Engine Shop Goes Full Throttle with Five-Axis Machining
Deep in the heart of Texas (Weatherford to be exact), Frankenstein Engine Dynamics (FED) manufactures some of the best custom engine parts used in the professional auto racing industry. The company has an excellent reputation for what it does, and its components are well-known for their quality, impressive designs, and outstanding performance. From the time FED opened its doors in 2005, the company’s products have met the racer’s need for speed. By 2015, FED cylinder heads, intake manifolds, and engine kits were in such high demand that the company desperately needed to rev up operations and expand, or lose out on a great growth opportunity.
In 2016, after conducting diligent research and taking on several partners, FED’s owner and CEO, Chris Frank decided to build a new 20,000 ft2 (1858 m2) facility, hire a talented team and incorporate advanced full five-axis machine tool technology that would accelerate production speeds without sacrificing part quality. These smart investments have paid off, and the company is on track for record growth as revenues consistently increase each quarter.
FED first gained a name for itself in the top range of the racing industry, creating cylinder heads for top-fuel dragsters going to NASCAR clients. It didn’t take long for drivers and crew members to notice that FED’s products exhibited outstanding craftsmanship and provided superior performance. From the beginning, Frank’s goal has always been to build engine parts that outperform and outlast anything else out there. He began with a very high level of racing clients with much faster cars and more money to invest in extremely expensive components.
“These customers expect performance and durability, and when they get it, word spreads quickly, but you have to get it right the first time because there is no second chance,” Frank said. There are a lot of different avenues of racing with many different areas to get involved in. The area FED chose to focus on is one of the most challenging—the cylinder head, which Frank calls the heart of the engine. “It’s extremely complex; it’s detail-oriented and in the end, that’s where the magic happens,” he said.
With FED’s expansion, the company now serves two types of clients and plans to expand its product lines to accommodate its new, broader range of customers. On one side, the company has what it considers professional racers—the clients who earn a living doing it. On the other, it has street enthusiasts—owners of cars like Corvettes or Camaros who just want to make their cars run faster and louder and give them what Frank calls a “cool factor.” The company has started development of a large product line for both types of clients. With its recent investment in new machining technologies, specifically those from Mazak Corp. (Florence, KY), the company is able to design and produce all its new products in-house. “Almost all of our clients prefer in-house components over shops that buy other people’s products and modify them,” said Frank.
Currently, FED has two Mazak Variaxis i-700 vertical machining centers with Mazatrol SmoothX Control and full simultaneous five-axis machining capabilities. The machines are equipped with 18,000-rpm spindles with compact nose designs for maximum Z-height part clearance, tilt/rotary tables, and automatic tool changers with storage capacities for up to 80 tools. The machines not only help FED machine parts faster, but also boost part processing flexibility and control. The machine’s table tilts in the A axis −120° to +30° and rotates in the C axis ±360°.
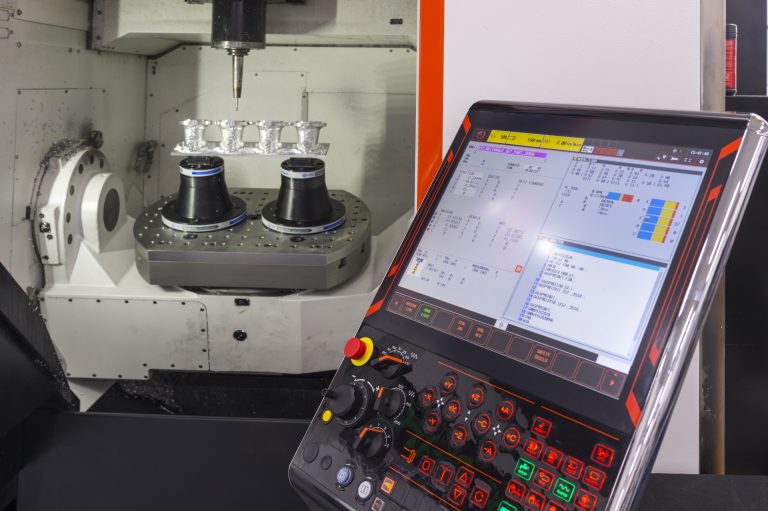
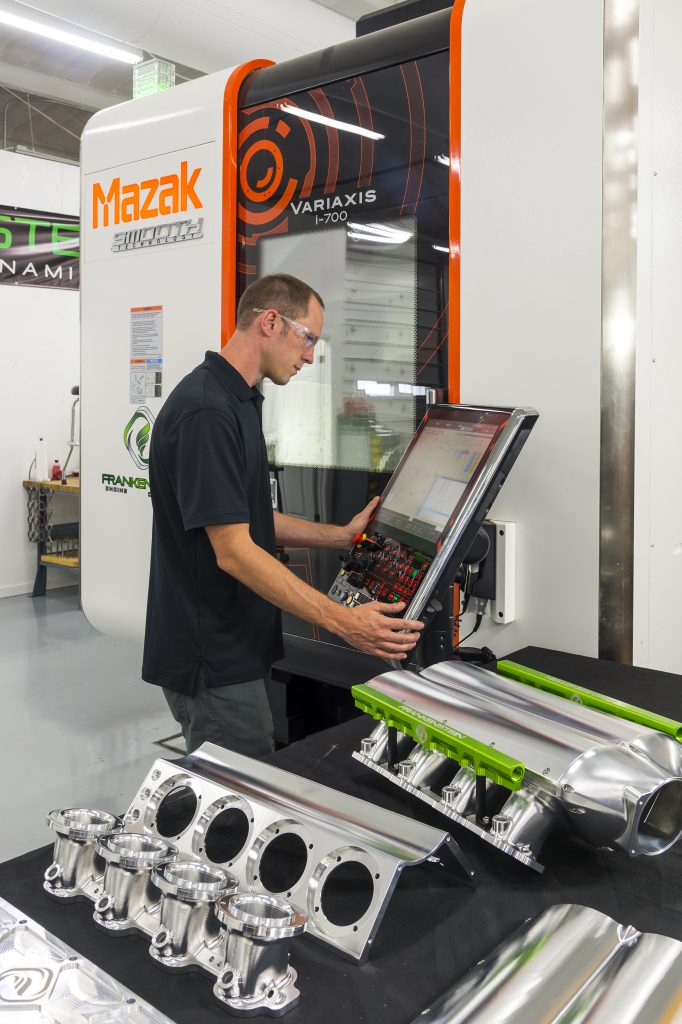
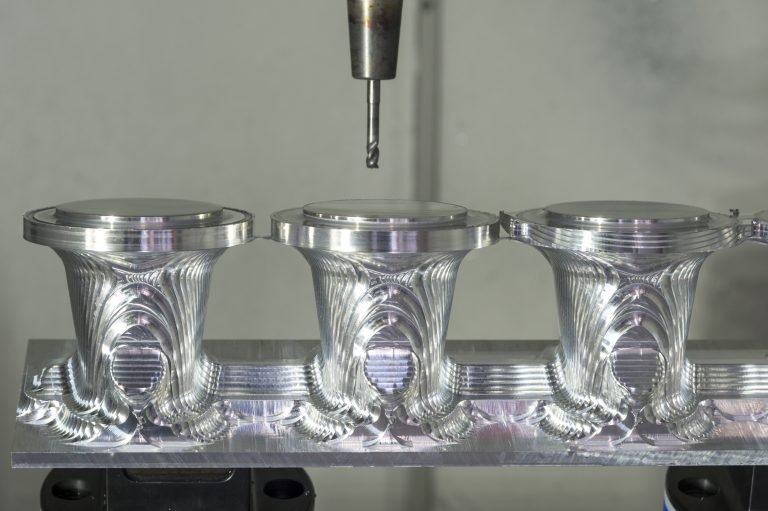
The machines FED chose to purchase not only allow the company to create components three times faster, but also one hundred times more accurately. “The process is extremely repeatable, and the software and interface have been phenomenal for us,” said Frank. FED is gearing up for much larger production runs. Frank said that before they purchased the Mazak machines, they were only able to do ten units every so often. With the Mazaks on board, the company can now do 300 units and sell them for half the price.
“The quality and value are the same, if not better, and because we’re able to do it faster, we can pass along that value to more customers,” said Frank. “Now that our new facility is up and running, we’re able to offer our products to the masses. Mazak is the sole reason for that.” FED plans to machine a variety of custom accessories and components to go along with its intake manifolds, such as valve spring retainers, billet products and anything else that shows promise in the development stage.
“We start with a solid block of heat-treated 6061-T651 aluminum. It’s a huge chunk. We can design anything that we can think of in CAD, program it, toolpath it and produce it on our Mazaks,” explained Frank. Jesse Meagher, FED’s lead CAD/CAM engineer and new product development lead, echoed Frank’s sentiments and also pointed out that there are many benefits to using the Mazak Variaxis i-700 machines over others. “Since the machine has a high-torque/high-horsepower spindle, such cuts don’t bog down the machine or damage it,” said Meagher. “We tried to do the same thing with older machines, and it just wasn’t possible.”
FED also relies heavily on the machines’ tool point center control, high-pressure coolant-through spindles and most of all their rigidity. “The machines are extremely stable, robust, and built to hold close tolerances. Compared to what we had, it’s night and day,” said Meagher.
Frank said that the company now runs a shift and a half while they finish infrastructure, but in the near future it will run two full shifts and also a lights-out shift. If all goes as planned, FED has its sights set on more Mazak Variaxis i-700s, as well as other Mazak model machines. Most of these machines will be used to service high-end racing clients. The demand is there, but even if the company goes into other avenues, all the machines will be used for racing at one time, and other jobs will be scheduled according to priorities.
Every component FED makes is built with safety in mind first. “Inferior products can cause a failure and lose a big race. Even worse, if something leaks and gets on the racetrack, it can cause another driver to crash,” said Frank. “With our Mazaks, we have confidence that everything we create is both safe and of the utmost quality and durability. It’s what our customers need and it’s the only way we want to do business.”
The biggest challenge FED faces for the future is to continue to build inventory and reduce setup times to get new products developed fast while still maintaining the highest quality. The company is considering robotics to load the machines so they can run more lights-out. “We are already working with Mazak on the best, most efficient options to add to our infrastructure,” added Frank. “Load times are crucial to getting where we want to be, and we trust the Mazak team to help us get there without sacrificing the high standards for which we’ve come to be known.”
Frank said that from the moment his relationship with Mazak began, he knew it was the right fit. “Everyone we dealt with at Mazak was extremely confident in their product and willing to stand behind it. There was never a moment that they said ‘we can’t do that,’” he said. “We expressed our goals and concerns, and they had no problem fulfilling our every need.”