Pallet size | Φ600 mm × 500 mm |
Tool shank (standard) | BT40 |
Max. spindle speed | 12000 min-1 (rpm) |
Max. workpiece size | Φ700 mm × 450 mm |
5-axis Machining Centers
VARIAXIS i NEO
- High productivity and environmental performance
- High-rigidity full gantry construction ensures stable machining accuracy
- Wide variety of available automation equipment, including a modular PALLETECH flexible manufacturing system, MPP (MULTI PALLET POOL), 2-pallet changer
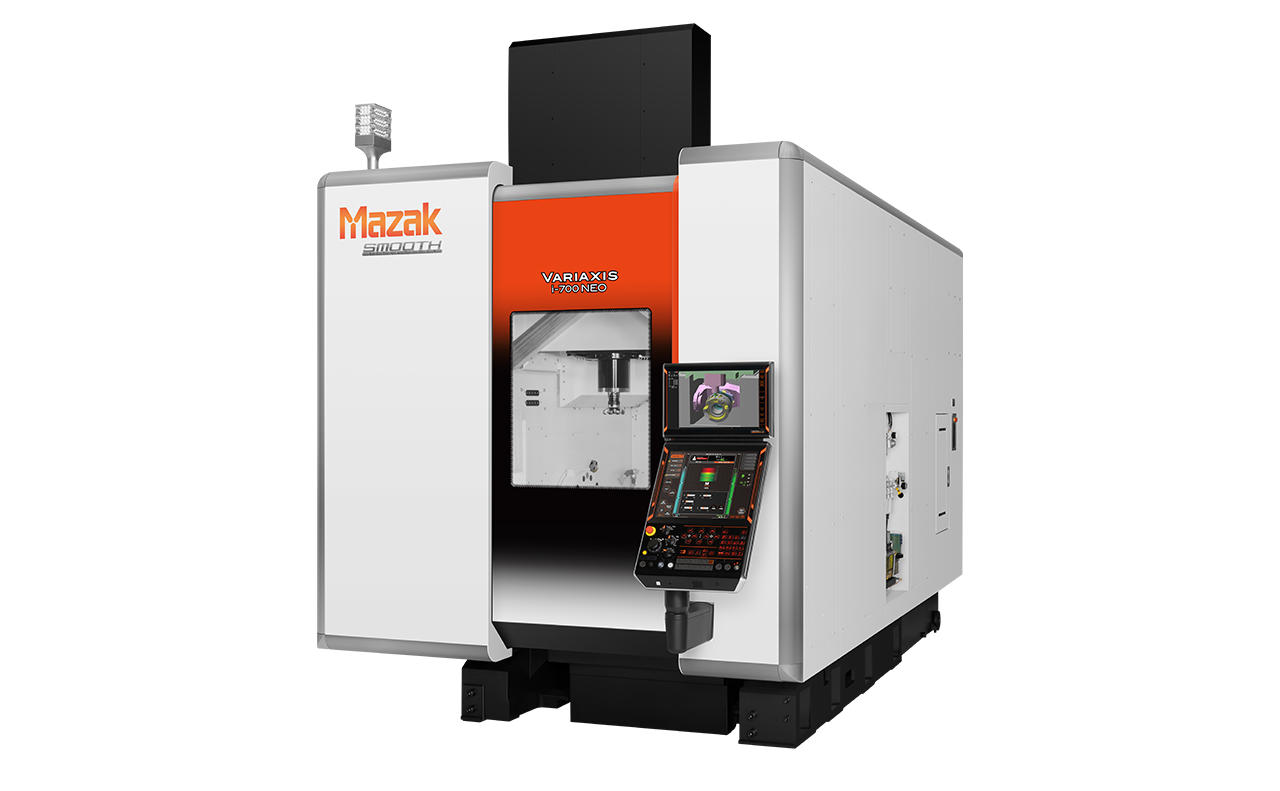
Wide variety of spindle selection and automation options to enable highly productive 5-axis machining
- Spindle specifications to meet a wide variety of machining requirements
- Enhanced cooling system of the rotary axes for sustained machining accuracy.
- Wide variety of available automation equipment, including a modular PALLETECH flexible manufacturing system, MPP (MULTI PALLET POOL), 2-pallet changer
- Compact multiple drum tree magazine with large storage capacity is optionally available
- Improved environmental performance with energy-saving equipment
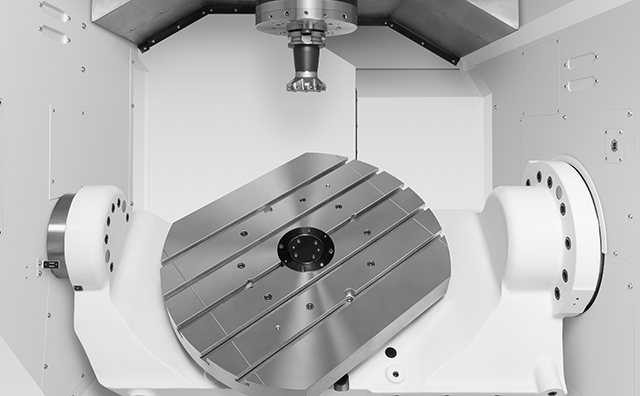
Spindle specifications to meet a wide variety of machining requirements
Spindles selectable according to material properties
The highly rigid spindle can perform heavy duty machining of steel as well as high speed machining of non-ferrous materials such as aluminum. High-speed and high-torque options are available.
Smooth Ai spindle*
The VARIAXIS i NEO series use AI to detect milling spindle vibration and adjust machining conditions automatically to produce unsurpassed surface finishes and high productivity. With the AI, even a less-skilled operator can make adjustments easily in a short time.
* Option
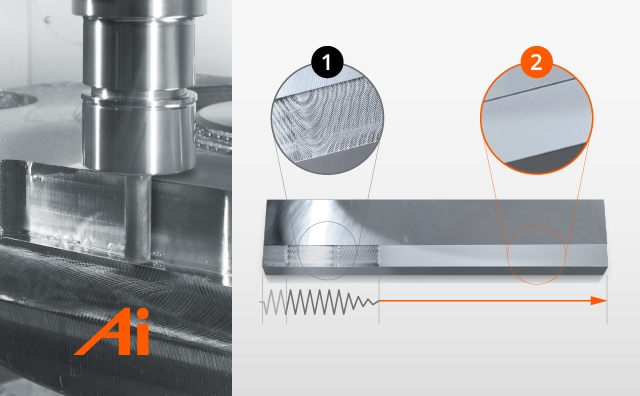
Various automated systems to improve productivity
Preparation for hydraulic fixtures*
Setup can optionally be supported with hydraulic fixtures that can enable clamping / unclamping of the workpiece. The number of ports can be up to 9 ports for the single table version, 4 ports inside the machine and 8 ports on the workpiece setup station for the 2-pallet changer version. Pneumatic fixtures are also available.
* Option
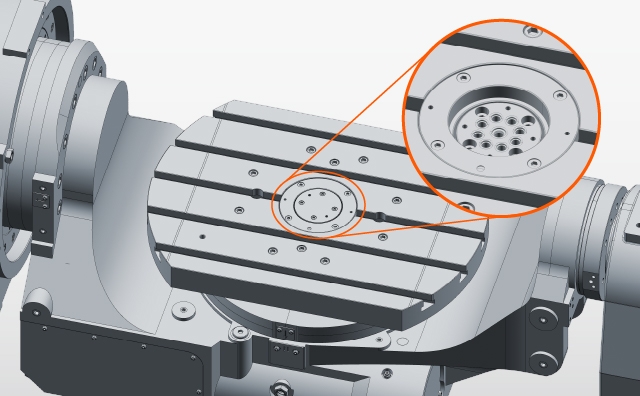
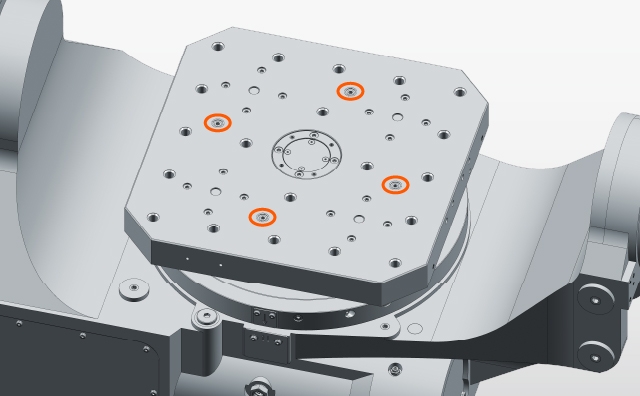
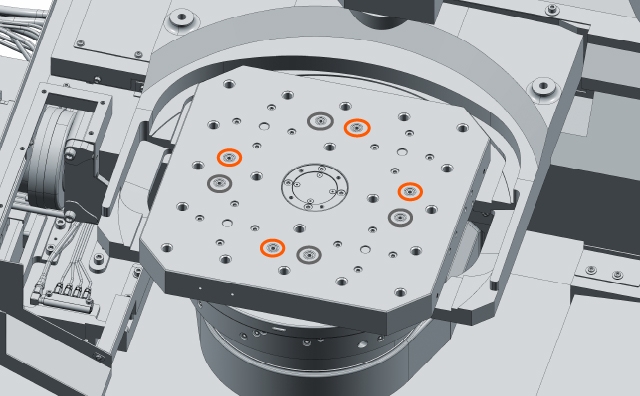
2-pallet changer*
The pallet changer option provides rapid changeover of workpieces for continuous machining operation. To achieve higher productivity, the next workpiece can be set up while the current operation is being machined. The 2-pallet changer offers a compact design and is suitable for mass production. Reduced length to pull out the rear conveyor saves space in the maintenance area.
* Option
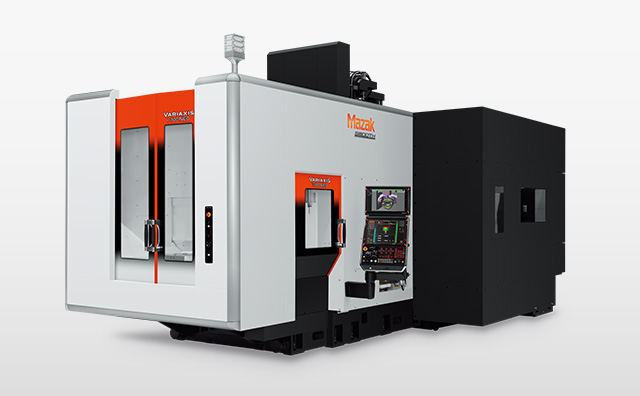
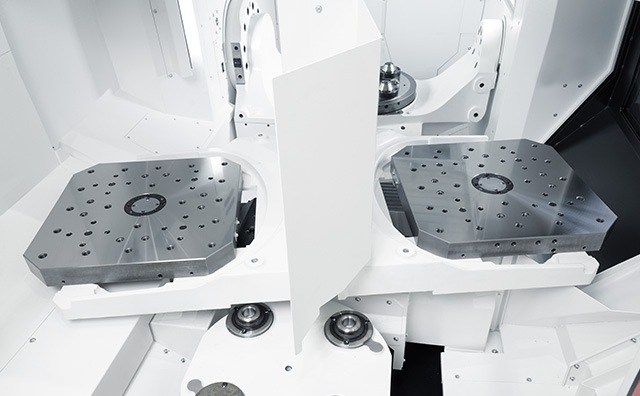
Tool magazine
The standard tool magazine accommodates 30 tools, with 40, 80 and 120-tool options available. This generous capacity provides ample storage for complex workpieces and high-mix production, as well as spare tools for prolonged continuous operations.
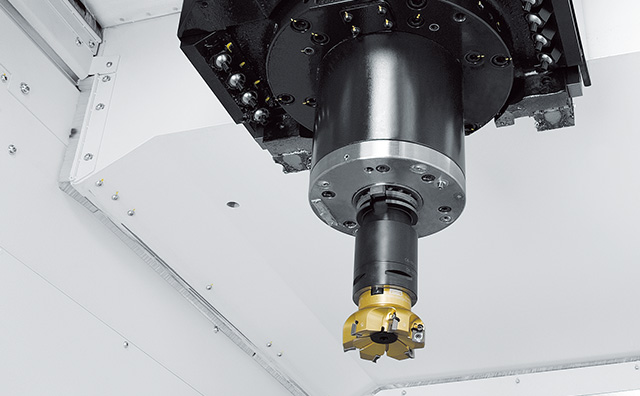

Multiple drum tool magazine*
The compact tool magazine capacity meets the requirements for small-lot machining of a wide variety of workpieces. Tools load automatically from the multiple-drum tool magazine to the magazine next to the machine. The new shifter mechanism reduces tool waiting time and improves productivity by positioning the tool to be used after the next one. The tool magazine size can be selected based on your production requirements. Optional equipment can be added after machine installation. Tools up to 350 mm (or 360 mm for some tools) in length can be mounted.
*Option
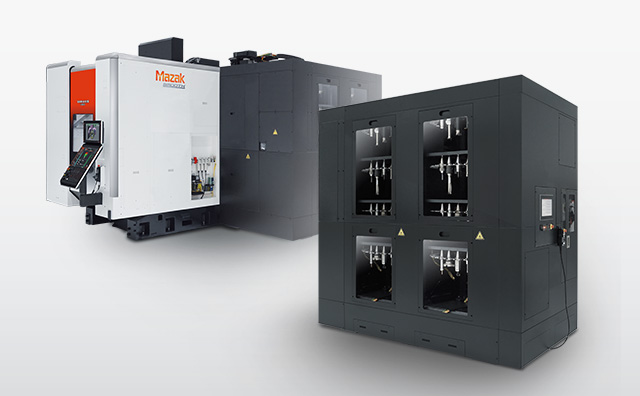
Improved environmental performance with energy-saving equipment
Energy Saver
Energy consumption and the regenerative power produced through the energy saving equipment can be viewed visually on the CNC system to stimulate awareness of energy conservation. In addition, the system can control coolant and other equipment based on the cutting amount to reduce power consumption.
* An optional Smooth coolant system is required for the control of coolant and other equipment.
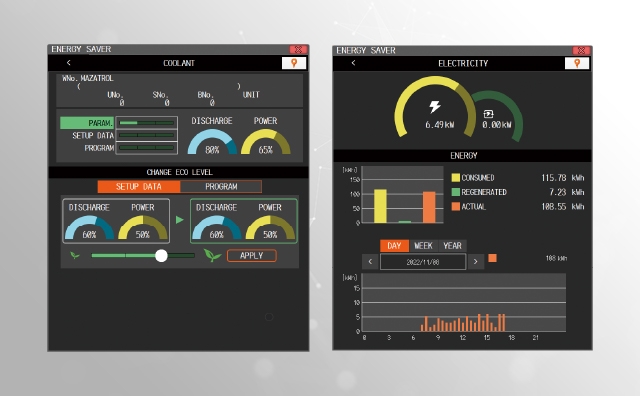
Environmentally friendly Smooth coolant system*
Optimal control of coolant discharge amount
Energy saver automatically determines the optimal coolant discharge for energy-saving machining. Processing with reduced power consumption is possible at all times.
- VARIAXIS i-800 NEO is not supported
*Option
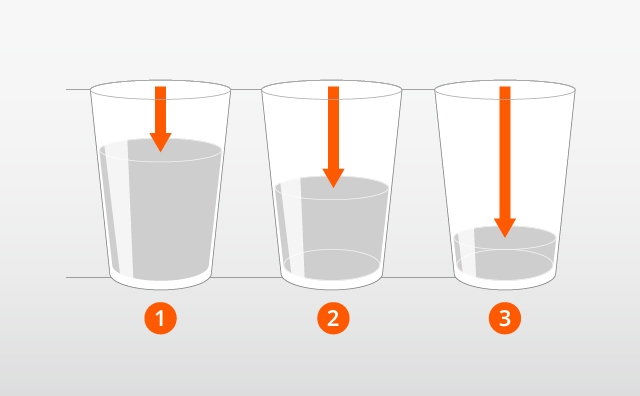
Energy-saving coolant system with sludge removal performance
No need to frequently clean the tank
The coolant tank has a coolant jet that makes a vortex in the center so that small machined chips will not settle in the tank. This feature makes it possible to keep the coolant tank clean and extend the service life of the coolant. Ease of maintenance is also ensured. The frequency of coolant changes is reduced as well as CO2 emissions at coolant disposal.
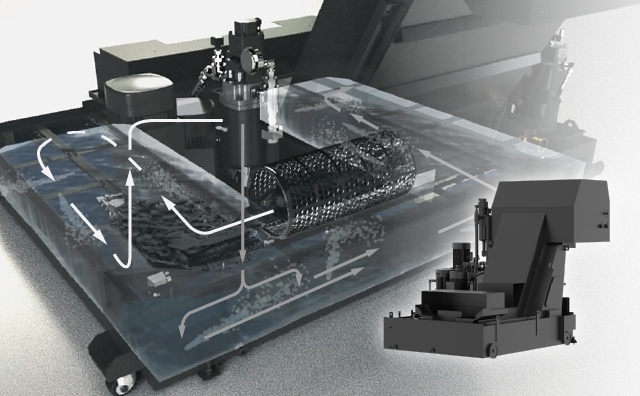