Spannfuttergröße | 8″ |
Max. Bearbeitungsdurchmesser | Φ320 |
Max. Bearbeitungslänge | 150 mm |
CNC-Drehzentren
DUAL TURN 200
- Symmetrischer Aufbau mit 2 Spindeln / 2 Revolvern
- Gleichzeitige Bearbeitung auf beiden Spindeln und automatischer Transfer von der ersten zur zweiten Spindel ermöglichen eine kontinuierliche Bearbeitung
- 30% Platzersparnis im Vergleich zu zwei 2-Achsen-CNC-Drehzentren der gleichen Klasse
- Berücksichtigt man den toten Raum zwischen den Maschinen, das Arbeitslager, die Wartungsbereiche und die Späneförderer, wird der Platzunterschied noch größer
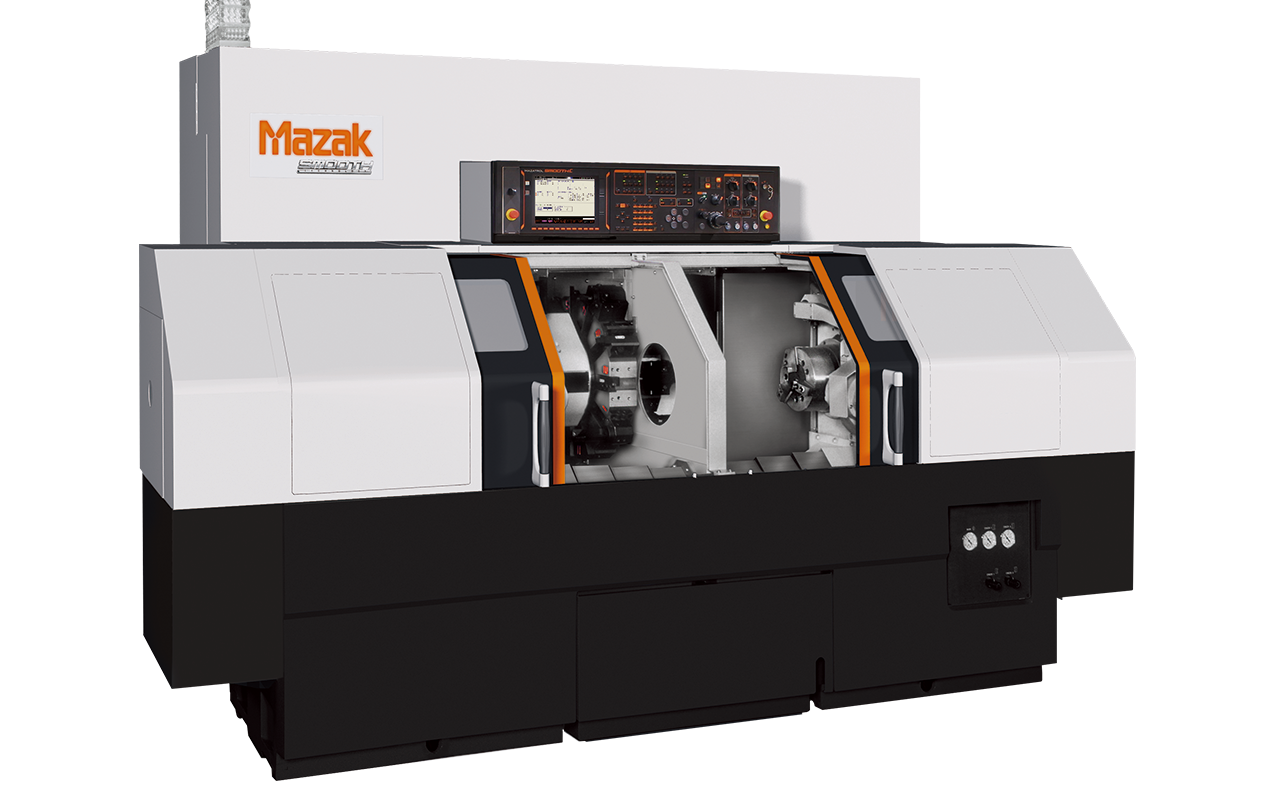
Symmetrischer Aufbau für hohe Produktivität
Symmetrische Spindel und Revolver
Auf beiden Seiten sind zwei Spindeln/Revolver mit der gleichen Bearbeitungsleistung angebracht. Die eingebaute Motorspindel gewährleistet eine hochpräzise Bearbeitung in allen Drehzahlbereichen, von niedrigen bis zu hohen Geschwindigkeiten. Mit der nicht abhebenden Rundtaktung kann das Spannen und Lösen von Revolvern mit hoher Geschwindigkeit und mit minimalen Störungen durchgeführt werden.
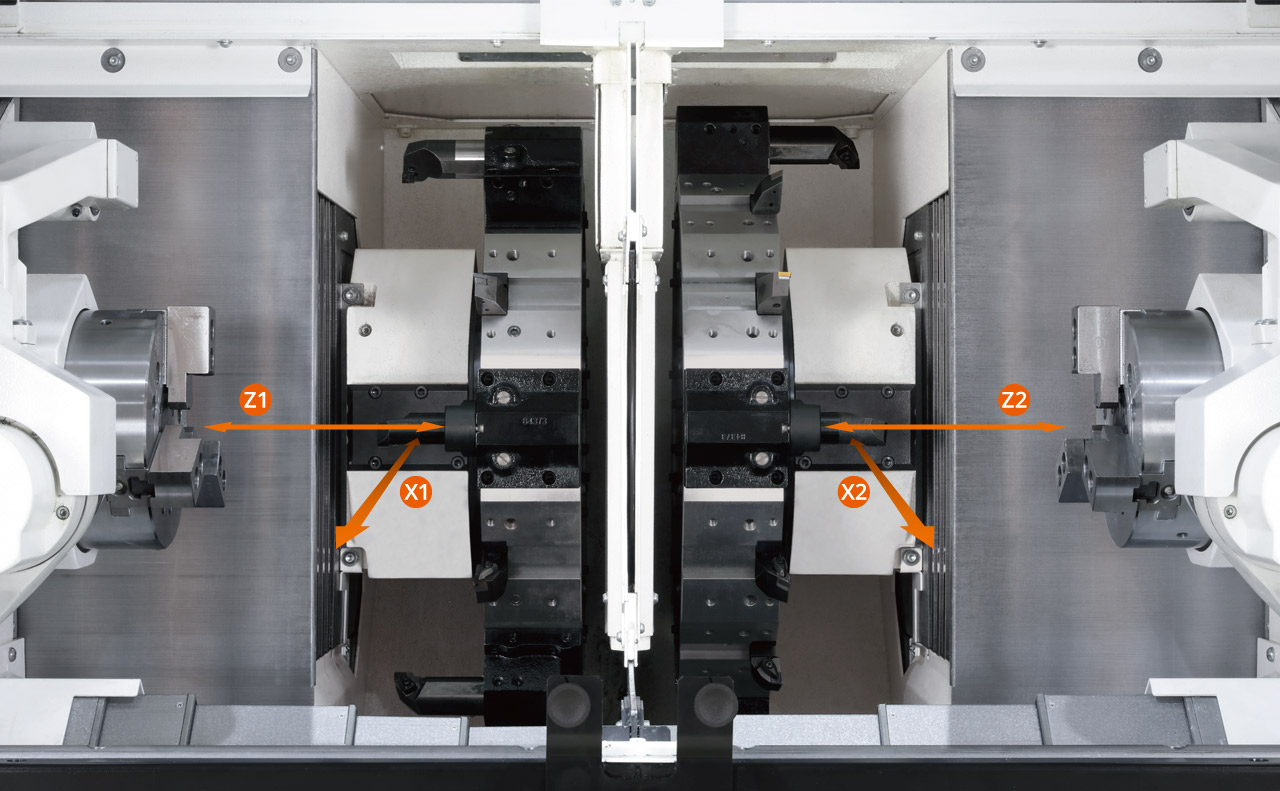
Kontinuierliche Bearbeitung mit automatischem Werkstücktransfer
Die automatische Hochgeschwindigkeits- und Hochpräzisions-Transferfunktion ermöglicht eine hocheffiziente OP10- und OP20-Dauerbearbeitung mit einer einzigen Aufspannung.
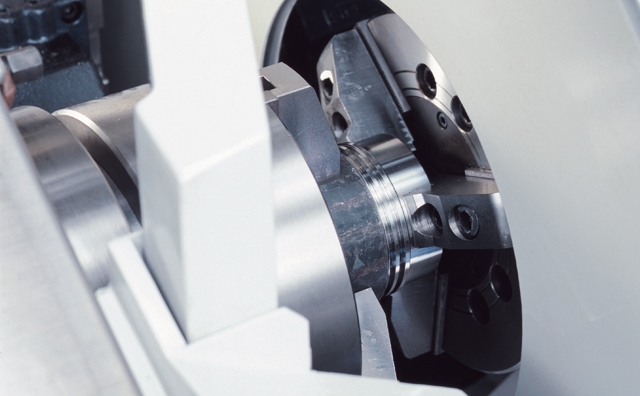
Automatische Trennwand für unabhängige Bearbeitung in beiden Bereichen
Die vollständige Trennung des Bearbeitungsbereichs verhindert, dass Späne und Kühlmittel auf die andere Seite gelangen. Es ist möglich, die linke und die rechte Seite getrennt zu bearbeiten oder ein Werkstück auszutauschen, während das andere bearbeitet wird.
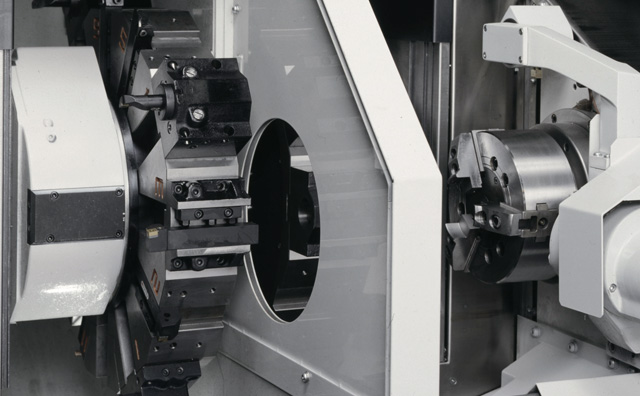
Hohe Produktivität und äußerst platzsparend
Kein Zwischenlagerbestand aufgrund der Prozessintegration
Der automatische Transfer integriert die Bearbeitung von OP10 und OP20 in den Drehprozess. Dadurch entfällt die Lagerhaltung bei der Bearbeitung von Werkstücken.
Erheblich verbesserte Flächenproduktivität (geringere Stellfläche)
Im Vergleich zu zwei 2-Achsen-CNC-Drehzentren der gleichen Klasse kann der Platzbedarf um 30% reduziert werden. (Verglichen mit unseren Produkten)
Dadurch werden die Laufwege und die Arbeitsbelastung des Bedieners erheblich reduziert.
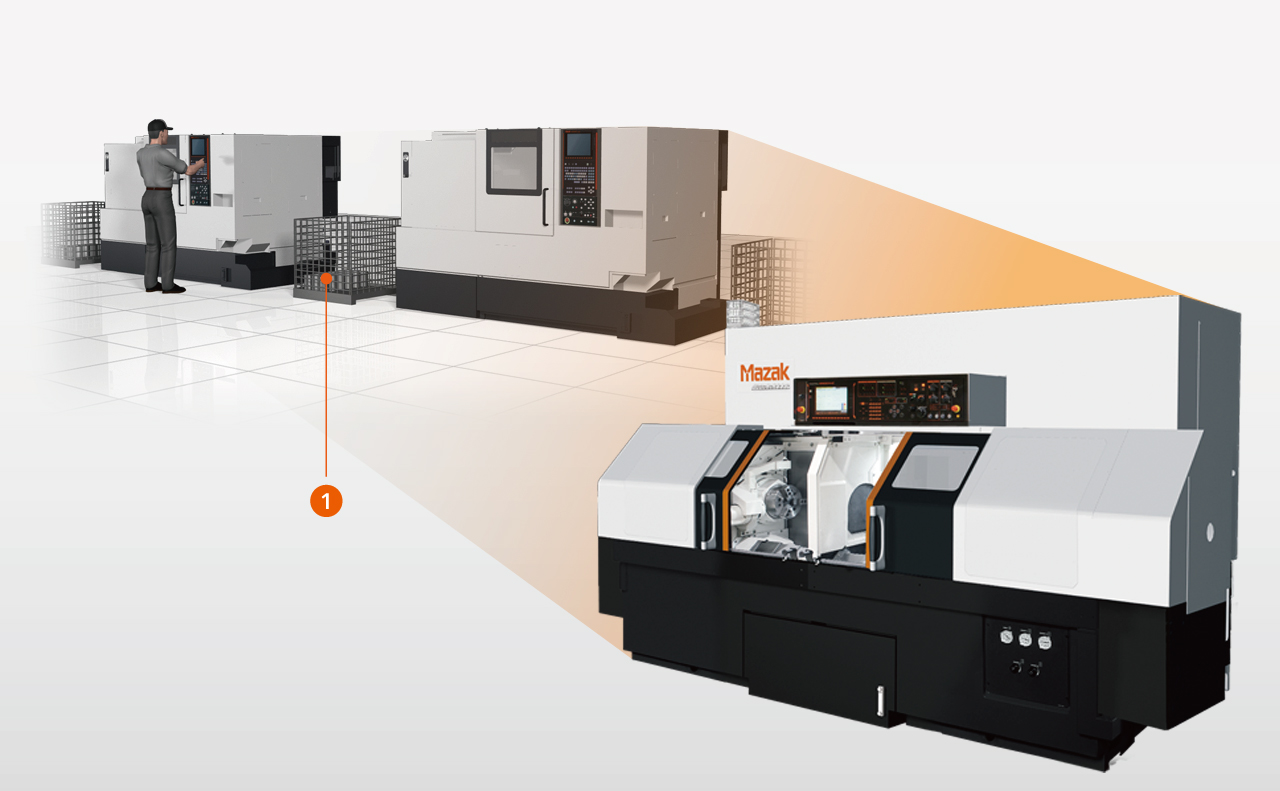
Vielfältige Automatisierungssysteme für Ihre Produktionsanforderungen
Automatisches Ladesystem
Das Ladesystem ist mit einer Werkstückentladevorrichtung ausgestattet, mit der das fertige Werkstück auf den Aufnahmetisch entladen werden kann, indem das Material einfach in das Spannfutter der Hauptspindel eingehängt wird.

Stangenlader + Ladergreifer
Die Stangen werden automatisch von einem Stangenlader zugeführt und die fertigen Produkte werden mittels Ladegreifer entladen.
Stangendurchlass 65 mm
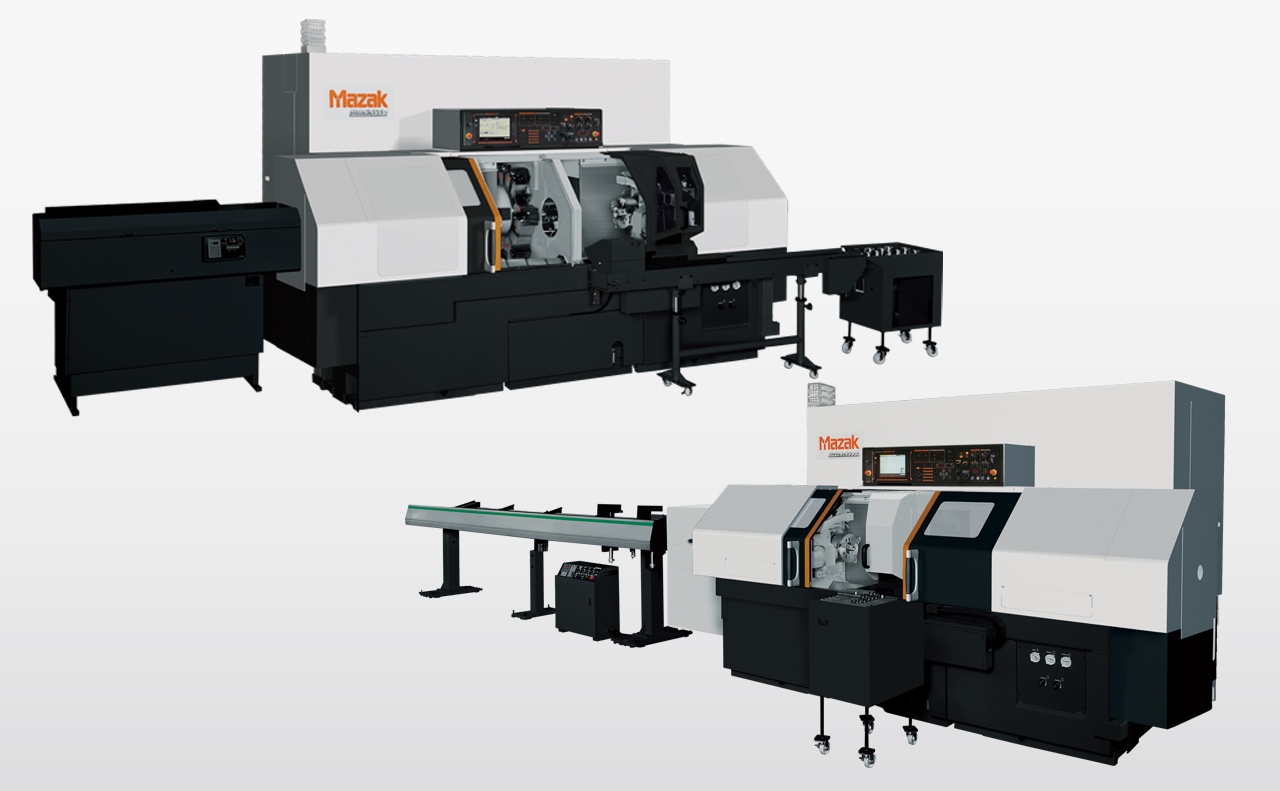
Portalladesystem
Automatische und kontinuierliche Bearbeitung von Spannfutter-/Wellenteilen aus OP10- und OP20-Prozessen können durchgeführt werden. Das Material wird automatisch in die Maschine geladen und das fertige Werkstück mittels Portalroboter entladen.
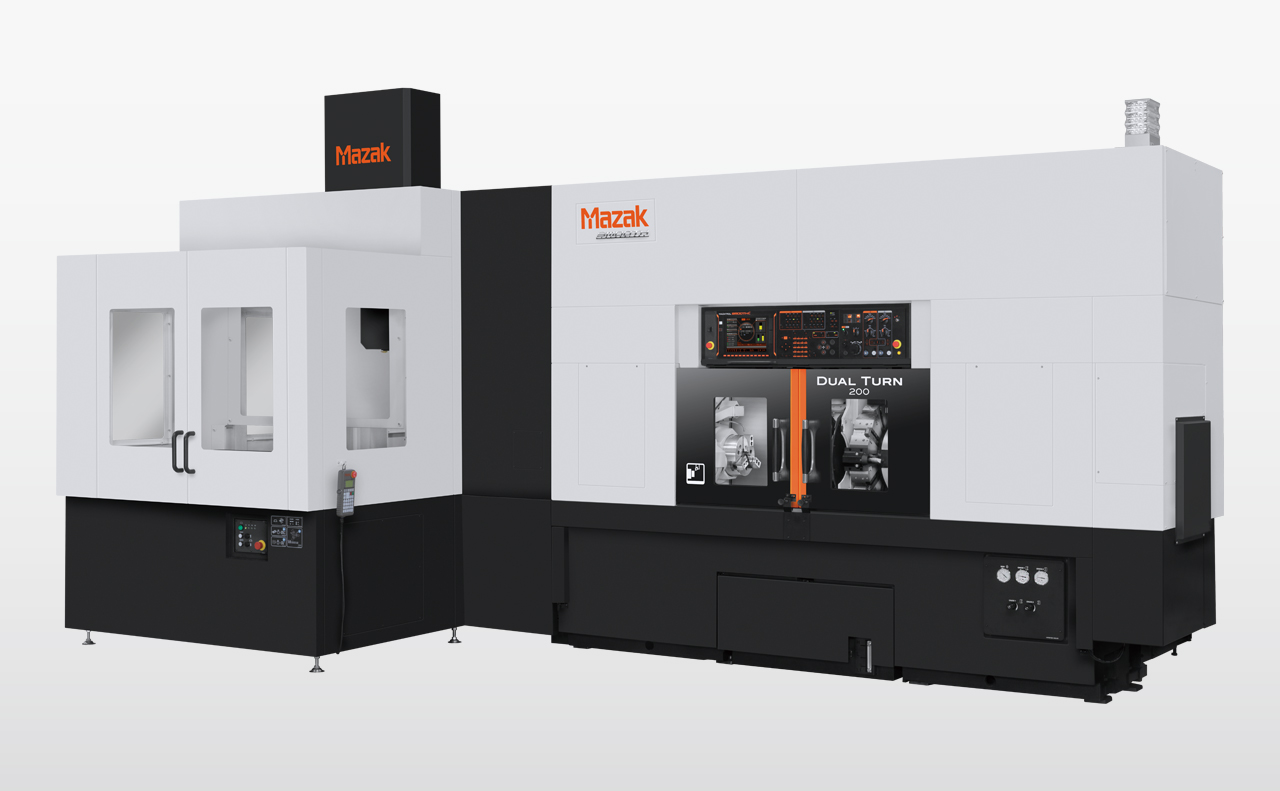
Portallader (Werkstückförderer mit 2fach Palettenwechsler) reduziert die Zeit für das Be- und Entladen von Werkstücken* um 20% im Vergleich zu früheren Systemen.
*Maschineninterne Betriebszeit
Vorheriger Portallader : 25,1 sec → GL-100 : 20,7 s
Schnellere Verfahrgeschwindigkeit : A-Achse 100 m/min, B-Achse 180 m/min
Schnelleres Be- und Entladen der Werkstücke: Verbesserter Sitz des Werkstücks im Spannfutter durch Andrücken des Spindelstocks an das Werkstück
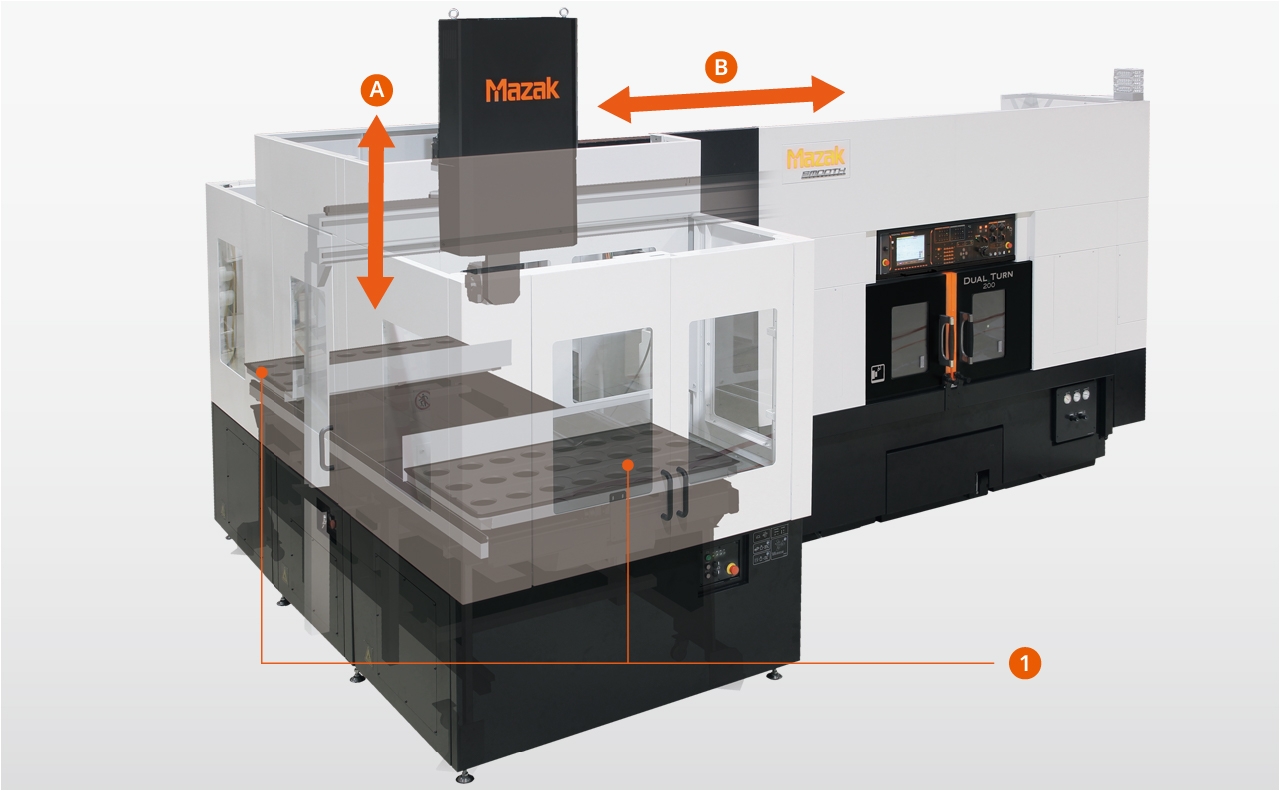
Einfache Programmierung dank MAZATROL-Dialogprogrammierung
Um 75% verkürzte Rüstzeit beim ersten Werkstück
Das Einrichten des ersten Werkstücks, von der Programmierung bis zur Überprüfung des Werkzeugwegs, dem Einrichten des Werkzeugs und dem Einrichten der Arbeitskoordinaten, kann in sehr kurzer Zeit durchgeführt werden. Im Vergleich zu anderen CNC-Steuerungen kann der Rüstaufwand um sage und schreibe 75% verringert werden.