Max. worksheet width | 1250 mm |
Max. worksheet length | 2500 mm |
Laser power | 2.0 kW / 3.0 kW |
Laser Processing Machines
SUPER TURBO-X FIBER
- Laser oscillator power options of 2.0 kW and 3.0 kW for processing thin to medium thickness materials
- Table feed system for minimum floor space and excellent table access
- Various intelligent functions to automate setup work
- Highly flexible automation system to save labour
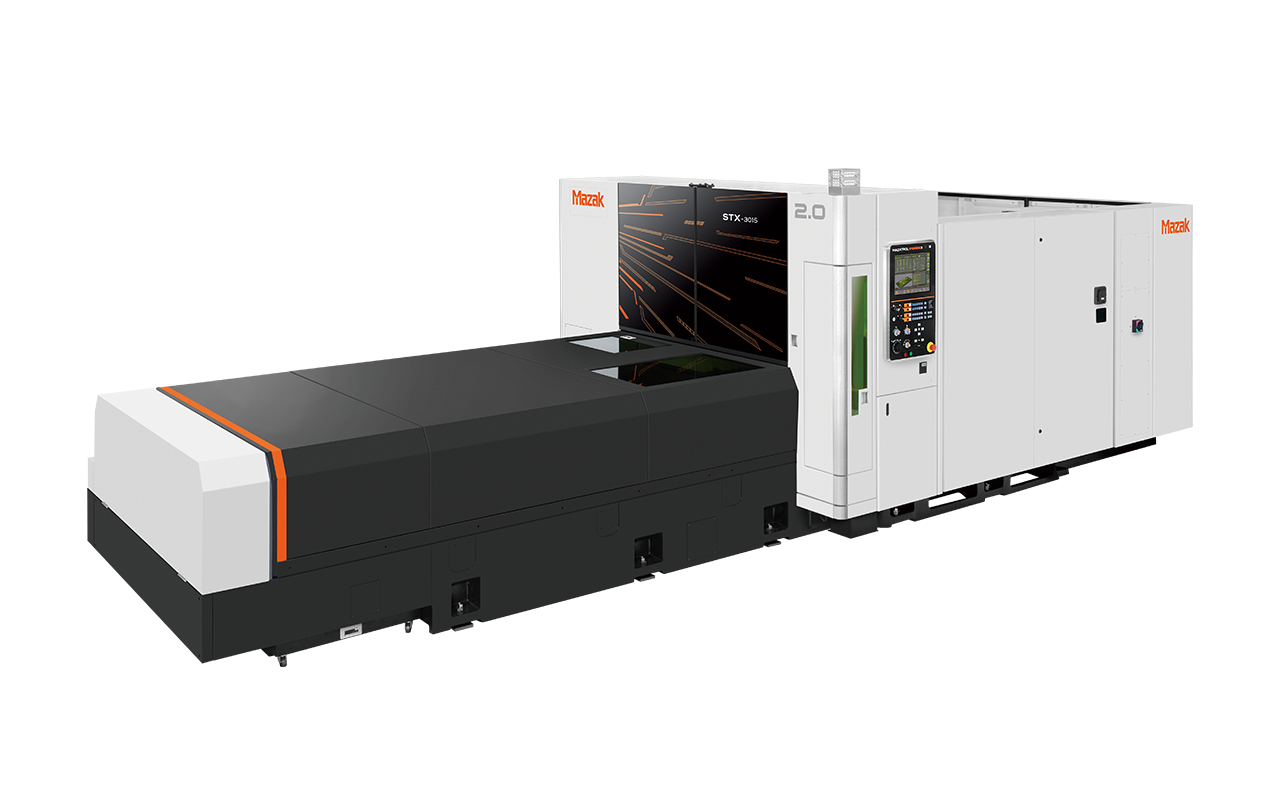
Space-saving, easy-to-operate machine design
Significant reduction in floor space
The table feed system of the SUPER TURBO-X FIBER series requires less than half the space of a standard flying optics type laser machine.
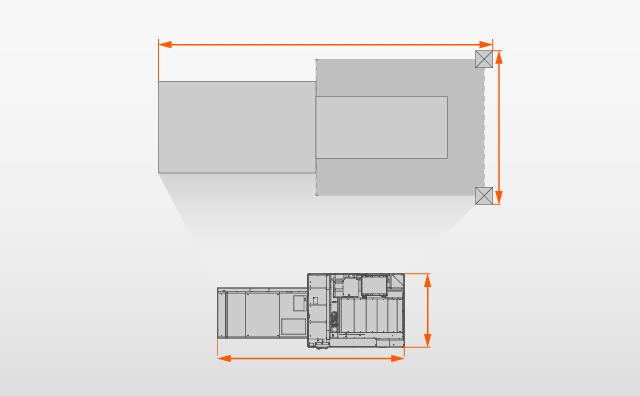
Excellent table access with the table drive system
The table feed system provides excellent accessibility and allows easy loading of material, not only for regular size worksheets, but also for remnant material, even for a single part. Unloading workpieces is also easy.
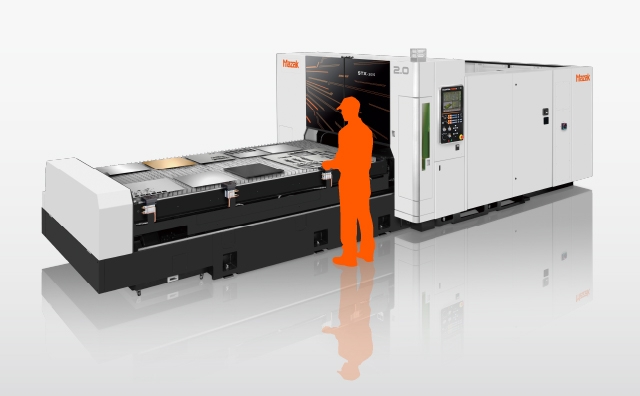
Enhanced torch for higher productivity in cutting thin to medium materials
Beam Diameter Control
This function controls the beam diameter by moving the collimating lens up and down. By adjusting the beam to the optimum diameter for various materials and thicknesses, the cutting speed of thin materials and the degree of melting of thick materials can be improved and stabilised.
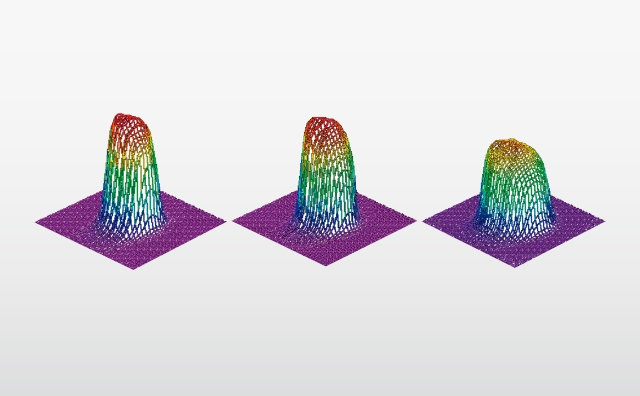
Auto Focus Positioning
The focal point is automatically adjusted to match the material by moving the focus lens up and down. Adjusting the optimal focus position between piercing and cutting enhances processing speed and productivity.
Machine model | SUPER TURBO-X FIBER SERIES |
---|---|
Torch type | Multi-control torch |
Beam Diameter Control | 〇 |
Auto Focus Positioning | 〇 |
Intelligent functions to automate setup work
Intelligent Set-up Functions
By automating the setup and adjustment work that are required every time the plate thickness or material changes, productivity is improved, resulting in a reduction of approximately 59 minutes in working time compared to conventional laser processing machines.
Conventional laser processing machine
Set-up work by operator, approx. 60 min.
SUPER TURBO-X FIBER series
Automated setup work, approx. 1 min.
Example of reduced setup time
Conventional laser processing machine | SUPER TURBO-X FIBER series |
Long in-process time due to many processes requiring operators | The variance in setup work and time between different operators is eliminated |
(1) Operator determines cutting conditions by referring to the machining cutting data | (1) Optimum lens and nozzles are automatically determined by inputting thickness and materials using the cutting condition database |
(2) Focal distance setting by the operator | (2) Automatic detection and setting of optimum focal distance |
(3) Operator selects and replaces the optimum nozzle Operator cleans the nozzles | (3) Automatic replacement with optimised nozzles Automatic removal of cutting spatter from nozzles |
(4) Operator adjusts gap calibration | (4) Automatic setting of profiling distance |
Intelligent Monitoring Functions
The system monitors the status of laser processing.
A sensor mounted on the laser processing head detects piercing and processing defects, such as burning and plasma.
If any defect is detected, the system correct the operations or temporarily pause them to achieve optimal processing.
Comparison of cutting time
Machine
SUPER TURBO-X FIBER series (2.0 kW)
Method
Conduct 100 piercing cycles with
Pierce Detection and without Pierce Detection.
(Values are example results and for reference only)
Machine | Without Pierce Detection | With Pierce Detection |
SUPER TURBO-X FIBER series (2.0 kW) | Mild steel 9 mm | 32% reduction |
Stainless steel 8 mm | 32% reduction | |
Aluminum 8 mm | 35% reduction |
Intelligent Cutting Functions
The system controls the laser to provide optimal sharp-angle high-quality cutting and high-efficiency processing, which were previously difficult with conventional techniques. By leveraging the accumulated technology and know-how of Mazak, optimal laser processing is performed.
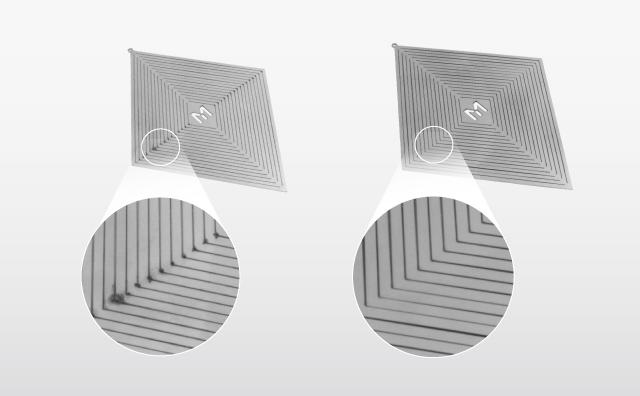
Flexible automation systems to improve productivity
Flexible Mazak Laser FMS
You can add shelves and machines to expand the system after the initial installation.
It can also be connected to your existing Mazak laser processing machines.
The number of machines can be expanded up to four.
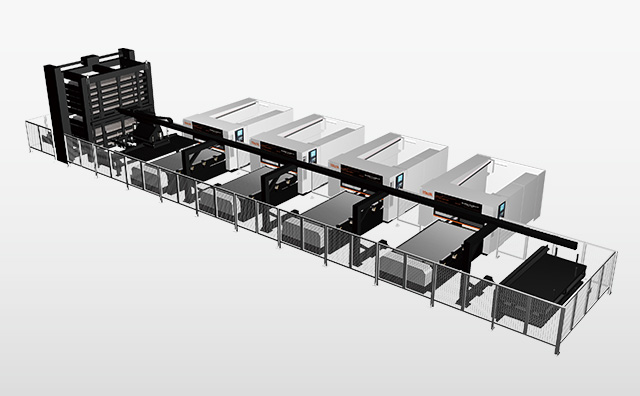
Higher productivity
Production processes can be managed through scheduled operation, enabling progress tracking.
The conveyor system can handle materials with a thickness of 25 mm. It contributes greatly to productivity improvement by reducing loading and unloading time with cranes and by reducing a heavy labour requirment.
Install new SUPER TURBO-X FIBER into the existing FMS system
The new SUPER TURBO-X FIBER model is designed to be interchangeable with the existing SUPER TURBO-X model that has been installed in the Mazak FMS system. The existing FMS system can be continued to be used as usual.
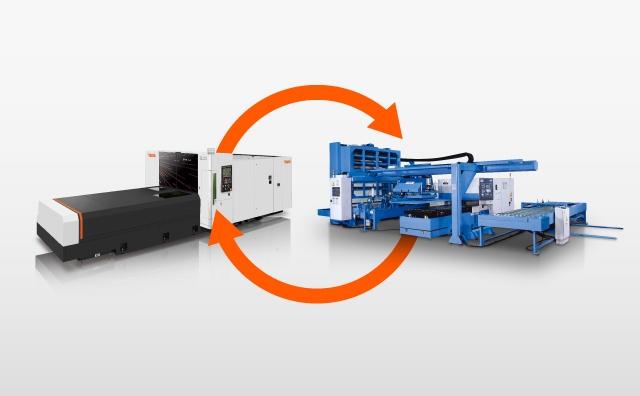
CNC system for comfortable operation
MAZATROL PREVIEW 3
15” touch panel colour LCD screen as standard. A simple, easy-to-understand screen layout ensures effortless operation. Fast access to frequently used displays such as the command screen, position screen, and programming screen.
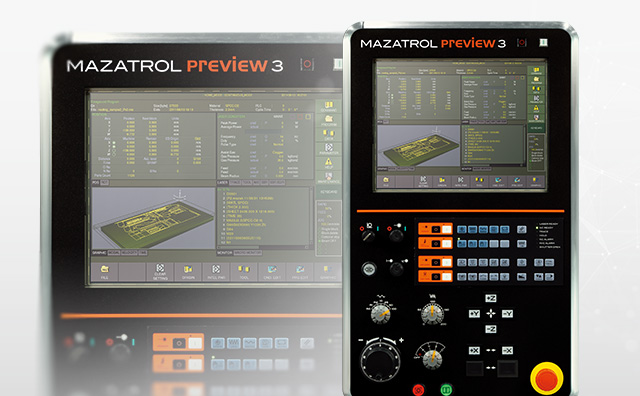