used for the base and column. Vibrations are suppressed even during high-speed operation.
High-accuracy scale feedback
High-accuracy scale feedback is equipped on the X-, Y-, Z-, B- and C-axis.
By detecting the absolute position, higher accuracy machining during thermal expansion can be performed.
Direct drive motor utilised by B-, C-axis
Direct drive motors are used for the B- and C-axis.
Since this eliminates drive systems with belts and gears, there is no vibration, heat generation and backlash, high-accuracy machining is ensured.
High-Accuracy
MAZA-CHECK: 5-axis tuning
To improve the accuracy of the machine, misalignment and tilt of rotary axes are easily and automatically measured and offset on an easy-to-understand operation screen. In addition to offsetting position deviation traveling parallel to the linear axis, angular deviation due to tilt direction can also be corrected.
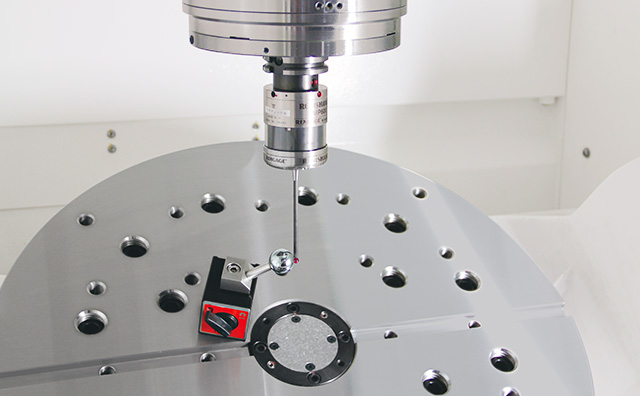
THERMAL SHIELD: Heat displacement control
THERMAL SHIELD is an automatic compensation system for room temperature changes, which realises enhanced continuous machining accuracy. MAZAK has performed extensive testing in a variety of environments in a temperature controlled room and has used the results to develop a control system that automatically compensates for temperature changes in the machining area.
Stable machining accuracy can be obtained over a long period of time without difficulty in countermeasures against thermal displacement.
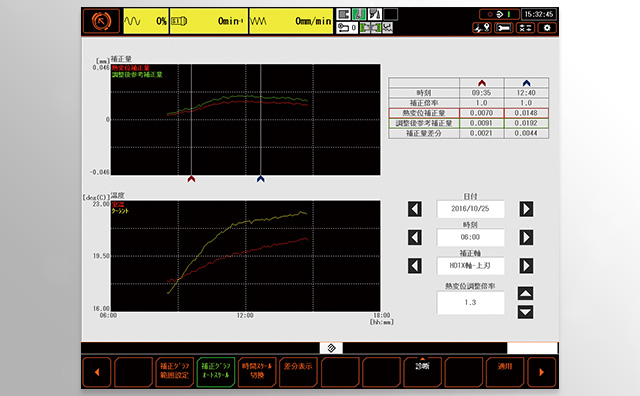