Pallet size | 500 mm × 500 mm |
Tool shank (standard) | CAT No.40 |
Max. spindle speed | 12000 min-1 (rpm) |
Max. workpiece size | Φ720 mm × 870 mm |
Horizontal Machining Centers
FF
- High cutting capacity and fast operation for high productivity
- Machine structure that facilitates the construction of a mass production parts machining lines
- Space-saving design for mass production parts machining
- High reliability and maintainability
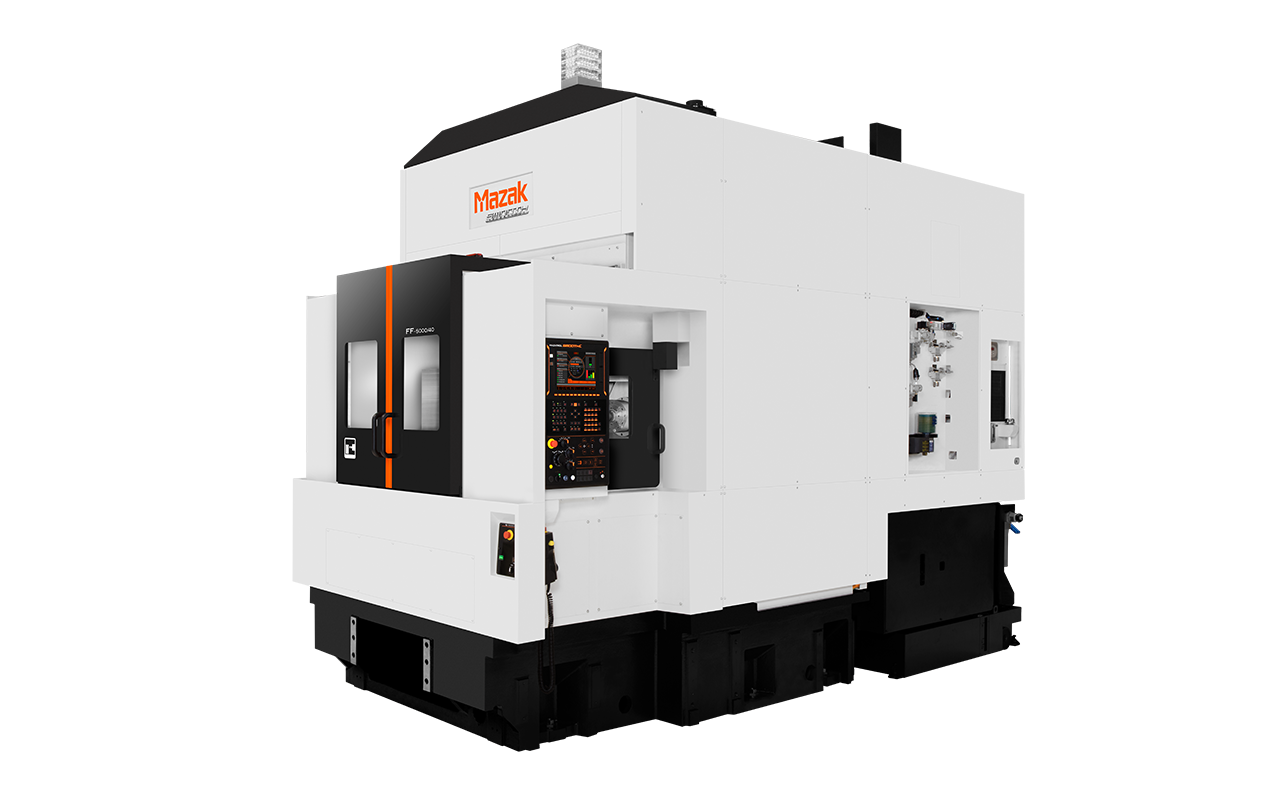
Exceptional cutting ability for machining a wide variety of materials
Suitable for machining a wide variety of materials
The rigid machine structure allows machining of not only aluminum, but also iron and cast iron.
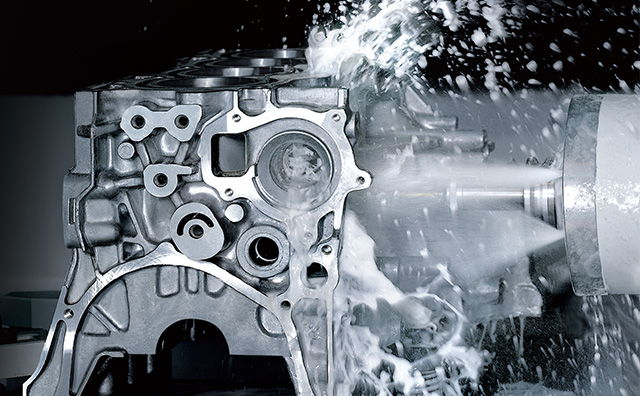
Built-in Motor Spindle
A built-in motor is adopted for the main spindle. The synergistic effect of a spindle that generates sufficient torque and a rigid mechanical structure provides excellent cutting performance.
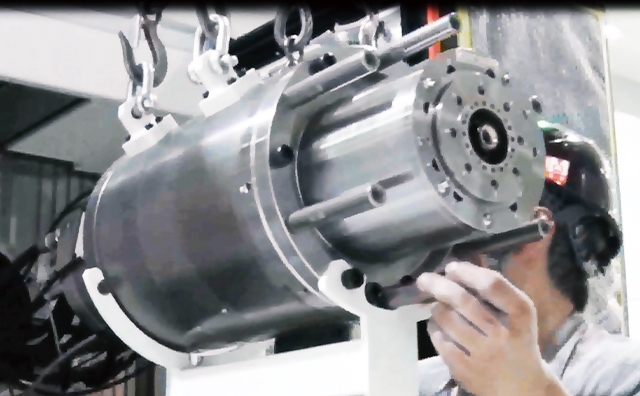
Actual cutting capacity
Φ80 mm face mill | Φ20 mm carbide luffing end mill | Φ100 mm face mill | |
---|---|---|---|
Truncation | 2503 mL/min | 720 mL/min | 268 mL/min |
Cutting depth / width | 5.5 mm / 65 mm | 20 mm / 3 mm | 3.5 mm / 80 mm |
Workpiece materials | A5052 | FC300 | S45C |
Spindle speed | 5000 min-1 | 9995 min-1 | 637 min-1 |
Rapid traverse rate | 7000 mm/min | 12000 mm/min | 956 mm/min |
Reduced non-cutting time thanks to high speed operation
High speed acceleration/deceleration spindle
This machine is equipped with a built-in motor spindle. Power loss is minimized and high-speed acceleration/deceleration is realized since drive gears are not used.
Spindle acceleration
1.4 sec (0→12000 min-1)
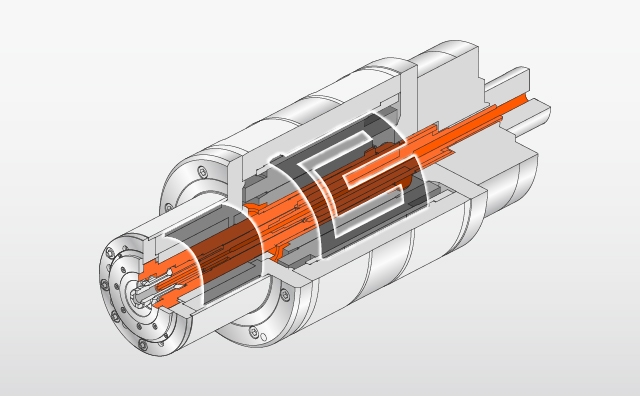
High-speed, high-acceleration/deceleration feed Z-axis (Ram structure)
The Z-axis, with high speed and high acceleration/deceleration, improves productivity in drilling operations such as tapping and drilling.
Rapid traverse rate
62 m/min
Acceleration
1.5G(FF-n5000/40、FF-5000/40)
1.2G (FF-5000/50)
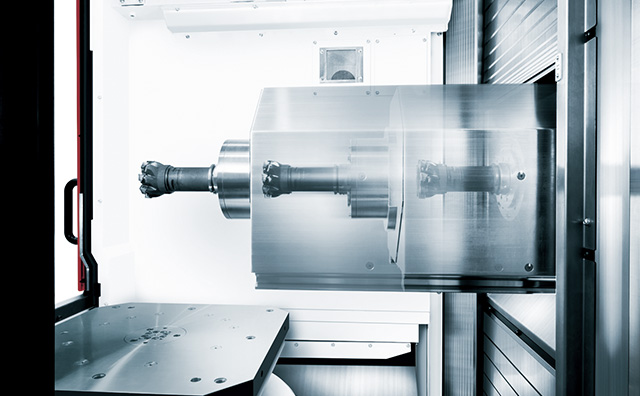
High Speed NC Table
The NC table is driven by a roller gear cam to achieve high-speed rotation and positioning.
Max. speed: 50 min-1
High-speed positioning: 1.5 sec/90 degrees
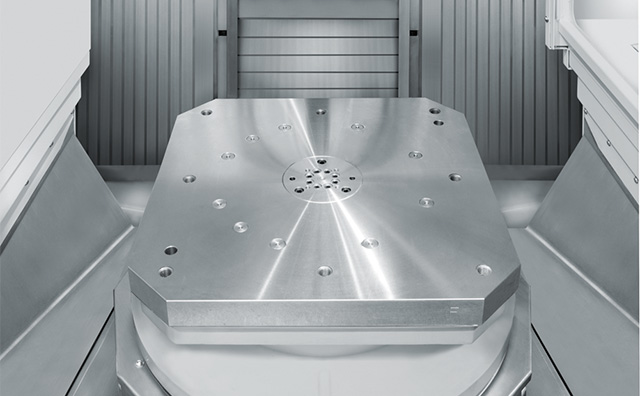
Space-saving and easy to build automated lines
Distance between machines 650 mm
Space saving is realized by the compact yet highly rigid structure and the placement of the magazine on top of the machine.
- Increased productivity per unit area
- Easy to build a line for mass production parts machining
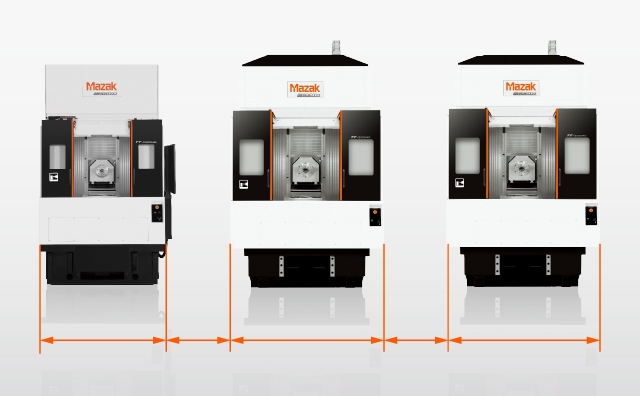
Various specifications and automations to suit your production system
Select the best table for your needs.
Three types are available for machining with optimum workpiece positioning: B-axis table specification, A-axis table specification (optional), and A-axis/B-axis table specification (optional).
B-axis table | A-axis table (optional) | A-axis/B axis table (optional) | |
---|---|---|---|
Table Specifications | ![]() | ![]() | ![]() |
Rapid traverse rate | 50 min-1 | 16 min-1 | 50 min-1 |
Table indexing time (90°) | 1.5 sec | 2.0 sec | A-axis: 1.6 seconds / B-axis: 1.5 seconds |
Building the Optimal Automation Line
This is a dedicated production line for automotive parts with 18 units of FF-5000/40 and 3 double arm gantry loaders.
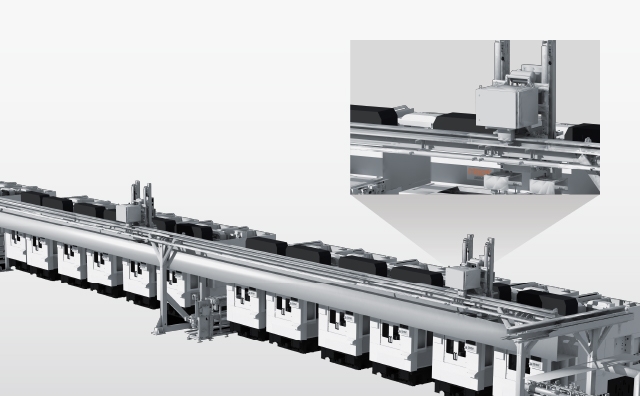
Automated line with loader robot
Automated production line with 20 units of FF-5000/40 and 5 articulated robots.
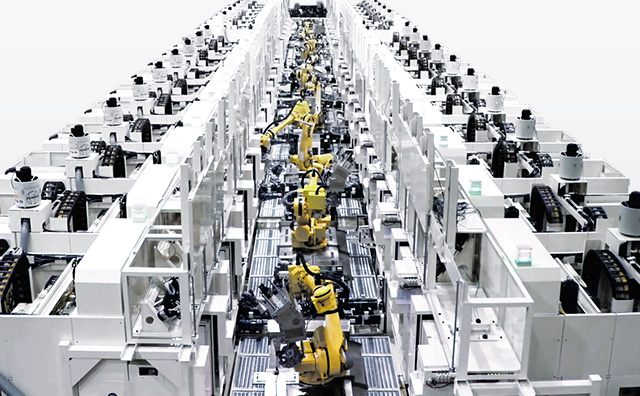
Machine configuration for high reliability and maintainability
X-, Y-, Z-axis drive
The machine configuration with fixed table allows the X-, Y- and Z-axis drive to be located outside the cutting area. High reliability is achieved by reducing susceptibility to chips and cutting water.
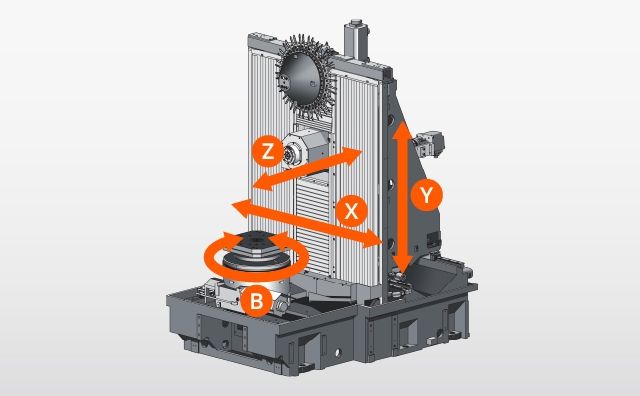
X-, Y-axis way cover
Accordion-type way covers provide high reliability and high durability for high speed operation.
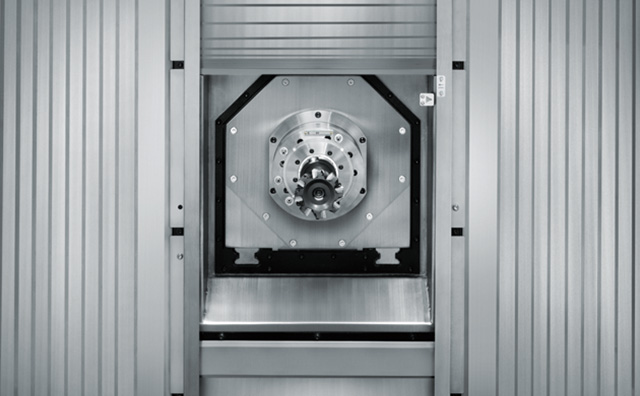
Spindle tool clamp
4,000,000 times long life disc spring
Excellent durability disc spring is adopted in the spindle tool clamping section. It enables stable parts machining even in mass-production parts machining where tool changeover frequency is extremely high.
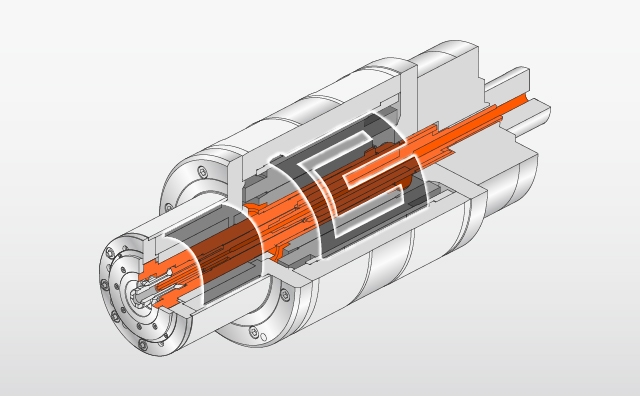
Direct ATC
The simple structure without an ATC unit or shifter unit provides high reliability for tool change.
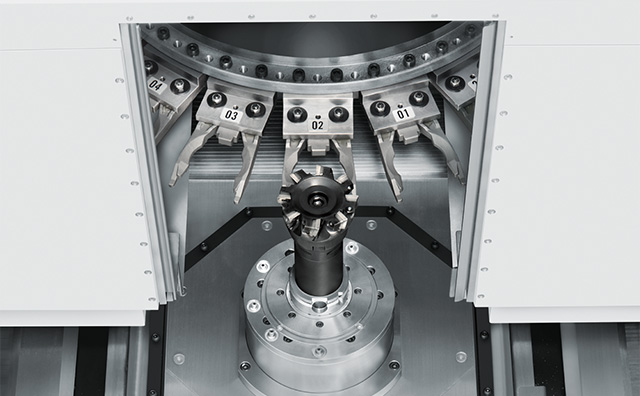
Oil controllers, hydraulic pressure units, air equipment
The system is centrally located in an easily accessible location to facilitate inspections.
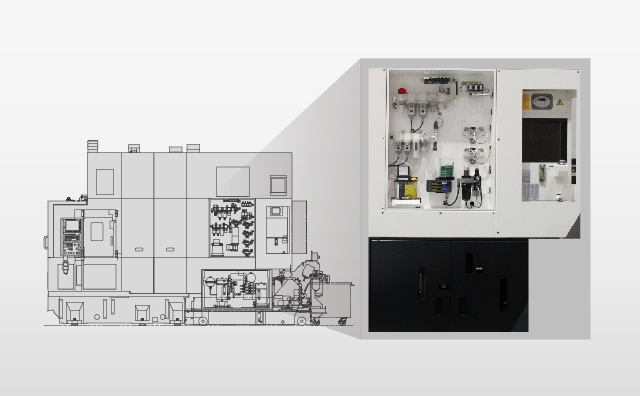