Chuck size | 8″ |
Max. machining diameter | Φ320 mm |
Max. machining length | 180 mm |
CNC Turning Centers
MULTIPLEX W
- Equipped with a symmetrical spindle and turret for high productivity
- Automatic workpiece transfer enables two-step continuous machining by both spindles
- Capable of multiple processing methods; turning, drilling, contour milling, and Y-axis machining.
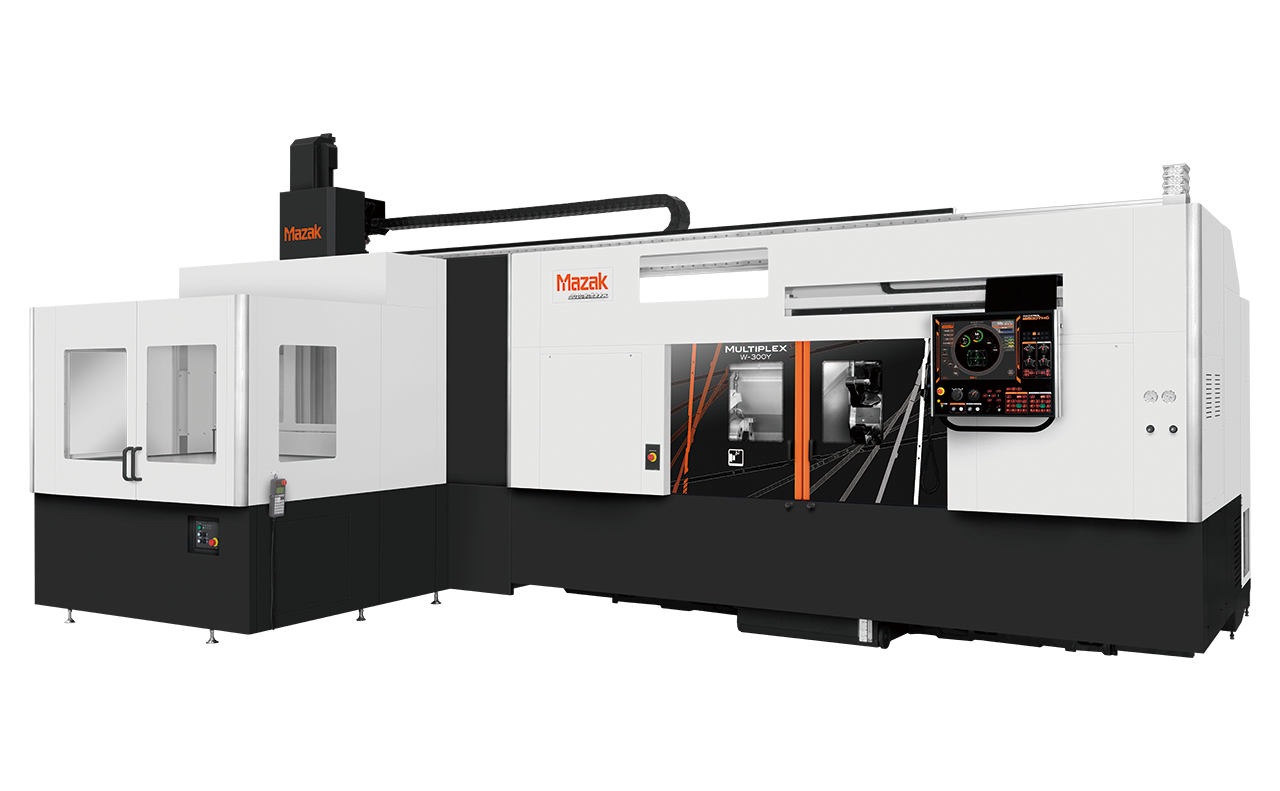
Symmetrical structure for productivity
Symmetrical spindle and turret
The two-step continuous machining using both spindles/turrets greatly improves productivity. Its capacity to handle 2 different workpieces separately, and machine long shaft workpieces by synchronizing the left/right spindle and Z-axis, makes it possible to work on a variety of applications.
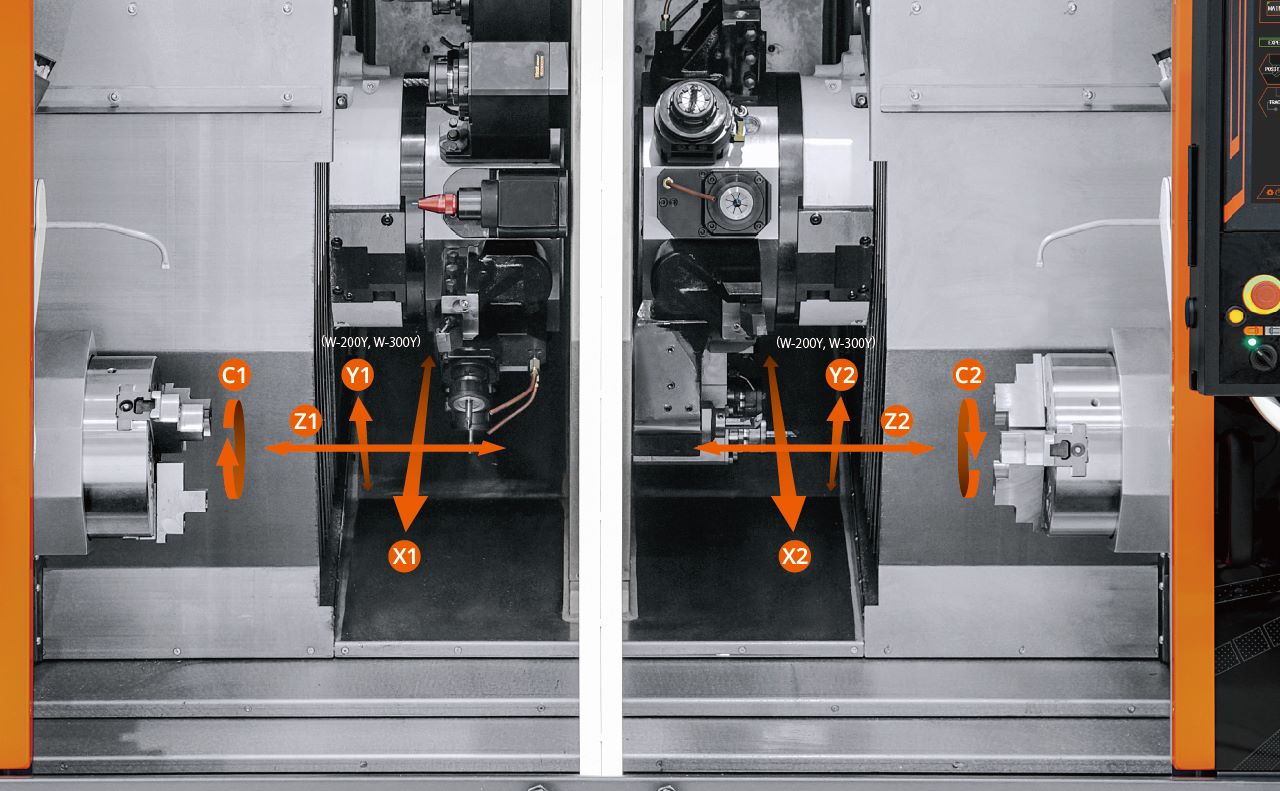
MULTIPLEX Processing for Higher Productivity
The MULTIPLEX W series is capable of continuous machining from the first process to the second process on the same machine, which ensures high phase accuracy even if workpieces are transferred between spindles. It can handle all of the processing required until the completion of the product, leading to multiple benefits such as reduced production lead time, improved machining accuracy, reduced floor space and initial cost, lower operating expenses, reduced operator requirements, and a more improved working environment.
Various machining methods for higher productivity
Y-axis ideal for multi-tasking (W-200Y, W-300Y)
Large Y-axis stroke for a wide variety of cutting, such as milling flats and drilling off-center.
Y-axis stroke:
W-200Y 100 mm (±50 mm)
W-300Y 154 mm (±77 mm)
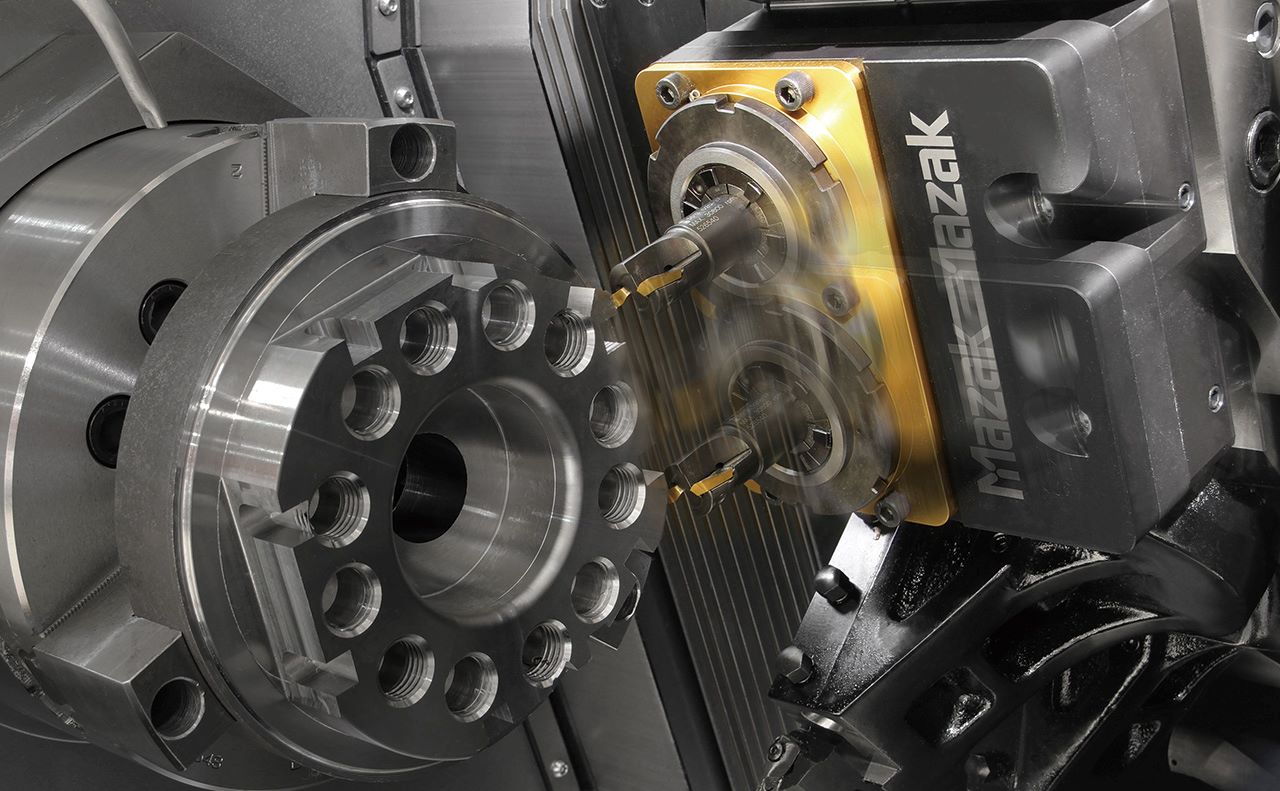
Continuous machining with automatic workpiece transfer
High-speed, high-accuracy automatic transfer function can make highly efficient OP1 and OP2 continuous machining with a single chucking operation possible.

Automatic partition for independent machining in both areas
Complete separation of the machining area prevents chips and coolant from scattering from the other side. This makes it possible to machine the left and right side separately, or to replace one workpiece while the other is being machined.
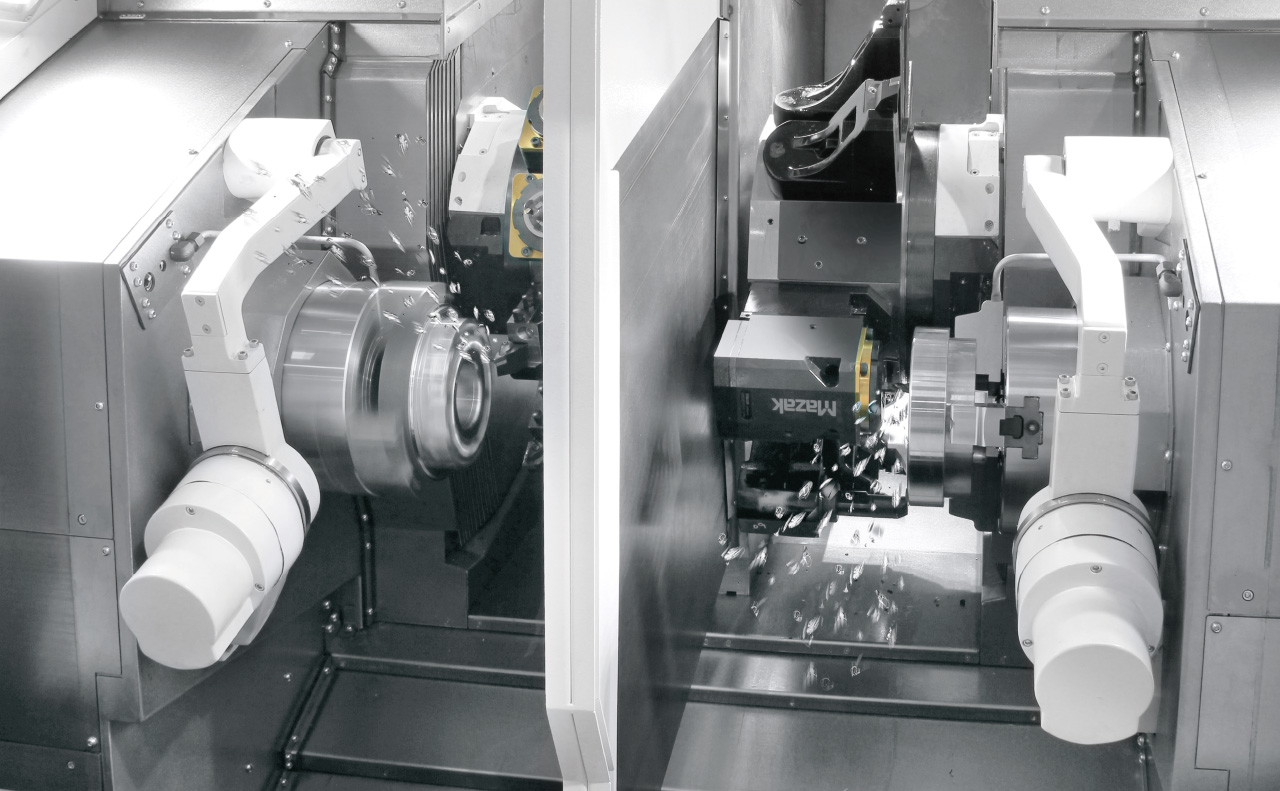
Automation options for even higher productivity
Automatic unload system
The basic system is equipped with a workpiece unloading device, which can unload the finished product workpiece to the workpiece stand, simply by attaching the material to the chuck of the main spindle.
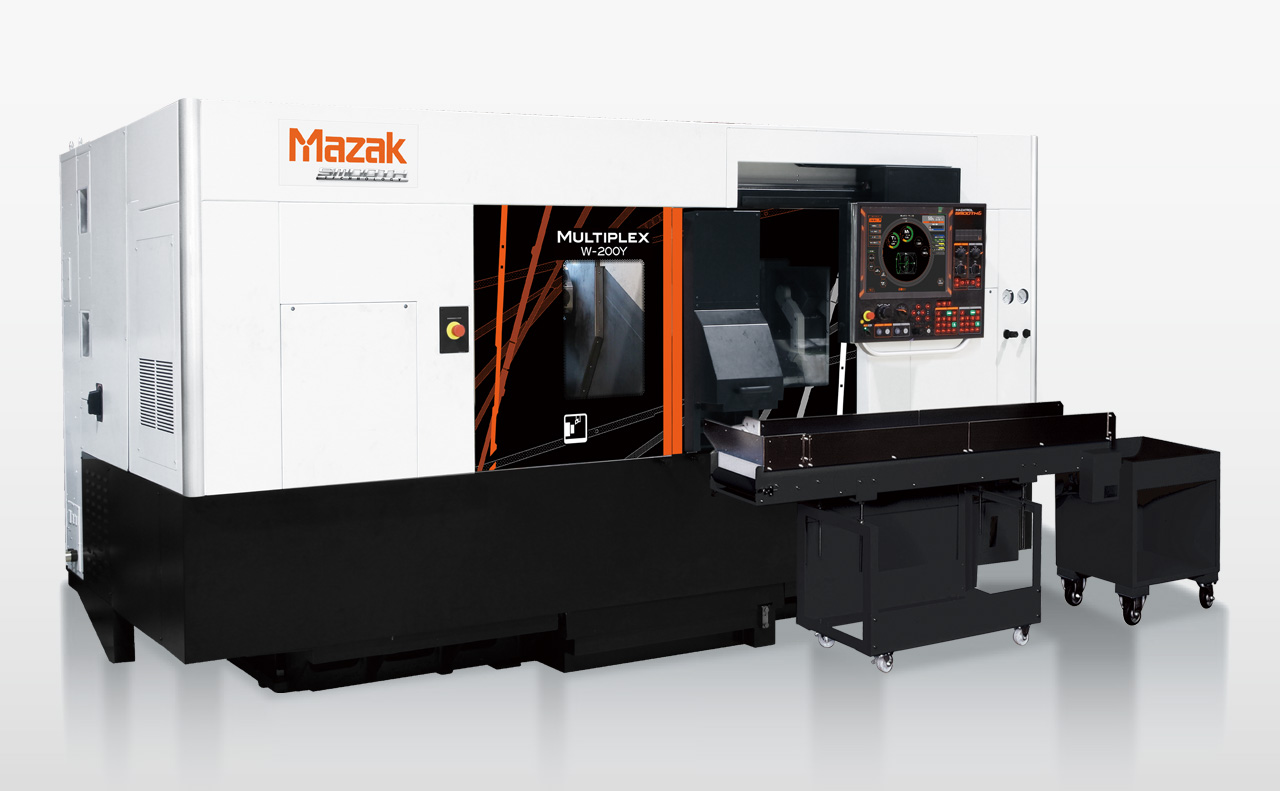
Gantry Loader system
The gantry loader system ensures high-speed automatic transfer of workpieces. Compared to previous models, the gantry loader operating speed is increased by 20% with simultaneous operation of the A- and B-axis and faster traveling speed.
It is also possible to connect multiple units or retrofit machines that have already been delivered.
Ease of programming
The CNC system MAZATROL SmoothG, which supports both EIA/ISO program and MAZATROL conversational program, is installed as a standard system.
QUICK MAZATROL
You can create programs while checking the machining shape and processes on the CNC screen to prevent programming errors and reduce programming time.
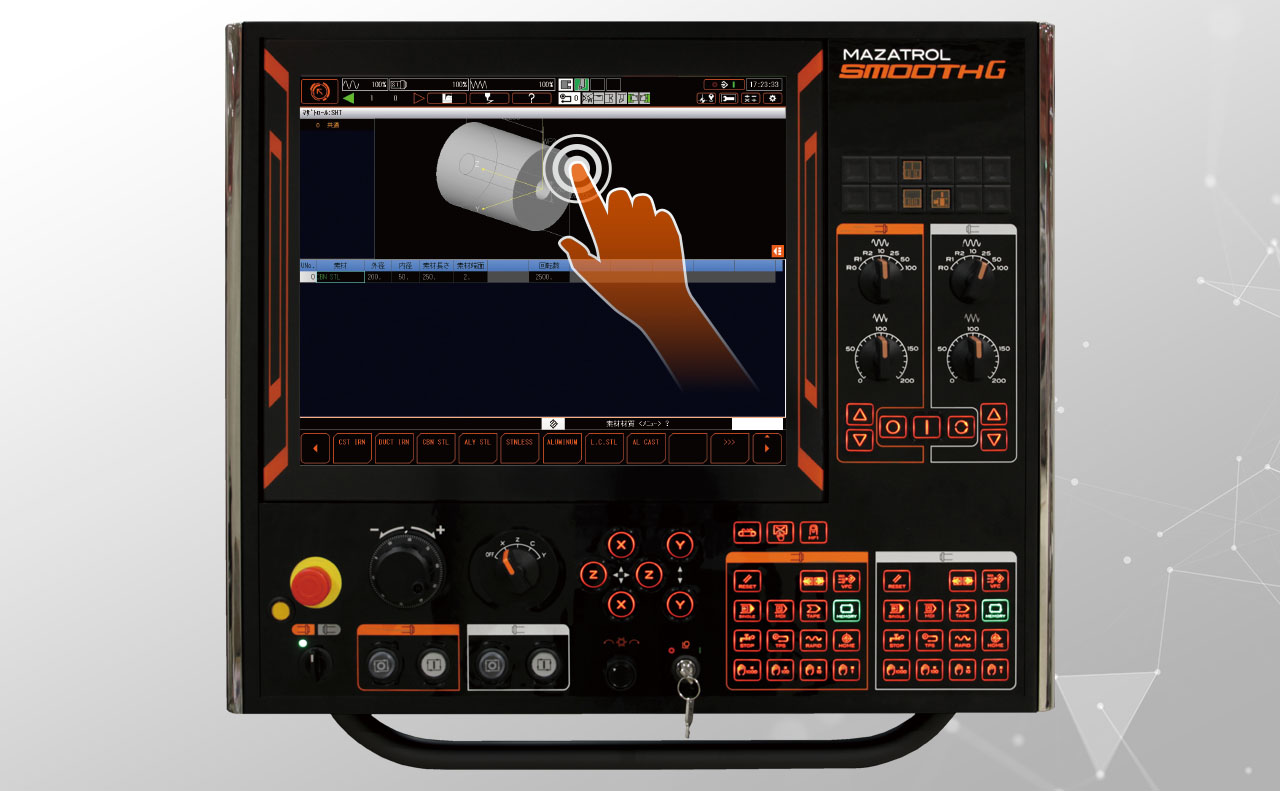
3D ASSIST
Workpiece and coordinates data can be imported from 3D CAD data to a MAZATROL program. No coordinate value inputs are required and input errors and time for program checking can be reduced.
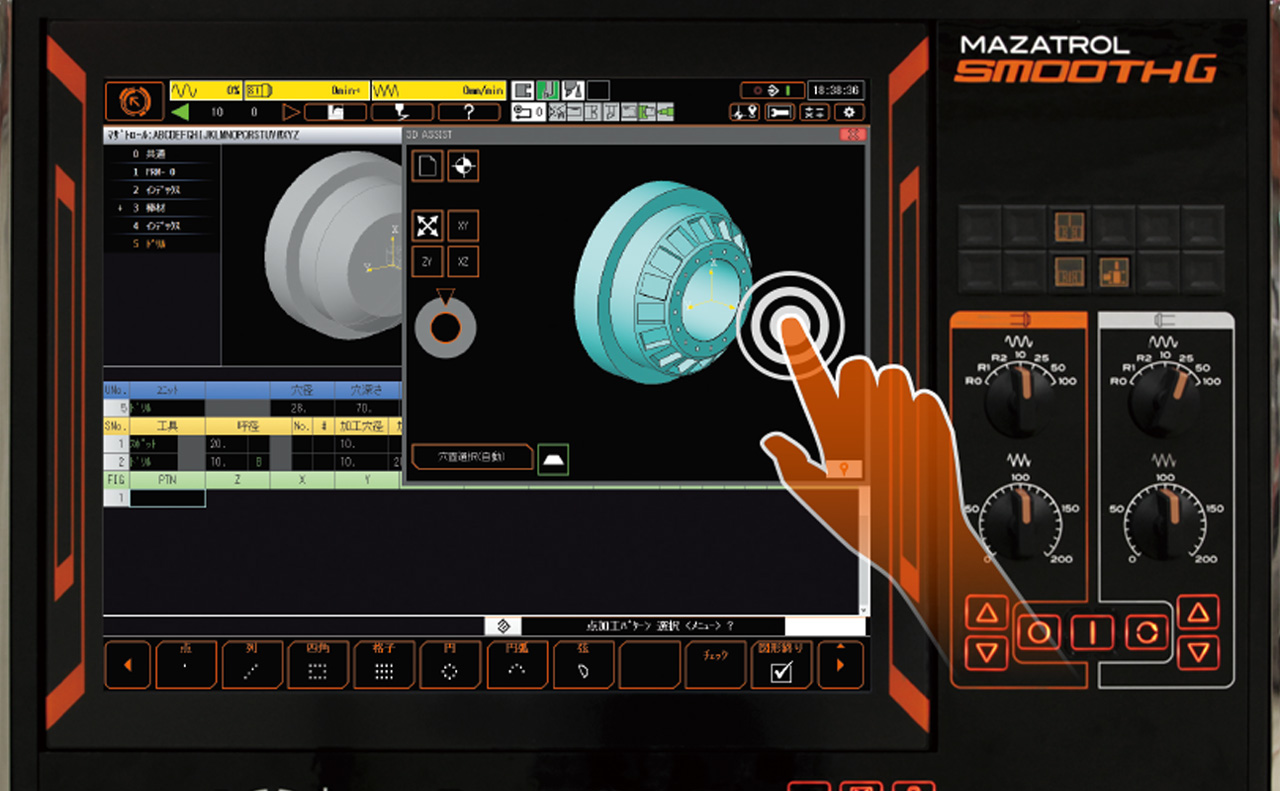
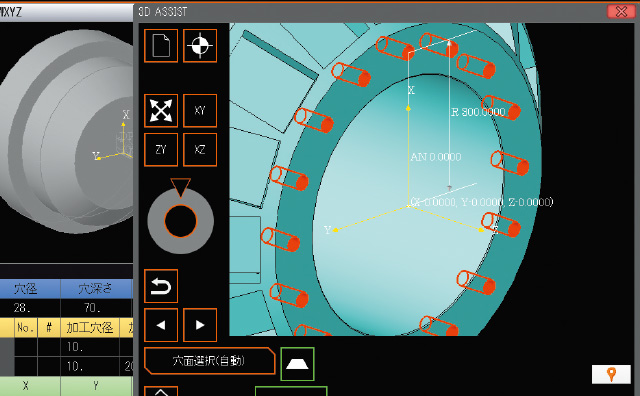
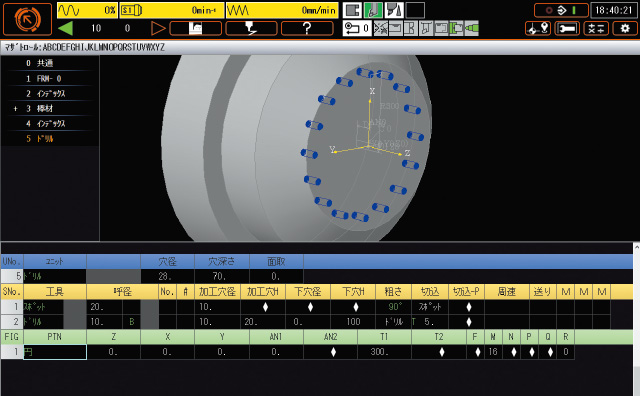