Spindelbohrung | Ø76 mm |
Spannfuttergröße | 8″ |
Max. Bearbeitungsdurchmesser | Ø320 mm |
Max. Bearbeitungslänge | 860 mm |
CNC-Drehzentren
HQR NEO
- Der Maschinenaufbau mit 3 Revolvern / 2 Spindeln reduziert die Zykluszeiten um ein Vielfaches
- Stangendurchlass bis Ø102 mm (Option)
- Automatisierungssystem für verschiedene Anwendungen vom Spannfutter bis zum Wellenteil
- MAZATROL SmoothG3 CNC-Steuerung für hocheffiziente Bearbeitung mit 3 Revolvern
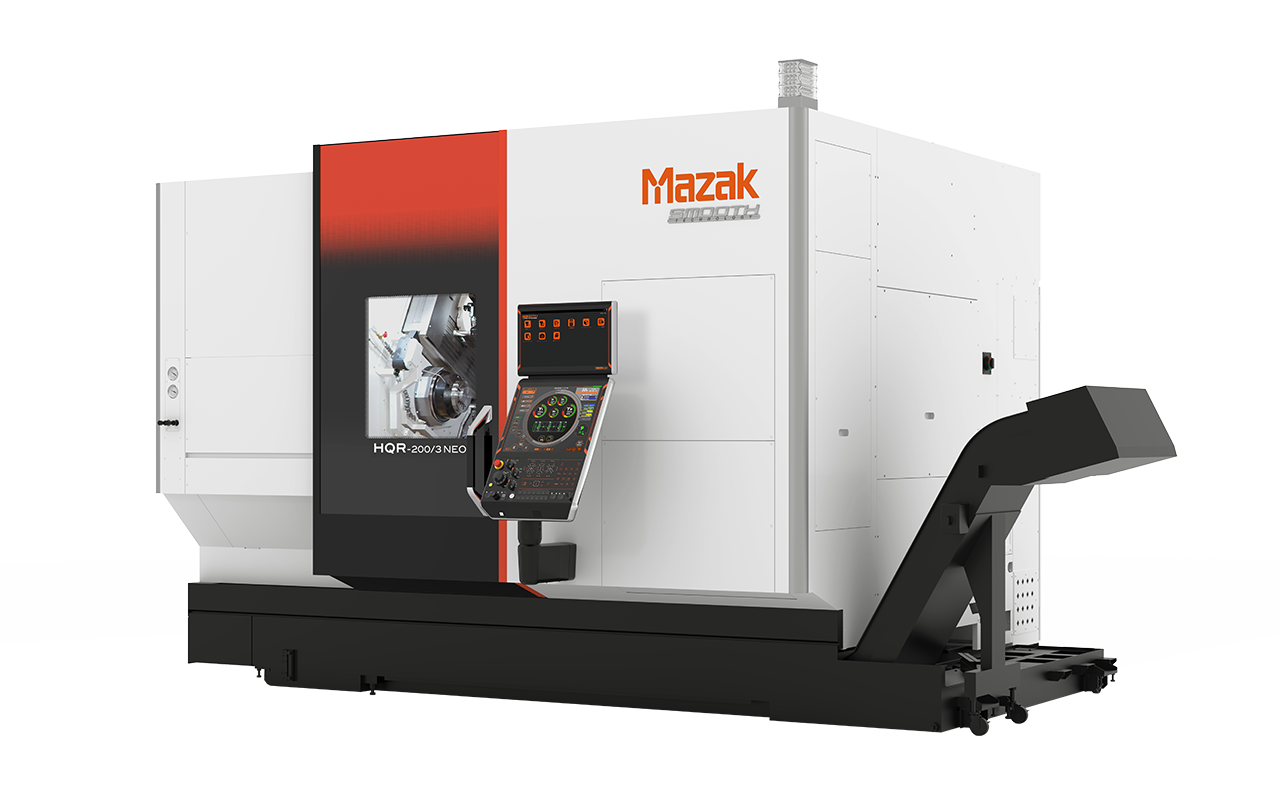
Kurze Zykluszeiten dank spezifischer Bauweise
Change to: Der einzigartige Aufbau der Maschine mit 3 Revolvern und 2 Spindeln ermöglicht die gleichzeitige Bearbeitung von zwei Werkstücken, während das Gleichgewicht durch den oberen und unteren Revolver beibehalten wird. Werkstücke, die sich im Bearbeitungsumfang zwischen dem ersten und zweiten Arbeitsgang unterscheiden, führen bei unserer Maschine zu einer signifikanten Produktivitätssteigerung im Vergleich zu herkömmlichen CNC-Drehzentren mit 2 Revolvern und 2 Spindeln.
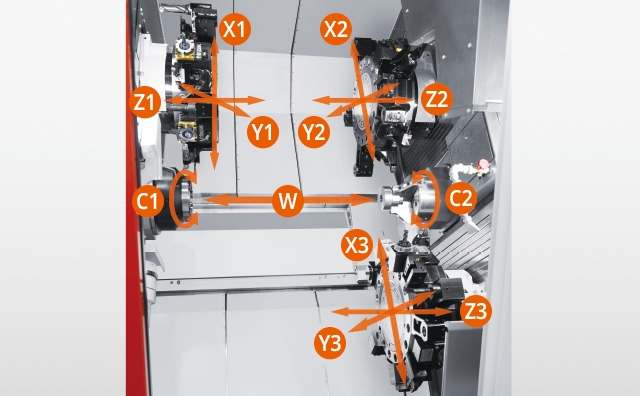
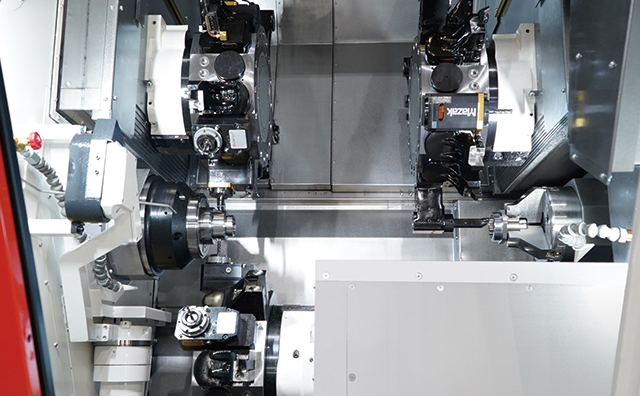
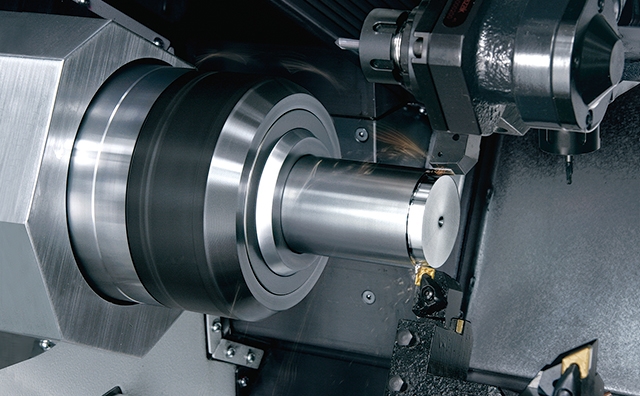
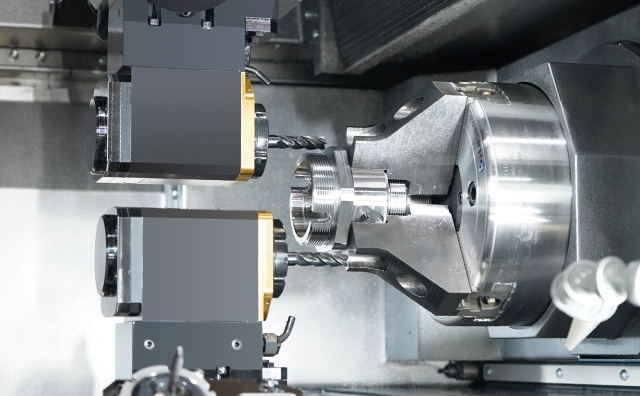
Stangendurchlass
Da sowohl die Hauptspindel als auch die Gegenspindel über große Spindelbohrungen verfügen, ist eine Bearbeitung von unterschiedlichstem Stangenmaterial problemlos möglich.
Maschinenmodell | Hauptspindel | Gegenspindel |
HQR-200/3 NEO | Ø65 mm | Ø65 mm |
Φ102 mm* | Ø65 mm | |
HQR-250/3 NEO | Ø80 mm | Ø65 mm |
Φ80 mm* |
* Optional
Höhere Produktivität dank Automatisierung
Eine Vielzahl von Automatisierungssystemen wie Stangenlader, Werkstückförderer und Roboter sind optional erhältlich, um einen langfristigen automatischen Betrieb zu unterstützen.
Stangenvorschubeinrichtung und Werkstückentladesystem
Effektive Fertigung des Werkstücks direkt aus dem Stangenmaterial. Durch den Einsatz eines Werkstückentladers anstelle des automatischen Teilefängers wird das Werkstück aus der Maschine entnommen, ohne die hochwertige Oberfläche zu beschädigen.
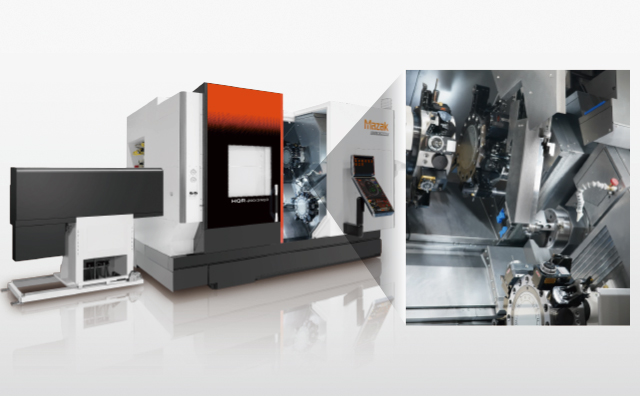
- Schritt 1
- Schritt 2
MAZATROL SmoothG3 CNC-Steuerung
4-Achsen-Simultanbearbeitung

- Die praxisorientierte grafische Benutzeroberfläche gepaart mit den Vorteilen eines Touchscreens ermöglicht schnelles Programmieren und hohe Bedienerfreundlichkeit.
Der spezielle Bildschirm für drei Revolver unterstützt zusätzlich die komplexe Bearbeitung.
- Die integrierte Kollisionskontrolle erkennt die komplexen Bewegungen der drei Revolver und vermeidet diese bevor sie passieren und gewährleisten so einen sicheren Betrieb.
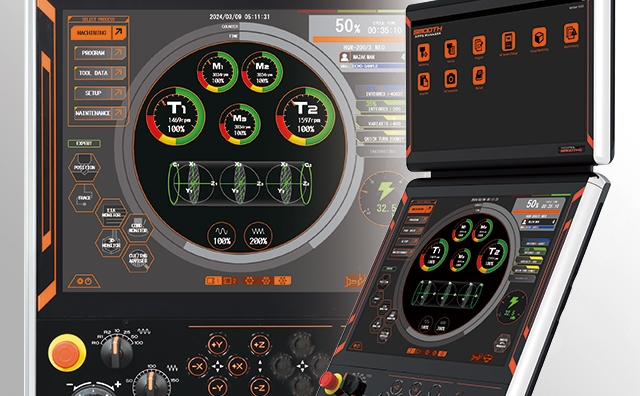
Schnittstelle für optimierte Benutzerfreundlichkeit
Großer Touchscreen für intuitive Bedienung
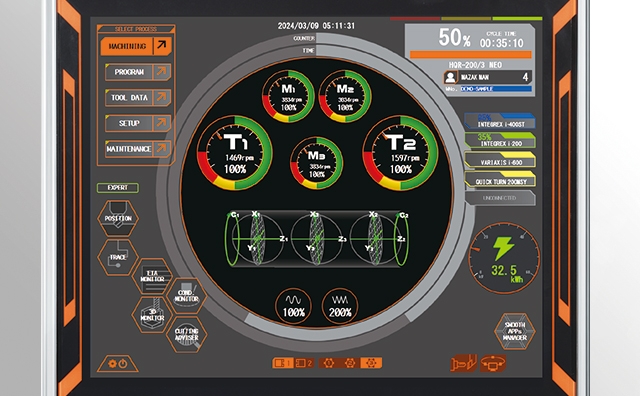
Hocheffiziente Bearbeitung mit speziellem Display für drei Revolver und Unterstützungsfunktionen
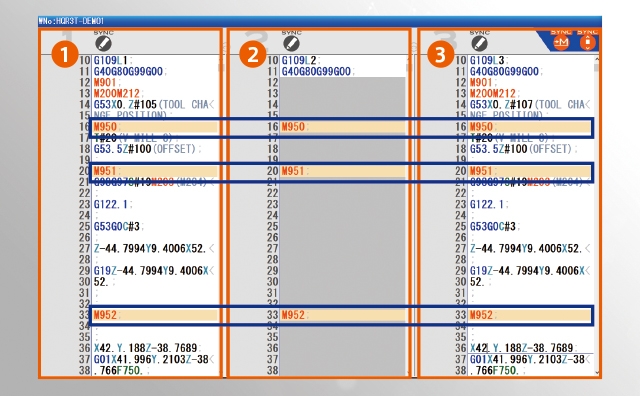
Das in drei Spalten unterteilte Display macht es ganz einfach, den Betrieb von jedem einzelnen Revolver zu überwachen. Der EIA/ISO-Programmierbildschirm zeigt die wartenden Befehlspositionen nebeneinander an und ermöglicht so eine intuitive und einfache Programmbearbeitung.
Verschiedene Programmprüffunktionen
Programmprüfungen sind bei Maschinen mit drei Revolvern ebenfalls schwierig, da die Bewegungen der Revolver sehr komplex sind und die Synchronisierung der einzelnen Revolver nur schwer zu gewährleisten ist.
Diese Funktionen unterstützen die Programmprüfung ohne die Synchronisation der Revolver zu stören.
Virtuelle Bearbeitung
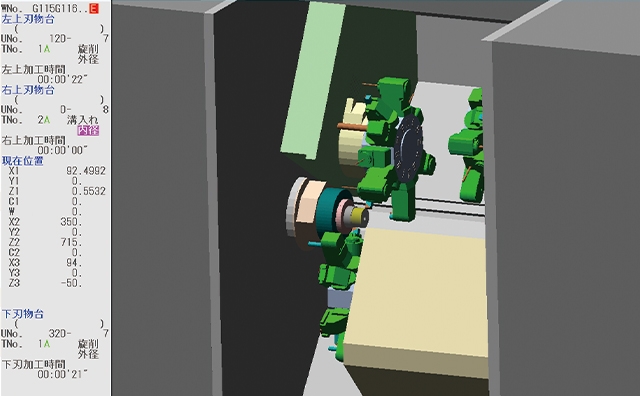
Durch eine Simulation unter den gleichen Betriebsbedingungen wie sie bei der Maschine vorliegen, wird die Bearbeitung und mögliche Kollisionen im Voraus überprüft.
Dies ermöglicht einen hochproduktiven Betrieb vom ersten Werkstück an.
Safety Shield
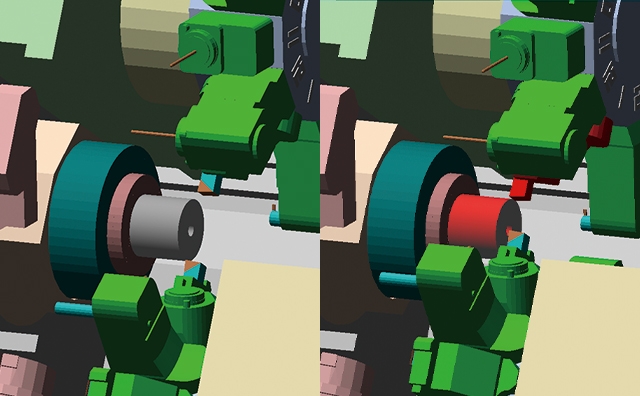
Selbst wenn die Achsen während dem Einrichten manuell bewegt werden, prüft das 3D-Modell auf dem NC-Bildschirm auf Kollision und alarmiert den Bediener, um Maschinenkollisionen zu vermeiden.
Inter-Grid Single Block Bedienung
Wenn ein Revolver einen Prozess beendet, werden alle Revolver gleichzeitig angehalten, auch wenn das Ende des Blocks für jeden Revolver unterschiedlich ist.
Dieser Inter-Grid Single Block-Betrieb sorgt für die Synchronisation zwischen den Revolvern und verhindert Störungen und längere Ausfallzeiten aufgrund von Programmfehlern.
Mit Inter-Grid Single Block Bedienung
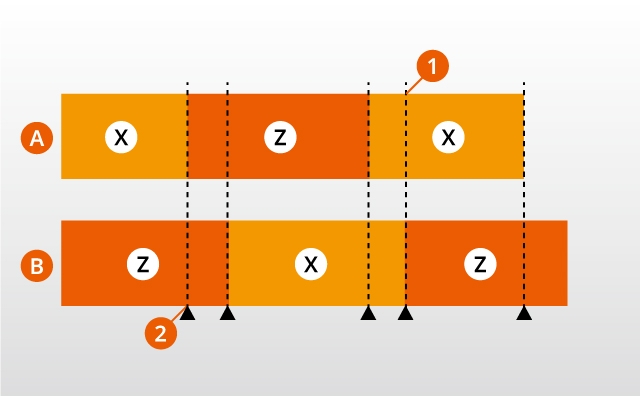
A: Revolver A
B: Revolver B
1: Wenn die Zustellung in der X-Achse des Revolvers B die Markierung ▲ erreicht, stoppt auch Revolver A.
2: Wenn die Zustellung in der X-Achse des Revolver A die Markierung ▲erreicht, stoppt auch Revolver B.
▲: Betriebsende
Ohne Inter-Grid Single Block Bedienung
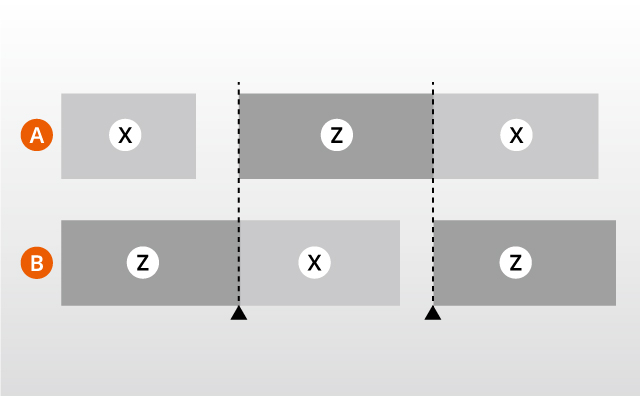
A: Revolver A
B: Revolver B
▲: Betriebsende
Synchronisierte Override-Bedienung
Die Übersteuerung, die eine Anpassung der Programmverarbeitungszeit ermöglicht, spiegelt sich nicht nur in der Betriebszeit der Revolver wider, sondern auch in der Standby-Zeit, so dass der Programmbetrieb ohne Unterbrechung der Synchronisation zwischen den Revolvern möglich ist. Dies ermöglicht eine präzise Kollisionsüberwachung.
Mit synchronisierte Override-Bedienung (50%)

A: Revolver A
B: Revolver B
1: Verweilzeit (Standby-Zeit)
2: Unterstützende Funktionen
3: Keine Programmfehler
Ohne synchronisierte Override-Bedienung (50 %)
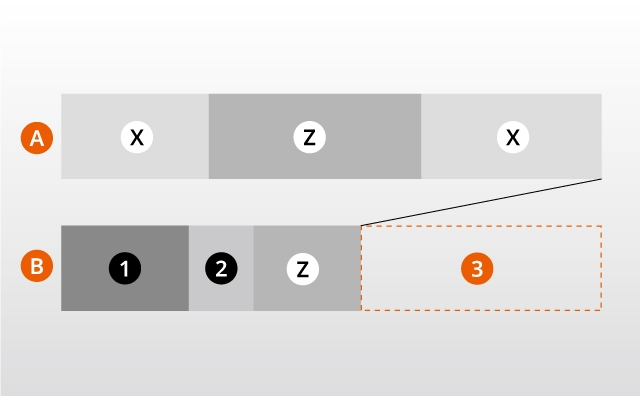
A: Revolver A
B: Revolver B
1: Verweilzeit (Standby-Zeit) Keine Zeitänderung
2: Unterstützende Funktionen
3: aufgetretene Programmabweichung
Manuelle Betätigung des Handrads
Das Bearbeitungsprogramm kann bei jeder Geschwindigkeit durch Drehen des Handrads der CNC-Steuerung von Hand bedient werden. Die Annäherungspositionen sowie potenzielle Kollisionen oder Beeinträchtigungen lassen sich präzise überprüfen.
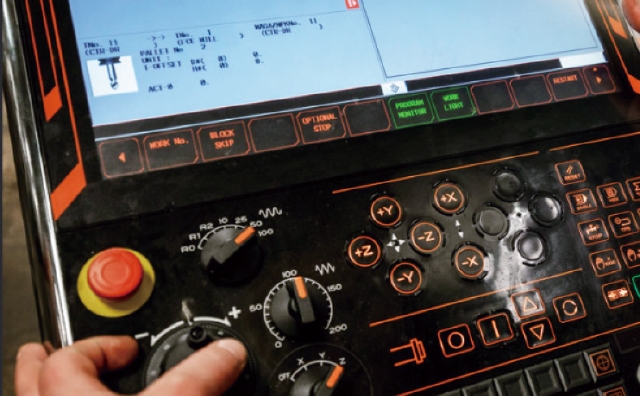
HQR-200/3 NEO
HQR-250/3 NEO
Spindelbohrung | Ø91 mm |
Spannfuttergröße | 10″ |
Max. Bearbeitungsdurchmesser | Ø320 mm |
Max. Bearbeitungslänge | 860 mm |