Chuck size | 8″ |
Max. machining diameter | Φ670 mm |
Max. machining length | 1011 mm / 1519 mm |
Multi-Tasking Machines
INTEGREX AG
- Gear process integration facilitates high-precision machining while reducing in-process time and initial costs.
- Three types of gear machining methods (gear skiving, hobbing, and endmilling) are integrated to meet diverse needs, from high-mix low-volume production to mass production
- Cutting tool paths and measurement can be easily and quickly generated by conversational programming
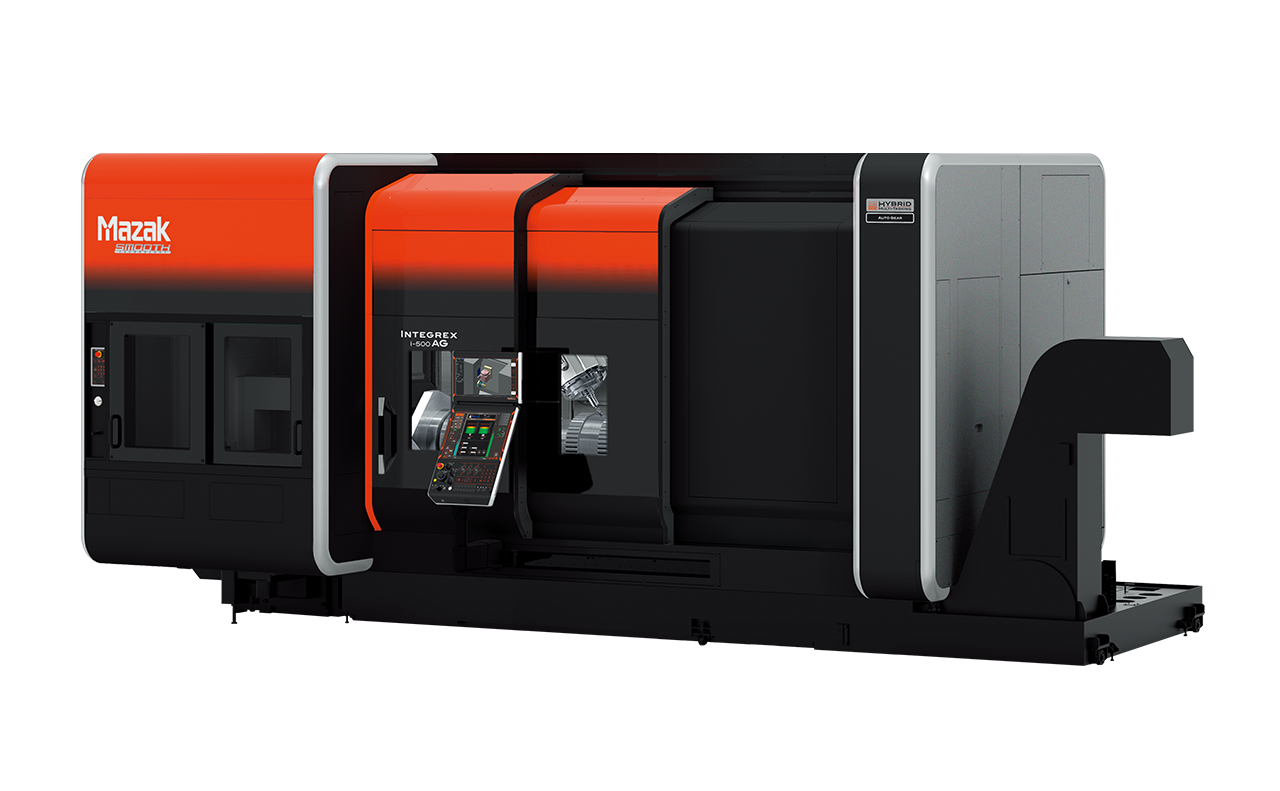
The combination of the INTEGREX with gear cutting and measurement
The INTEGREX AG series performs turning, milling, 5-axis machining and gear machining
Three gear machining methods - gear skiving, hobbing, and endmilling - are integrated into this single machine. It meets your production needs, ranging from flexible machining using general-purpose endmills to mass production using specialised tools. Furthermore, gear measurement can be performed in the machine.
- 1: 5-axis machining
- 2: Gear cutting
- 3: Gear measurement
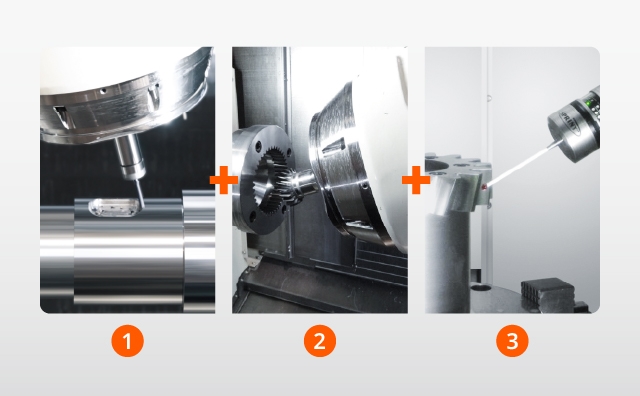
Produce gears without a dedicated gear cutting machine
Gear skiving
- High-accuracy gear skiving with the unique control technology of INTEGREX AG.
- The precision of the rotational synchronisation between the turning spindle and milling spindle is maintained even at the maximum rotational speed of each spindle.
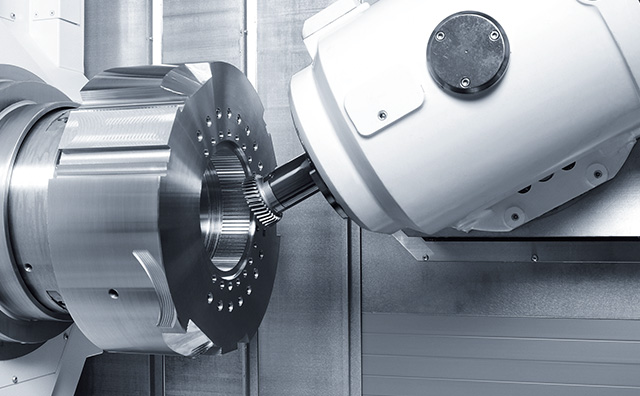
Hobbing
With intuitive settings, gear cutting is performed using dedicated hob cutters. The gear hob arbor supported on just one side provides ISO class 7 machining accuracy. The "Smooth Gear Hobbing" programming support software includes unique features. "Hob Shift" shifts the hob cutter machining point for each pass to extend the tool life and "Micro Geometry" modifies the point where the gear teeth meet after machining.
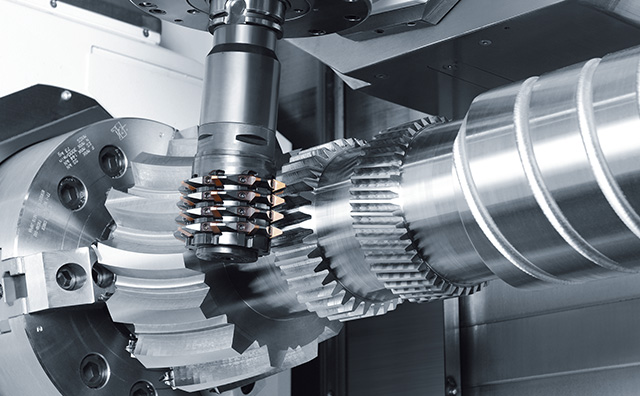
Endmilling
You can use commercially available endmills. Using the dedicated software "Smooth Gear Milling", gear teeth can be cut one by one with a standard endmill. The "Tooth Profile Correction Function" and "Tooth Lead Correction Function" modify the machined gear teeth. The functions provides ISO class 5 (former JIS class 1) machining accuracy.
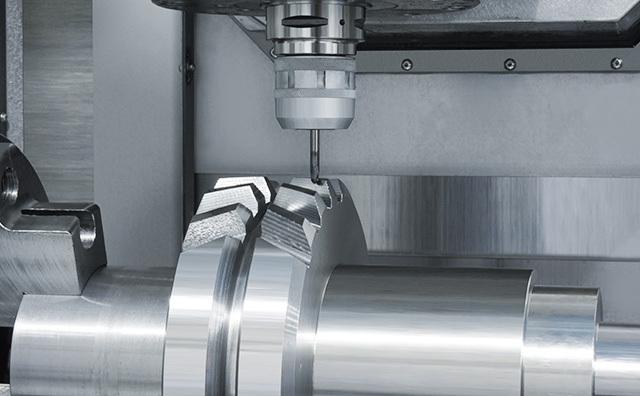
In-process time reduction
Comparison of hobbing by a multi-tasking machine and endmilling by a INTEGREX AG
In the case of parts machining for high-mix, low-volume production, specialised tools such as hob cutters require a lot of time just to prepare the tools and jigs. The INTEGREX AG can machine a wide variety of gears with commercially available endmills, thus significantly reducing manufacturing lead times.
1: Preparation of tools and jig
2: Programming
3: Gear machining
4: Machining
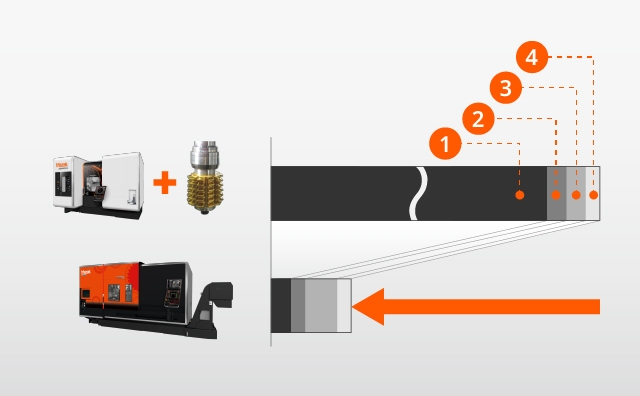
Gear tooth location for in-phase positioning of other machined features
Gear tooth radial in-phase location
After gear skiving or hobbing, the centre angle of the gear tooth groove is identified. Based on the identified phase angles, the machine can be automated up to keyway machining, drilling, and deburring with a ball endmill. The central angle of the gear tooth groove is identified on the end face or tip circle while determining the presence or absence of teeth. The actual identification accuracy is 0.005° (16 μm on a 360 mm diameter circle). The probe posture and probe feed direction without interference can be set according to the shape of the target workpiece and the stylus contact points.
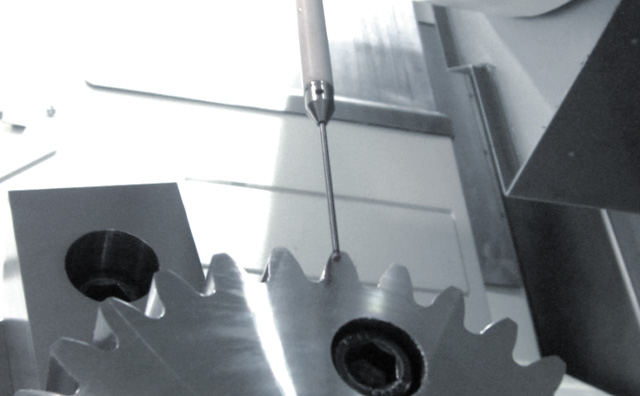
Gear face scanning is optionally available. Visualise the machined gear face by measuring the gear profile and lead.
Gear profile and gear lead measurement*
The gear profile and gear lead are measured immediately by attaching the scanning probe after machining.
The number of setups required for transporting the machined workpiece to the 3D measuring machine for inspection, and then back to INTEGREX for additional machining, is reduced.
The measurement results are displayed on the MAZATROL SmoothAi display, and the gear tooth surface can be viewed.
*Option
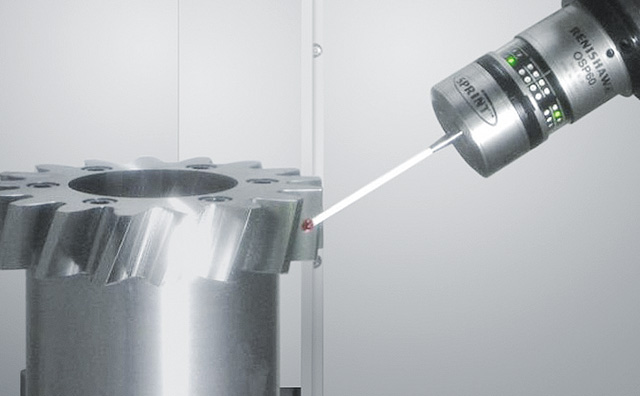
Gear tooth surface measurement with scanning probe
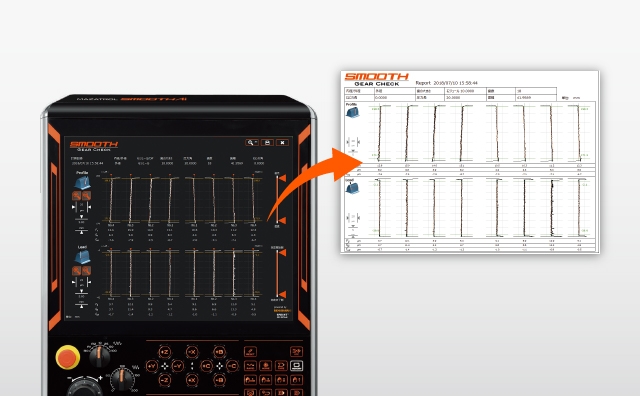
MAZATROL SmoothAi displaying measurement results
Measurement results on the CNC display can be output as an image (PNG file) with a single touch.
Conversational programming for high-accuracy gear cutting and measurement
Programs are created easily and quickly by simply setting up the various parameters and feedrates indicated in the drawings while viewing the graphical guidance. This supporting software creates dedicated G-code programs, and further generates machining and measurement paths automatically. Gear cutting and measurement are performed by pressing the cycle start button.
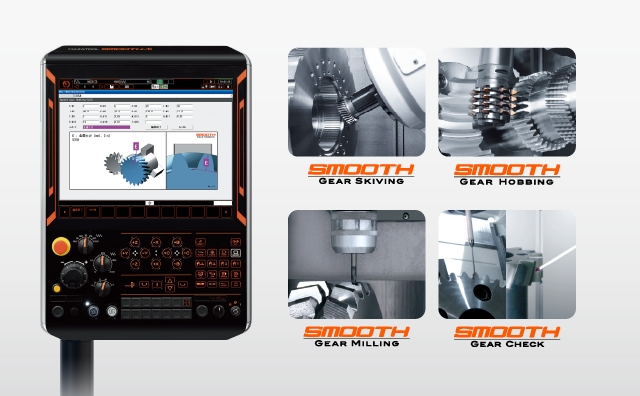